Retool the Auto Manufacturing Process to Save Time & Money: 5 Strategies
Key Takeaways:
- Cost and delivery necessitate early design and production insights for automakers
- Manufacturing process models improve manufacturability, costs, sustainability, supply chain resilience, and agility
The Full Article:
The automotive industry is under pressure to launch new models quickly that address evolving consumer demands. This requires digital solutions that provide a high degree of accuracy and efficiency via manufacturing process models. These solutions should optimize manufacturing operations, profitability, and sustainability. Companies that can simulate and enhance their various types of manufacturing processes are better positioned to meet tight launch schedules, improve the functionality of finished goods, address risk, innovate faster, and increase profits.
aPriori can simulate a manufacturing business’s processes and deterministic routings. The goal is to optimize different types of manufacturing processes based on cost, sustainability, and manufacturability requirements. For example, sheet metal, typically steel or aluminum, is shaped using a variety of processes like stamping, die cutting, and punching. Selecting the right machines and processes can have a significant impact on speed and cost.
Using aPriori’s discrete manufacturing process models, engineering, purchasing, and production can explore manufacturing alternatives down to the machine level.
Digital Manufacturing Simulation is Key to Reducing Cost and Manufacturability Issues
A recent PwC 2023 CEO Survey revealed that 76% of CEOs plan to invest in process and systems automation in 2024. It underscores why executives should optimize lean manufacturing process models via advanced technologies like aPriori.
Automakers must identify potential cost outliers and manufacturability issues upfront even before the design process begins. Cost constraints and tight delivery deadlines pressure automakers to ensure design and process manufacturability throughout product development.
Simulating production, like batch process manufacturing and continuous process manufacturing, before actually going to production enables product development teams to collaborate in real-time, circumventing cost and manufacturability issues. Identifying and mitigating issues via the digital product twin (design), digital process twin (manufacturability), and digital factory (production) creates a seamless digital thread. Executing it early in product development is essential, saving time and money.
Engineers can validate the production process and improve quality control before physical implementation. By simulating the manufacturing processes and deterministic routings, engineers can identify potential issues (e.g., inefficient production sequences, and other repetitive manufacturing issues) before they ramp up production. This enables them to fine-tune product designs, adjust machine parameters, and improve overall process efficiency.
aPriori applies its physics-based process models and deterministic routings to 3D CAD models or the automaker’s virtual representations of physical products, gaining manufacturability and sustainability insights in the early design stages. Companies can then innovate to reduce cost, CO2e emissions, and delays (e.g., engineering change orders [ECOs]).
5 Incentives to Optimize Manufacturing Systems with aPriori
Here are five reasons why automakers should leverage them:
1) Manufacturability: Automakers must ensure vehicles meet quality standards. Manufacturing techniques such as stamping, injection molding, machining, and casting are among the most common parts used by automakers. Simultaneously, automakers want to minimize the number of unique parts required to produce components (e.g., electric vehicle [EV)] drive trains). This reduces assembly and manufacturing costs during vehicle development. This base includes cost, quality, and sustainability. Automakers often are under pressure to boost productivity, necessitating ECOs reductions too.
aPriori’s digital process twin determines the best manufacturing method via manufacturing processes and routings simulations (e.g., injection moldings). Each product development stage can consider alternatives down to the machine level, identifying the best production process for manufacturability.
2) Cost: By utilizing manufacturing process models, companies can quickly locate parts that could be more cost-effective by using a different production method. For example, aPriori can automatically analyze and identify cost drivers for large sheet metal parts, comparing production on multiple machines of different sizes. It saves money upfront because there is no need to start with a physical factory or machinery. They also get a better handle on overhead costs (labor, electricity, etc.) required in specific production areas.
Production planning and simulation can be done virtually, reducing capital expenditures and time. Utilizing aPriori’s manufacturing process models early in product development ensures automakers save money downstream. This step is essential since automakers need to cost early in product development.
“Having a tool like aPriori allows your design and sourcing teams to say, ‘I have this part. I think there may be a better way to manufacture it.’ Instead of having to redesign the component, send it out to RFQ, and play the waiting game. We can make small changes to our digital simulation to skip all of that.” An aPriori Customer
3) Sustainability: A product’s early design determines 80% of its environmental impact throughout the lifecycle. Automakers can create sustainable components with accurate manufacturing process models, optimizing performance vs. weight ratio (e.g., lightweighting). Consequently, fuel consumption and total cost of ownership are lowered.
Automakers transitioning to EVs must fully understand the manufacturing process before moving to production. To evaluate their supply chain’s CO2e across the value chain (Scope 3), manufacturers can use the digital factory twin, which creates a virtual representation of supplier factories and their own manufacturing locations.
4) Supply Chain Management: For automakers, the ultimate goal is to get to automated quoting (also known as Zero RFQ) as one aPriori customer did. Design can be impacted, ultimately influencing all the other aspects (manufacturability, cost, sustainability, and agility/speed to market). Manufacturers can simulate production based on various raw materials, machines, and processes, improving their supply chain risk management. aPriori’s 87 regional data libraries globally facilitate faster quoting times, improve supplier relations and negotiations, and ensure manufacturers can get the necessary parts quickly and cost-effectively.
As more companies grapple with supply chain delays, they will work towards integrating them into their operations rather than viewing them as a stand-alone. Being able to quickly understand the impact of the design on your supply chain intrinsically creates a resilient one.
5) Agility and Time to Market: Design engineers and production are no longer siloed and can now accelerate and improve product development throughout the lifecycle. Digital manufacturing—the digital thread—enables all product development players to work from the same centralized data and insights, facilitating more cohesive communication and decision-making. Manufacturing process simulation removes the traditional bottlenecks between product development teams and optimizes the production rate for launch.
Automakers are no longer physically limited via the production facility. Be it the design engineer, supplier, or factory floor worker, the production process now can be tapped into the digital factory anywhere. Transparency, workflows, and time to market improve. For one aPriori customer, manufacturing simulation created an invaluable EV opportunity to innovate, streamline processes, and get their vehicles to market faster. Additionally, the manufacturer met sustainability initiatives while identifying millions of dollars in potential product cost savings.
aPriori: Where the Rubber Meets the Road
The expression “where the rubber meets the road” applies to automakers. Those employing manufacturing process models can make important discoveries through meaningful analysis. They bridge the divide between planning and execution, keeping automakers’ final product cost and delivery on track.
Are Net-Zero Goals a Pipe Dream? Not with aPriori
Weigh cost vs. carbon tradeoffs with our sustainability insights, reducing CO2 and improving profitability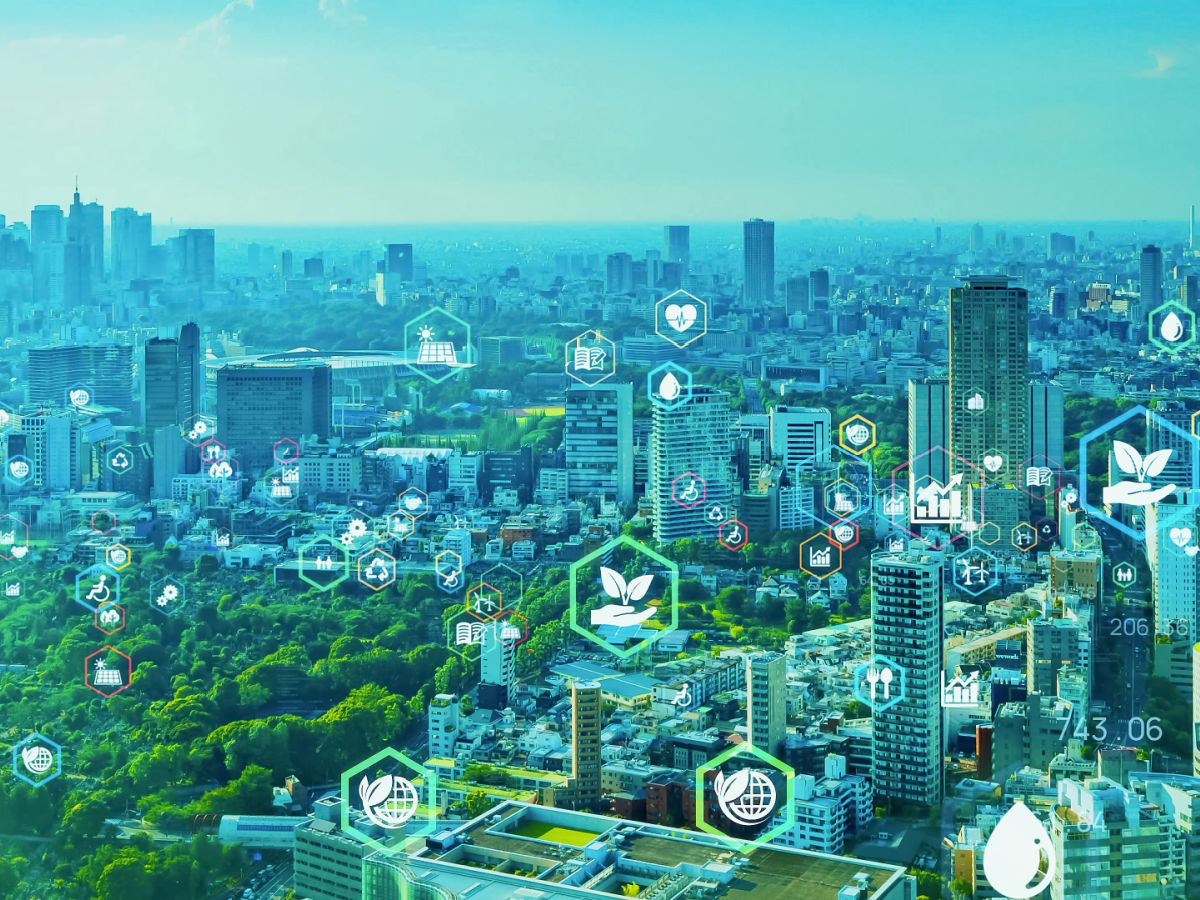