2024 Sustainable Manufacturing Outlook: Uncover ‘Hidden Carbon’
Key Takeaways:
- CO2e “hidden” during product design and production can threaten a manufacturer’s bottom line
- Learn how manufacturers are reducing embodied carbon and addressing other 2024 sustainability priorities
The Full Article:
The manufacturing industry faces a critical moment in decarbonization. Despite some progress, the path to achieving net-zero emissions remains elusive as many companies are either delaying or scaling back their sustainability pledges, according to EY.
The financial impact of sustainable manufacturing continues to grow. This includes carbon taxes on imports that don’t meet sustainability benchmarks, government incentives to spur sales of green products, and customer/investor pressure for measurable decarbonization achievements.
Fortunately, manufacturers can still recover lost ground quickly and/or use their sustainability advances to extend their competitive advantage.
aPriori’s 2024 Sustainable Manufacturing Outlook spotlights opportunities focused on embodied carbon emissions. The first two sections below define embodied carbon and explain why it is central to addressing climate change. Then we examine how manufacturers can reduce embodied carbon throughout the product development lifecycle without sacrificing profitability or innovation.
- What is Embodied Carbon?
- Why Embodied Carbon is Tipping the GHG Scales
- Uncover “Hidden CO2e” With Data-Driven Product Decisions
- Drive Cost-Carbon Optimization
- Set Carbon Costs With Internal Carbon Pricing
- Sidestep Financial Penalties With a Green Supply Chain
- Capitalize on Sustainability Incentives
- Take the Next Step Toward Net-Zero
1. What is Embodied Carbon?
Embodied carbon is the amount of CO2e emitted during the production of a product. This includes raw material extraction and refinement, manufacturing, and assembly. Companies with the visibility to assess the carbon impact during product design and manufacturing gain the ability to identify opportunities to reduce carbon that are often hidden due to the complexity of this process.
The other main greenhouse gas (GHG) emissions category is operational carbon, which represents the amount of CO2e emitted during the operational (in-use) phase of a building or product. This includes energy consumption, use, management, and maintenance of a product or structure.
2. Why Embodied Carbon is Tipping the GHG Scales
The transition to a cleaner energy grid is accelerating. In 2022, renewable power capacity grew worldwide by nearly 13% and is projected to increase by one-third in 2023, according to the International Energy Agency. A greener energy grid, coupled with advances in electrification (e.g., electric vehicles replacing gas-powered cars), is reducing operational carbon.
As such, embodied carbon becomes a higher percentage of overall GHG emissions and is increasingly important to address. One-quarter of the global carbon footprint is embodied in traded goods, according to the U.S. Department of Energy Office of Science and Technical Information.
And this varies by industry. In the building materials and construction industry, embodied carbon will account for 49% of the total carbon emissions between 2020 and 2050, according to a United Nations (UN) report. To put this in perspective, nearly half of all CO2e for a building project is already released before its first tenants move in.
Find out how Carrier is capitalizing on the green building boom. Learn how Carrier accelerated environmental product declaration (EPD) verification of a new HVAC chiller system to meet the growing demand for LEED-certified buildings (Leadership in Energy and Environmental Design).
Embodied carbon is far more complex to calculate than operational (in-use) carbon. And manufacturers require the ability to measure embodied carbon emissions in their design and production processes to help reduce global warming.
3. Uncover “Hidden CO2e” With Data-Driven Product Decision
Approximately 80% of a product’s embodied carbon footprint and cost is locked in during the design phase. Manufacturers that proactively address cost during product development are also increasingly extending this capability to measure a product’s carbon impact during this phase.
This is pivotal because traditionally a product’s carbon footprint is calculated once it’s already been manufactured based on life cycle inventory (LCI) data for life cycle assessment (LCA) tools. LCAs provide users with massive amounts of cradle-to-grave CO2e data across industries from agriculture to automotive.
Use LCA Data as a Launch Point for Product Design Insight
Due to its depth and complexity, LCI data is traditionally only used by experts such as LCA research scientists/analysts and sustainability managers. Without access to LCA tools (and the ability to test multiple design scenarios in real time), product design teams traditionally don’t have the tools to reduce a product’s environmental impact.
LCAs are usually based on averages across industries and applications to serve the broadest user base. For example, LCA software typically calculates carbon based on finished mass. However, it’s more accurate for manufacturers to use rough mass analysis because it includes material waste. Calculating rough mass can significantly affect the actual CO2e measured and vary considerably by manufacturing process. In one example, a die-cast process generated 4% material waste compared to a nearly 70% material waste to machine the same component.
Gain Data-Driven Insights with Geometric Analysis of Design Files
The design of a product can also affect CO2e emissions, but that level of granularity isn’t available in LCA tools designed to provide global averages. That’s because LCAs tend to rely on surface modeling to estimate a product’s CO2e based mainly on mass and materials. By contrast, geometric analysis of 3D CAD designs provides greater accuracy because it evaluates the carbon emissions for each product component (including the housing/surface).
Consider two products that look and weigh the same. The product with a greater wall thickness likely has higher embodied emissions due to the longer manufacturing cycle time required to produce and cool the wider components.
Combine Your Manufacturing Data with LCA CO2e Estimates
To gain accurate, immediate access to carbon data, leading manufacturers are using data-driven manufacturing solutions such as aPriori that integrate with LCA data.
Importantly, solutions like aPriori provide precise analysis of designs, coupled with modeling of digital factories and processes, to automatically align accurate CO2e data with a specific product design and factory. Companies that harness their design and manufacturing data can gain precise carbon emissions data based on factors ranging from materials to production specifications down to the machine level.
As we outline in the next section, gaining insights into how cost and carbon affect one another in a product design is essential.
4. Drive Cost-Carbon Optimization
The challenge of reducing embodied carbon lies in its complexity. Traditional methods struggle to accurately measure and analyze carbon emissions across complex supply chains and manufacturing processes. This hinders manufacturers’ ability to make informed decisions.
Solutions like aPriori are addressing this challenge by providing data-driven insights across product manufacturing: including the 3D CAD model (digital twin), manufacturing process (manufacturing process twin), and specific production facility (digital manufacturing twin).
aPriori, which integrates ecoinvent’s LCI data, enables product development teams to evaluate cost and carbon emissions simultaneously. This includes the ability to simulate how changes in designs, materials, manufacturing processes, and specific factories can impact CO2e and cost.
5. Set Carbon Costs With Internal Carbon Pricing
What’s the cost of carbon to your organization, and how do you assign a dollar value to CO2e during product design? Companies are establishing Internal Carbon Pricing (ICP) as a mechanism to put a strategic value on reducing their GHG emissions, and to use the financial “cost” of carbon to guide sustainability improvements.
With a set cost assigned to each ton of carbon, businesses have an “apples-to-apples” comparison to help make effective business and investment decisions, incentivize departments and suppliers effectively, and support low-carbon innovation.
Solutions like aPriori can use a manufacturer’s ICP to report on production and carbon “costs” and review how changes to design scenarios can impact cost and carbon.
6. Sidestep Financial Penalties With a Green Supply Chain
European Union’s (EU) “carbon tariff” – the Carbon Border Adjustment Mechanism (CBAM) – is designed to level the playing field between EU companies that have strict environmental rules and foreign businesses that can sell cheaper exports partially thanks to lower sustainability regulatory requirements. When CBAM enters into force in January 2026, carbon-intensive EU importers of some materials or components will be mandated to purchase carbon certificates.
Management consulting firm BCG estimates the EU tax could increase the cost of materials made by more carbon-intensive producers, such as China, Russia, and India by 15% to 30% overnight. This potential is causing manufacturers to reevaluate their supplier management strategy based on the location of select vendors.
To evaluate the potential CBAM impact on their profits, manufacturers can conduct a regional cost using either ICP benchmarks or carbon costs on the EU’s Emissions Trading System (ETS). To streamline this process, aPriori provides nearly 90 regional data libraries (aPriori RDLs) to benchmark production capabilities and typical manufacturing costs across the globe.
Sourcing teams can use our RDLs to compare production costs and carbon among factories in Shanghai, China; West Bengal, India; Northern Mexico; Taiwan; and other regions. Manufacturers can also use aPriori to evaluate alternative designs using different materials, manufacturing processes, or other considerations to decarbonize a product. (Read more about aPriori solutions to address CBAM.)
Mandatory Scope 3 (supplier) reporting also drives the requirement for a greener supply chain. California’s SB 253 and SB 261 laws will require mandated climate-change disclosures throughout an organization’s supply chain beginning in 2026. And the EU’s Corporate Sustainability Reporting Directive (CSRD) will require similar Scope 3 sustainability reporting, also scheduled to take effect in 2026.
This requires collaboration and partnerships with suppliers committed to sustainable practices. By utilizing tools like aPriori’s digital factories, manufacturers can gain insights into the carbon footprint of their suppliers, identify areas for improvement, and foster a collaborative approach to reducing emissions throughout the value chain.
7. Capitalize on Sustainability Incentives
Governments around the globe are recognizing the urgency of climate action and are implementing various incentive programs to encourage sustainable manufacturing practices. The CHIPS Act and the Inflation Reduction Act in the U.S., and an estimated $74 billion in clean energy subsidies in the EU, are prime examples of this shift, offering financial and technological support to companies transitioning towards greener operations.
These incentives provide a valuable opportunity for manufacturers to invest in and commercialize sustainable technologies such as EVs, reduce their carbon footprint, and gain a competitive edge in the marketplace.
8. Take the Next Step Toward Net-Zero
A clear sustainability strategy and plan to reach its goals provide a foundation to stay competitive. And digitalization is central to reducing carbon emissions rapidly and effectively across an organization. To underline this point, BCG reports that companies with a leading position on sustainability calculate emissions at the product level and use digital capabilities for emissions management.
By embedding sustainability into the core of business operations and strategic planning, manufacturers can create a culture of environmental responsibility and drive meaningful change. By embracing innovative technologies, collaborating with partners, and taking advantage of available incentives, manufacturers can reach their carbon reduction targets and pave the way for a more sustainable future.
Elevate Your Analysis of Cost, Carbon, and Manufacturability Trade-Offs
See how aPriori revolutionizes manufacturing with real-time cost, sustainability, and performance insights for every product design!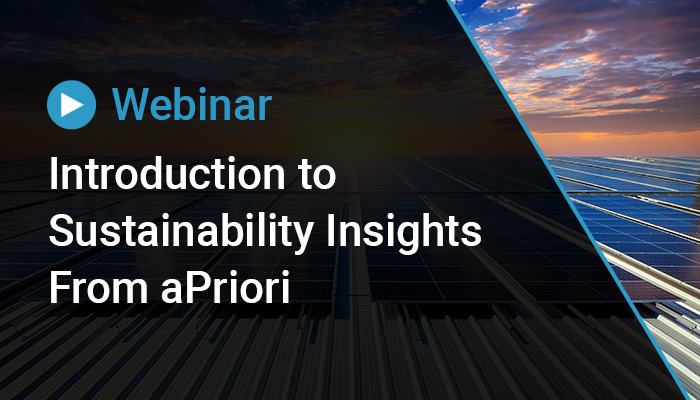