Case Study
How to Use Value Engineering Software to Identify Product Cost Outliers
Introduction
Value Engineers are under the unique pressure to decrease the cost of products faster. But legacy systems, clunky spreadsheets, outdated costing practices, and lengthy quoting processes make value engineering harder than ever.
Companies like Axcelis have embraced digital manufacturing to enable their value engineers to significantly improve profit margins.
Learn how a value engineer at Axcelis was able to quickly and easily save 10% on parts by using aPriori’s digital manufacturing simulation software.
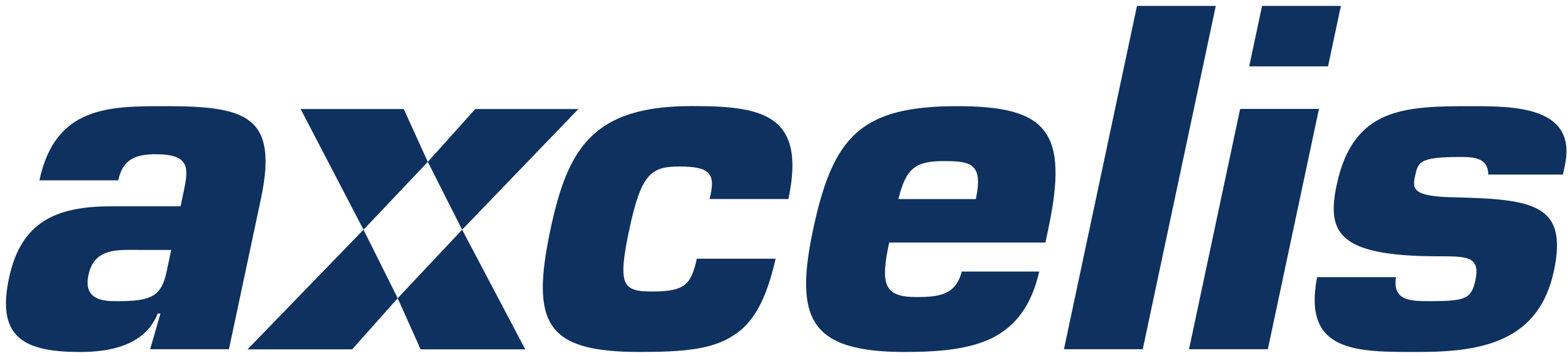
Company Details
Industry
Semiconductor Manufacturing
Number of Employees
1,122
Revenue
$900M
Website
aPriori Product
aP Pro
The Problem
Improve Profit Margins By Decreasing the Cost of ProductsThe Solution
Use Value Engineering Software to Automate Product CostingThe Role of Value Engineering
Axcelis is always looking to reduce cost and create a better and more efficient process and product and relies heavily on its value engineering team to do so. In business for more than 35 years, Axcelis builds semiconductor manufacturing equipment, specifically ion implantation systems, one of the most critical and enabling steps in the IC manufacturing process.
What is Value Engineering?
The primary purpose of value engineering is to reduce cost and increase margin for a company, specifically by redesigning or modifying designs.
During new product design, the ultimate goal is to make better design for manufacturability choices upfront to avoid going over cost later during production. However, it does not always happen that way.
Ultimately, the goal is to reduce the base cost of products to increase margins. Axcelis has a small value engineering team. One of their biggest challenges was trying to control and reduce costs. Enter aPriori.
Value Engineering Software for Automated Cost Analysis
Value engineering software enables value engineers to understand detailed product costs early in the design process. There are a number of benefits to using value engineering software.
- Identify and Eliminate Cost Drivers Early – Quick costing of CAD 3D models enables you to identify cost drivers and potential manufacturability issues early in the design phases.
- Improve Product Value – Once cost drivers and manufacturability issues are understood, you can quickly develop design alternatives comparisons to highlight further saving opportunities.
- Eliminates Surprises – You can track calculated cost against target cost at the component and system level on either a week to week or month to month basis. This is critical reporting for value engineers.
Reduce the possibility of getting surprised with excessive engineering change orders related to cost or manufacturability at the end of the design lifecycle.
aPriori in action. In this demo video below, watch how aPriori can help to identify and eliminate product cost drivers.
Using aPriori for Value Engineering
aPriori allows Axcelis faster analysis. It can even run several different scenarios at once by looking into new designs that we’re working on, which allows us to adjust costs on the fly.
With aPriori, the team at Axcelis can manipulate the data and make more informed decisions while waiting on a quote. In fact, we can actually try different iterations while we wait and then use the quote from our supplier as a baseline to negotiate with them. At that point, we can use aPriori to help determine if one change or another will help to reduce cost that much more. And sometimes, that makes all the difference for us.
How to Implement Cost Avoidance with aPriori
Cost avoidance is the greatest value that we receive from aPriori. Cost avoidance can also be hard to track. That’s especially true when you get involved in a case late in the game and have to shift focus to the end cost.
That’s exactly what happened in the following example. aPriori’s Customer Success Team helped Axcelis to identify a supplier that was supplying parts at a higher cost than alternative suppliers for similar components.
Axcelis engaged aPriori to scan through 100 machined and sheet metal parts, all of them sorted by cost, material, volume, complexity, manufacture region, and supplier. We were then able to review these parts for cost and design outliers and compare actual costs with aPriori’s estimates.
We used the mass of each part as a driving factor. That data led into a cost vs. mass baseline, which gave us a group of parts on which to direct the next phase of the analysis. That led us to looking into the complexity and material composition of the parts, which can drive costs way up.
Running through 10 different components across various companies, we went back and renegotiated with the supplier that had the higher costs. This project led to a direct cost reduction, but it also helped Axcelis to avoid cost during the initial design and supplier selection on future projects.
All the components in this example were of high or medium complexity and were all primed for a design for cost review. This design for cost review led to additional cost savings on the reviewed parts and cost avoidance on similar part concept designs.
Experience aPriori in Action
Meet with an aPriori expert and learn how we can help you to eliminate product costs, improve productivity, and reduce your carbon footprint.