June 29, 2022
Staying Ahead of the Global Chip Shortage
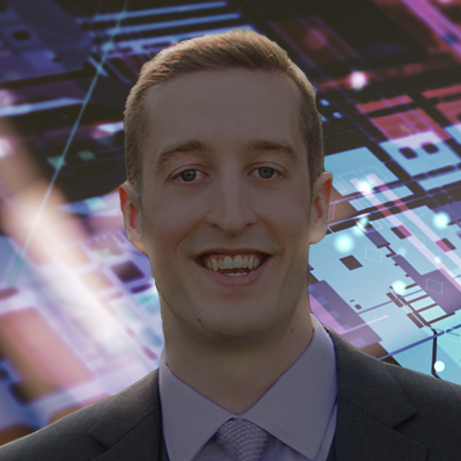
Transcript
Leah Archibald: The supply chain issues that have plagued manufacturers of electronics over the past two years are not going away. There still aren’t enough chips on hand to fulfill the needs of all our smart devices, and engineers have had to redesign current products to use whatever components they have on hand. Even worse, they’re put in a the challenging position of trying to design future products without knowing what components might be available. How can engineers meet the needs of today and also stay ahead of the chip shortages of tomorrow?
My guest is mechanical engineer Sam Ellis. He started his career at Raytheon and led engineering teams at companies like Micross components, providing mission critical chips to manufacturers in the Defense, Aerospace and Telecommunications industries. He’s here today to talk about how design engineers can adapt and thrive in the new world of question mark components.
Sam Ellis, welcome to the podcast.
Sam Ellis: Thank you for having me, Leah. I’m excited for this the session today.
Leah Archibald: I wonder if you could start by giving us an example of what it looks like when data sharing really works to help teams adapt to components shortages.
Sam Ellis: If I could set up the dream scenario, this is what it would look like. I’m a design engineer. I’m working on my printed circuit board assembly. I’m selecting my components. And I’m just living in my design software. I don’t want to leave that. Outside of my conscious attention, there is a system that ties into my design software. As I’m putting my bill of material together, it’s extracting all of those components that I’ve selected for my design. It’s taking those components and parsing them through a supply chain analysis tool. It’s looking at what’s the availability on these components. What’s the lead time? How many suppliers are offering these? What’s the supply chain risk? That’s all happening automatically in the background. And then when problem components bubble up to the top, the sourcing specialist or the procurement specialist gets alerted, and they can now spend their valuable time looking at only the 5% of components on that BOM that are going to be problematic. Then they can come back to engineering and have a conversation: Let’s look at some other options here. Is there a way we can use other components.
Leah Archibald: So, more information sharing and more automated alerts take less manual work for the designer. And then there’s less resting on your shoulders.
Sam Ellis: Exactly.
Leah Archibald: Alright, so here’s a different question: How can design engineers build more flexibility into the designs that they’re creating? Because even in the best-case scenario, there’re going to be changes in the future.
Sam Ellis: Design flexibility is going to be largely driven by the function and eventual use case of the product. Back when I worked in the defense industry, there were a lot of restrictions. These include what lead materials are acceptable and what environmental requirements have to be met. There might not be commercial off-the-shelf parts that meet those criteria. But as a design engineer, you should try as best as possible to avoid custom or sole source components. You don’t want to lock yourself into one option – you want to be able to specify potential alternates on that bill of material. So while you can’t predict the future, you want to give the procurement team or the contract manufacturer as much diversity on that bill of material as possible so that in the changing landscape they can go and fetch what components are available.
Leah Archibald: How hard is it to think about different materials or components that you could use? How hard is it to test those scenarios, and how hard is it to play one scenario against the other in your mind without sacrificing the overall quality of the product?
Sam Ellis: There are a range of difficulties, and it comes down to the level of component. If I’m looking at a passive component such as a resistor or a capacitor, oftentimes it’s enough to just specify a value instead of a specific part number. There are tens to hundreds of different manufacturers that are all making similar components that can meet that criteria. In that case, the contract manufacturer can go and fetch any one of those. That would be called a drop-in replacement. I might have one specified and the contract manufacturer, if they can’t find that one, can literally go and get 10 other part numbers and just drop one right in without a problem. It doesn’t have to come back to engineering for evaluation. It’s going to work perfectly. That’s the easy scenario.
Where it gets a little more complicated is in those active components like the micro circuits. For the chips, there’s not as diverse of a supply chain. There are not as many manufacturers. Producing those types of components gets a little more challenging.
Leah Archibald: So, what do you do in those challenging situations?
Sam Ellis: Even though there are not as many manufacturers, they generally still do produce a range of values or a range of different criteria for each component. There could be an automotive grade component. If you’re not an automotive, you might not need that high of a grade of a component. You might not need to go to the extensive requirements at that level. You could use a lesser grade, but then still have that automotive grade as a backup or an alternate.
Sometimes there are different package types. I have a chip which essentially sits inside the package that will be placed on the printed circuit board. That chip has all the functionality that the design needs, but it could be packaged in multiple different ways. A common one is an 8-Lead SOIC that’s a surface mount component. But that could also be packaged in a different type of component that’s installed as a through-hole instead. The problem there is that there are obviously preferable packages. A supplier may produce two or three times more of one package type than the other. But in the end, it comes down to the availability. If there’s a certain package type that’s more available, and you’re still early in your design process, look to use that one instead.
Leah Archibald: So, some packages are going to be necessary based on the tolerances of a particular industry, like so for example Defense or Automotive might have smaller ranges of tolerances, but if you’re in consumer products that might not be as limiting a factor. So in your initial designs, you can add some specifications for more leeway?
Sam Ellis: Exactly. That’s something that happens often today. When procurement can’t find a specific component, they find one that’s similar. It might have some different high intolerances, so in that case they go back to engineering say: Hey, does this still work with our design? If so, can we use that instead?
So instead of doing that on the back end, when I’m designing my product, I should plan for that flexibility. I should specify what is the lowest or widest tolerance range that’s acceptable for my component. I want to use that as my primary. And then I can specify some alternates that have some tighter tolerances or some higher specified grades that are still an option. Maybe they’re more expensive, but at least they’re there, and procurement doesn’t have to break into design again – they know that this component is going to work and they can use that as a replacement.
Leah Archibald: So when I ask you the question, how do you build flexibility in to your design designs, you’re literally saying build in flexibility. Like when you create the 3D CAD model, you actually put in the metadata that says: this is the flexibility.
Sam Ellis: That’s a perfect way to put it. There’s a term called the bill of material health. It’s a good term too that trends with that flexibility. The more flexibility you have in your design, the healthier your bill of material is going to be because there’s that range of products that you can grab.
Leah Archibald: And if you have this information in your design system and if that data is shared with sourcing, then you eliminate the step of sourcing having to go back to design and saying: Can you give me some other flexible options? If you literally build in the flexible ranges at the beginning, you don’t have to do this back and forth dance.
Sam Ellis: That’s exactly right. In the extreme sense you can even go for a different printed circuit board design. You might have one critical component and only one supplier makes it. So you have to use that component. But it might come in package type A and package type B. You could potentially design two different circuit boards, one for a package type A, one for package type B, and build in some flexibility around your critical component. That’s not going to be preferred because it adds complexity to a design, but it can be a last ditch effort if you’re stuck using a critical component.
Leah Archibald: And it’s another way of giving options to the team in the future. Your first level option was: Can I make it in a whole bunch of different places in the world. Your second level option was: Can I deliver it in different packages? And your third level option was: if I can only make it through one supplier, can I make it on different machines or using different processes so that your supplier has that flexibility.
Sam Ellis: And again, it comes down to setting up some kind of automated system. A design engineer doesn’t want to sit there and for every component in a 250 component bill of material and find 10 alternates for each one. That’s going to be a waste of time. So we’re back to the importance of automation. Use a solution like aPriori that can provide all of those potential alternates that might work, and then rank those alternatives.
Leah Archibald: I hear the advantage that having a really robust platform for flexibility and storing metadata about designs can give to the engineers. And I see how it’s taking some of the headache away from sourcing, But when you zoom back to the manufacturer as a whole, what kind of competitive advantage can this information sharing system give to the manufacture as a whole? Because when we talk about staying ahead of the global chip shortage, it’s really the competitiveness of the whole enterprise that we’re talking about here.
Sam Ellis: In my mind, it all comes down to speed to market. If you establish this system of collaboration between those two different groups, both teams have the information that they need. They don’t have to spend too much of their time with manual inputs. The information is available earlier to not only both to Engineering and Sourcing, but also to the management team. So yes, I could be working on one product, but the management team is going to be overseeing multiple different products. They are going to be able to see if there can be some way to consolidate the list of problematic components. And then for those that they can’t get rid of, we know earlier in the design phase, and we’re not running into an unforeseen 32-week lead time when we go to the contract manufacturer.
Leah Archibald: So when I ask you what is the competitive advantage that an information system provides to the manufacturer, you’re saying that it’s not a new competitive advantage. It’s the same old competitive advantage – time to market – but we’re making it happen faster through this new technology.
Sam Ellis: Yes, that is perfect. Couldn’t have phrased it better myself.
Leah Archibald: Well, this has been extremely enlightening. Sam Ellis, thank you so much for joining me on the podcast today.
Sam Ellis: Pleasure to be here. Thank you for having me.
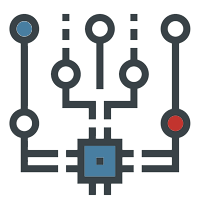