January 15, 2025
The Cost of Offshoring for US Manufacturing
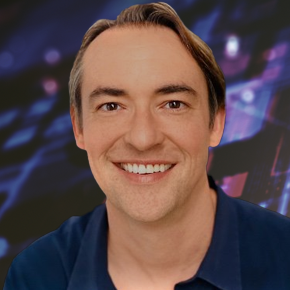
Transcript
What is the real cost of offshoring?
When you think about offshoring, reshoring, or nearshoring, you’re probably thinking about cost. Certainly, the cost of labor and energy is a primary deciding factor when it comes to offshoring, reshoring, or nearshoring decisions. But what about the hidden costs of offshoring?
This is a subject our guest knows a lot about. John Gardner writes about the hidden costs of offshoring and the increasingly apparent benefits of nearshoring. He is the author of Manufacture Local: How to Make America the Manufacturing Superpower of the World.
What are some of the hidden costs when it comes to offshoring?
John Gardner: Well, I think there are hidden costs for a nation and a civilization as a whole, and I feel very passionate about those. But I also think there’s a lot of hidden costs for a company.
The cost of offshoring can include:
- Cost of stolen intellectual property and product replication.
- Cost of dealing with inconsistencies in production batches.
- Cost of critical language translations.
- Cost of delayed deliveries because of reduced supplier control.
- Cost of internal personnel expansion required to manage a major offshore supplier.
- Cost of travel to ensure that suppliers’ facilities and parts remain compliant and problems are resolved.
- Cost of lost business because of product availability interruptions.
- Cost of fees paid to customers because of late product shipments caused by inconsistency.
- Cost of dealing with quality problems.
John Gardner: On the cost of dealing with quality problems, one of my biggest clients is the largest electric motor manufacturer in the world, and for years and years I’d hear them say, “I have to fix this batch of electric motor shafts because it was cheaper to make the whole part overseas than fix the problems once we got it in hand.” So that highlights a big problem in our economy and how America approaches manufacturing.
Leah Archibald: There are many different types of costs you listed there, and some of them are dollars and cents costs. But there are other types of costs there too: time costs, or speed to market costs. Is there a single way that we can quantify these costs too?
John Gardner: Yes. What nobody talks about is economy of scale. Economy of scale is quite powerful.
Offshoring manufacturers lose on economy of scale
Economy of scale is a powerful example of the cost of offshoring. If you look at a manufacturing company, if they’re making 100,000 pieces, the per piece price goes way down. But if they’re making 10 pieces, the price goes way up because you have to do the same tooling, the same programming, the same setups, the same cutting tools, all for 10 pieces, and spread that cost out over 10 pieces as opposed to 100,000 pieces. So when you have economy of scale, large volume lots, and you ship those overseas, another nation is taking advantage of economy of scale. And what that does is it allows manufacturers in other countries to justify the investments in robotics and automation, but not those at home. I talk to a lot of shop owners who say, “I don’t really want to put the money into a new robotic cell because I don’t know if I’ll have the volume to do it. So I think a lot is it lost when you ship millions of parts overseas and have small batch lots. Your local nation is suffering then because you don’t get to take advantage of economy of scale.
Leah Archibald: You talk about economies of scale in terms of manufacturers keeping control of cost and keeping all the cost savings in their own pocket. But I’m also wondering if there are informational economies of scale where when you offshore your intellectual property, you’re not bringing in-house all the key performance data from your manufacturing operations that’ll help you learn how to make better products, make products faster, troubleshoot your product development process so you can get products to market faster.
John Gardner: You’re 100% spot on. And another point is when you offshore and have someone else make your stuff, you loose a lot of potential for innovation. A lot of innovation happens around mass manufacturing: you see something that could improve the process, or you see something that can improve the product.
Leah Archibald: So with all the different manufacturers you’ve worked with, do you see a gap in terms of the way they think about the information, the data that they need to be capturing, and how that impacts their bottom line?
John Gardner: I see a huge gap. Of the 252,000 manufacturing companies in America, 75% of them are 20 employees or less. And these small machine shops, which make up the majority of American manufacturing, for the most part are not set up to capture a ton of information and do data crunching. These shop owners are busy as heck trying to quote jobs, buy the tooling, get more business — you know — run the shop floor. And I think the lack of volume in American manufacturing stops them from growing at the pace where they would have hundreds of thousands of parts to manufacture and that they would then implement data systems to analyze that.
The tool historically to force volume manufacturing to come back to a nation has been tariffs. And that’s what American manufacturers need so that volume jobs come back.
Leah Archibald: I’m so glad that you mentioned the data infrastructure that machine shops need because that’s one of the focuses of aPriori: giving manufacturers this tool so they can quote faster and analyze their CAD parts so they don’t have to do that all manually. But you’re saying there’s another piece that needs to happen nationally to empower small machine shops to be able to quote at scale and produce at scale, and you’re telling me it’s tariffs?
John Gardner: It’s volume production. And the tool historically to bring volume production back to a nation is tariffs. The United States was the world’s largest manufacturer prior to World War II, and World War II is a perfect example of how that power was turned to defend a nation. And so to rebuild manufacturing might, we need to have tariffs to drive large volume manufacturing back to the US so that our manufacturers can justify the investment in automation robotics and software. That’s my opinion.
Low tariffs impact local manufactures
Leah Archibald: Tariffs has been a huge conversation after this last US election. Are you encouraged by tariffs being part of the national conversation?
John Gardner: Yes, I’m dramatically encouraged. I think manufacturing was the dirty stepchild that was never talked about, but it really is the foundation of economy. And as far as information systems, I think a lot of the shops that I talk to, big shops, they’re hesitant to invest in new equipment, new CNCs because they don’t have the volume to justify that. My machines are not up at full capacity even though we have very cutting-edge technology. My machines are not at full capacity because the manufacturing sector is really being challenged by other nations.
Leah Archibald: Tell me about your own manufacturing operations and what you’ve seen in the past few years in terms of the pressures facing manufacturers today.
John Gardner: I sell a patented cutting tool that’s used in metal manufacturing, automotive, aerospace, military, agriculture, oil, and gas. So it’s used across the board to do a process called broaching. I started this in 2005 when offshoring was really hammering American manufacturing, and I’ve seen the manufacturing industry just continue to contract. I’ve seen the manufacturing industry go through dramatic shocks. Covid was a massive shock. Then you saw manufacturing spike up after Covid as we started making things again and the economy opened up. And now the manufacturing industry has been in contraction for two years, a steep contraction. I actually think it’s a recession, a manufacturing sector recession. And I think that’s totally due to the fact that we tariff on an average rate of 3.4% where other nations have 50%, or 100% tariffs on our goods going into their nation.
Leah Archibald: I appreciate your frontline eyes on this situation, and I encourage everyone to read this book, Manufacture Local: How to Make America the Manufacturing Superpower of the World. Thank you for joining me on the podcast.
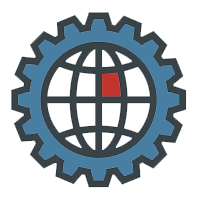