How to Get the Auto Industry Back on Track Despite Chip Shortages
Small computer chips have created a huge manufacturing roadblock over the last few years. In fact, it is estimated the global chip shortage cost the U.S. economy $240 billion in 2021. GM alone estimated $2 billion in lost revenue because it did not have the semiconductors needed to complete new car and truck production.
Electric vehicles (EVs) were especially vulnerable during this shortage because they can require twice as many semiconductors as their combustion engine counterparts—between 2,000 to 3,500. Because chips weren’t available, Ford, Nissan, Tesla, and other companies delayed their EV and hybrid launches.
To help automobile/EV manufacturers address the challenge, aPriori has highlighted potential opportunities overlooked in the supply chain—and outlined practical steps to get back on track through digital manufacturing simulation.
What’s Causing the Auto Chip Shortage?
The pandemic effectively froze many industries and forced semiconductor fabs and other manufacturers to lay off employees and reduce (or stop) production. Additionally, car manufacturers and their suppliers responded to the dip in demand by canceling orders for semiconductors and other components. Because the auto industry represents less than 10% of global semiconductor sales, chip fabs easily offset this loss by filling orders for computers, electronics, and other devices.
As the economy recovered and car manufacturers refocused on production, many companies realized their semiconductor suppliers didn’t have the capacity to deliver immediately because they were working overtime to serve consumer electronics and other industries.
Because semiconductors can vary significantly by size and capacity, a chip for a laptop isn’t typically used for a car brake system or an LED dashboard. So, semiconductor fabs traditionally create new chips for the auto industry. It typically takes three months‘ minimum to convert raw materials into razor-thin chips. Once the chips are produced, supply chain managers must then navigate transportation potholes and delays to deliver the chips to suppliers and manufacturers.
How long will it last?
The auto chip shortage is exacerbated domestically because 88% of semiconductors are manufactured overseas. The US Congress recently pledged $52 billion to increase national semiconductor production, but building high-tech chip plants is a long, expensive process that won’t provide short-term relief to American-based industries.
Projections vary significantly regarding the length of this shortage. Deloitte indicated that the chip shortage should be over by the end of 2022. Intel believes it could take several years to resolve the global semiconductor shortfall.
Cars now run on semiconductors
New gas-powered cars are typically packed with semiconductors for safety (blind-spot detection and braking), performance (monitor and regulate motor parts), and comfort (seat control and connectivity). In EVs, battery management, motor control, and advanced safety features fuel the need for more semiconductors. Autonomous driving capabilities—and associated sensors—also require more chip-based electronics.
Jumpstart Innovation with Digital Manufacturing Simulation
There are pockets of opportunity for automotive companies to get the computer chips and related components needed for production. But sourcing challenges will likely require companies to make strategic product decisions quickly. To help address this requirement, digital manufacturing simulation software accelerates product design with confidence and provides insights for global sourcing and production decisions.
Automotive clients use aPriori’s Digital Factories to conduct design for manufacturability (DFM) and design to cost (DTC) analysis to vet supply chain alternatives, reduce production time, and more.
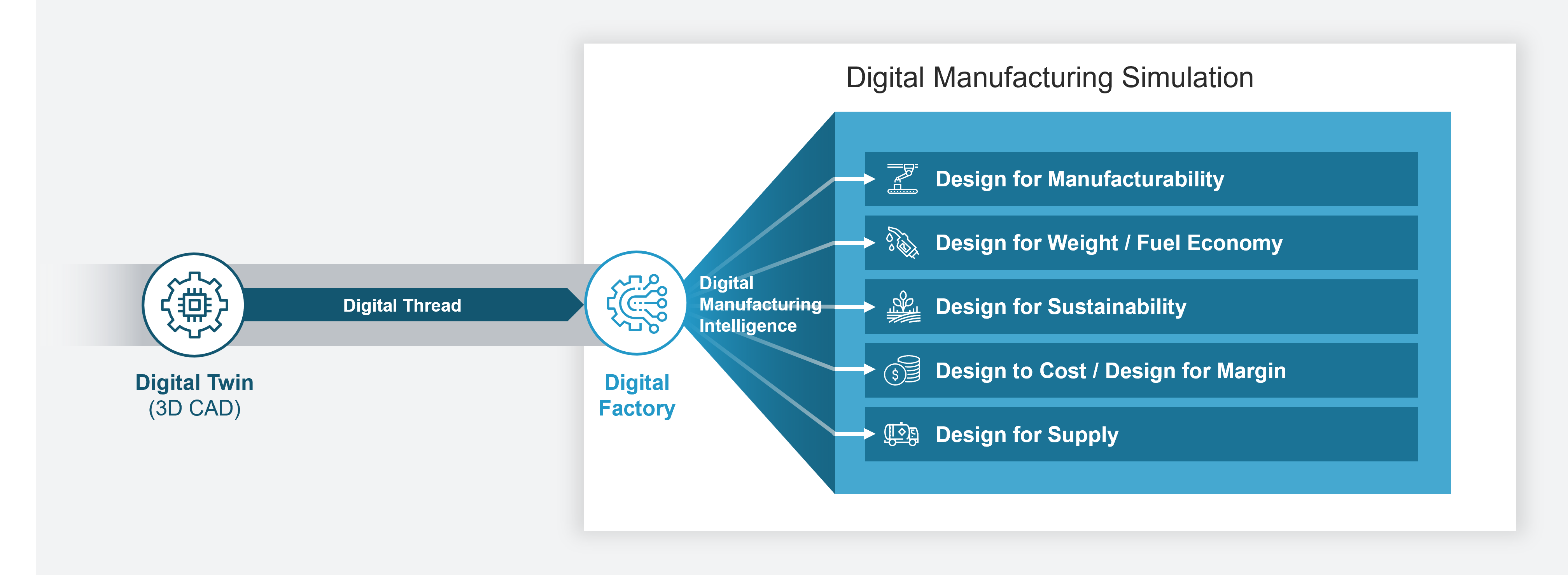
Companies use a digital thread to connect product design files (3D CAD/digital twin) to a digital factory (see Figure 1). This process fosters collaboration, ensures that everyone is using the latest product information, and maintains a single source of truth (version control). Using manufacturing-focused simulation capabilities, the digital factory enables sourcing and quality teams to analyze 3D CAD data and investigate the impact of changing designs, selecting alternative components, and using new manufacturers to address product considerations ranging from performance to profitability.
Teams use digital factory capabilities to analyze product criteria, including:
-
Alternative part/component evaluation
-
Manufacturability (production speed, efficiency, and reliability)
-
Weight, fuel efficiency, and related product properties
-
Sustainability
-
Design for supply (availability)
-
Profitability (incorporates the component, assembly, and other costs)
Apply Digital Manufacturing Simulation Throughout the Lifecycle
Applications and examples for the automotive industry include:
Simulate and verify design changes rapidly
Many car companies are pursuing new vendors to address the semiconductor auto chip shortage. An alternative supplier, for example, may provide the semiconductors as part of a larger printed circuit board assembly (PCBA) manufacturing solution. If the automotive brand traditionally purchases semiconductors and PCB assembly services separately, its sourcing teams need the tools to make an “apples-to-apples” cost comparison—and determine what it should cost to purchase the entire assembly.
Component scarcity and deliverability timelines may also require companies to explore BOM alternatives. This could include evaluating polymer or film-based capacitors to replace ceramic MLCCs or replacing other back-ordered components or parts.
Digital manufacturing simulation helps to reduce physical prototyping requirements, accelerate pilot production tests, estimate the cost impact of alternatives, and eliminate costly and time-consuming problems during full-scale manufacturing.
Flag potential manufacturing problems during design
Manufacturing simulation can also help identify manufacturability issues that could lead to excessive scrap rates and/or slow-cycle times. Identifying potential manufacturing issues early in the development process provides more time to make design updates instead of incurring costly production mistakes. Companies also use the digital factory to help assess time and cost alternatives for product assembly.
Identify the right suppliers
By integrating digital manufacturing simulation technology, you can filter suppliers based on variables such as regional labor rates and machine availability.
The aPriori digital factory supplier database provides cost structures in nearly 100 global manufacturing regions to provide users with accurate, updated data. As an example, a business can quickly evaluate other supply chain partners based on specific parameters. Or, get a comprehensive understanding of total costs if a product is sourced from Mexico, Taiwan, or Brazil.
With this information, sourcing professionals can guide the selection of a vendor able to support on-time production and help match each component to the most efficient supplier possible.
The earlier an issue is recognized, the easier it is to find an optimal alternative, such as sourcing a different supplier.
Streamline quoting with “Zero-RFQ”
Companies need to move quickly once they find the right vendor. Automotive companies require a collaboration engine to understand suppliers’ granular manufacturing costs and capabilities. For favored suppliers, models can be tuned to enable a “Zero-RFQ”—and issue purchase orders to a supplier with full confidence in a first-pass quote.
Take the next step
When implemented effectively, digital transformation eliminates silos among design engineers, sourcing, and manufacturing. The result is new levels of collaboration, speed, and confidence in decision-making. Automotive innovators with the agility to design new products with an interchangeable BOM will be well-positioned to avert supply chain roadblocks and capitalize on new vendor sourcing opportunities.
Zero-RFQ Dramatically Accelerates Sourcing Process by Automating Supplier Selection
Alstom & aPriori Case Study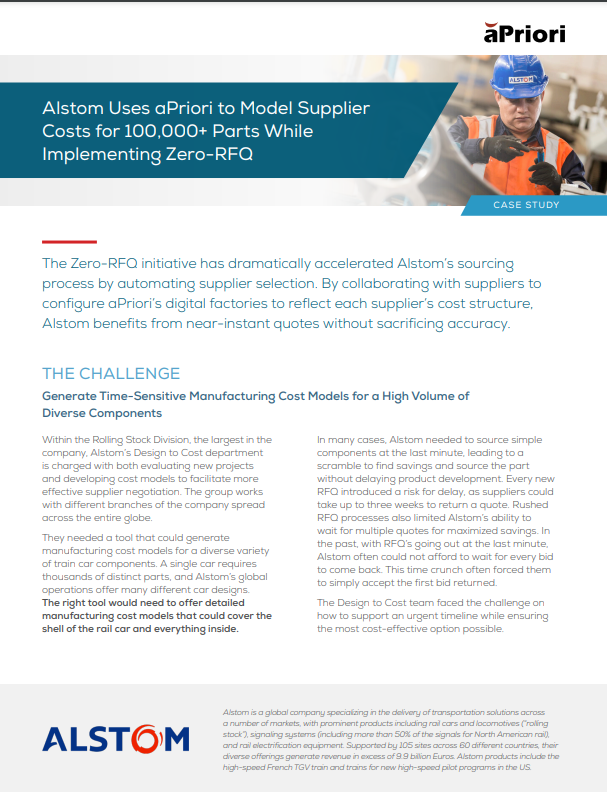