2024 Manufacturing Outlook for Sourcing & Supply Chain Resiliency
Key Takeaways:
- Geopolitical unrest, pricing volatility, and sustainability demands add to supply chain vulnerability
- Digitalization, supplier regionalization & diversification, and process agility are the main 2024 priorities for sourcing and procurement teams
The Full Article:
Resilience remains a top priority for manufacturers, who continue to increase their operational visibility and transparency and become more agile to proactively address potential supply chain disruptions. To remain competitive in 2024, digital transformation solutions enabling organizations to achieve supply chain resiliency, profitability, and sustainability goals are crucial.
According to KPMG, “smart” supply chain management and sourcing initiatives will make waves powered by advanced technologies such as automation, data analytics, digital twins, and more.
This article explores six main priorities that manufacturers are navigating to stay ahead of the competition in 2024:
- Increase Supply Chain Speed and Performance with Digitalization
- Build a Solid Foundation for Artificial Intelligence
- De-Risk Supply Chains and Evaluate Reshoring
- Offset Labor Shortages via Automation
- Capitalize on Economic Tailwinds to Accelerate U.S. Manufacturing Growth
- Use the Green Supply Chain as a Competitive Advantage
1. Increase Supply Chain Speed and Performance with Digitalization
Digital transformation (DX) can significantly benefit manufacturing sourcing and procurement teams. A growing body of work shows that successful DX initiatives require effective planning and a detailed implementation plan that addresses new technology, employee training, and operational guidelines (workflows) to drive value.
A 10-year Deloitte study of publicly traded companies worldwide finds that DX tied to an effective strategy and a comprehensive deployment and onboarding process can yield a market capitalization increase of up to 5%. By contrast, DX programs executed without the same level of rigor can cause value erosion.
Here are two areas of strategic sourcing to consider enhancing:
I) Streamline Supplier Communications and Revisit Strategic Sourcing Operations
Manufacturers and suppliers want to streamline their sourcing and procurement processes in the current business landscape. A survey conducted by IndustryWeek in collaboration with aPriori found that 70% of respondents want to accelerate the quoting process, and 79% prefer a 24-hour to two-week completion window.
Digital tools like aPriori provide a centralized solution for real-time supplier collaboration and information exchange. These automated platforms eliminate the need for traditional request for quotation (RFQ) processes that are time-consuming and prone to delays.
Instead, today’s digital technologies deliver “Zero RFQ” or automated procurement capabilities that enable manufacturing companies to:
- Send purchase orders (POs) directly to their trusted and preferred suppliers, saving them time
- Collaborate with suppliers on a transparent database to foster open discussions on design, cost, manufacturability, and sustainability
- Build long-term relationships with suppliers by aligning key assumptions and driving win-win scenarios
II) Accelerate the Product Design and Production Process
Digital automation-driven solutions help innovators bring together teams spread across different departments. These teams can combine their efforts on a single solution covering design, manufacturing, and sourcing operations.
With access to real-time data and visibility into the design and production process, sourcing professionals can get involved early in product development. This helps them identify potential component shortages and recommend design alternatives and changes to an existing bill of materials (BOM). This way, manufacturing companies can avoid supply chain risks and mitigate any negative impacts that may emerge.
aPriori’s real-time co-working application, aP Workspace, expedites task management and provides data audibility for decision-making. Users can access links to the application from their product lifecycle management (PLM) systems to gain actionable insights. These capabilities allow teams to collaborate seamlessly and communicate effectively, achieving their profitability and sustainability goals without reinventing existing business processes.
2. Build a Solid Foundation for Artificial Intelligence
Manufacturers continue to make digital investments to automate processes, manage data, strengthen internal resources, and facilitate cross-functional collaboration. The result is faster and more informed business decisions for forward-thinking manufacturers.
Generative artificial intelligence (AI) is one of the most alluring digital tools. S&P’s 2024 Supply Chain Outlook states, “While AI cannot prevent supply chain disruptions, if deployed in the correct manner, it could provide predictive probabilities of future disruptions.”
AI cannot work in a vacuum: It needs robust, accurate data to analyze and address specific manufacturing challenges. But as the MIT Sloan Management Review points out, “Manufacturing data is often localized or specific to a particular industry domain or a company’s operations. As a result, there isn’t a lot of relevant data available for building reliable AI models.”
Additionally, product design, sourcing, and manufacturing data often reside in individual departments (either in systems that are not integrated or personalized spreadsheets filled with supplier information that is not easily accessible).
Centralizing and providing access to data across the product development life cycle is central to making data-driven insights (with or without AI). Adding weight, carbon emissions, and other information to a PLM system – which already stores a bill of materials (BOM) – makes it easier for product development and sourcing teams to make decisions confidently and anticipate potential issues throughout the development process.
Manufacturers can also use automated analysis solutions like aPriori’s aP Generate, which integrates with the PLM to centralize critical manufacturing information. aP Generate links to aP Design and aP Workspace in the PLM, enabling users to take further steps or ask questions for up-to-date decision-making.
Some manufacturers are already gaining end-to-end insights using digital twins to connect product design, manufacturing processes, and individual factory capabilities. This data-driven insight is powerful on its own. And it can serve as part of a digital platform that AI can use to make additional analysis quickly.
Prioritizing data quality is key to unlocking the full potential of AI in the manufacturing industry. With data-driven insights, manufacturers can evaluate alternatives, improve scenario planning operations, transform business models, and enhance supply chain resiliency.
3. De-Risk Supply Chains and Evaluate Reshoring
Maintaining a diverse supplier base and reducing overreliance on specific supplier locations mitigates risks associated with geopolitical issues, natural disasters, and other unprecedented events like the 2020 pandemic. Diversified supply chains improve resilience and ensure business continuity in today’s dynamic global environment.
One tool that can help manufacturers with this is aPriori’s Regional Data Libraries (RDLs). These digital libraries provide real-world and timely variable material and supplier production costs across 87 global regions. By utilizing this feature, innovators can assess manufacturing alternatives effectively, consider the impact of region-specific tariffs, and avoid an overreliance on specific regions with potential risks. This often leads to significant cost savings and reduced lead times.
Manufacturers can also consider the benefits of reshoring specific manufacturing operations. This can lead to a reduction in shipping costs and taking advantage of valuable tax credits. For instance, automotive manufacturers can use reshoring to redirect the electric vehicle (EV) supply chain to the U.S. This helps eliminate their dependency on semiconductors produced in China and capitalize on a $7,500 tax credit.
In its annual Reshoring Index report, the global consulting firm Kearney provides further insight into U.S. reshoring initiatives. Its findings include:
- 96% of manufacturing executives are considering reshoring their operations
- 92% of executives have a positive outlook on reshoring initiatives
- An increase in executives focusing on geopolitical risks due to U.S. regulations and measures
Read our insights on why reshoring U.S. manufacturing could be right for you.
4. Offset Labor Shortages via Automation
According to Deloitte’s 2024 Manufacturing Industry Outlook survey, nearly 80% of respondents consider labor market shortages a critical threat. To address this challenge, approximately 50% of manufacturing executives equip their production workforce with advanced digital technologies and flexible schedules. This approach aims to:
- Enhance employee engagement and retention
- Increase operational productivity, reduce costs, and improve profitability
- Improve supply chain resiliency, visibility, and performance
Leading innovators like Woodward leverage aPriori’s automation, simulation capabilities, and actionable insights to counteract the shortage of skilled workers. By employing aPriori, the company can achieve more with fewer resources, such as:
- Reducing supplier lead times from 10 weeks to just one week. Additionally, the company transitioned to a smaller quoting team, reducing the number of specialists from five to one person.
- Automating the sourcing process enables Woodward to streamline negotiations for labor, overheads, and margins with suppliers. Additionally, aPriori’s automation-driven digital factories allow rapid, near-instant quotes for the manufacturer, enabling it to achieve its Zero RFQ initiatives.
- Enhancing decision-making processes through aPriori’s actionable, real-world insights into product design, sourcing, costing, and manufacturing. Woodward can streamline its supply base, evaluate its in-house production capabilities, and make strategic sourcing decisions.
5. Capitalize on Economic Tailwinds to Accelerate U.S. Manufacturing Growth
Product innovators can take advantage of positive economic factors supporting business growth in the upcoming year. These economic trends include:
I) Federal Investments in Manufacturing Innovation
The Biden administration has introduced new measures to strengthen North America’s supply chains and reduce costs. One of the measures implemented is the Creating Helpful Incentives to Produce Semiconductors (CHIPS) Act, which aims to reduce America’s reliance on foreign-produced chips.
This federal initiative includes $231 billion to build semiconductor factories in the U.S. The program also includes a 25% tax credit for capital investments in semiconductor production to spur innovation and manufacturing in this area.
Alongside the U.S. CHIPS initiative, the Inflation Reduction Act (IRA) aims to propel clean energy and sustainable manufacturing domestically. The IRA provides more than $1.7 billion in funding and additional tax credits to incentivize manufacturers. This initiative primarily targets consumers, empowering them to purchase green products like EVs.
Companies across multiple industries can take advantage of the incentives offered by federal programs. For instance, the building and construction industry can capitalize on these incentives by developing energy-efficient buildings with sustainable insulation, lighting, and heating, ventilation, and air conditioning (HVAC) systems. Similarly, federal investments to advance the clean energy sector range from EV production in the automotive industry to zero-emissions battery materials.
6. Use the Green Supply Chain as a Competitive Advantage
Product manufacturers increasingly recognize the growing demand from customers and stakeholders for sustainable, green innovations. Manufacturers can achieve a net-zero future by selecting the appropriate raw materials and production processes to decarbonize their product portfolios.
Across the globe, several regulations have been implemented to increase sustainable manufacturing and sourcing operations. These measures include:
- California’s Climate Corporate Data Accountability Act (SB 253). Starting in 2026, companies with more than $1 billion in annual revenues must disclose their Scope 1 and 2 greenhouse gas (GHG) emissions to the public. This will be followed by the Scope 3 supplier emissions disclosure in 2027. The state believes this new reporting mandate will propel U.S. manufacturers’ focus on climate action.
- EU’s Carbon Border Adjustment Mechanism (CBAM). According to the EU, this policy is designed to tax importers based on the carbon emissions of products entering the union. This helps prevent “carbon leakage,” or when EU companies move their production to countries with less stringent sustainability regulations. Carbon leakage applies to production processes involving materials such as iron/steel, aluminum, hydrogen, and more.
The financial impact of sustainability requires manufacturers to assign a cost to carbon as they design new products and initiate value engineering on older products. Internal Carbon Pricing (ICP) is an approach that manufacturers and other organizations use internally to assign a cost for each ton of carbon dioxide equivalent (CO2e) emitted. This enables manufacturing and sourcing teams to understand the cost of carbon and to compare it to traditional manufacturing costs (e.g., material, labor, and manufacturing overhead costs).
With an “apples-to-apples” comparison, sourcing teams can easily evaluate carbon and other manufacturing costs. Then, they can select the suppliers that will enable them to reach their key performance indicators for cost, CO2e, and other goals.
Gain the Ability to Navigate Global Supply Chain Uncertainty
The ongoing process of digital transformation shapes the 2024 manufacturing outlook. This encompasses trends like Generative AI, automation, and digital twin technologies for supply chain resiliency. Advanced digital solutions like aPriori provide real-time advantages, from accelerating product design to counteracting critical labor market shortages.
In addition to investing in digital technologies, economic tailwinds, fueled by initiatives like the CHIPS Act, provide sustainable growth opportunities and promote reshoring.
At its core, this post highlights the various obstacles, opportunities, and trends that manufacturing companies can expect to face in the upcoming year.
Get the State of Procurement Report
Learn how manufacturers and suppliers address speed, collaboration, sustainability, and more!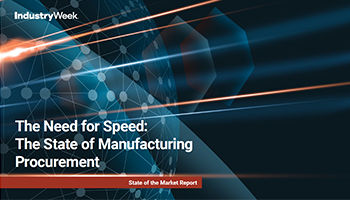