4 Ways to Accelerate Manufacturing Design
Key Takeaways:
- Product design is the seminal point in determining final product cost, manufacturability, CO2e, and time to market
- aP Design can optimize the entire product development lifecycle, ensuring a competitive advantage for manufacturers
The Full Article:
Today, manufacturers have to do more with less. That means more competition, pressure, sustainability compliance, disruptions, and higher costs, with fewer design engineers and less time and resources.
It requires a more holistic approach that begins from a product’s inception. It is especially critical when you consider the following:
- Approximately 80% of a product’s final cost is locked in during the design stage
- 80% of a product’s environmental impact is determined by its earliest design
- Late-stage design changes and engineering change orders (ECOs) account for significant cost overruns and, worse, missed launch dates
With the right digital solution, many cost, production, sourcing, and sustainability issues can be resolved in manufacturing design without slowing time to market. Let’s explore four areas where manufacturing design issues can be mitigated and time to market accelerated.
4 Ways to Accelerate Manufacturing Design
The 2024 Deloitte Manufacturing Industry Outlook notes that manufacturers continue to face economic uncertainty, skilled labor shortages, supply chain disruptions, and pressure to innovate sustainably.
Here are four tactics manufacturers can employ to address these issues without impeding time to market:
- Early Cost Estimation: Early design stage cost breakouts can be extremely difficult and time-consuming to identify without visibility into the financial impact of product development decisions – including material selection, design tolerances, and manufacturing processes. It can be difficult to isolate, measure, and model for cost analysis. As a result, it often simply is not done or even on the radar of many manufacturers. Others will rely solely on supplier quotes for product cost approximation or not even consider until the cost engineer calculates cost post-design when it could be too late to remediate. Integrating cost estimation in the design phase can facilitate faster time to market. aPriori provides real-time cost insights based on design decisions, allowing you to optimize for cost-effectiveness early on. Forbes notes that more companies are adopting data-driven decision-making in cost engineering this year. Gartner estimates that 65% of B2B sales organizations will move to data-driven decision-making by 2026, employing technology that ties workflow, data, and analytics together. Predictive, data-driven analytics can better forecast possible cost overruns with real-time insights and recommendations to course-correct earlier in product development. aP Design helps facilitate this process, optimizing designs for cost, manufacturability, and sustainability automatically and simultaneously.
- Design Optimization: Aesthetics and performance aside, design errors and functional redesigns can result in ECOs, slow time to market, and cost increases. AI-powered design and sourcing insights like aPriori can identify potential design issues and provide recommendations to reduce process and production complexities, lead time, and manufacturing costs. aP Design delivers scenario criteria updates across multiple design iterations (e.g., fully burdened cost, CO2e, DFM), reducing redesigns and late ECOs. Materials, production processes, and cost targets can be optimized at this most critical stage. Insights provide suggestions to lower costs without compromising product quality. Manufacturers can leverage the digital product, process, and factory twins, which combined, create the digital thread in the design process and throughout product development.
- Supplier Collaboration: The design stage is the optimal time to engage with suppliers, ensuring alignment on cost-effective materials, processes, and lead time. KPMG revealed that 71% of global companies highlight raw material costs – including material type, utilization, and standard and non-standard stock size– as their main supply chain threat in 2023. Though it’s obvious, designers rarely consider material availability or delivery timelines. They might not have the ability to factor them in or they simply are not incentivized to consider them. Without design insights, some raw materials and their associated costs could be missed. Design for manufacturing (DFM) offers more cost-effective material alternatives, and leveraging the digital thread ensures product development team members are kept in the loop regarding material, manufacturability, or cost issues to proactively address them. Teams can also apply design for assembly (DFA) to streamline production and reduce cost with products that can be easily assembled by optimizing component placement, materials, and processes like machining. For example, aP Design automates 3D CAD design analysis of parts and assemblies, quickly evaluating the design based on the geometry, manufacturing method, and the location of the manufacturing facility. Design engineers can significantly avoid unnecessary product costs, reducing the risk of delays and accelerating time to market. Market fluctuations also influence product cost drivers. A fact-based tool like aPriori’s Regional Data Libraries (RDLs) help manufacturers uncover supply chain costs across 87 global regions and improve supplier collaboration and negotiations.
- Scenario Analysis: Simulating various designs, manufacturing processes, and factory selections via digital twins can detect cost outliers and manufacturability, sourcing, and sustainability issues early in product development, ahead of any time-consuming and expensive virtual prototyping through FEA or CFD. design and manufacturing process feasibility can also be assessed in a virtual scenario rather than too far down the product development cycle. As a result, fewer late-stage ECOs are required, risks are identified and mitigated sooner, and time to market is not impeded. Moreover, aP Design’s scenario analysis provides real-time data, allowing all team members to proactively respond to any speedbumps, improving upon the product’s development and accelerating time to market. Comparative analysis of multiple design variants, alternative materials, and sourcing options is also available. Assembly scenario data in a single view is accessible to all team members.
Leveraging aP Design’s interactive guidance allows enhancements to be made quickly to optimize designs and address potential bottlenecks and other risks.
Fail Fast, Succeed Faster
Agile processes, such as those within AI-powered design and sourcing insights, are more iterative, allowing product development teams to identify potential failures sooner, so they can succeed faster.
aP Design uniquely provides critical feedback with every iteration, enabling generative design analysis to drive greater optimization more cost-effectively and, equally important, faster, accelerating time to market and boosting the competitive advantage.
Late-Stage Designs Slowing Your Time to Market?
Watch our webinar to find out how automated analysis and early cost and manufacturability insights reduce costly delays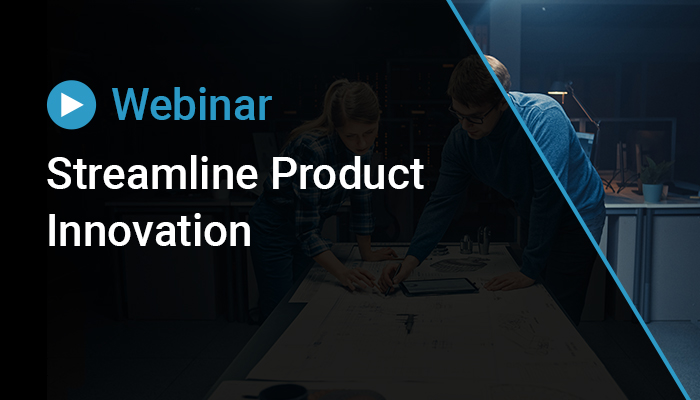