The State of Supply Chain Management & Procurement Survey Results
Supply chain stability may be slowly returning to pre-pandemic levels, but procurement between manufacturing brands (OEMs) and their suppliers is poised to change significantly. New research from aPriori and IndustryWeek shows that longstanding supply chain management challenges are giving way to new opportunities for manufacturing brands (OEMs) and their suppliers.
The global survey findings show that manufacturing OEMs and suppliers are focused on accelerating the sourcing and procurement process through collaboration, automation, and digitalization. And supply chain sustainability requirements are reshaping day-to-day sourcing operations.
Speed and the State of Manufacturing Procurement
IndustryWeek, in partnership with aPriori, fielded a 2022 survey to better understand the state of procurement between manufacturers and their suppliers – including current struggles, common goals, and where priorities may differ.
Our report – “The Need for Speed: The State of Manufacturing Procurement” – is based on responses from 345 manufacturers and suppliers in Asia (including Australia), Europe, and North America. Seventy-nine percent of survey participants are upper management, titles that include the C-suite, as well as vice president, director, or manager. Download the full report now.
Key report findings follow below.
Multi-pronged Sourcing Strategies
Sourcing and procurement workflows have accelerated over the years, but they still don’t move at the pace that competitive businesses require. Only 4% of organizations have said it takes up to one week for the average sourcing and procurement process — from initial specifications delivery to quote acceptance. The majority of respondents report this process typically takes one month or longer.
Specifically, quoting takes longer when internal expertise is required — such as greenfield costing and design/manufacturing guidance. Nearly half of survey respondents say these processes take between six and 15 weeks. Also, more than 50% of those surveyed report that quoting for complex parts and assemblies takes at least six weeks.
To move at the speed of business, discrete manufacturers and suppliers overwhelmingly want to streamline sourcing, quoting, and procurement.
Source: “The Need for Speed: The State of Manufacturing Procurement” (aPriori)
Lack of Collaboration is a Key Cause of Delays
The accuracy of quotes typically varies significantly by level of complexity. Suppliers often face pressure to respond to bids quickly to maintain customer satisfaction and gain new orders — despite often not having all the necessary bid information or project visibility required to provide an accurate quote.
Complex bid packages that include multiple requirements are the No. 1 reason for delayed supplier responses to a request for quote (RFQ). Both suppliers and OEMs agree that challenges collecting information rapidly and a lack of transparency, are key hurdles to overcome.
Ad Hoc Procurement Systems are Pervasive
Organizations typically don’t have a single source of truth to manage sourcing and procurement. They heavily rely on email (70%) and spreadsheets (52%). Reliance on legacy or manual methods may contribute to significant collaboration and cooperation challenges.
For example, respondents cite a lack of complete design specs; transparency into quoting details; and a lack of collaboration or clarity around design that leads to inaccurate bids. They also say there are difficulties in adjusting to extenuating factors, such as rising material costs or logistics problems.
Keys to Removing RFQ Hurdles
What will it take for manufacturing sector organizations to speed up sourcing and procurement? It starts with a focus on how suppliers and manufacturers work together. For the most part, manufacturers and suppliers agree on the significance of these collaboration challenges.
Specifically, survey respondents have said visibility, collaboration during the quoting and design processes, and self-service quoting capabilities are the top ways to improve collaboration.
The research shows that suppliers and manufacturers think standardizing how data is shared is the most significant step to improving collaboration.
Key Stat: 68% – Connecting OEM & Supplier Data Systems is Very Important
Improve Supplier Relationships and Collaboration
Although OEMs and suppliers show a shared interest in increased collaboration, responses reflect divergent views on how to achieve this goal. Notably, suppliers are less interested in regular should cost analysis and standardizing data than their customers. This is likely due to supplier concerns that OEMs may try to erode their margins.
To underscore this point, nearly one-quarter of suppliers want visibility into evaluation criteria to ensure that cost isn’t the only factor in OEM decision-making.
Take Advantage of Self-quoting/Zero RFQ
In addition, respondents place great value on self-quoting or self-service functionality; 94% have said their organizations use some of these capabilities to share information during the sourcing and procurement process.
Both suppliers and manufacturers believe that self-quoting/zero RFQ capabilities can improve transparency, reduce administrative burdens, and increase project requirement standardization. And this approach can be instrumental in preventing shortages and addressing shifts in customer demand quickly.
The Growing Importance of Supply Chain Sustainability
Companies are increasingly prioritizing sustainable sourcing to address climate change concerns, alleviate supply-chain disruptions, gain competitive advantage, reduce costs, and better comply with new regulations. No matter the reason, 81% of the respondents cite sustainable sourcing as extremely or very important to their businesses today. In fact, 80% report that sustainability has a very or extremely significant impact on their sourcing directives or priorities.
Additionally, 40% of respondents expect sustainability requirements to affect their sourcing priorities within the next 12 months, while another 26% say it will impact sourcing within the next 1-2 years. Asked how they are addressing sustainability sourcing efforts, respondents most commonly cite working with suppliers to reach carbon dioxide equivalent (CO2e) reduction targets, followed by selecting partners based on their carbon footprint, and sourcing alternative materials.
Keys to Improving Supplier Relationship Management
To gain the necessary visibility and agility in complex manufacturing, organizations should seek ways to connect data systems, automate workflows between OEMs and suppliers, and enable self-service functionality to streamline this often unwieldy process. A connected platform provides a single source of truth that helps organizations gain insights across the supply chain by replacing siloed or disconnected systems and tools such as email, spreadsheets, and homegrown applications.
An integrated manufacturing collaboration software solution streamlines conversations and reduces the complexity of navigating multiple tools to ensure transparency and early visibility around key issues including product costs, manufacturability, and carbon-dioxide footprint data.
The right platform offers a unified set of product design and manufacturing data in a single environment. Teams across product engineering, product cost, sourcing, and manufacturing can review design files and specifications in a coworking environment.
aPriori’s Collaboration and Task Management for Design and Manufacturing
To address these challenges, aPriori has launched aP Workspace, a new collaboration and task management application to accelerate and optimize the entire product design and manufacturing process. The aP Workspace application unifies disconnected product teams and data, and provides a robust coworking and task management environment to optimize product designs for cost, sustainability, and manufacturability.
aP Workspace is a purpose-built collaboration solution that:
- Establishes a single source of truth: Enable all project stakeholders to work on the same data in one place in real time. Use digital thread capabilities to enable users to access the latest product information in their analysis.
- Is intuitive to use: Improve collaboration by customizing product data for design or business reviews, and supplier negotiations. Enable users to highlight different scenarios by product cost, risk, sustainability, and other relevant metrics. And simplify communications by enabling users to mark up and comment directly on 3D models and provide line-item cost data in real time.
- Provides transparency: Have the ability to drill down to see all comments from all users, and use this traceability to better understand a project’s evolution.
- Simplifies task management: Streamline product development with automatic alerts for assigned tasks and get updates to stay current on project status. And turn off the constant stream of updates in task areas that don’t directly impact users.
The right collaboration platform provides multiple benefits — including the acceleration of sourcing and procurement, and real-time collaboration between manufacturers and suppliers. As a result, companies can achieve greater agility, efficiency, and competitive advantage.
Watch our video to see what makes aP Workspace different.
Get the State of Procurement Report
Learn how manufacturers and their suppliers are addressing speed, collaboration, sustainability, and more!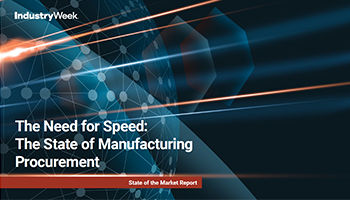