Driving Business Value through Digital Automation and Manufacturing Intelligence
The global economy has faced a seemingly endless series of challenges during the past year. And most leaders don’t expect this trend to let up. According to a 2021 Deloitte report, more than three-quarters of executives interviewed expect their organizations will change more during the next five years than during the past five.
To navigate the “new normal,” digital transformation (DX) is providing organizations with the added speed and agility to remain competitive. In manufacturing, DT is propelling some new products to market 20-40% faster by connecting operations and accelerating key phases of the product development lifecycle.
The manufacturing industry is more dynamic than ever with digital-born startups taking the market by storm. SpaceX, Rivian, Arrival, and Canoo are just a few examples of disruptive digitally born natives.
And some established brands are using digital solutions to grow. John Deere has infused artificial intelligence (AI) and computer vision into its products for precision agriculture. During harvesting, farmers monitor operations and adjust machinery in real time using John Deere’s connected solutions. Company executives have credited Deere & Company’s digital strategy with helping to increase net revenue by 19% year over year in its fiscal Q1 2021 report.
Adopt Digital-focused Business Capabilities
Many organizations are focusing their post-pandemic planning on integration and collaboration, automation, and manufacturing intelligence. But it isn’t easy for established companies to become digital. Seventy-five percent of senior executives surveyed by Accenture say their business functions – including R&D, engineering, production sourcing, and operations – often compete against each other instead of collaborating on digitization efforts.
Strengthen Supplier Relationships
The evolution of the buyer-supplier relationship illustrates how business is changing. Two decades ago, cost was the primary driver during negotiations. More recently, many manufacturers have been expanding buyer-supplier collaboration by sharing additional operational insights and offering a greater level of transparency.
Today, more manufacturers are forming true supplier-buyer partnerships that require a shared understanding of strategic goals and high transparency regarding capabilities, resources, and costs. With a shared business outcome and the ability to leverage joint expertise, both parties are invested to succeed.
Companies with this advanced supplier-collaboration capability tend to outperform their industry competitors by nearly 2X, according to McKinsey research. Recently, automaker Ford announced a strategic collaboration with chip company GlobalFoundries to shore up its supply of core components. And Northrop Grumman selected Mynaric as a strategic supplier to gain preferred access to Mynaric technology and to co-develop new space laser communications technologies.
“Sourcing 2.0” is also providing advantages for businesses with traditional supplier relationships. Alstom provides rail cars, locomotives, signaling systems, and other transportation solutions in 60 countries. By generating supplier-specific manufacturing cost models directly from its 3D CAD files, Alstom’s purchasing team can now award purchase orders to suppliers based on aPriori’s output to avoid lengthy negotiations. Alstom estimates this “Zero RFQ” process is saving 40% on recurring costs. (Read the Alstom case study or watch the video.)
Accelerate with Automation
Procurement isn’t the only critical operation that’s changing. Product lifecycles are now much shorter. Simulation and prototyping advances are helping increase pre-launch maturity, reduce late-stage design changes, and minimize post-launch product issues. And the evolution to an agile stage-gate process infuses more collaboration – and faster release cycles – into product development.
And leveraging data across the product lifecycle is also critical. We’re seeing more companies integrating their enterprise systems and introducing data lakes to share information across product development and sourcing applications. Many companies are incorporating design for manufacturability and cost insights during the product design cycle instead of trying to capture higher margins through value engineering after a product is launched.
Apply Manufacturing Intelligence
According to PWC, 61% of digital champions have already digitized their product development process. And by 2025, PWC sees the majority of digital champions co-creating their products, leveraging digital simulation, embracing product portfolio management, incorporating data analytics and AI, and utilizing digital prototyping, agile development, and digital twins.
Just like procurement is moving to become part of an agile ecosystem, so is engineering. Companies are becoming a part of a broader integrated partner ecosystem that focuses on internal and external co-creation with agile and digitized development processes and methods.
Manufacturing intelligence is a critical part of a digital thread that can guide design decisions from early design to ongoing production. Manufacturing and cost intelligence solutions are helping manufacturers accelerate their digital transformation and drive automation. By helping to connect the product development production silos, individuals can work faster and more efficiently across departments.
And by using manufacturing intelligence downstream that was created early in the design process, companies establish consistent manufacturing results across the product development process. All of this helps accelerate business outcomes.
Use Digitization to Accelerate Manufacturing
Cloud computing, AI, and automation are key building blocks for digital transformation. But the value of digital transformation depends on how organizations leverage these technologies to improve business outcomes.
Effective manufacturers are using new capabilities to unlock product, sourcing, and other insights from legacy systems and using this insight to make fast informed decisions throughout the product development lifecycle. The ability to combine precise digital twin product specifications with “if/then” sourcing and manufacturing simulation capabilities illustrate the power and flexibility of DT. And automation can play a key role in helping to tie manufacturing business process together.
aPriori’s digital manufacturing solution provides real-time intelligence to make product design, sourcing, and manufacturing decisions quickly and with greater accuracy. Our manufacturing intelligence plays a key role in accelerating business operations by tying product design and manufacturing operations together. Successful teams are using DX technologies, including aPriori to gain actionable insights for teams throughout the product development lifecycle to meet evolving market demands quickly.
See aPriori In Action
Learn how aPriori can help you to adopt digital focused business capabilities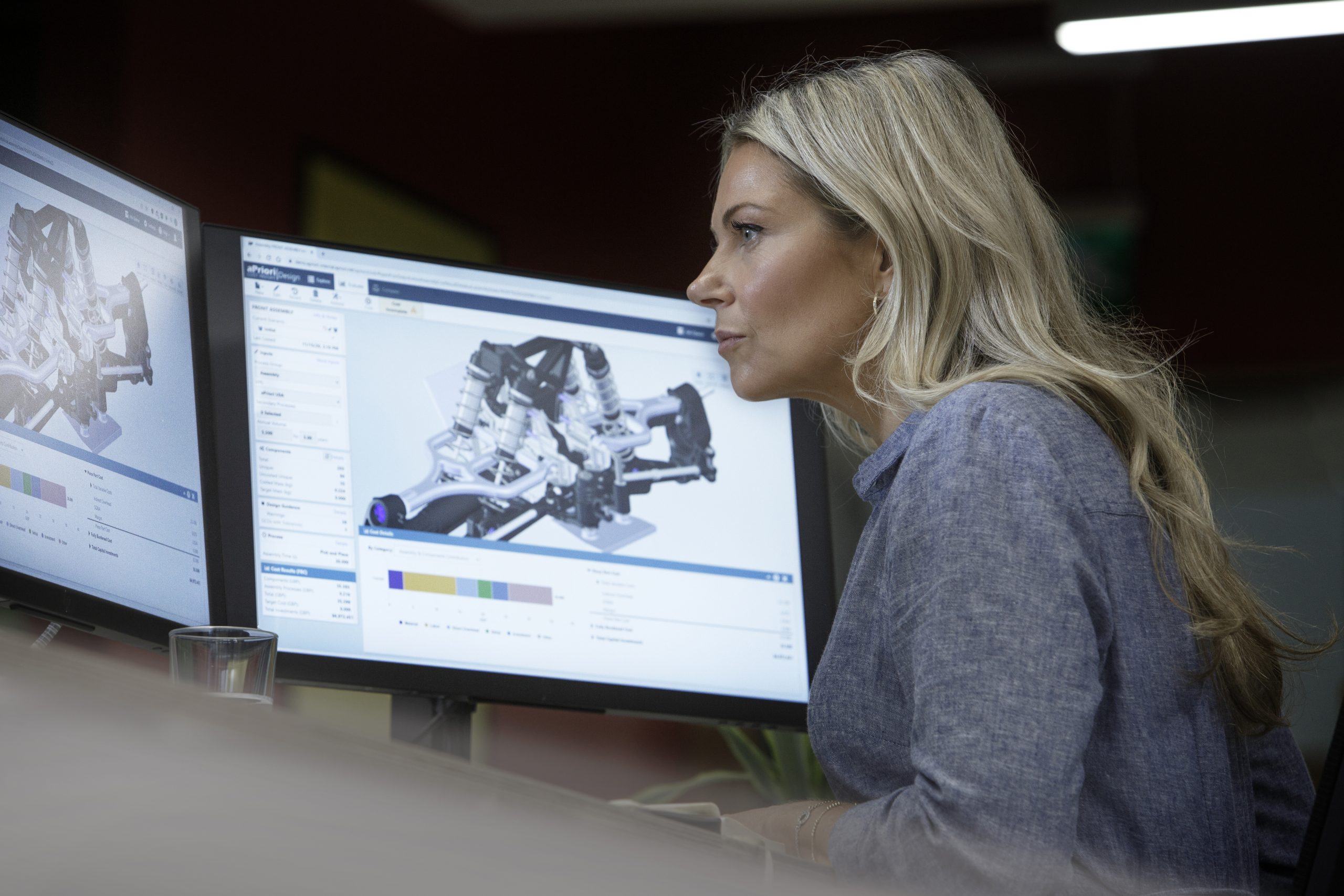