4 Manufacturing and Design Engineering Trends for 2024
Key Takeaways:
- Prioritize cost, design for manufacturing (DFM), and sustainability early in the product design phase to accelerate time to market and boost profitability
- Improve early-stage problem-solving among cross-functional teams with collaboration
The Full Article:
The manufacturing industry faces a range of challenges that can blunt growth and profitability. To help navigate these pitfalls, we address design and manufacturing trends that business leaders are adopting to address current economic challenges:
- Empower Design Engineers to Lead in Costing and DFM
- Improve Cross-Functional Collaboration During the Early Design Phase
- Optimize Product Design With the Power of Digital Twins
- Drive Profitability, DFM, and Sustainability
1) Empower Design Engineers to Lead in Costing and DFM
To accelerate innovation, manufacturing companies increasingly involve design engineers in costing and DFM processes early in product development. By improving cross-functional collaboration, teams can:
- Accelerate new product design and ideation. Efficient and streamlined designer-cost engineering collaboration enables manufacturers to address early design problems quickly and confidently. Consequently, companies have more time for continuous innovation and strategic initiatives, such as evaluating design options for the next product in the pipeline and accelerating its time to market (TTM).
- Reduce engineering change orders (ECOs). Pinpointing design problems in the early stages of product engineering can help manufacturers steer clear of costly and time-consuming ECOs that often have an adverse impact on TTM.
2) Improve Cross-Functional Collaboration During the Early Design Phase
According to Tech-Clarity, around 93% of companies recognize the value of improving internal collaboration and plan to invest more in this area to accelerate systems engineering. By fostering effective collaboration, coupled with digital technology investments, companies empower designers to play a significant role in evaluating the cost and manufacturability of initial product concepts.
Early-stage product collaboration enables stakeholders, including designers (mechanical engineers), cost specialists, and procurement experts, to combine their competencies to:
- Ensure fair pricing of components and raw materials
- Make informed decisions on reshoring and selecting suitable global suppliers
- Identify cost outliers that could potentially impact expense projections and profit margins
- Enhance product life cycle management and timelines to bring high-value innovations to market faster
- Improve the project management process by making it more agile and streamlined
aPriori’s real-time collaboration and task management application, aP Workspace, enables entire manufacturing and design engineering teams to break down silos. It provides a single application to access centralized product design and manufacturing engineering data, fueling faster and more educated decision-making. Check out how aP Workspace unifies cross-functional teams in the graphic below.
3) Optimize Product Design With the Power of Digital Twins
Once a design specification has been finalized, a blueprint is required to bring the product to life. This is where the concept of the digital twin comes in. At its core, a digital twin is a virtual representation of a physical product, typically presented in the form of a 3D computer-aided design (CAD) model. It comprises the digital design of the product and pertinent manufacturing data. Further, it may include product lifecycle management (PLM) data and related information.
The digital twin can be a designer’s greatest ally. Since it acts as a virtual prototype of a product, the digital twin helps to:
- Optimize manufacturing processes and identify savings opportunities. Digital twins can simulate real-world scenarios, enabling teams to assess cost and sustainability trade-offs and make better, more economical manufacturing decisions quickly.
- Improve collaborative decision-making. Utilize valuable digital twin data for real-time collaboration and strategic decision-making across all levels of the organization. Effective and streamlined cross-functional collaboration enables manufacturers to bring their new, cost-effective, and high-quality products to market faster.
- Provide a more agile process and reach new levels of manufacturing efficiency. Employ digital factories to evaluate “make vs. buy” decisions, compare suppliers, and optimize selected factories down to the machine level for production.
According to recent findings, the utilization of digital twin capabilities will become increasingly common in Internet of Things (IoT) applications by 2027.
Dana Accelerates Product Design With Digital Twins
Dana Corporation, a leading innovator of light vehicle drive systems, is a prime example of how embracing digitalization and adopting DFM practices can lead to success. The manufacturer states that if a production process or design is deemed too expensive during late-stage product development, it could experience losses as high as $3 million. To prevent such losses from becoming a reality, the company uses aPriori’s digital twin capabilities to identify early design issues and gain real-time guidance for effective redesigns.
4) Drive Profitability, DFM, and Sustainability
It is important to understand that the obstacles and objectives that manufacturing companies face have a ripple effect. They do not just affect the manufacturer’s initiatives and actions; they also impact progress associated with continuous improvement goals.
Moreover, a manufacturer’s sustainability efforts are only as effective as the sum of its parts, including its suppliers. Therefore, manufacturers and others need to collaborate to strengthen their sustainability efforts by sharing carbon dioxide equivalent (CO2e) emissions data. This will help them gain a comprehensive understanding of their supply chain’s carbon footprint.
However, many companies struggle to balance cost and sustainability requirements. According to an article in The Engineer, almost 70% of manufacturing decision-makers restricted their sustainability strategies due to critical cost pressures. Fewer than half (43%) prioritize waste reduction, while only 43% and 29% focus on improving efficiency and reducing power utilization, respectively.
While sustainability initiatives may be difficult to implement and may be perceived as expensive upfront, the long-term benefits for both the manufacturer and the planet are significant. By reducing CO2e, addressing supply chain issues, alleviating labor shortages, and producing high-quality products, manufacturers can achieve their manufacturability, profitability, and sustainability targets simultaneously.
Amplify The Power of Your Manufacturing Capabilities
Digital integration, data analysis, and strategic collaboration are central requirements for today’s manufacturers. With aPriori, manufacturers can “shift left” and proactively address cost, DFM, and sustainability during the early stages of product development. aPriori’s digital twin technology enables manufacturers to simulate real-world manufacturing scenarios, allowing them to make cost-effective and sustainable decisions. These capabilities are instrumental in refining manufacturing processes, evaluating supplier and factory options, and ultimately driving efficiency across production lines.
aPriori empowers manufacturers to navigate the complexities of modern manufacturing by fostering greater efficiency, sustainability, and profitability. This strategic approach not only addresses immediate operational challenges but also sets the groundwork for long-term success in a fiercely competitive global market.
This post was originally published on Dec. 13, 2022, and updated on April 30, 2024.
Explore Our “Hot Take” Videos
Discover how manufacturing and design engineering teams tackle major business problems with aPriori.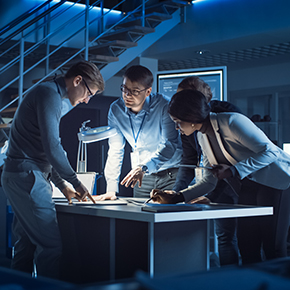