Case Study
How to Reduce Supplier Costs with aPriori
Introduction
As different suppliers have different methods for allocating cost, a consistent touchstone for discussing cost structure is the key to avoiding contentious negotiations and focus on working collaboratively to identify savings opportunities.
Harman was searching for the right technology to efficiently integrate with design and sourcing workflows, that had the ability to work directly with 3D CAD models, and could work with the varied manufacturing processes required by their diverse – often complex – product offerings.
aPriori offers all the tools and customization that HARMAN needs to get to true cost transparency – enabling meaningful negotiations with their suppliers to reduce costs.
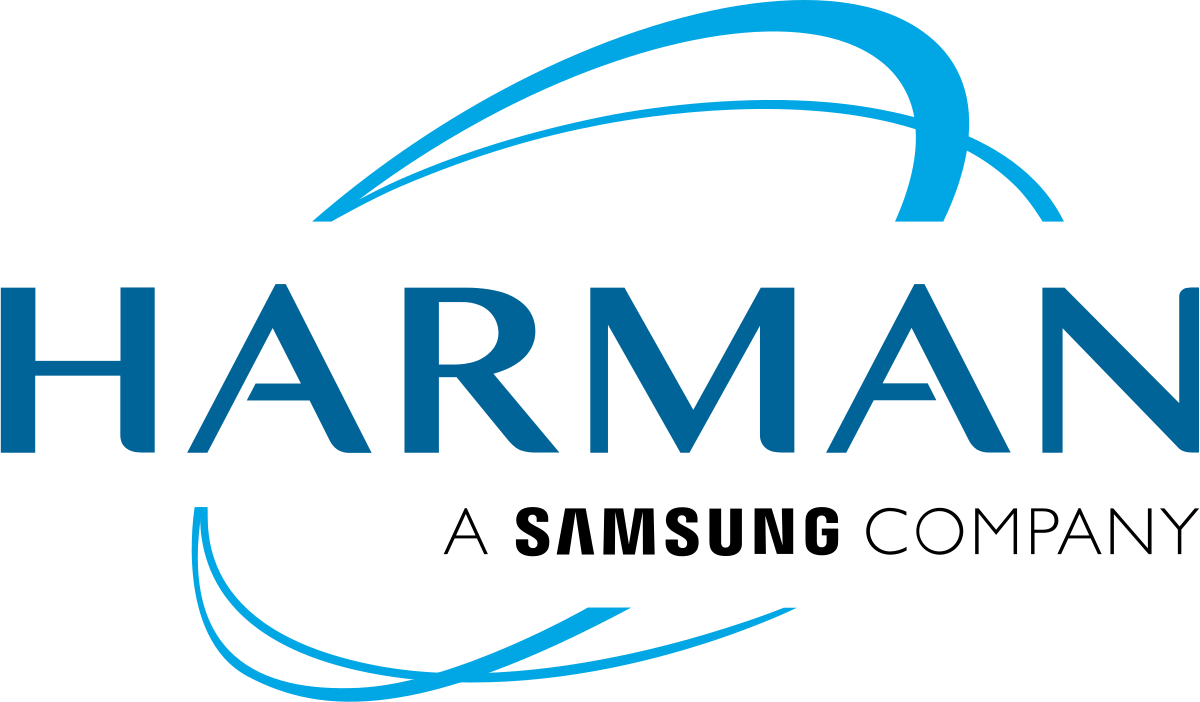
Company Details
Industry
High Tech Electronics
Number of Employees
30,000
Revenue
$8.8 Billion
Website
aPriori Product
aP Pro
The Problem
Develop Manufacturing Cost Models Capable of Driving True Supplier Cost TransparencyThe Solution
Use aPriori to Quickly Generate Manufacturing Cost Models for Third-Party Supplied PartsFocus on Reducing Supplier Costs
The Best Cost Analytics team at HARMAN primarily focuses on supplier costs.
They needed a technology that would offer them powerful transparency into the pricing offered by third party suppliers. This technology would need to offer detailed insight into product cost structure.
They needed manufacturing simulation technology that could quickly analyze a design and correctly allocate costs using unique, supplier-specific cost drivers as the only way to build a true partnership with suppliers.
How to use Use Manufacturing Simulation to Produce Reliable Cost Targets
HARMAN selected aPriori as the best technology to support their mission. aPriori’s ability to configure custom digital factories for a variety of production processes allows its flexible use across a wide variety of HARMAN products.
Simulating manufacturing for products as diverse as speakers and digital cockpits, telematics and Advanced Driver-Assistance Systems (ADAS), aPriori provides HARMAN with manufacturing cost models for production processes including plastic molding, stamping, die casting, electro-mechanical components, and more.
True digital manufacturing simulation leverages digital factories that can be configured to reflect important parameters for different products, regions, and suppliers.
With these simulated process models in hand, HARMAN has reliable targets for the cost of each part. These targets represent a goal that can be achieved through long-term supplier collaboration.
HARMAN’s Best Cost team operates based on the principle that sharing this knowledge will help nurture long-term supplier relationships based on trust and win-win negotiations, not gamesmanship.
aPriori’s ability to work fast was also instrumental in its selection by HARMAN. With the ability to analyze a design to generate a digital twin almost instantly once a 3D CAD is uploaded, aPriori facilitates more transparent sourcing without slowing down the development process.
How Manufacturing Simulation Promotes Additional Cost Savings
Using simulated manufacturing cost models as a starting point, HARMAN works with suppliers to identify cost inefficiencies and develop a transparent, mutually shared understanding of that supplier’s manufacturing cost structure.
aPriori’s simulation-driven cost models are being used both for new products and to identify cost optimization opportunities among pre-existing designs.
This capability not only helps keep costs down but drives considerable operational efficiencies. Once a supplier’s cost structure is clearly defined based on mutual refinement of aPriori’s manufacturing cost models, the RFQ process can be dramatically streamlined.
Automated Supplier Quoting With Zero-RFQ
Over time, this enhanced modeling capability may mature to a fully automated Zero RFQ process.
The traditional RFQ process not only creates delays but involves substantial expenditures of time and resources for both HARMAN and its suppliers. With aPriori’s manufacturing cost models and HARMAN’s dedication to supplier collaboration, this overhead will be dramatically reduced.
In its current implementation, HARMAN uses aPriori to generate supplier cost targets, but still issues a traditional RFQ. As integration and cost collaboration with suppliers become more mature, they aim to implement a Zero RFQ capability.
Once a supplier and HARMAN agree that the aPriori digital factory is configured to reflect reality, HARMAN and its partners will be able to agree on cost without issuing an RFQ — with full confidence in the simulated price point. HARMAN’S Best Cost team is currently conducting initial experiments with Zero RFQ processes.
Experience aPriori in Action
Meet with an aPriori expert and learn how we can help you to eliminate product costs, improve productivity, and reduce your carbon footprint.