Apprenticeships + Digital Initiatives: Solve Labor Shortages and Accelerate Future Talent
Manufacturers still face a skilled worker shortage. According to an article in Deloitte, the manufacturing sector lost 578,000 jobs during the pandemic in 2020. Even more alarming, US manufacturing is expected to have 2.1 million unfilled positions by 2030.
One area where manufacturers are struggling to find workers is at the entry-level. Although entry-level manufacturing positions typically pay a higher starting wage than industries such as hospitality and retail, many of these jobs continue to go unfilled.
What can manufacturers do to attract and retain talent? The answer lies in an apprenticeship program. An advanced manufacturing apprenticeship program with digital initiatives can further alleviate these shortages.
This article will provide an overview of the current manufacturing labor shortage. We will explain the various on-the-job training programs for manufacturing, apprenticeship training resources, and how manufacturers can alleviate labor shortages and provide additional benefits to manufacturers and employees. Additionally, we will discuss how digital initiatives can support workforce development.
What is A Digital Manufacturing Apprenticeship?
Manufacturing apprenticeship programs are a great opportunity for manufacturers and potential employees, mainly if organizations have implemented digital initiatives that align with an on-the-job training program. An apprenticeship is a hands-on opportunity to get one’s feet wet in an industry-specific job, gaining invaluable knowledge and experience that no amount of academic education can provide. It is an actual workforce development program in every sense of the word.
An internship may offer experience with or without compensation. Typically, it is short-term. On the other hand, an apprenticeship encompasses:
- Commitment to formal employment
- Pay based on experience and apprenticeship level, which can increase over the course of the program
- Industry and position-based instruction as well as hands-on training
- Mentor program, pairing the apprentice with a more experienced employee who can impart knowledge and offer guidance
Depending on the technical position or required knowledge level, an apprenticeship can take one to four years. Many often conclude with certifications, secure full-time employment with the organization, and higher pay.
Why Should Manufacturers Implement an Apprentice Program?
According to the U.S. Department of Labor, apprentices have grown over the last decade, with a 64% increase in new apprentices since 2012. Nearly 15,000 new apprenticeship programs were created between 2016 and 2021.
They also are a win-win. Employees gain valuable education and training. Commencing a successful apprenticeship, they can improve their pay grades with average starting salaries of $77,000.00. Participants also increase future career growth opportunities. Manufacturers typically enjoy a 93% retention rate on employees upon apprenticeship program completion.
According to a Deloitte article, the manufacturing industry continues to have perception challenges, contributing to a lack of job applicants. The National Association of Manufacturers Q4 2021 Manufacturers’ Outlook Survey noted that nearly 83% of manufacturers mentioned attracting and retaining a quality workforce as their top challenge. Similarly, almost 45% of manufacturers said they had to turn down business opportunities because they did not have enough workers.
The good news is that manufacturing perceptions are changing for the better. The pandemic underscored how vital manufacturing is to the economy and our way of life. A Deloitte article indicated that manufacturing workers were essential during the pandemic, so critical personal protective equipment (PPE) and ventilators could be produced. Additionally, manufacturers were crucial in ensuring that the supply chain remained open and operational.
As a result, manufacturing perception improved during the pandemic. For instance, among workers surveyed for a Deloitte 2022 U.S. perception of manufacturing study, 73% viewed manufacturing as critical to the Covid-19 response due to their production of ventilators, PPE, and other essential equipment. The same study found that 69% of workers surveyed felt that manufacturing’s “essential” status helped sustain many jobs during the pandemic.
Five Steps to Implementing an Apprenticeship Program
Manufacturing technologies can debunk residual perceptions and close the labor gap. Aligning digital initiatives such as manufacturing simulation platforms can attract potential apprentices and strengthen your program.
According to the U.S. Department of Labor, there were 593,690 active apprentices and 27,385 apprentice programs in 2021. There are apprenticeship programs for several high-demand manufacturing positions, including tool and die makers, machinists, manufacturing engineering technicians, and aerospace engineers.
Employers can register their apprenticeship programs with the U.S. Department of Labor. Prospective job seekers will have the reassurance that a manufacturer’s apprenticeship program meets national quality standards.
Consider the following five steps to implementing a registered apprenticeship program for your organization:
- Determine your occupation concentration area. If unsure, you can check available occupations at the apprenticeship.gov site. Register your selection and then utilize available training programs. Industry experts have been vetted to facilitate the implementation process.
- Secure a program sponsor or partner. Sponsors and other key partners, such as a business or consortium of professionals, are essential to an apprenticeship program. They should include industry associations, labor organizations, educators, workforce development, apprenticeship resources, boards, and those willing to sponsor such vital programs. Sponsors should have a Registered Apprenticeship Program, overseeing all program administration and operations.
- Ensure your apprenticeship program meets industry standards. The Office of Apprenticeship or State Apprenticeship Agency (SAA) staff can evaluate it for local (SAA) or national (OA) standards. Complete the registration process through their Express Interest form.
- Build the apprenticeship program framework. There are many questions to consider when building a framework. Here are some to get started:
- What industry standards will you follow to ensure that apprentices are well-trained and prepared for high-demand fields in manufacturing?
- What will be the starting pay for apprentices?
- What will your wage progression look like as apprentices advance through the program?
- What benchmarks will they need to meet to advance their pay scale?
- Will you offer formal education as well as hands-on training?
- Will you provide mentors to partner with each apprentice?
- Is the apprenticeship program in person, virtual, or both?
- Will there be supplemental support in college or university affiliation programs?
- Will you require additional educators for the program?
- How will you recruit and manage diversity, inclusion, equality, and accessibility initiatives?
- What metrics will you use to ensure apprentice safety and meet/enforce worker regulations and requirements?
- What certifications will you offer, and what formal credentials will you provide graduates?
- Implement and manage your apprenticeship program. Like every other aspect of your organization, overseeing your apprenticeship program is an ongoing responsibility. It is vital to assess what is working and what is not. It is essential to measure your success and attrition rates as well. Apprenticeship.gov can provide additional support and resources.
Alleviate Labor Shortages and Skills Gaps
An apprenticeship program is a highly effective way to alleviate labor shortages and close skills gaps in manufacturing. It has a profound impact when combined with manufacturing technologies such as simulation platforms.
The Deloitte survey noted that 57% of executives who enhanced technologies used daily by employees potentially elevated those workers’ experiences and satisfaction. There are other benefits to apprenticeship programs that are partnered with manufacturing technologies:
- Upskilling: Manufacturing is no longer limited to a manual skill set. More workers expect upskilling opportunities, particularly with technology. As a result, these employees acquire invaluable knowledge and experience to build a technology-based career. Moreover, the manufacturer fosters talent for the organization’s future, strengthening its position in the marketplace.
- Attraction and Retention: Manufacturers that invest in their employees and nurture their career growth tend to attract and retain workers. Technology is key to this process as more incoming talent craves a technology-based organization and a position that aligns with it. Combining career development and the latest technologies is integral to mitigating labor shortages and reducing employee attrition. Additionally, cultivating future talent will close the gaps left by more experienced workers who retire or leave for other positions.
- Onboarding: The traditional method of manufacturing requires years of training. Today’s manufacturing technologies expedite this process, onboarding employees faster and more thoroughly. When using manufacturing technologies like aPriori, apprentices can better understand each manufacturing facet through insights and other visual, interactive tools. It also frees more experienced workers to focus on manufacturing’s highly technical or complex aspects.
- Productivity: Manufacturing technologies are an ideal training partner for an apprenticeship program. Not only do they onboard and train apprentices faster and more efficiently, but they also boost productivity and time to market. Technologies like aPriori’s early visibility feedback encourage apprentices and other workers to take a more proactive approach to problem-solving. More automation comes with these technologies. As a result, workers also have a better work-life balance, which is a top priority for most.
- Profitability: By combining lower pay scale work experience via the apprenticeship with manufacturing technology, manufacturers can do much more with less. At the same time, this technology gets apprentices up to speed faster, increasing time to market, higher output, and more – all of which improve profitability.
All these things typically lead to higher rates of job satisfaction. Greater productivity leads to higher profits, enabling manufacturers to pay better salaries. Additionally, such learning and training opportunities empower new employees and apprentices, affording them a clear path to progress within the organization.
Apprenticeships: The Path to a Brighter Future for All
Although the labor shortage issue will not disappear anytime soon, manufacturers can implement measures such as apprenticeship programs and manufacturing technologies to alleviate it. As a result, you will not only attract more workers but improve your operations in the process.
You also will be better positioned to weather the next disruption. Improved technologies enable agility. Most importantly, proactive, satisfied employees will be invested in the organization’s success, thanks to a solid apprenticeship program.
Explore How Woodward Shortens Quoting Timelines From 10 Weeks to 1 Week
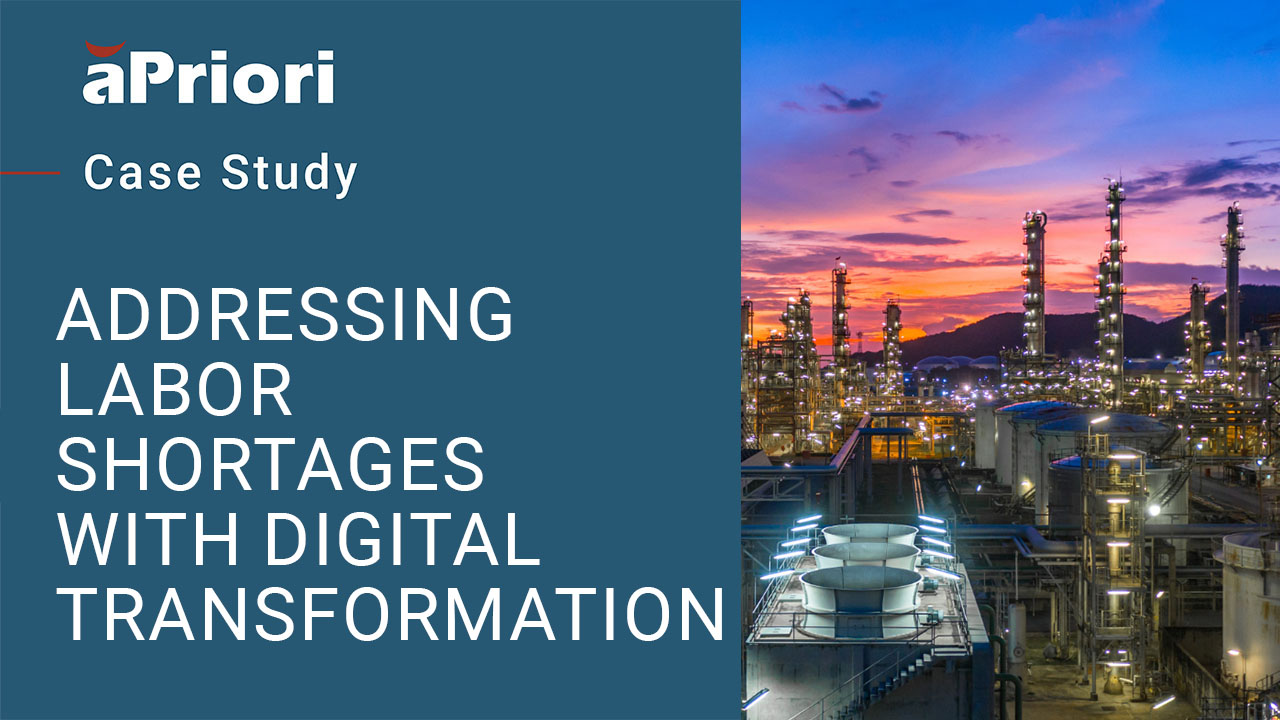