3 Ways the Pandemic is Driving Digital Transformation in Manufacturing
The manufacturing industry has been under construction over the last decade as design engineers rode the innovation wave that accompanied rapid technological advancements. But all too often, the processes that take engineering ideation through production have been left behind while the products themselves experience a digital transformation.
In the wake of the COVID pandemic, experts project an easier recovery for organizations that embraced more technologically mature workflows, leaving those with manual, less agile ways behind.
But exactly how much of the industry is behind the digital curve?
Inherently curious, aPriori partnered with The Engineer, a UK-based publication, in order to quantify the impact of the pandemic in the industrial engineering sector. We needed to better understand the changes that were written on the walls of a global shutdown and those that seemingly bucked the trends and had analysts scratching their heads. The Engineer published a full report of the survey findings, which can be found here. Over 400 people responded to the survey, with the majority in Aerospace and Defense and Industrial Equipment.
There are three things we learned about the state of our industry during the crisis that point at the growing need for a digital transformation in manufacturing.
1. 61% Aren’t Actively Using Digital Manufacturing Technology
This was a surprising statistic for 2020 where technology reigns. Legacy manufacturing processes often required desktop applications that became inaccessible during the shutdown. Additionally, teams that rely on face-to-face collaboration were rendered suddenly challenged, slowing down productivity.
But it also points to a remarkable opportunity for those using automated digital platforms or those teams that are agile enough to onboard technology remotely. In an industry where the innovation curve can catapult a brand into the limelight, this moment in time presents an unheard-of opportunity to displace long-running brand domination and bring a new, diverse portfolio of manufacturers to the market.
To take advantage of this opportunity, costing and sourcing employees will have to be ready to make quick, yet informed decisions on purchasing. A strong understanding of should-costs and the capacity for quote automation will become essential tools for workers in these roles to successfully navigate the supply chain.
2. 54% of NPI Plans Have Changed or Will Change
If it’s been said once, it’s been said a hundred times over, these are unprecedented times. People are doing more with less resources, team members, and budgets. It would follow that companies would begin to adjust their expectations of what engineering teams can accomplish realistically with these new restrictions but it seems that the strategy is somewhat split.
More than half of the survey respondents anticipate a change in expectations for New Product Innovation. This could point to a split in the industry’s technological savvy. The transition to a work-from-home environment hit every worker a bit differently. The advent of cloud-based manufacturing solutions eased that transition for early adopters, minimizing a few of the obvious hurdles but beyond that, those with turbo-charged technology, like those with access to aPriori’s full suite of solutions, have the capacity to catapult beyond other manufacturers who have been struggling to match competitors serve for serve.
3. 72% believe costing consistency will be important to the future of manufacturing
Keeping costs down was a fairly obvious outcome of the disruption, considering the shutdown caused revenue stalls across all industries. But consistency marks a trend we’ve seen for a number of years among fast-growing manufacturers. It’s simply not enough to keep costs down; estimating pricing components closely and consistently is just as important. So much is tied to the cost of manufacturing that fluctuations in small parts add up quickly and cause revenue impacts that are felt long-term. Antiquated quoting processes rely on manual calculations, are based on single manufacturing systems, and don’t take into consideration the myriad of ways to produce a single item.
CONCLUSION
While we can’t predict with certainty what the future of manufacturing will hold, the pandemic has created an opportunity for manufacturers to lean into the agility and consistency afforded by modern technology. Recovering faster and shock-proofing your manufacturing processes may be the catalyst for the digital transformation long awaited in the manufacturing industry.
How to Engineer an Industry Bounce Back
On Demand Webinar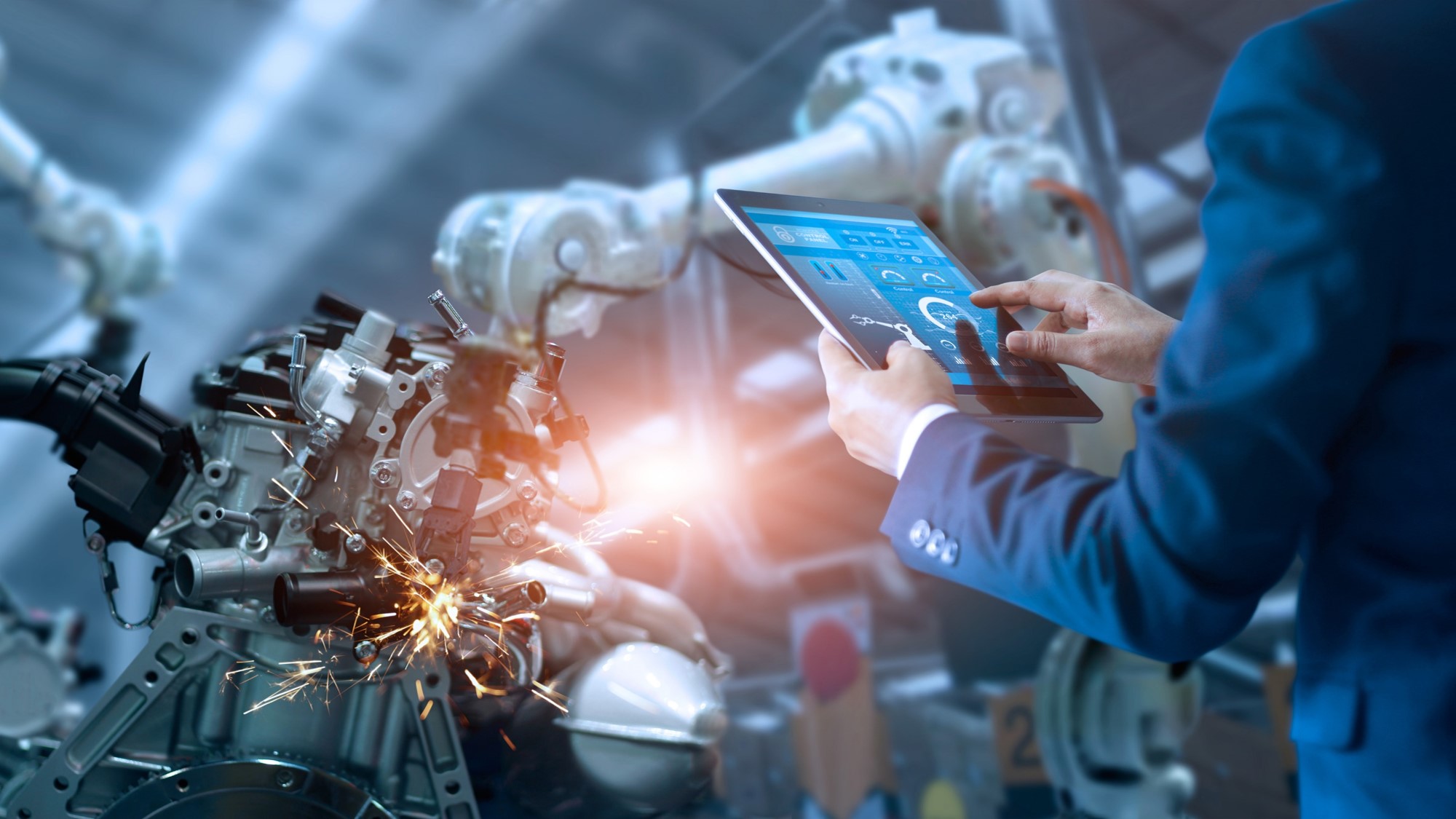