How to Reduce Time to Market for NPI with Digital Manufacturing Simulation
Behind each breakthrough technology on the market today is a complicated web of interconnected teams all charged with a singular goal: push the boundaries of innovation to deliver the right product at the right time and the right cost. As your product moves through its lifecycle, each functional area plays an integral part in getting to the finish line. When new product introduction (NPI) stalls in the design cycle or unforeseen challenges arise in sourcing or manufacturing, it risks missing target launch deadlines or running at a loss. So how do you reduce time to market for NPI?
A sophisticated digital manufacturing software with the capability to simulate real-world manufacturing environments for enhanced collaboration can eliminate long lag times, late-stage ECOs, costing discrepancies, and manufacturability issues on a rolling basis across your entire product lifecycle. Here are a few best practices for reducing time to market for NPI.
Practice Early-Stage Costing & Design to Cost Methodologies
The hand-off between design and manufacturing is not always as linear as we’d like. Signing off on a new product design is just the first of many complicated collaborations between your entire PLM team. Each time a product is passed back to design, valuable time is lost on the road to revenue. To keep things progressing, early-stage manufacturing simulation with the intention of performing scenario analysis and highlighting potential manufacturability issues, and avoiding unnecessary costs, also known as design-to-cost practices, is an essential way to reduce hand-backs and keep NPIs moving forward.
Imagine a process in which technology uses geometry extractions to allow design engineers to cost automatically early on within the concept design process. Running geometry extractions through a high-powered manufacturing simulation that provides accurate analysis of real-world manufacturing conditions can help you pivot early, avoid costly mistakes, and to design for manufacturability. When this manufacturing simulation is paired with an extensive regional or global data library tied to sourcing product components it enables quick evaluation of manufacturing options, both in-house and at supplier facilities.
A key point to all of this is the central database architecture required for keeping engineering, manufacturing, and sourcing teams all in the know and working collaboratively. As your NPI journeys through the product lifecycle, each department has a different lens through which they are viewing and changing the product. Without a centralized system in place, powered by state-of-the-art technology, silos, and insufficient tools bungle workflows and waste valuable time.
Provide Real Time Updates for Your Entire Organization
When introducing a new product, cost targets are often broken down by the varying functional units. Traditionally, there is a lack of transparency across groups and cost fluctuation across these groups. For example, the decision to switch from in-house to out-of-house production impacts the total cost burden of your product. The original design engineer’s cost projection becomes instantly outdated.
The best way to solve for fluctuating costs is to leverage digital manufacturing simulation software. Using your existing CAD model you can quickly re-generate cost calculations and a manufacturing simulation to provide real-time cost transparency to new projects. Here’s how aPriori’s latest solution, aP Generate unifies global product teams through real-time automation.
- Engineer designs components in CAD, checks files into the PLM system
- The PLM automatically checks for manufacturability of parts
- aP Generate integrates with the PLM, providing relevant cost content including;
- product cost feedback
- design for manufacturability score
- reporting stored back into your PLM
- Engineer is notified of the latest manufacturability score and cost
- From a link in the notification, the Engineer can review guidance and leverage those insights to make design updates or get support as necessary
Automate Production Optimizations Using Design for Manufacturability
A product’s manufacturability score is a complicated matrix of discrete manufacturing capabilities, machine optimizations, sourcing, and tool selection. While humans are capable of manually assessing each scenario individually, the bandwidth and time to production of these evaluations’ limits progression.
Automation has become a key differentiator between a product hit or miss. In particularly volatile markets this can be especially true. Utilizing the latest DFM technologies and digital factories, an issue manufacturing sharp corners or accounting for slower cutting speeds to accommodate more detailed tooling becomes more transparent. By bringing obstructions into focus earlier on in the design phase, you can plan for longer production times or find alternative design techniques to eliminate hard-to-manufacture components.
Simulated and automatic Design for Manufacturability practices can alleviate:
- Slow operations
- Contouring operations
- Obstructed surfaces
- Ineffective machining
- Early analysis of machining tolerance
- Whole size and radio tool selection issues
- In-house vs out of house manufacturing trade-offs
Leverage Digital Manufacturing Software to Accelerate Your NPI to Market
Managing a long and non-linear production lifecycle has been a major challenge facing the manufacturing industry for some time now. The advent of digital manufacturing software which centralizes, automates, and integrates within your existing PLM has allowed manufacturers to accelerate time to market and gain a competitive advantage.
A Practical Guide to Design for Manufacturability
Learn how design choices impact the production process, including impact on cost.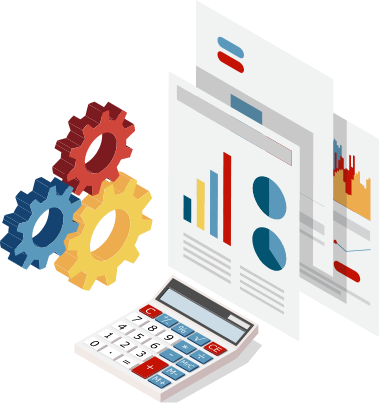