Case Study
How Carrier Saves Tens of Millions with aPriori
Historically, companies have relied on senior staff members or inefficient spreadsheets to cost model. In many cases, they waited weeks, or even months, for supplier quotes.
With manufacturing simulation, complex products can be run through highly-accurate cost models in just minutes. That’s exactly what Carrier achieved by implementing aPriori. In fact, one of Carrier’s first success stories with aPriori included the identification of a $200k annual savings for a set of screw compressor rotors. Initial successes like these paved the way for expanded use of aPriori on many components throughout the organization and have driven over $20 million in value.
We explore their story in more detail in the case study below, including how aPriori will help Carrier meet their emissions reduction goals.

Company Details
Industry
Consumer Durables
Number of Employees
56,000
Revenue
$20.42 billion
aPriori Product
aP Pro; aP Design; aP Generate
The Problem
Modeling Manufacturing Costs for Complex Parts Requiring Multiple Manufacturing ProcessesThe Solution
Use Digital Factories to Simulate Manufacturing and Generate Should Cost Models for Carrier DesignsWho is Carrier?
Carrier manufactures products across three primary market segments: HVAC (both residential and commercial), refrigeration, and fire/security. Across these markets, Carrier generates nearly $20 billion in sales, employing 50,000 people.
Problem: Modeling Should Costs for Complex Parts
The should cost professionals at Carrier face the difficult task of analyzing and optimizing costs for a diverse range of products. These products require different manufacturing processes including casting, sheet metal bending, wire harnesses, PCB assembly, and additive manufacturing.
The cost engineering group’s mission is to optimize product cost and value through both improved supplier negotiation and more cost-effective design.
Employing subject matter experts for each category of manufacturing process listed above, Carrier’s cost engineering group works directly with design engineers and supply chain representatives throughout the organization to identify cost drivers and the potential for value-driven improvements.
Tools like Excel spreadsheets or traditional cost estimation software were not well-suited to generating accurate manufacturing cost models for this high-tolerance, multi-faceted production process. Precisely modeling manufacturing costs for this assembly without the capability to analyze an actual 3D model was simply not possible.
In this video presentation, aPriori Lead User at Carrier, Tristan Abend, shares how their team handles complex geometries using aPriori.
How Carrier Uses Digital Factories to Automate Should Cost Models
Carrier identified aPriori as the right technology for this manufacturing cost modeling challenge. Carrier’s cross-functional should cost team uses aPriori to tackle a wide range of manufacturing cost modeling projects.
They utilize 80+ digital factories in their aPriori implementation, taking full advantage of the capability to generate should cost models across the full range of manufacturing processes required by their products. In addition to utilizing customizable digital factories, they have developed several in-house manufacturing cost models to reflect some of Carrier’s unique designs and production requirements.
aPriori’s configurable digital factory approach has allowed Carrier’s should cost professionals to build detailed, highly accurate models of suppliers’ costs for rotor manufacturing. These manufacturing cost models are based on the precise tolerances required by Carrier for every aspect of the design.
For instance, the added manufacturing time required by cylindrical grinding and sand casting for compressor rotors is a prime cost driver for these components. Never before has Carrier been successful in generating a precise manufacturing cost model of this essential cost driver. The use of aPriori’s simulated manufacturing, based directly on a 3D model of the rotor, is a game changer for Carrier’s should cost team.
Expanded Use of aPriori Across Carrier
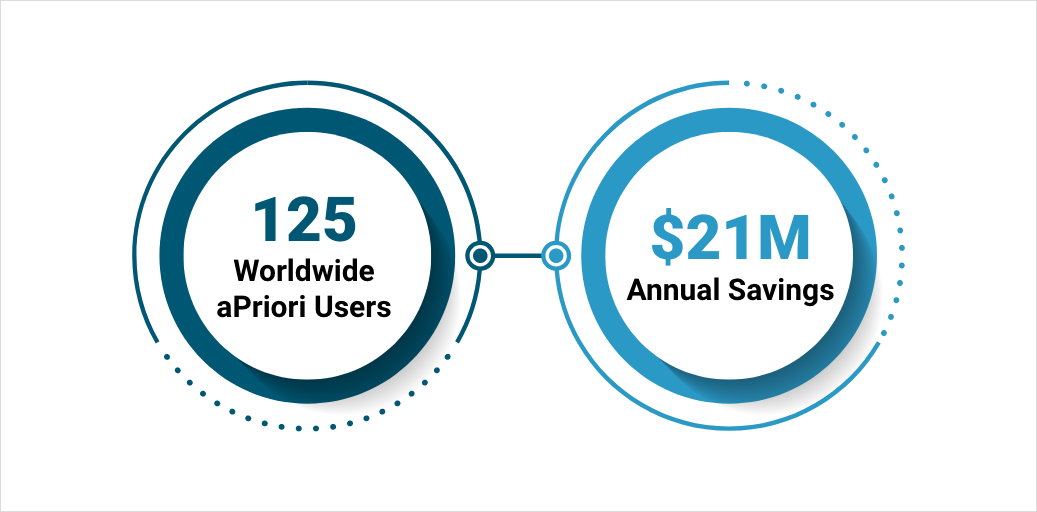
Zero RFQ
Carrier’s should cost team is actively planning to leverage aPriori’s capabilities to generate even more value across the organization. A near-term priority is using aPriori digital factories to achieve a near zero RFQ time with key suppliers. Once a digital factory is specified to a particular supplier, digital manufacturing simulation can be used to achieve an extremely fast, accurate quote for new RFQs.
Today, even before the adoption of a zero RFQ process, aPriori’s should cost models support more robust strategic sourcing decisions, providing timely guidance on not only efficient supplier costs but lead times and carbon intensity.
Automated Component Library
The should cost group also plans to use aPriori to automate an organization-wide component library. Carrier uses a huge array of components across its many business units. Experience has led to insight into these components’ costs, but this data is currently not systematically organized and available for the broader organization. By using aPriori as a repository for these components and their manufacturing cost models, Carrier will automate the integration of crucial knowledge with a digital thread available to business units across the entire organization.
Design Engineering
Starting with seven total aPriori users in 2019, Carrier has already expanded access to 125+ users worldwide (with plans for further growth), including design engineers from many different parts of their diverse global operation. PLM integration allows these designers to integrate aPriori’s insights with minimal disruption to their existing workflows, streamlining adoption and accelerating uptake by engineering teams.
How is aPriori integrated with Carrier’s design workflows?
Carbon Emission Reduction Goals
As with should cost modeling, aPriori will enable Carrier’s engineers to access carbon emissions data integrated within their PLM software, baking sustainability into the design process like never before.
How aPriori is Supporting Carrier’s 2030 ESG Goals
Carrier is using aPriori as a critical tool in its mission to achieve a gigaton in carbon emissions reduction by 2030. Their aggressive ESG plan calls for over $2 billion of investment in solutions that incorporate sustainable design principles and minimize the life-cycle impacts of their products. Generating granular data on carbon emissions is a challenging endeavor for Carrier’s complex global supply chain.
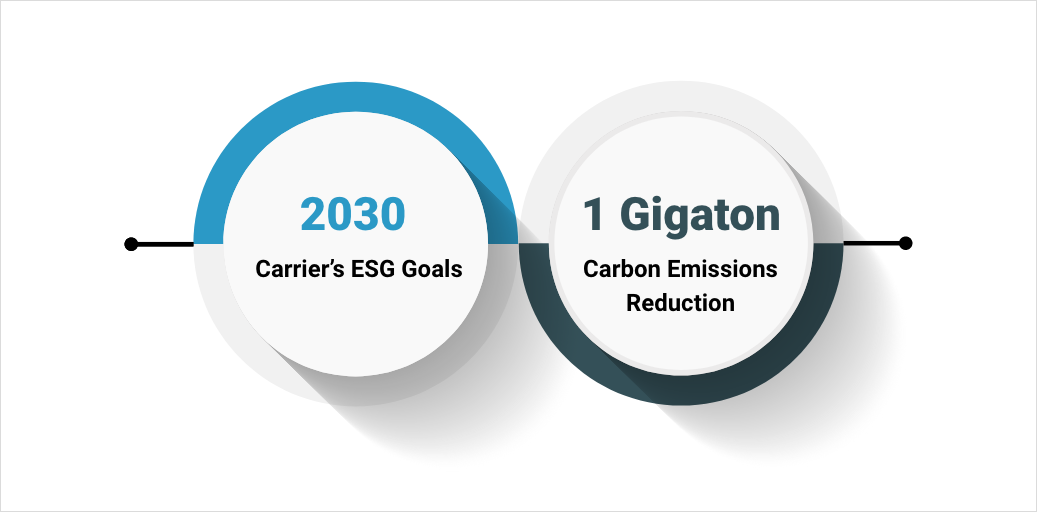
Hear more about Carrier’s approach to sustainability from Tristan Abend, Carrier’s Value Engineering manager, from his presentation at aPriori’s 2022 Manufacturing Insights Conference.
Experience aPriori in Action
Meet with an aPriori expert and learn how we can help you to eliminate product costs, improve productivity, and reduce your carbon footprint.