July 14, 2025
AI for Profitable Sustainability
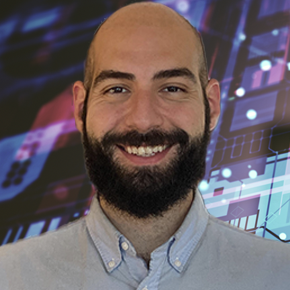
Transcript
For many manufacturing companies, the twin goals of improving profit margins and increasing sustainability have been at odds. But could AI technology change all that? My guest today is Berk Birand, the CEO of Fero Labs, which focuses on achieving profitable sustainability with the help of AI. I’m going to ask him today to untangle the mess of conflicting priorities so we can figure out if it’s really possible to be both sustainable and profitable in manufacturing today.
What in your background brought you to AI for Profitable Sustainability?
Berk Birand: I have a background in engineering. My most recent academic stint was doing a PhD at Columbia University in New York in the field of electrical engineering and computer science. I did research in the telecom space broadly, so I worked on developing algorithms that helped 5G base stations operate more effectively. I worked on developing algorithms that helped make the infrastructure of the internet more reliable and consume less energy. And of course, there’s a big narrative right now around AI and generative AI specifically, requiring a lot of energy. So I developed algorithms that helped those fiber optic networks act more effectively.
And then, towards the end of my PhD, we were looking for an area to apply our backgrounds. And my co-founder’s background is in AI research, specifically machine learning research. The other co-founder comes from an industrial background himself. But ultimately, the three of us came together with the goal of finding an area where we could apply our backgrounds that would have the largest potential impact. I remember I was looking into the smart home space, which was kind of growing at the time. But the magnitude of the problems in the industrial space was just incredible.
As responsible citizens, we try to do the right thing. We make sure we don’t run the AC when we’re at home, for example. But at a single steel factory, the amount of savings you could achieve in one second dwarfs the savings that thousands of people could achieve if they turned off their AC. So the magnitude of the impact that we could have was massive. And specifically, the need for the type of technology that we were specializing in, in AI and data technologies, was growing in popularity and becoming more of a burning need for manufacturers to be able to leverage the data that they have to achieve better process optimization.
The manufacturing use case: For years, sustainability has been a trade-off with profitability. Is this changing?
Berk Birand: It’s a very good question, a difficult question, because there are different kinds of sustainability, different ways to achieve sustainability. I would distinguish hardware-based sustainability approaches from software-based sustainability approaches or data-based sustainability approaches. So on the hardware side, there are many technologies like solar power and wind power, and other technologies like maybe carbon capture that are more likely in the near future. And these require a lot of investment. And of course, the goal is that after these investments are made upfront, eventually the savings will pay for these upfront investments.
The software-based or data-driven approach is a little bit more subtle. The advantage of it is that it’s available today. And the goal of these types of technologies is really to make your factory more efficient as it stands now. Of course, every factory has been trying to be more efficient all along. For the past 50 years, there are different kinds of tools that have been developed in order to help engineers run their factories more efficiently. Six Sigma is an example of the Toyota production system. But what we see is that frequently these technologies fall short of achieving the kind of improvements that the modern factories need.
Specifically, these types of approaches are not built to deal with the complexity of the typical factory and the complicated data landscape of a factory as well. So if our goal is to help the factories run as effectively as possible, we believe that profitability and sustainability can actually go hand in hand, that it doesn’t have to be one versus the other.
Let me start with a very concrete example. One of the prominent ways of making steel these days, steel products, such as steel beams or steel coils that are going to car manufacturing, is by melting scrap steel and then turning it into fresh new products. This is perfect from a sustainability perspective because it’s effectively 100% recycled products. Now, this is perfect because the chemical sector and other sectors are trying to become as recycled, or another term for this would be circular, as the steel sector is and has been for the past 20-30 years.
That said, using the waste of one system to power another system, even though it is great from a sustainability perspective, is actually very hard to run a factory in this way. It’s very hard to build complicated steel products in this way. And even when it is possible to build medium complexity steel products, it’s very hard not to waste a lot of resources in achieving that production. So in this context, within steel manufacturing, the notion of profitable sustainability allows factories to continue making steel in this way, but then reducing the waste in raw materials, reducing the waste in production volume, and being able to build more complicated, higher value steel products that then increase the top line as well, because now they can sell these for more.
Finding that trade-off between profitability and sustainability is, we believe, a little bit easier in the software data-driven approach.
How does AI help the steel manufacturer scrap less?
Berk Birand: First, it takes a machine learning AI model that effectively knows how each parameter affects the ultimate quality of the production. Some of these relationships are, of course, known to the engineers. For someone who’s been working at a steel plant, they understand how carbon affects the strength of their steel. But there are hundreds of inputs, and some of these are much less well understood. They might be unique to an individual plant. They might be unique to a type of product that a plant manufactures or a specific scrap source that they buy scrap from.
Knowing the objective of the data and the costs, small savings that could be in the seven digits per year for even a medium-sized steel plant, allows engineers to still make sure they match their quality goals, and reduce their costs.
In this case, this cost reduction also comes with a sustainability benefit. If I’m saving raw materials from being consumed over the course of about a year, this adds up quite substantially. So in the sustainability community, this would be scope three emission reduction, which comes with a profitability increase at the same time.
So, to us, profitable sustainability means effectively building software that can drive both sustainability and profitability simultaneously by exploiting the savings available in many plants. We estimate that companies can achieve about a 5% increase in their EBITDA profits by doing things better day in, day out, 24-7, using AI as a supporting team member within their teams.
What is the difference between AI for engineering and chatting with an LLM?
Berk Birand: The way that I would describe the difference between an LLM kind of product is that engineering AI models are built to work with and digest numbers, to compute phenomena, and to compute numbers. So the AI can show some graphs of, for example, here is what I think of all these 100 parameters and how they impact your targets. And an engineer can look at it and say, Okay, this one is interesting. Help me optimize this one. Then the AI can run in the background, and then the engineer could be coming in at work at 9 A.M., and see an email coming from AI saying, I’ve discovered that if you did these slight changes, you could save this much in dollar numbers and also saved this much in your scope 2 emissions.
Manufacturing organizations are not typically the early adopters for any kind of technology, and for good reason. You’re dealing with a very complex system, running a plant across three shifts, where there are safety concerns. So it’s a very complex process. Initially, we were met with a lot of skepticism. Two things have changed this. First of all, the world has gone through an incredible supply shock. And so the realization of any manufacturer is that we can’t just keep doing the same thing we’ve been doing for the past 30 years and then expect to be around for the next 30 years. Things are changing very quickly, and we need to adapt. The second change has been the availability of tools like OpenAI’s ChatGPT, where folks were able to play around with AI. I think most people can realize that within the space of AI, there’s something interesting here. Ultimately, these two phenomena change the perception of these kinds of technologies, so factories are more open to applying AI to manufacturing.
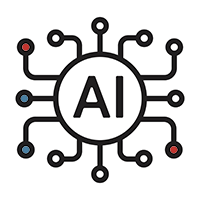