Case Study
How Spirit AeroSystems Uses aPriori to Accelerate RFQ Response Time
How can manufacturers accelerate the timeline for responding to RFQs? Gathering the required cost data often requires knowledge of numerous manufacturing processes. Simply soliciting the necessary information from manufacturing experts across the organization can cause days of delays before quoting work can begin.
In this case study, we look at how Spirit AeroSystems uses aPriori to automate and streamline the process of responding to RFQs. By using a digital factory that reflects its unique manufacturing processes and cost drivers, Spirit can use simulated manufacturing to generate detailed, accurate quotes in hours rather than days. By providing granular, value-added manufacturability insights along with quotes, this new process will be a true marketplace differentiator for Spirit’s bids.
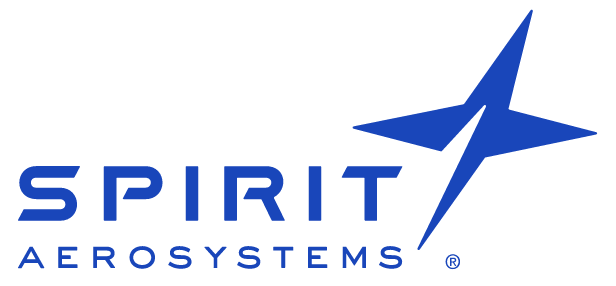
Company Details
Industry
Industrial Machinery & Equipment
Number of Employees
16,100
Revenue
$1.17 Billion
Website
aPriori Product
aP Pro
The Problem
Streamline the Quoting Process for Complex Parts Requiring Multiple Manufacturing ProcessesThe Solution
Use Simulated Manufacturing to Speed Up RFQ Response While Providing Value-Added DFM InsightsWho is Spirit AeroSystems?
Spirit AeroSystems is one of the world’s largest manufacturers of aerostructures for commercial airplanes, defense platforms, and business/regional jets. Spirit leverages its expertise in aluminum and advanced composite manufacturing solutions to deliver core products including fuselages, wings, pylons, and nacelles.
Headquartered in Wichita, Kansas, Spirit’s 16,000+ person team supports customers from ten different global locations covering over 20 million square feet of offices and manufacturing facilities.
Problem: Streamline the Quoting Process for Complex Parts Requiring Multiple Manufacturing Processes
Spirit’s fabrication team in Wichita offers 3rd-party fabrication services to help generate the greatest possible revenue for Spirit’s substantial machining capacity. They needed a solution that could help speed up the process of responding to customer RFQs. The existing process depended on gathering input from numerous manufacturing experts, each of them using their own ad hoc, manual tools and procedures to estimate cost.
The right tool would need to analyze customer designs to generate detailed should cost models and deliver a competitive, realistic quote to customers. And it would need to do so far faster than the existing, manual process.
Ideally, this solution would also help predict manufacturability issues early, empowering Spirit to support its quotes with granular manufacturability analysis (and even recommendations for saving).
Spirit’s product engineering group in Wichita had been using aPriori Pro for Design to Cost work since 2016, and their successful experiences confirmed that aPriori would be a strong fit for the fabrication team. In the following video, Spirit’s David McGinley explains how an inexperienced designer was able to save 11% on one of the very first components they analyzed using aPriori.
Solution: Use Simulated Manufacturing to Speed Up RFQ Response While Providing Value-Added DFM Insights
aPriori provides Spirit’s fabrication group with a fast, accurate, and consistent capability to generate highly detailed product cost models directly from a 3D CAD file. Using simulated manufacturing in a digital factory configured to reflect Spirit’s manufacturing facilities, aPriori can model product costs just minutes after a customer CAD file is received.
Learn more about aPriori’s digital factories.
aPriori’s digital factories are compatible with nearly any major 3D CAD model, dramatically reducing the time and manual input needed to generate a detailed cost breakdown and respond to customer RFQs.
Because aPriori can automatically check for design features likely to cause manufacturability issues or excess cost, Spirit can provide detailed feedback on not only what a design will cost to produce, but how key issues can be addressed before the design is finalized for manufacturing.
Result: Robust Cost Estimates for RFQs in Hours, Not Days
Before aPriori, the fabrication group’s quoting process depended on soliciting the input of many subject matter experts for different manufacturing processes such as machine fabrication, hard tooling, chemical finishing, heat treatment, and assembly. Because this knowledge needed to be gathered up front, a delay from any of these experts risked bogging down the quoting process for days at a time.
With aPriori, initial cost models can be generated automatically in the digital factory. This shift jumpstarts the quoting process, allowing work to begin consistently as soon as the full project parameters are received from the customer.
Manufacturing experts have an opportunity to review the results of the simulated cost model and provide feedback accordingly. This process allows for Spirit’s digital factories to be refined over time–and allows for digital factories to incorporate the expertise of even personnel who do not interact with aPriori directly.
Initially, Spirit’s aPriori implementation focused on the Wichita, Kansas fabrication team. Looking forward, they plan to continue expanding its adoption to more of their global fabrication facilities.
Experience aPriori in Action
Meet with an aPriori expert and learn how we can help you to eliminate product costs, improve productivity, and reduce your carbon footprint.