August 17, 2022
Is Additive for Everyone?
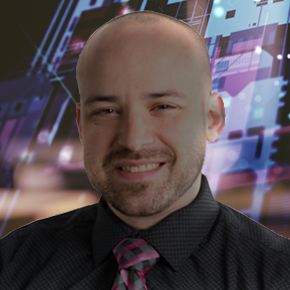
Transcript
Leah Archibald: How do you decide if additive is for you? My guest today Robert Turck comes to us from Fast Radius, a leader in additive manufacturing. He joined when Fast Radius was just a start-up, and he has seen customers go through the process of evaluating whether or not additive should be a serious consideration in their supply chain. Robert Turck, welcome to the podcast.
Robert Turck: Thank you so much for having me, Leah.
Leah Archibald: Let’s go back in time a little bit. Can you tell me when you started to get excited about additive technology and what excited you most about it?
Robert Turck: Absolutely. I was working for a company called NN, and through their acquisitions over time they had purchased a facility that did 3D printing – metal additive manufacturing. They were utilizing this technology for the orthopedics industry – essentially printing parts that were going into our bodies. For example, a hip joint that was being printed in a single process as opposed to being made through multiple pieces and joined together. To me, I just found that absolutely fascinating. Not only are we putting printed metal parts for bodies, but we’re also making joints off of one single process.
Leah Archibald: Are there types of parts that lend themselves better than others to additive manufacturing?
Robert Turck: Absolutely. Generally, very complicated geometrical structures lend themselves to additive manufacturing. A huge part of additive’s innovation is the ability to print lattice structures. We can take a solid part and reduce its weight by essentially creating a webbed structure internally. You sacrifice very little internal strength, but you gain the benefits of removing all of the filler that’s not needed. You can’t do this with traditional manufacturing in a cost-effective manner. The ability to do this in 3D printing gives it a huge leg up.
Another type that comes to mind is air flow inside of a particular component. Think of a manifold that has to have a very specific airflow, or a way of diverting fluid through a particular system. 3D printing allows you the freedom to essentially design whatever flow that you might want.
The other thing that’s specific to additive is customizability. In traditional manufacturing, you set up a process for one design and produce it in mass. In 3D printing, you’re allowed to make changes on the fly. You may have a particular design that you thought was golden, but when you lock it in it turns out you didn’t foresee a particular issue. Now that it’s in the field, it’s a complete failure, and you’re going to have to scrap tens of thousands, maybe hundreds of thousands of dollars down the drain and start from scratch. But if you’re were prototyping in 3D printed materials, then you could be able to change the design in seconds.
Leah Archibald: So, it sounds like additive lends itself well to designs that are customized for each use case, whether that’s per individual or in the field quickly swapping out parts. Is there any other use case for large manufacturing concerns where 3D printing might help at scale?
Robert Turck: The original thought behind what 3D printing is all about was for prototyping, and that does lend itself to particular uses within the product lifecycle. But there are also certain places in which 3D printing can be used for mass production – areas in which the geometric structure of the part either cannot be manufactured in the traditional sense, or it can’t be done cost-effectively.
The other place where there’s potential for it to shine is the ability to source locally – where all you really need is the material at a specific site. One such application was brought to us by a customer. They were 3D printing shower heads to be custom fit for a special residential location.
Leah Archibald: Going into this conversation I kind of had this question in my mind: is 3D printing for me if I’m GE? Is 3D printing for me if I’m Boeing? Now I think maybe that’s the wrong question. I think the question is: is 3D printing for me based on the value I’m providing to the customer? If I’m the section of Boeing that’s making aircraft doors for 1000 airplanes, then 3D printing isn’t for me. But if I’m further down the product life cycle and I’m replacing a small part on the airplane that’s very difficult to get, where the sourcing chain is very long, but I can have a printer in my truck, then 3D printing is for me.
To go back to your shower head example, 3D printing isn’t for me if I’m Lowe’s and I’m trying to get thousands of shower heads to go on my stock shelves. But in my custom design bathroom unit, 3D printing might be for me. I think it goes back to what value we’re producing for the customer, and that will also be reflected in the price that the customer is willing to pay for this particular type of value.
Robert Turck: You’re touching on some very good points there. And there are also applications even for the same part manufactured over and over again. This is true if there’s no good way of doing a traditional manufacturing for this particular part. For example, there may very well be a need for reducing weight on part of an aircraft, and maybe you’re willing to pay a little more for reducing the weight overall because you save on fuel with a lighter aircraft. You might be reducing the weight through creating lattice structures, or you could be reducing the weight by not having to join parts together. Maybe you have a single part that’s printed as multiple parts in one piece, as opposed to having it manufactured in multiple pieces and then assembled where failure can occur by not properly joining materials. And of course, that also touches on the cost of shipping these discrete parts to different locations to have them assembled and then shipped back to another location to have them assembled into larger pieces. There’s an opportunity through innovation and design to reduce the amount of pieces and make them single parts, much like that hip joint we were talking about at the beginning.
Leah Archibald: I’ve been talking as if 3D printing is all one monolith – as if there’s only one machine that 3D prints things. But could you give us an idea of different types of 3D printing that maybe have different cost levels to a manufacturer or that might work in different situations?
Robert Turck: There is a huge range. You can even go as basic as the Hobbyist or Prosumer market for 3D printing. You can get some really decent prints nowadays – really inexpensively. You can even buy a printer. Then of course, there’s a much higher end expensive piece of equipment that can cost up to half a million dollars to acquire. And sometimes service bureaus will rent or lease this equipment as opposed to purchasing it outright. Printer costs aside, the material costs are quite varied as well from printer to printer. Whether it’s a liquid resin, or whether it’s a powdered metalized material, it has to have very specific properties in order for it to fuse properly, even down to the powder for HP’s Multi Jet Fusion printer. There are so many different ways you can manufacture using 3D printing. The one that most people understand is FDM, Fused Deposition Modeling, where you have essentially a line or a coil of filaments or plastic being extruded through a hot nozzle and liquefied or brought to near to its melting temperature.
You also have things like MJF, Multi Jet Fusion from Hewlett Packard, which will take a powder form of plastic, bring it up to near its melting temperature, then use light or laser to essentially melt the specific cross-section that needs to be brought above its melting point. This creates a melt that solidifies and then creates a new layer.
Leah Archibald: At one point I worked at a shoe company, and I would see the prototypes of the shoe bottoms being printed. The printer laid down a level of sand and then melted some parts of the sand, over and over again over a series of hours. You would get this shoe bottom that weighed maybe 150 pounds and it looked like you were pulling this mountain of shoe out of the Earth. It wasn’t anything you would actually put on your foot, but it gave you the idea.
Robert Turck: That brings up a good point: how do you go from essentially what looks like a sandcastle into this part that’s actually usable? There is a step generally in 3D printing that most would not be aware of unless they’re actually sitting in a factory and witnessing it. There’s a post-process step that take place after the 3D printing. You have individuals that are specialized with precision tools essentially sanding down what’s not needed or removing the support material off of the pieces. The clean-up part of it is something that you don’t think about when you say: Hey, I’ll just hit print!
Leah Archibald: So when manufacturers are thinking of taking this technology on board – either for particular use cases, or because they want to re-shore some of their production – it’s not just the cost of the printer and the printer material to think about. There’s also a specialized labor cost that needs to come with this, because with every 3D printed part, there’s some kind of specific post-process.
Robert Turck: Absolutely. And even before that specialization that you’re referring to for the post-process, there’s a ton of engineering work that goes up front to making the part actually manufacturable for 3D printing. There could be a tweak that makes it more cost effective for 3D printing. Also, the orientation in which you’re printing the part affects its material properties if it’s not an isotropic material. Isotropic indicates that it would have the same material strength properties in all directions regardless of the orientation. But some are not isotropic. FDM, the traditional type of manufacturing we’re aware of, is not isotropic in nature. The Z-axis, the one in which there are layers and layers built off the top of one another, will fail much sooner than it would if you were trying to put tension on the XY region.
Leah Archibald: And aPriori has a whole software system that helps the design engineer make those decisions.
Robert Turck: Absolutely. It’s almost like The Matrix. Like: I don’t know how to fly a helicopter, but let me go ahead and download this and now I know how to do it. That’s kind of like what aPriori does with the design insights it provides.
Leah Archibald: My favorite party ice breaker question has always been: if you could download one skill Matrix style, without having to do any lessons or any practice, what skill would you pick?
Robert Turck: A sense of irony. [laughter]
Leah Archibald: [laughter] Well, Robert Turck, this has been such a pleasure. Thank you for joining me on the podcast today.
Robert Turck: Pleasure is all mine, Leah, thank you.
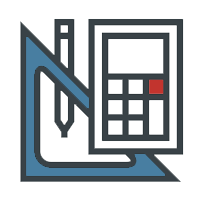