The Digital Factory: What You Need to Know
A digital factory is a virtual representation of a specific physical factory that enables product teams to simulate production. By using the digital factory to test product designs and manufacturing processes, companies gain insights to increase product profitability, manufacturability, and sustainability. And manufacturers unlock access to valuable new design, sourcing, and planning capabilities with real-time manufacturing insights.
This guide details how teams across the product development lifecycle are using digital factories to:
- Pinpoint early manufacturability issues to reduce costly late-stage design changes and accelerate time to market.
- Use automated insights to scale product design, sourcing, and other operations.
- Identify new suppliers, streamline quotes, propel more effective negotiations, and support data-driven supply chain decision-making.
- Improve results for design for manufacturability (DFM), design to cost (DTC), and other product development benchmarks.
Download the Guide Now!
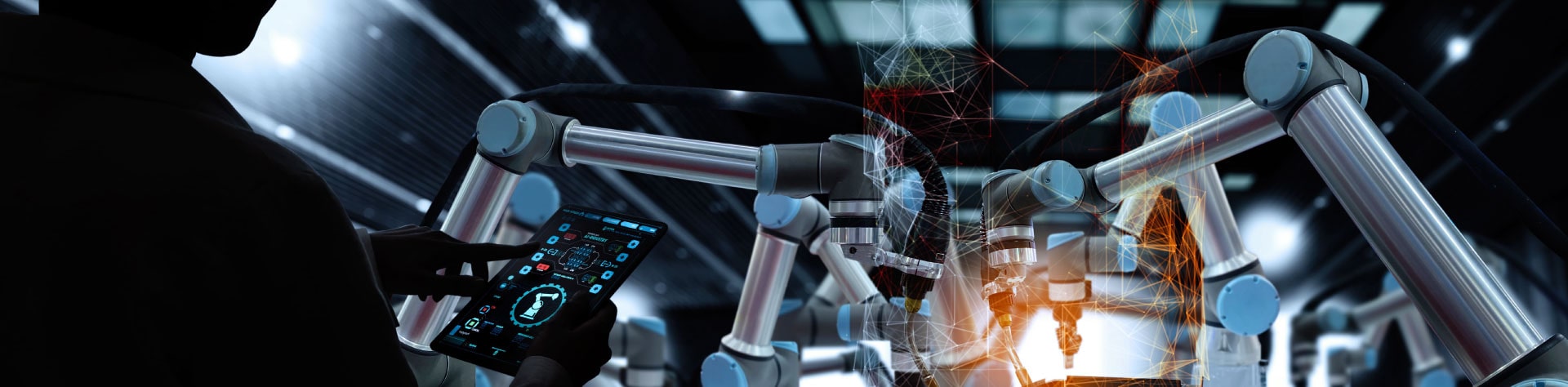
What is a Digital Factory?
Digital Factory Definition
A digital factory provides a virtual “twin” of a physical factory. Digital factories simulate manufacturing by leveraging all the intelligent features captured within a 3D CAD model (or “digital twin”).
Using digital factories to simulate manufacturing in the design phase, engineers can pinpoint potential manufacturability or cost issues early, when there is still time to consider design alternatives. Through automation, simulation can catch these issues with minimal intervention from engineers. And, because digital factories can run simulations in near real-time, they can offer these benefits without slowing down workflows or impeding innovation.
Advantages of Digital Factories and Other Digital Twins
By using digital twins and digital factories to simulate real-world scenarios, manufacturers can compare alternatives rapidly and make decisions confidently to address their goals, such as reducing product design cost, accelerating time to market, comparing cost and sustainability trade-offs, and evaluating reshoring/friendshoring alternatives.
Digital twins underpin the Internet of Things (IoT), Industry 4.0, and related digital transformation initiatives that combine data from multiple sources to create new capabilities, and gain new levels of insight and intelligence. Manufacturers can simulate, analyze, and predict outcomes using this virtual replica, leading to more informed decision-making and optimization of processes.
Digital twins broadly fall into three categories:
- Digital Product Twins refer to 3D CAD models (virtual replicas) of physical products that include components and assemblies, along with overall product size and shape.
- Digital Process Twins determine the most effective product manufacturing method by simulating manufacturing processes and routings (e.g., injection molding and additive manufacturing).
- Digital Factory Twins are virtual models of physical factories that include precise factory-specific production capabilities and detailed costs including labor, electricity, materials, and overhead rates across the globe.
Connecting multiple digital twins breaks down silos among departments and stages of the product lifecycle. This ensures that all relevant information is shared and accessible. This integration allows for a more collaborative and efficient workflow, as data from one stage can inform and enhance processes at another (e.g., the ability to see how a single design change can reduce manufacturing costs or shorten cycle times).
Linking data across the product development ecosystem provides a data foundation that is interoperable, scalable, and has the agility to support business needs today and in the future (e.g., machine learning, artificial intelligence [AI], IoT, etc.).
How Does a Digital Factory Work?
Geometry
Properties
Tolerances
Complexity
Size
Surface Finish
Material
Weight
Digital factories can be configured to reflect different routings, types of equipment, production volumes, labor costs, material costs and more. Regional data libraries help ensure the digital factories reflect real-world geographic variation in cost drivers like labor rates, cost of electricity, etc. You can learn more about the data sources and methodology behind aPriori’s 87 different regional data libraries here. This level of detail is essential for accurately modeling costs and capturing nuanced manufacturability issues in the simulation.
Engineers can analyze production options down to the machine level, simulate multi-factory or multi-process routings, and accurately simulate cycle times for each stage of the production process. Depending on the task at hand, aPriori can either automatically suggest optimal routing and machine selections or conduct a simulation based on pre-determined criteria.
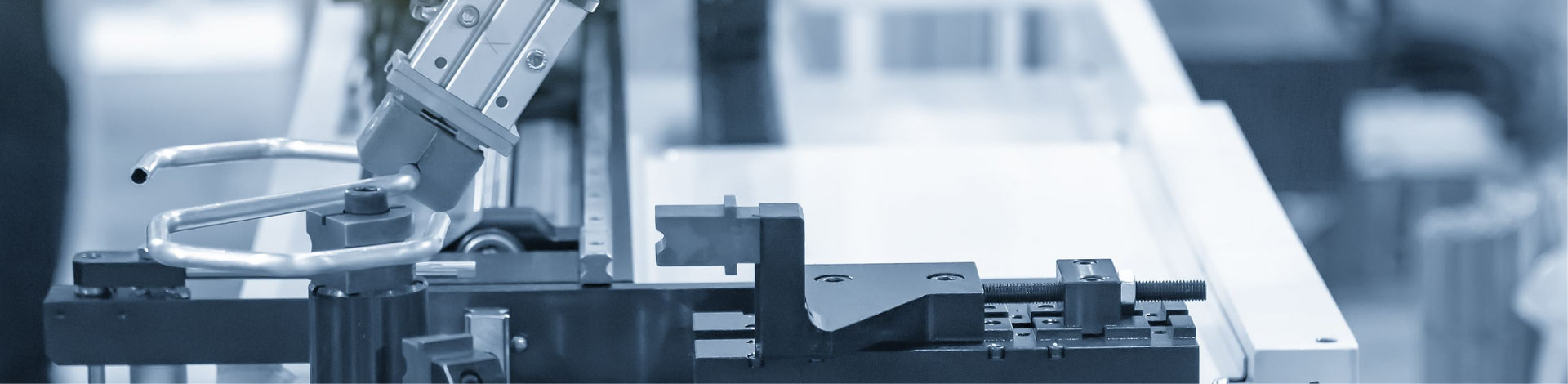
What Manufacturing Processes Can You Simulate in a Digital Factory?
How Can a Digital Factory be Used?
The digital factory can be used as both a hands-on design tool and a hands-off, automated solution for manufacturability and cost simulation. Because aPriori can run simulations in minutes as engineers update the CAD design, it provides an ideal tool for evaluating design, sourcing and manufacturing alternatives without slowing down the product development process.
Automation is accomplished through integration with aP Generate connected to a company’s PLM software: an engineer simply checks in a new or updated CAD design, and aPriori automatically runs a simulation to check for manufacturability or cost issues. If issues are detected, an e-mail is automatically sent to the appropriate party.
Each simulated production run in the digital factory generates a highly detailed “should cost” model, a projection of a product’s total cost if efficient manufacturing and distribution practices are followed. These robust should cost models draw on myriad factors—everything that goes into the cost structure of a real product—including labor, materials, overhead, equipment/ facility rates, and profit margin.
These should cost estimates serve as targets that can be used to evaluate designs, optimize existing products, negotiate with suppliers, and more. We cover each of these topics in this article. For a deeper look at should costing methodology, our guide here offers a great free resource.
The aPriori Digital Factory:
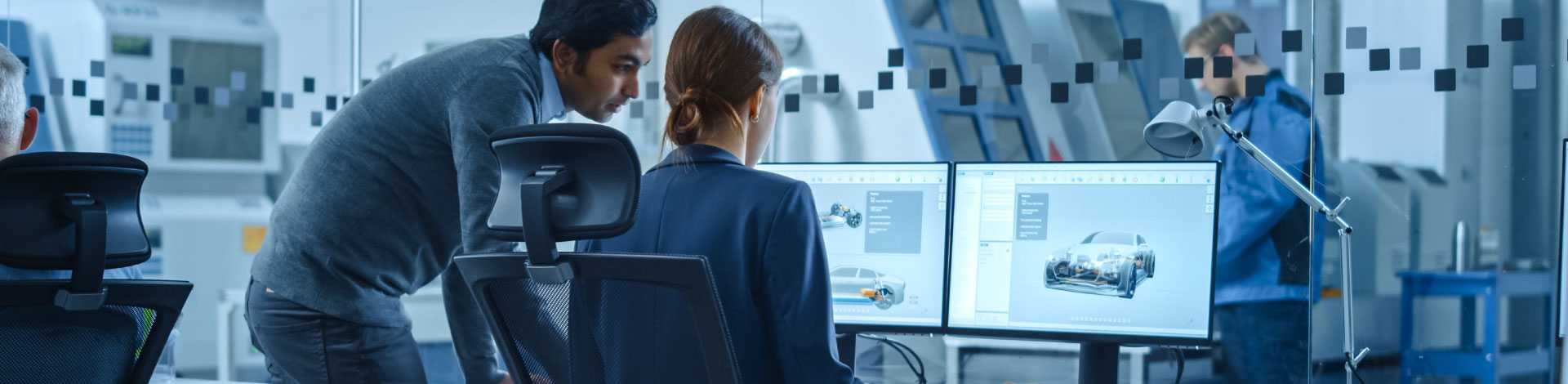
How Does a Digital Factory Benefit Design and Product Development?
In short, digital factories offer insights that can directly improve profitability, accelerate time to market, and inform more consistent, reliable manufacturability and cost models than is possible using traditional tools like spreadsheets.
Simulated manufacturing helps avoid last-minute manufacturing issues or cost overruns—issues that risk delaying orders, harming customer relationships, and losing market share. These broad, long-term benefits show why digital factories are an instrumental part of accelerating digital transformation in manufacturing.
Compared to traditional cost estimation tools, digital manufacturing simulation develops comprehensive cost models that are:
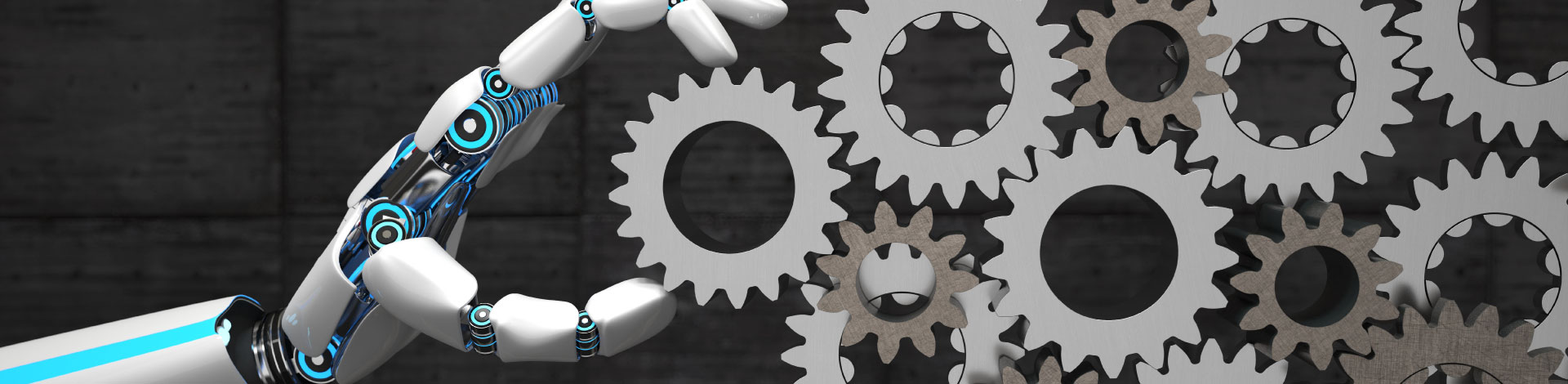
Will My Design Be Manufacturable?
Design for Manufacturability in the Digital Factory
Because digital factories actually simulate production, they can catch issues likely to arise during the physical manufacturing process.
Manufacturability describes the degree to which a product can be effectively manufactured given its design and production requirements. Design for manufacturability (DFM) is the practice of designing products with their manufacturing efficiency and cost in mind from the beginning. You can learn more about this topic in our practical guide to design for manufacturability here.
Traditionally, engineers create a design based on functional needs. They then hand off the design to either a manufacturing team (to approve the design for internal manufacturing) or the sourcing team (which may need to wait weeks for quotes from an appropriate supplier). Without digital manufacturing simulation, engineers simply cannot be expected to foresee every potential manufacturability issue. While engineers can employ rules of thumb for manufacturing-friendly design, the sheer quantity and variety of variables underlying manufacturability are too great to predict without simulation-driven assistance.
Digital manufacturing simulation is a powerful method for evaluating overall feasibility. In some cases, a design cannot be manufactured at all using the specified process and materials. Second, manufacturability is deeply interrelated with hitting cost targets (see above), and digital manufacturing simulation can catch issues that are likely to drive excess cost through problems in the manufacturing process itself.
What Will My Design Cost to Produce?
Design to Cost in the Digital Factory
Design to Cost (DTC) is an organizational methodology for integrating cost management with decision making at the design stage. You can learn more about this methodology and what makes it different in our blog here.
The digital factory is the perfect tool to help engineers hit cost targets without requiring them to learn a complex new skill or slow down the design process.
Without digital manufacturing simulation, it is almost impossible for a designer to anticipate every cost implication of their design choices. The most efficient option might depend on tolerances embedded in the design model, special secondary treatment options, current cost of materials, production volume or labor rates for a supplier on the other side of the world. This lack of cost visibility means that issues are often only discovered when it is too late to respond effectively. It also means that far too many product development initiatives end in weeks of wasteful design churn.
Today’s manufacturers cannot afford to wait weeks for a supplier quote or initial manufacturing run only to realize that cost targets won’t be met. At this late stage, engineers will not have time to change the design, and sourcing teams are left insufficient time to find the most efficient supplier or negotiate on price. This sort of late-stage crunch leads to both missed cost targets and a delayed product launch.
These traditional limitations show precisely why a digital factory can be so valuable for Design to Cost. With digital manufacturing simulation, design teams have real-time visibility into virtually every aspect of a product’s cost structure. Expensive cost drivers can be quickly identified and eliminated. aPriori digital factories go a step further, offering proactive recommendations on how to mitigate detected issues. Because design, sourcing and manufacturing alternatives can be compared in real-time, the design team can explore different options for creating the highest possible end user value while meeting (or even beating) cost targets.
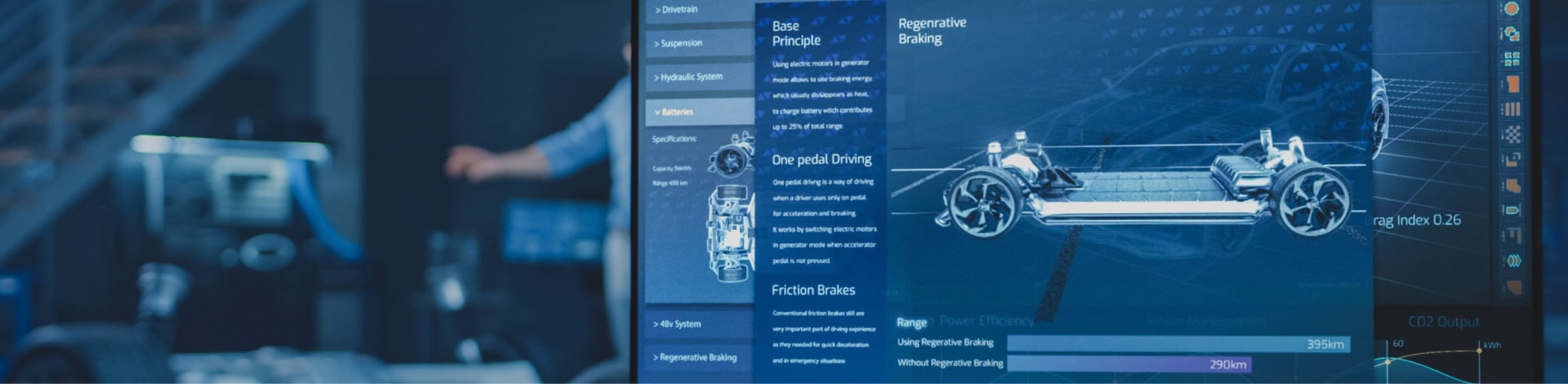
Optimize Manufacturability and Cost for Current Products
Digital factories transform not only new product design, but an organization’s ability to improve profitability for its current product portfolio.
In certain industries, it is still common to push through a design cycle and get a new or updated product to market as fast as possible with minimal regard to manufacturing cost. Once the product is launched to market, value engineering teams go to work to try and identify ways to “squeeze” cost out of the manufacturing process with the objective of improving profitability as they scale production volume.
Using aPriori digital factories, value engineering teams can very quickly create and study design alternatives for potential savings. Similarly, sourcing and manufacturing teams can quickly evaluate alternative strategies for sourcing or manufacturing a product. For example, a product initially manufactured at an internal manufacturing plant in Des Moines, Iowa could be evaluated against the cost of manufacturing that same product at a supplier in Guadalajara, Mexico.
Manufacturing studies could be conducted by running a product design on one line in a digital factory, and then comparing that against another line with different machinery to see if any savings can be derived.
Each of these different types of value engineering studies can be accomplished extremely quickly, delivering insights to system users in minutes instead of weeks using alternative methodologies. Savings from these studies can often be measured in millions of dollars.
Discover how one aPriori customer used value engineering to identify product cost outliers in this case study.
Supporting Sourcing Decisions with the Digital Factory
Digital factories are not just for design engineers. For sourcing teams, digital manufacturing simulation is a valuable resource for sourcing new suppliers, streamlining quoting, negotiating the best possible price, and enhancing long-term collaboration with trusted suppliers.
For a deeper look at how digital manufacturing simulation can help reduce supply chain cost and risk, we recommend our white paper here.
Informing Strategic Decisions Like Make Versus Buy
For example, digital factories provide an ideal environment for evaluating make-buy decisions. Instead of waiting for quotes or comparing internal manufacturing costs to ballpark estimates of outsourced production, simulated manufacturing allows for a detailed comparison that can be generated directly from a CAD model.
In addition to make-buy decisions, simulated cost models can be used to both address general strategic sourcing questions (like sourcing a part from one region versus another) and specific manufacturability questions (such as the most efficient machine for a supplier to use).
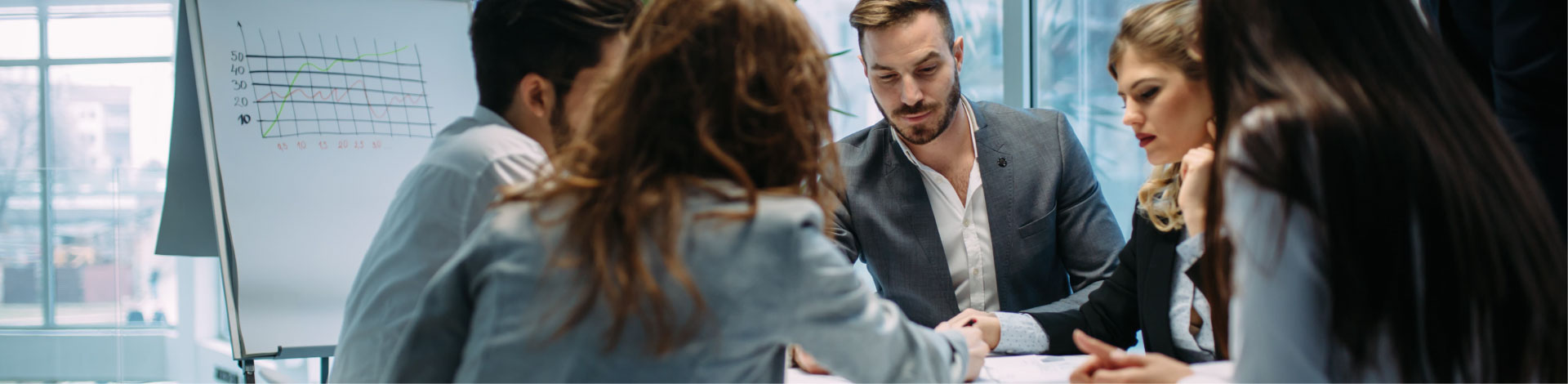
Sourcing and Verifying New Suppliers
When sourcing products from a supplier, digital factories are a great method for verifying that they can achieve their quote in practice. Suppliers will not always foresee manufacturability issues when issuing a quote, and this failure can lead to either cost overruns, delays, or a complete failure to deliver.
Simulated production using regional data libraries and data on the machinery used by a particular supplier can substantially reduce the risk of these outcomes. In fact, simulated production can even help a supplier deliver a product more cost-effectively. For example, digital manufacturing simulation might uncover that a manufacturer is using outdated machinery, paying bloated raw material rates, or choosing an inefficient production technique.
Enhanced Negotiation and Supplier Collaboration
Once a promising supplier is identified, output from simulated manufacturing in the digital factory also helps to promote a more mutually beneficial, collaborative negotiation. With compelling, detailed data on what a product should cost, a manufacturer can focus on discussing the cost structure itself rather than negotiating tactics.
Finally, digital factories can help streamline the quoting process itself. As simulated manufacturing is used to inform more and more sourcing initiatives, a manufacturer can become increasingly confident that its simulated quotes will provide a reliable first-pass projection.
Over time, sourcing teams can even work with trusted suppliers to develop a more nuanced understanding of their cost structure for further refinement of their manufacturing cost model. At some point, the model can even be so refined that it will support a “zero-RFQ” process—simply issue a purchase order for a design without waiting for a quote at all. We take a closer look at how to collaborate with suppliers to reduce product costs in this blog
How Digital Factories Help Maintain an Agile Supply Chain
As the ongoing supply chain crisis shows, maintaining an agile, responsive supply chain is more important than ever. When a supplier can no longer deliver, it can cause systematic shock waves in a manufacturing supply chain. The sourcing team can find itself looking to locate new suppliers for many different crucial parts at once, with almost no time to vet suppliers, negotiate, or wait to see who provides the most competitive quote.
When faced with situations like these, a digital factory is the perfect tool for simulating different scenarios to identify the best solution. Simulation can be used to verify supplier quotes and feasibility, align parts to the most efficient regions and suppliers, and generate a reliable should cost model without delaying the sourcing process. The speed and precision of simulated manufacturing in the digital factory adds up to unprecedented agility when responding to fast-moving supply chain developments.
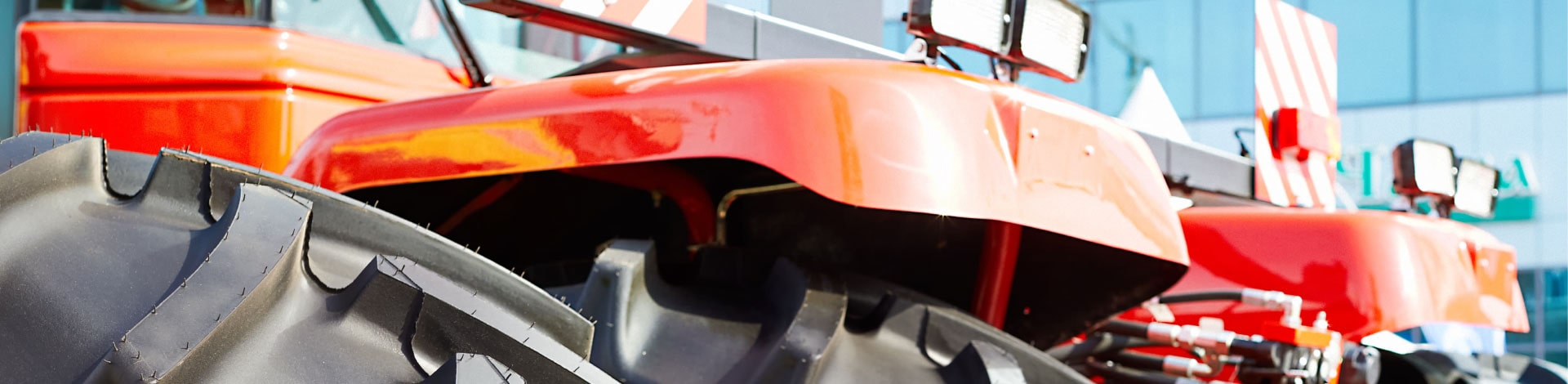
See the Digital Factory in Action
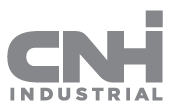
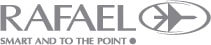
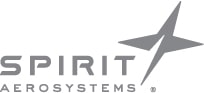
aPriori customers use digital factories to source more efficient suppliers, integrate DFM and DTC insights at the design stage, and identify cost outliers in existing product portfolios. The stories below provide some great examples of how valuable digital factories can be.
CNHi Uses Digital Factories to Identify Millions in Savings
CNH Industrial is a multinational manufacturer which makes agricultural and industrial equipment, with offerings ranging from harvesting combines to marine vehicles. Using digital factories, they have already identified over two million dollars of savings on a single project.
You can learn more about how CNH did it in this 5-minute video.
Spirit Aerosystems Uses Digital Factories to Enhance Their Design to Cost Strategy
Even the most subtle design decisions can lead to cost-inefficient products. In this case, a young engineer added small aesthetic features to a design, unintentionally driving up manufacturing costs for no functional reason. In this quick two-minute video case study, you can see how Spirit Aerosystems used aPriori to spot these issues in minutes, straight from the associated CAD file, for 11% savings on this design.
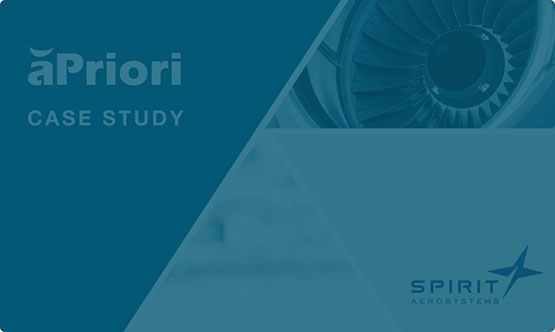
Rafael Leverages Digital Factories to Support Design for Manufacturability
Rafael, an Israeli aerospace company, uses aPriori to support Design for Manufacturability.
In the case study, you can learn how they used digital manufacturing simulation to investigate after a part continued to return no-bids from trusted suppliers. Simulation revealed that an arbitrary design choice was resulting in an undercut that was unnecessarily driving up costs by 50%.
Watch to see how they eliminated the problem, reduced costs, and were rewarded with plenty of competitive bids.
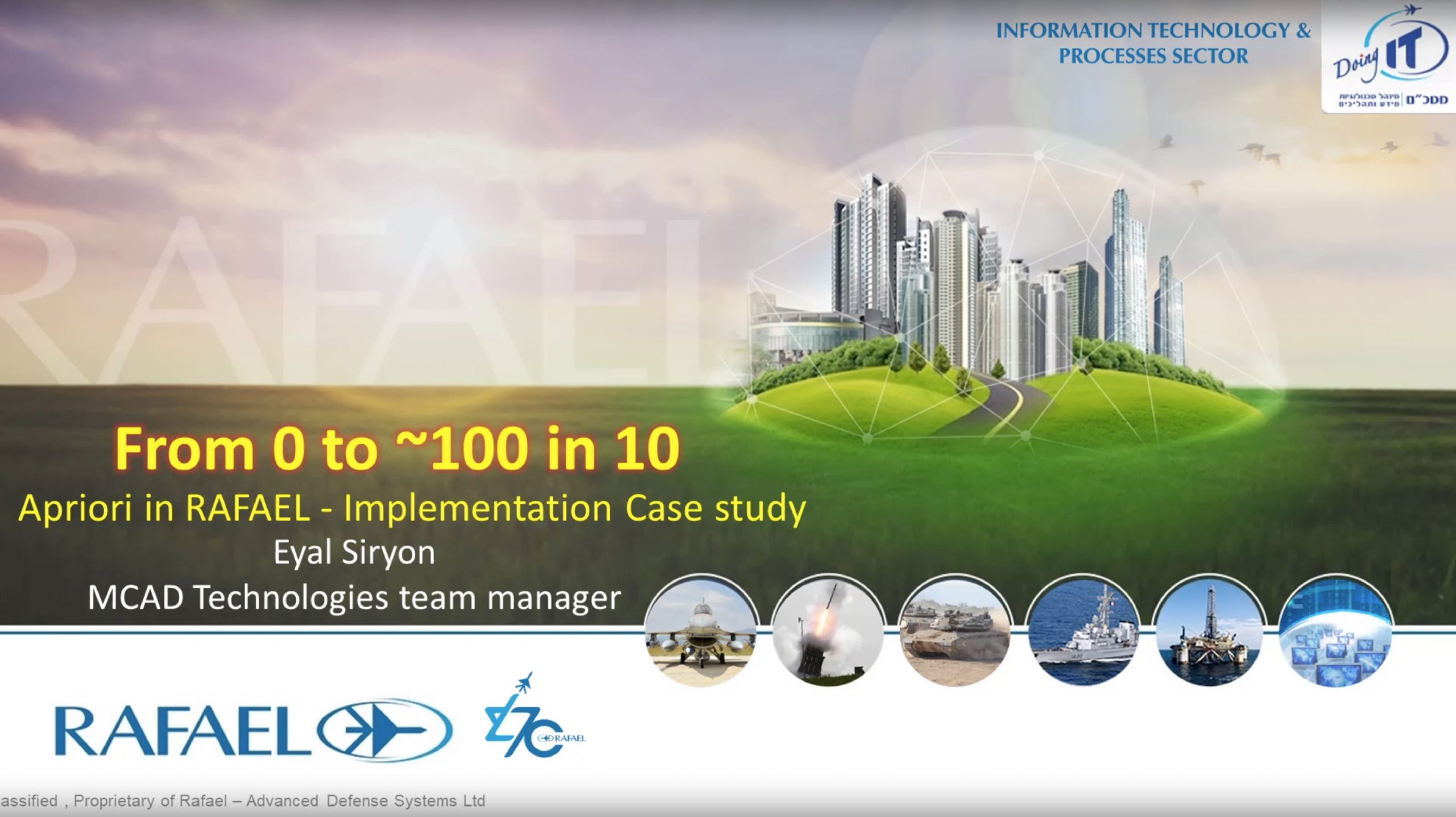
Learn More about Harnessing Digital Factories at Your Organization
Digital factories drive holistic strategic benefits that add up to a true competitive advantage. From evaluating design alternatives, to sourcing suppliers, to monitoring executive KPI’s through integrated reporting capabilities, aPriori helps reduce costs, enhance sourcing agility, accelerate product development timelines, and ultimately deliver a value-maximized product.
To learn more about aPriori, how it works, and how it is helping manufacturers understand manufacturability, cost, and sourcing better (and faster) than ever, click the button below.