Address Labor Shortages to Ensure Productive, Cost-Effective Product Lifecycle Management
The pandemic has led to The Great Resignation, reducing the talent pool, and adding to upskilling shortfalls. Though manufacturing added 55,000 jobs in April 2022, employment in this sector remains down by 56,000 since February 2020. Supply Chain Brain noted that the average separation rate of supply chain managers increased by 28% from 2020 to 2021. By implementing a manufacturing insights platform, manufacturers can address labor shortages to ensure productive and profitable product lifecycle management (PLM).
In this article, executives and other manufacturers will discover how early manufacturing insights can be leveraged to address labor shortages and their associated issues. By implementing a manufacturing insights platform such as aPriori, technology is used to break down design, cost, and sourcing silos and enable teams across the enterprise to collaborate more efficiently and cost-effectively, as part of PLM integration. With one single source of truth, enterprises can streamline productivity (addressing labor shortages today and in the future), build more robust operations, and a healthier bottom line.
Understand the Manufacturing Workforce Landscape
A McKinsey podcast noted U.S. manufacturing accounts for approximately $2.3 trillion of the gross domestic product (GDP), employing about 12 million and supporting hundreds of local economies throughout the country. Though these statistics appear to have minimal impact on the overall economy and workforce, manufacturing is responsible for 20% of the U.S. capital investments, 30% of productive growth, and 60% and 70% for exports and business research and development, respectively. It also creates a ripple effect in other sectors as well.
Turnover remains high, despite 84% of manufacturing jobs lost during 2020 being added back to payrolls. To retain them, manufacturers should better engage existing employees and evolve the workplace. Fifty-eight percent of respondents to a Deloitte survey feel manufacturing jobs have limited career prospects, but 80% might be interested in roles with enhanced training and clear career paths.
Manufacturing executives recognize that more diversity and balanced gender representation are likely to expand the available talent pool. While 84% of surveyed manufacturing executives felt that their companies are effective in fostering an equitable and inclusive environment for new hires, they also acknowledged that more work needs to be done.
What is Product Lifecycle Management?
Digital manufacturing is the gateway to engage employees, provide upskilling, and evolve the workplace. Thanks to the cloud, it also enables better collaboration, which is essential to enhanced product lifecycle management.
Product lifecycle management (PLM) is the process of effectively managing all data produced by various software applications. All inter-departmental workflows as a new design matures (early concept, final production, retirement, obsolescence) become a part of PLM. Traditionally, PLM management has been a manual operation. The cloud’s genesis has moved PLM into a more efficient, cost-effective, and less labor-intensive process. Consider these three ways PLM addresses labor shortage issues:
- Attract the Workforce with PLM Integration
Automation allows manufacturers to have a greater global reach and workforce, helping stem labor shortage issues. It also enhances product lifecycle management or PLM integration, streamlining operations and accelerating time to market.
Cloud collaboration and intelligent manufacturing solutions attract more diverse and technology-focused workers. They also help to upskill employees. In fact, attracting and retaining a quality workforce is a top focus for 83% of manufacturers surveyed. Most workers still prefer employment in other sectors such as retail, services, and technology, according to the Deloitte survey.
- Utilize PLM Tools to Answer Workers’ Concerns and Wants
Two-thirds of consumer respondents see manufacturing jobs as innovative and problem-solving. Manufacturers should reiterate that technology is expected to enhance, rather than replace, jobs. For instance, digitalization, robotics, and artificial intelligence can make jobs safer and enable employees to do more productive work. McKinsey states that the U.S. is in a prime position to become more competitive. Digital transformation is that path forward.
Reliance on a local labor force is no longer necessary with digital transformation and product lifecycle management. The cloud has enabled organizations to collaborate in real-time regardless of location. Workers want to be productive, and safe on the job and contribute to their organizations in measurable ways. An effective product lifecycle management system can answer their concerns and wants.
- Discover How PLM Tools Address Labor Shortages
PLM management ushers newer and better technologies into an organization’s processes. More importantly, it improves operations and optimizes its existing workers regardless of labor shortage issues.
By investing in PLM tools, a manufacturer can see an average increase of 10% in production output, 11% in factory capacity utilization, and 12% in labor productivity. Best of all, it can identify how manufacturing can be done better and faster as well as when it is most cost-effective to outsource production.
The Advantages of PLM Tools
Outsourcing may not always be the most cost-effective route. PLM tools can identify where it makes sense to utilize the organization’s talent versus outsourcing it. Here are a few of the key advantages to using PLM tools.
PLM tools can model and simulate the cost and manufacturability of parts and processes. It also can:
- Enhance manufacturability decision-making
- Attract employees desiring technology-focused positions, upskilling, and education
- Identify cost savings
- Streamline the PLM process reducing manual functions and personnel hours
- Accelerate time to market
As noted in our recent blog article, Top 7 Manufacturing Challenges in 2023, manufacturers are using technology to supplement traditional upskilling and retraining programs. Now, they can automate processes, real-time assistance, and team collaboration within employees’ tasks and workflows.
Labor shortages will continue for the foreseeable future. Manufacturing simulation can compensate for these shortfalls, while also streamlining product lifecycle management.
How aPriori Works with PLM Systems
aPriori enables manufacturers to enhance the manufacturability and cost of new product designs, lessening design engineering’s workload, improving product value, and reducing time to market. Our cloud-based simulation software is discreet but powerful. It will automatically analyze the manufacturability of your digital twin CAD models each time they are checked into your Product Lifecycle Management (PLM) system and identify potential DFM issues. The system also will calculate a detailed manufacturing cost including any required tooling costs and associate them with each part.
Your engineer need only get involved if the system has detected and identified a potential manufacturability or cost issue, reducing the time and effort normally required with this function. The PLM system manages your product or module configuration, but if you choose to include your cost information in the PLM, regardless of configuration, aPriori will provide a complete cost picture. It will highlight the most important cost drivers on these parts, providing recommendations to remediate them.
A Better Enterprise Through a Sustainable Workforce
Digital manufacturing is and will continue to be, the lifeline for manufacturers. Without digitization, our workforce will not be sustainable; let alone thrive.
Utilizing manufacturing simulation does more than solve the labor shortage. It creates a more sustainable workforce and PLM process as well as boosts productivity and profitability. In turn, manufacturers remain agile and competitive, ensuring their longevity.
Are Labor Shortages Impeding Your Production?
Learn how Woodward addresses labor shortages, while digital transforming.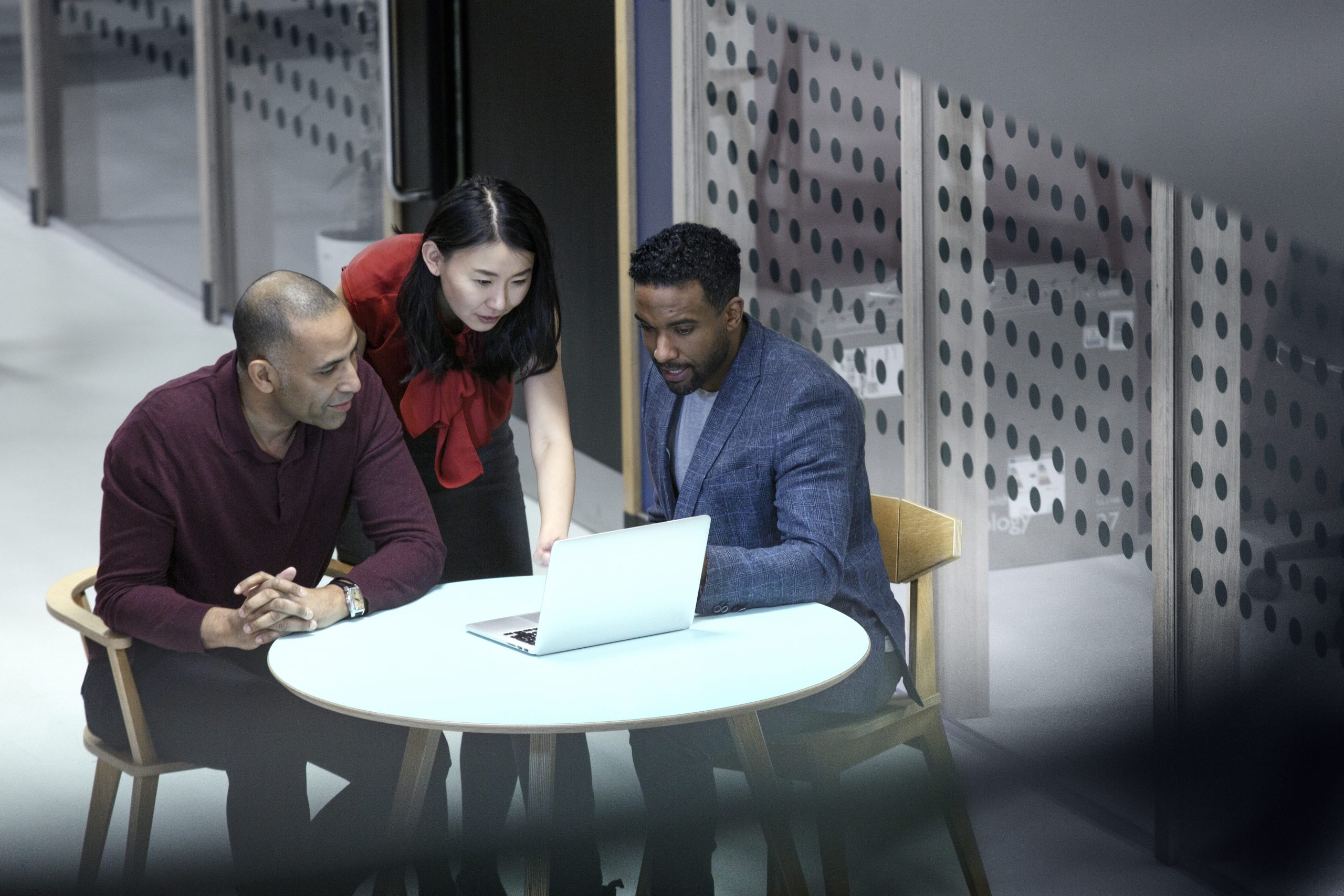