Product Cost Transformation Strategies for Engineering and Procurement Leaders
Key Takeaways:
- Cost transformation focuses on fostering long-term value creation and innovation.
- This includes adopting a bottom-up approach (known as zero-based budgeting), applying digital transformation (DX) capabilities, and implementing operational changes.
The Full Article:
Manufacturers face ongoing pressure from investors and customers to improve profitability and sustainability amid economic uncertainty. During periods of inflation and economic headwinds, cost-cutting gains added importance.
A survey of senior executives revealed that enterprises are targeting an average of 7% savings in 2023, according to the Information Services Group (ISG). The 2023 ISG survey also found that 69% of enterprises met their 2022 cost-savings targets while 31% did not.
Cost-reduction efforts often operate independently at the departmental level, or are part of sweeping organizational changes (e.g., a corporate restructuring with a reduction in force) to meet short-term goals.
But without a coordinated cost strategy, there’s no overarching directive to ensure that cost-cutting efforts are aligned across cost engineering, sourcing, and other departments to meet short-term targets and reach long-term goals. Siloed cost-reduction initiatives and selective corporate cuts can provide incremental gains but fall short of achieving transformational change.
Successful manufacturing leaders are taking a strategic approach to cost transformation, which focuses on fostering long-term value creation and innovation. This includes adopting a bottom-up approach (known as a zero-based approach), applying digital transformation (DX) capabilities, and implementing operational changes to drive added value.
Use a Zero-Based Strategy for Cost Transformation
New ideas often require a new framework to recalibrate the “we’ve always done it this way” mindset to adopt a new way of thinking to achieve transformational savings instead of incremental reductions. So, rather than examining longstanding department-level budgets and operations to identify cuts, try a zero-based approach.
This strategy encourages manufacturing executives to reimagine their organizations from scratch by using a bottom-up approach and by focusing on company-wide opportunities to increase efficiency, expand capabilities, and contain costs. This process can include justifying every expense at the beginning of each budget cycle to encourage a thorough review of all expenses.
Accenture describes a zero-based model as “a new way to drive profitability that emphasizes the future over the past.” And more than just a cost-cutting exercise, a zero-based approach is a strategic realignment of resources, talent, and processes. Using cost-benefit analysis, the zero-based methodology incorporates elements of Peter Drucker’s “systematic abandonment” process to eliminate activities regularly that are no longer useful. This process also includes ranking and prioritizing activities based on their perceived value to the organization and its goals.
As an example, McKinsey advocates companies focusing on resources allocated throughout an organization to help determine staffing levels, identify redundancies, and further refine roles and responsibilities. Another component is to examine the should cost of raw materials and components, along with a supplier’s direct and indirect costs (based, in part, by factory location).
Transforming a series of cost-focused activities into a cohesive program requires manufacturers to rethink ownership and accountability beyond departmental siloes. Organizations that empower employees to contribute to change by incorporating their ideas tend to increase employee commitment to making changes successful.
Managers and employees who have visibility into corporate progress against key performance indicators (KPIs) can identify opportunities to make improvements quickly without waiting for formal reviews. That said, a formal review process enables stakeholders to assess their progress to date and adjust accordingly.
As with any new process, internal training and a commitment to open communication is integral to a successful rollout and ongoing success. Learn how Woodward implemented new DX capabilities within its corporate procurement operations with aPriori.
Apply Digital Transformation as a Lever for Cost Savings
Digitalization technologies can help manufacturers further contain costs with new levels of efficiency, speed, and accuracy. This includes applying technology to optimize business processes, integrate and extend existing systems, and gain new levels of collaboration and visibility throughout the product development process.
Effective DX solutions enable organizations to rethink entire processes, provide real-time guidance to make improvements, and provide the data required to make decisions quickly and confidently. A zero-based approach can provide the roadmap to success, and DX can serve as the engine to drive an organization to the next step in its business maturity model.
To help manufacturers achieve their goals, the aPriori Manufacturing Insights Platform provides automated insights for users to reduce costs while improving sustainability, productivity, and manufacturability. aPriori extends manufacturers’ digitalization investments, add new levels of automation, and delivers visibility across the product development lifecycle to make decisions quickly and confidently. aPriori’s DX capabilities enable manufacturers to:
1. Gain Insights from Design through Production: aPriori uses the digital twin concept to simulate the entire product manufacturing process. By connecting aPriori’s product design, manufacturing process, and factory “digital twins,” manufacturers can gain visibility across the product development lifecycle. This includes running “what-if” scenarios for product designs, manufacturing processes, and individual factories or production regions.
2. Integrate and Strengthen Existing Investments: aPriori automatically extracts geometric data from 3D CAD files checked into product lifecycle management (PLM) systems. The solution leverages the 3D data and connects three digital twins—product, process, and factory—to generate precise carbon, cost, and manufacturability breakdowns.
3. Establish a “Central Source of Truth” for Product Data: aPriori’s digital thread establishes a closed-loop process that provides a single, reliable source of information that stakeholders can use to make informed decisions. Specifically, aPriori uses the digital thread to connect performance and manufacturing data between the digital twin and downstream applications (e.g., design engineering, sourcing, manufacturing partners, etc.). This enables teams to work faster and more efficiently by using updated digital product information.
4. Connect Teams and their Data: aPriori eliminates departmental silos by connecting teams including design and cost engineering departments, sourcing and procurement teams, sustainability groups, and suppliers. This provides an end-to-end solution to automate product manufacturing cost estimations to increase profitability.
5. Analyze Costs at Scale: aPriori empowers sourcing teams and other stakeholders to identify cost outliers across multiple dimensions (e.g., material, component type, etc.). aPriori provides the automated insights to conduct a spend analysis at scale, identify cost outliers, and then use manufacturing insights to establish should cost models to compare current component costs against costs based myriad direct and indirect expenses based on production region. (Read more about aPriori’s should cost capabilities.)
6. Make Decisions Quickly and Confidently: aPriori provides the end-to-end visibility and the data required for stakeholders to make decisions quickly regarding cost, sustainability, supply chain risk, and more.
Implement a Holistic Cost Transformation Strategy
Strategic cost management in manufacturing requires a holistic approach. Read more about the pillars of implementing a zero-based cost transformation across your organization.
1. Establish a Cost-focused Mindset: Examine costs (and associated operations) from multiple vantage points. One view is at a business level across departments and functions. In this case, a CFO or other team is responsible for this business-level initiative with input from stakeholders across the enterprise. It means moving beyond traditional downsizing in response to economic stress and establishing a system where cost management is an ongoing strategic activity.
2. Connect Costs to Outcomes: View every dollar spent as an investment in creating value for customers and in developing cross-functional capabilities to deliver that value. This requires a deep dive into budget discussions and prioritizing expenditures that align with strategic goals.
3. Adopt a Proactive Posture: Analyze your current expenses and evaluate the short- and long-term benefits of making operational changes. Importantly, ensure that you incorporate often overlooked aspects of cost, including:
- The financial impact of sustainability, including costs associated with the European Union’s “carbon tariff.”
- “Technical debt” and other overlooked costs associated with relying on older, siloed systems.
4. Gain Visibility Across the Organization: Stakeholders require the ability to understand how costs and associated processes operate throughout an organization. This is key to identifying potential redundances, hurdles, and overlooked costs – and establishing effective benchmarks.
5. Automate and Accelerate: Apply technologies like manufacturing simulation, process automation, and real-time automated insights to streamline design and production, supply chain management, and cost analysis. DX should be an ongoing strategy, focusing on long-term benefits rather than short-term fixes.
6. Rethink Your Supplier Ecosystem: Understand where to invest and where to outsource. Capitalize on your core differentiators and continue to build that capability in-house. In parallel, also recalibrate your supply chain with trusted partners and other vendors to gain efficiency, address gaps in skills/capabilities, and increase resilience against potential risks. This could include outsourcing select manufacturing processes and other non-core functions, and expanding R&D investments.
Leverage Cost as a Competitive Advantage
Achieving cost transformation requires a strategic blueprint and focused execution across the organization. For senior manufacturing executives, the path to effective business transformation is multifaceted. It involves a strategic shift in how costs are perceived and managed, and a commitment to continuous improvement and innovation.
By adopting a zero-based approach to guide the transition to strategic cost management, along with digitalization capabilities from aPriori, manufacturing leaders can not only navigate challenging economic conditions but also position their companies for long-term success.
Drive Profitability & Sustainability Through Cloud Collaboration
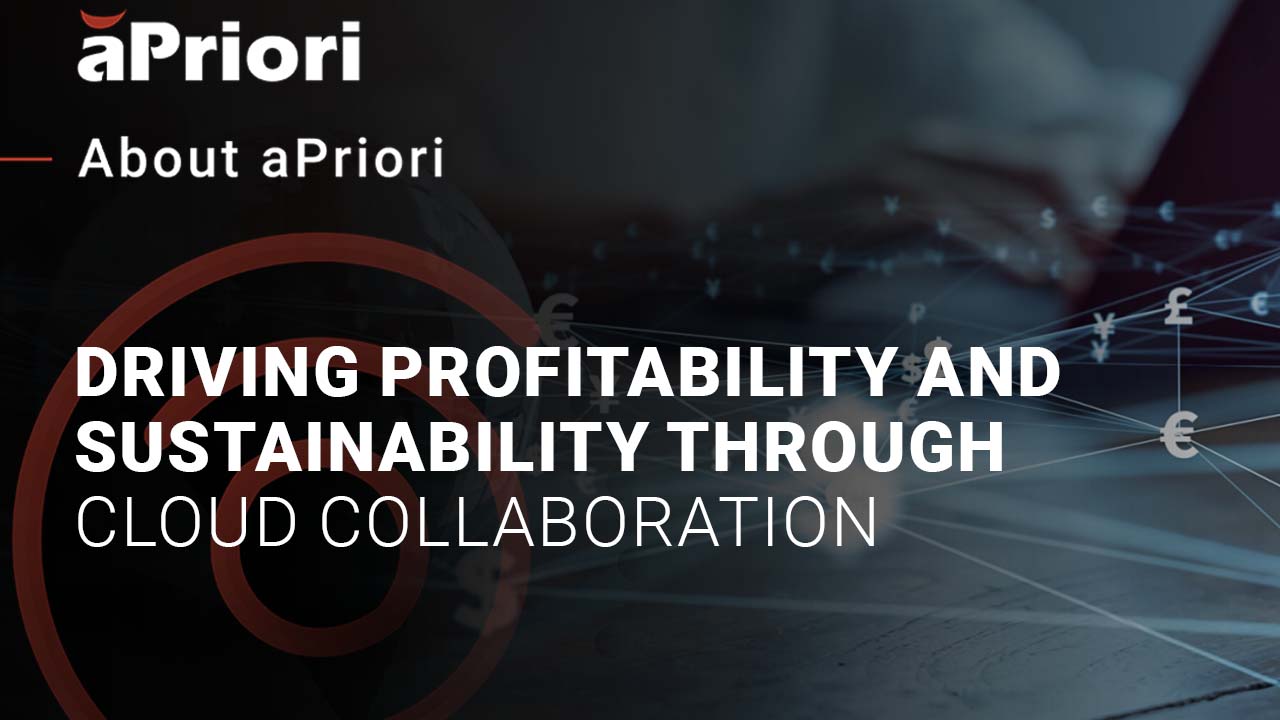