Supply Chain Management in the Age of AI: Unlocking Value at Scale
Key Takeaways:
- AI solutions are on course to make a significant impact on supply chain management
- Learn how to overcome the challenges of AI adoption and how AI automation is providing new levels of speed and insights for data-driven decision-making
The Full Article:
Artificial intelligence (AI) technology represents a significant opportunity to manage the scale, complexity, and real-time insights required for effective supply chain management. To underscore AI’s potential impact in this area, Gartner projects that nearly three-quarters of procurement leaders will adopt AI by the end of 2024.
But advancing AI (or other emerging technologies) from “opportunity” to “impact” requires careful planning and a solid foundation for success. The following sections outline opportunities, applications, and key considerations for harnessing AI applications for supply chain management (SCM):
- How to overcome “dirty data” to adopt AI
- AI use cases for sourcing and procurement
- Take supply chain management to the next level with AI
Defining AI for the Supply Chain
To provide context for this blog, let’s first define various types of AI. Traditional AI, also known as deterministic AI, operates using defined logic rules to process complex information quickly. Deterministic AI examples include simulation software for product design and manufacturing, and automation software.
Generative AI, however, uses machine learning and deep learning to create software code, images, text, and other unique outputs that mimic human creativity.
1. How to Overcome “Dirty Data” to Adopt AI
AI algorithms are only as good as the information it can access. And using clean, accurate data across departments is an ongoing challenge at many companies. McKinsey reports that up to 70% of the effort associated with AI-based initiatives is tied up in harmonizing data.
Similarly, a 2024 Manufacturing Leadership Council (MLC) survey reveals that 68% of manufacturers cited data issues as their biggest challenge to AI adoption. The survey also uncovered manufacturers’ biggest challenges using AI-related data:
- 63%: poor data quality
- 55%: contextualization
Let’s examine how to address the following data challenges to capitalize on the benefits of AI.
Improve Data Quality:
Manufacturers are addressing data quality challenges by combining actual historical product data with simulated insights (deterministic AI) to provide the foundation required to produce relevant generative AI responses (and to prevent AI “hallucinations”).
While a manufacturer’s actual historical data provides a timeline of cost, production volume, etc., this information won’t necessarily help you uncover areas that are costing you time, money, and customer satisfaction (e.g., how do you know if you’re overpaying for a component if you only have quote and payment information?).
To gain these types of insights, manufacturers rely on simulation and modeling to identify opportunities for improvement across the organization. With complete control over product data, manufacturers can instantly adjust shop floor labor rates for a plant in Taiwan or raw material cost data to reflect inflationary pressures.
Increase Data Contextualization:
Sourcing, product design, and manufacturing data sets often reside in individual departments (either in siloed systems or spreadsheets filled with supplier information that’s not easily accessible).
Manufacturers are using the digital thread to connect real-time data across multiple systems to maintain a single source of truth. Companies have contextualized data at their fingertips – including cost, carbon footprint, and manufacturability (DFM) – when they tie together 3D CAD files, product life cycle management (PLM) systems, enterprise resource planning (ERP) systems, and other information.
This level of insight makes it easier for sourcing teams to make decisions confidently and anticipate potential issues throughout the development process.
AI Use Cases for Sourcing and Procurement
Enhance Supply Chain Planning and Strategic Planning
Busy procurement teams can use automated AI insights to focus on activities with the greatest potential impact to optimize their limited resources. Automated AI insights are providing manufacturers responsible for global supply chains with new levels of speed and accuracy across functions to:
- Identify cost-saving opportunities at scale by analyzing thousands of parts at one time to identify outliers for both cost and carbon footprint
- Optimize the entire production process for cost and other factors rapidly based on design, material selection, manufacturing process, and specific factory location
- Make decisions quickly and confidently using automated insights to compare multiple complex scenarios (e.g., compare “build vs. buy” options, material selection, quantifying the cost impact of disruption/risk, etc.)
- Compare production options by evaluating digital factories down to the machine level for a granular understanding of costs, production speed, and other factors
- Analyze cost, carbon, and DFM simultaneously to make informed decisions, have detailed conversations with suppliers, and avoid expensive delays
Streamline and Accelerate Bid/Supplier Selection
Use AI-enabled automation to improve operational efficiency with suppliers. By digitizing supplier selection, providers/vendors and manufacturers can save time and operational costs.
Woodward is a $3.2 billion developer of advanced energy control systems for commercial and military customers. The company’s global commodity team uses aPriori’s AI-powered technology to configure digital factories to reflect key suppliers’ cost structure and capabilities down to the machine level. With this information, Woodward can simulate production across multiple supplier digital factories to identify the most appropriate supplier option.
Woodward uses its digital factories to power its self-quoting (Zero RFQ) initiative for key suppliers and to identify open capability and capacity. As a result, the company went from a 10-week supplier lead time to a one-week lead time.
Scale Your Supplier Network Rapidly
How long does it take your organization to evaluate the capacity of your corporate plants? And how fast can your sourcing team evaluate the benefits and drawbacks of switching manufacturing to a new region? Use AI tools to address issues including:
- Pinpoint capacity issues quickly. Digital factories provide manufacturers with access to valuable design, sourcing, and planning capabilities. In addition to high-level factory capacity information, advanced manufacturing and supply chain planning teams need to see the process for each design alongside detailed production cycle time metrics. Teams use this information to determine the processes and number of machines required to meet production volume goals and identify capacity issues.
- Compare regional manufacturing costs. Even one supplier forced offline can leave a business scrambling to source hundreds of parts or produce complex assemblies within a tight timeline. With digital manufacturing simulation, product manufacturing teams evaluate other geographies based on sourcing costs in Brazil, Mexico, or other countries. Labor, overhead, and tool-shop rates are just some variables required to model costs and evaluate regional manufacturing options accurately.
- Expand your supplier network: Use AI to rapidly identify and qualify new suppliers based on your specific requirements. Manufacturers can digitally recreate their suppliers’ factories to better understand costs associated with cycle time, materials, etc. And they can use aPriori to compare total manufacturing cost data across nearly 90 regions to compare supplier quotes against industry averages. This visibility is essential to sourcing competitively, particularly for organizations expanding their supplier reach geographically.
Boost Supply Chain Resiliency and Antifragility
Use AI technology to automate the analysis of your current supply chain capabilities and audit your top-tier suppliers for resiliency, which can include insights to:
- Determine whether there is a regional overreliance on suppliers and specific components/materials – and redistribute accordingly
- Address shipping and logistics roadblocks (e.g., natural disasters, political unrest, and capabilities in some regions that have not returned to pre-pandemic operations)
- Evaluate alternative countries for sourcing and manufacturing
- Identify new suppliers and evaluating alternative manufacturing methods
Also consider assigning a financial “premium” for reliability (increasing the antifragility of your supply chain). For example, Accenture reports delays and bottlenecks affect revenue growth between 7%-11%. The survey of more than 1,200 senior executives also notes that manufacturers may be willing to pay a 3-5% premium for significantly higher supply chain reliability and resilience.
Depending on the size of the sales opportunity and other factors, speed to market can more than offset added supply chain costs.
Compare Cost and Carbon Across Supply Chain Operations
Trade tariffs, “carbon taxes,” transportation costs, and other variables can also impact a product’s total unit cost (TUC). The European Union’s “carbon tax” – the Carbon Border Adjustment Mechanism (CBAM) – could increase the material costs of imports from carbon-intensive countries by 15%-30%. (Learn more about the CBAM’s impact on manufacturers.)
To set a financial value of CO2e during product design, manufacturers are using Internal Carbon Pricing (ICP) to quantify the value of carbon reduction. By setting a cost per ton of carbon, manufacturers have an “apples-to-apples” comparison to help make effective business and investment decisions, incentivize departments and suppliers effectively, and support low-carbon innovation.
AI-powered solutions like aPriori can use a manufacturer’s ICP to report on production and carbon “costs” and review how changes to design scenarios can impact cost and carbon.
Take Supply Chain Management to the Next Level with AI
By leveraging AI technologies, manufacturers can gain unprecedented control over their sourcing, procurement, and overall supply chain operations with predictive insights. AI offers a path to greater efficiency and insight by providing teams with the tools to make informed decisions that drive cost savings, enhance supply chain reliability, and accelerate time-to-market.
These data-driven advancements will also enable manufacturers to increase their responsiveness (service levels) and address shifting market trends quickly and confidently.
As AI continues to evolve, forward-thinking manufacturers will be well-positioned to scale their supplier networks, streamline operations, and navigate the complexities of global supply chains with confidence. Embracing AI is no longer just an opportunity—it’s the key to unlocking value at scale and staying ahead in an increasingly competitive market.
Get our Supply Chain Report to Accelerate Sourcing and Reduce Risk
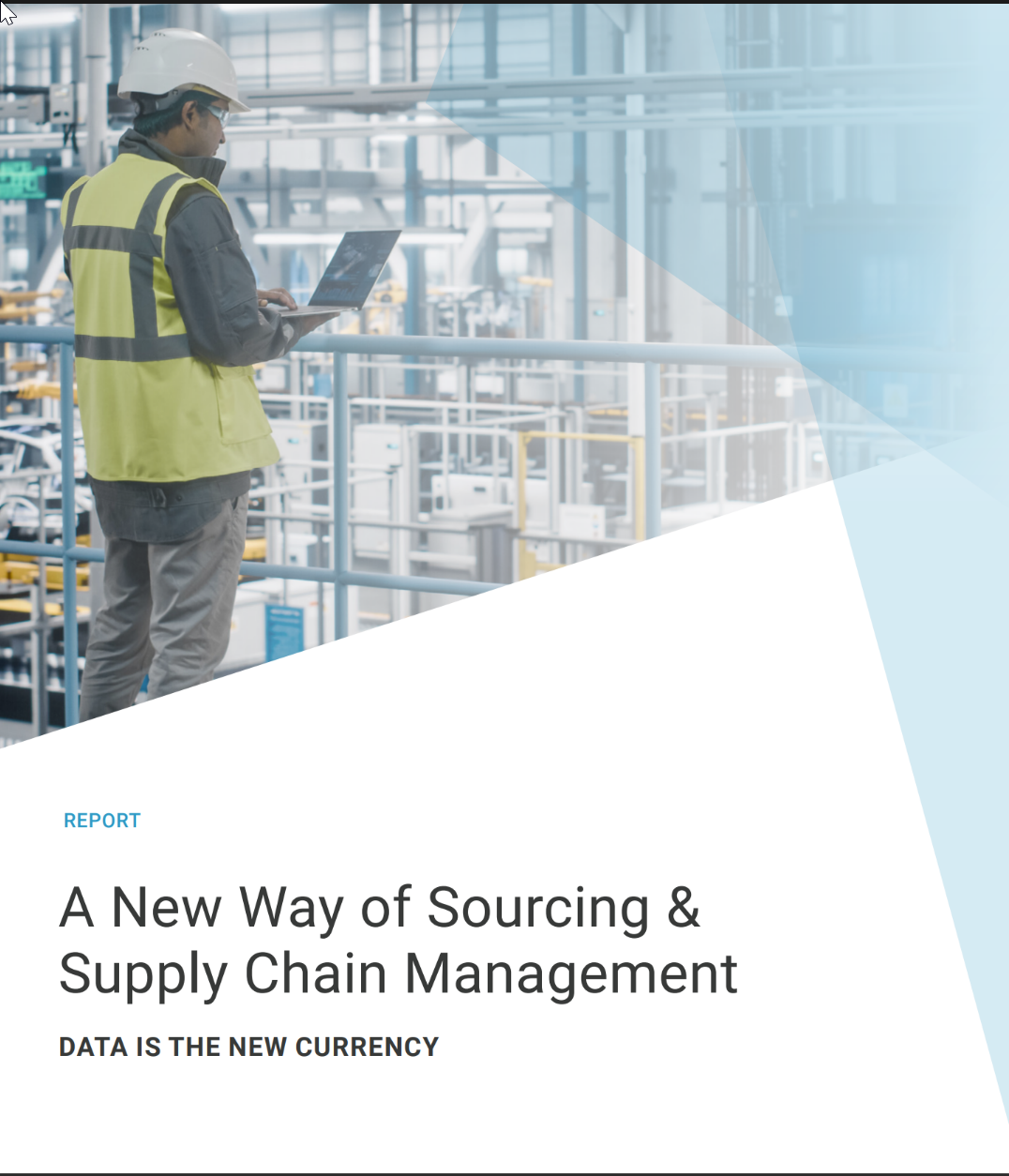