What Is Design to Cost? An Overview With Examples
Key Takeaways:
- Design to Cost helps manufacturers reduce design-stage expenses, accelerate time to market, and avoid costly late-stage redesigns
- A robust cost strategy enables designers to integrate cost management into their workflows, enhancing team efficiency
The Full Article:
Manufacturers consistently aim to cut costs, striving to achieve lower expenses while maintaining the desired product functionality. This results in higher profit margins, increased market share, and more satisfied customers.
Historically, manufacturers often estimated and managed costs using an ad hoc strategy; however, this approach is becoming increasingly outdated. Forward-thinking organizations are now embracing Design to Cost methodologies and solutions that provide comprehensive insight into the cost structure during the crucial product design phase.
Explore the Design to Cost methodology, identify the steps needed to transition an organization to these practices, and examine practical examples. Then, discover the critical role of digital manufacturing insights technology in the methodology’s foundation. Navigate the sections below:
- What Is Design to Cost?
- An Essential Paradigm for Manufacturing Cost Reduction
- The Transition to a Design to Cost Culture
- How aPriori’s Cost Management Solution is an Essential Enabler for Design to Cost
- Embrace Design to Cost for Competitive Advantage
What Is Design to Cost?
Design to Cost (DTC) is an organizational methodology that integrates cost management with decision-making at the design stage. The DTC approach transforms costs from a post hoc business target to an independent variable within the design process.
By implementing DTC, product development teams can effectively design high-quality innovations within pre-determined cost targets from the outset. Consequently, they can avoid costly and late-stage engineering change orders (ECOs), enabling them to bring their new products to market more quickly.
What Makes Design to Cost Different
Manufacturers have always needed to consider costs. Traditionally, they prioritized product design first and then determined its price. Design engineers focused more on performance, appearance, and reliability than cost when making early design decisions.
If the designed product proved too costly for the market, engineers had to redesign it to a new cost target. These target costs were often effectively arbitrary from a design perspective. They would calculate cost-cutting targets simply by subtracting the desired manufacturing profit margin from the market price.
Ignoring a granular analysis of the most salient cost drivers while setting cost-cutting targets across every aspect of a design is a recipe for poor outcomes. Design engineers risk chasing low-impact cost drivers, which could unduly harm the design’s functionality. If they do not identify the most inefficient cost drivers, the design may remain far from competitive in the marketplace.
Most manufacturers have now adopted a more rigorous methodology for estimating product costs. This approach can range from extrapolating from similar past projects to summing up core material and labor costs using an Excel spreadsheet. However, manufacturing cost estimation remains an increasingly complex analytical problem, and these back-of-the-envelope costing systems may only generate vague estimates of a product’s true final cost.
An impactful DTC strategy aims to improve estimate precision substantially, but this approach doesn’t just seek more accurate cost targets. It also strives to accomplish something else entirely: integrating simulation-driven cost analysis at the design stage. The goal is to shift the onus of cost-cutting away from arbitrary targets. Instead, in a DTC environment, costs are directly tied to the design decisions that drive them.
An Essential Paradigm for Manufacturing Cost Reduction
Competitive pressures in manufacturing, coupled with the growing complexity of international supply chains, are driving more manufacturing companies to invest in DTC strategies. The design engineer can influence 70% of a product’s total cost, making these strategies highly effective.
To conduct a comprehensive analysis of cost drivers for a design, design engineers must leverage solutions that evaluate an extensive range of potential cost drivers accurately. A brief list of considerations include:
- Specifying material. Beyond direct costs, additional material usage indirectly affects process and ecological costs, along with the other factors below. The analysis needs to cover everything from tolerance to machining requirements.
- Evaluating packaging, shipping, and logistics. To determine a design’s true cost, teams must consider its weight, volume, fragility, and storage requirements.
- Ensuring manufacturability. Factors such as cooling times, facility availability, and equipment costs are crucial for every aspect of design.
- Taking labor into account. Adding a part that requires manual assembly, for instance, can have a cost impact far out of proportion to its direct materials cost.
However, analyzing these factors in insolation isn’t possible: every design choice affects the cost and functionality of the rest of the design. While these relationships can be clear cut—like added weight requiring increased component tolerances—they can also exhibit incredibly complex interactivity (particularly when including facilities and supply chain costs).
Managing complex, interrelated variables of this magnitude requires a significant organizational commitment to integrating cost management into product engineering’s culture and an investment in innovative software for manufacturing cost estimation.
The Transition to a Design to Cost Culture
The DTC approach raises critical questions about organizational ownership, specifically who is responsible for managing product costs. Traditionally, a gap exists between business units with functional control over cost management and pricing (sales or business development with input from upper management) and the design teams. This disconnect can lead to organizational silos preventing a holistic evaluation of cost drivers. In worse cases, this can result in a “turf war” between engineering and other business units over the viability of cost targets.
To foster an effective costing strategy, organizations must empower design engineers with the responsibility, authority, and solutions to integrate cost management into the design process. This alignment helps organizations unify their thinking about cost management, functional design, customer needs, and marketplace pricing. See how design teams leverage aPriori to optimize products to meet cost targets and eliminate late-stage changes that extend the product development process:
This shift certainly requires a change in the engineering culture. However, implementing cost management during the design stage goes beyond simply learning new jargon. Many essential cost drivers are largely opaque to ground-level product engineers. Engineers need solutions that enable them to analyze cost in the design context holistically without burdening expert resources or hampering innovation.
For instance, when engineers explore design alternatives, they might notice that adding more of a particular component slightly increases the marginal material cost of the design while enhancing reliability. However, each marginal addition doesn’t exhibit a linear effect on the final cost. After several components are added, the overall design surpasses the weight threshold. This change requires manufacturing it in a second facility with higher tariffs and a less advantageous exchange rate differential than the first. Thus, the complex effects of a design decision may cost significantly more than a traditional designer could reasonably anticipate.
In the past, quantifying these sorts of dynamic interactions when comparing design alternatives was almost impossible. However, advanced manufacturing cost estimation solutions now make this possible.
How aPriori’s Cost Management Solution is an Essential Enabler for Design to Cost
An automated manufacturing cost estimation platform, like aPriori, is an essential foundation for the DTC methodology. The solution robustly and accurately analyzes every element of a design’s cost structure down to the machine level to improve decision-making. Here are a few key functionalities and features of the aPriori Manufacturing Insights Platform:
- 440+ physics-based manufacturing process and cost models, including additive manufacturing, assembly, casting and forging, electronics, and more
- Extensive Regional Data Libraries (RDLs) that provide detailed breakdowns of total manufacturing costs, such as material expenses, labor rates, and manufacturing overhead (direct and indirect overhead costs, tool shop rates, etc.)
- Three levels of automation:
- Part/assembly 3D CAD geometry analysis: Get instant cost estimates and feedback on manufacturability from 3D computer-aided design (CAD) models
- Bulk costing analysis: Efficiently evaluate multiple parts/assemblies to identify cost-saving opportunities
- PLM integration-based analysis: Streamline workflows by integrating automated design analysis and actionable insights into the product lifecycle management (PLM) system
This depth of technological capability is crucial, as teams not only need to calculate a product’s cost drivers but also analyze the cost drivers for alternative designs at the speed of business. Moreover, teams can employ aPriori’s sustainability insights to measure and reduce a product’s carbon dioxide equivalent (CO2e) emissions from the initial design stage. This capability helps manufacturers innovate for a sustainable future.
Real-Life Examples Showcasing the Power of aPriori for Cost Management
Across the globe, industry-leading manufacturers use aPriori to accelerate the product cost process and achieve exceptional outcomes. Examples include:
- Each redesign was costing Dana Corporation $3 million. Until they started using aPriori.
- Carrier saves up to $30 million in critical project costs
- Thompson Aero Seating, an airline seat manufacturer, reduced the cost of its top 50 most expensive machined parts by 40% within two months
Embrace Design to Cost for Competitive Advantage
Adopt a DTC strategy to remain competitive. Integrate cost management into design to enhance product quality, streamline product development processes, and save costs. Solutions such as aPriori drive this innovation and efficiency, helping manufacturing companies design cost-effective, high-quality products from the start.
Want to boost your design efficiency by 70%?
Get aPriori's Guide to Manufacturing Cost Estimation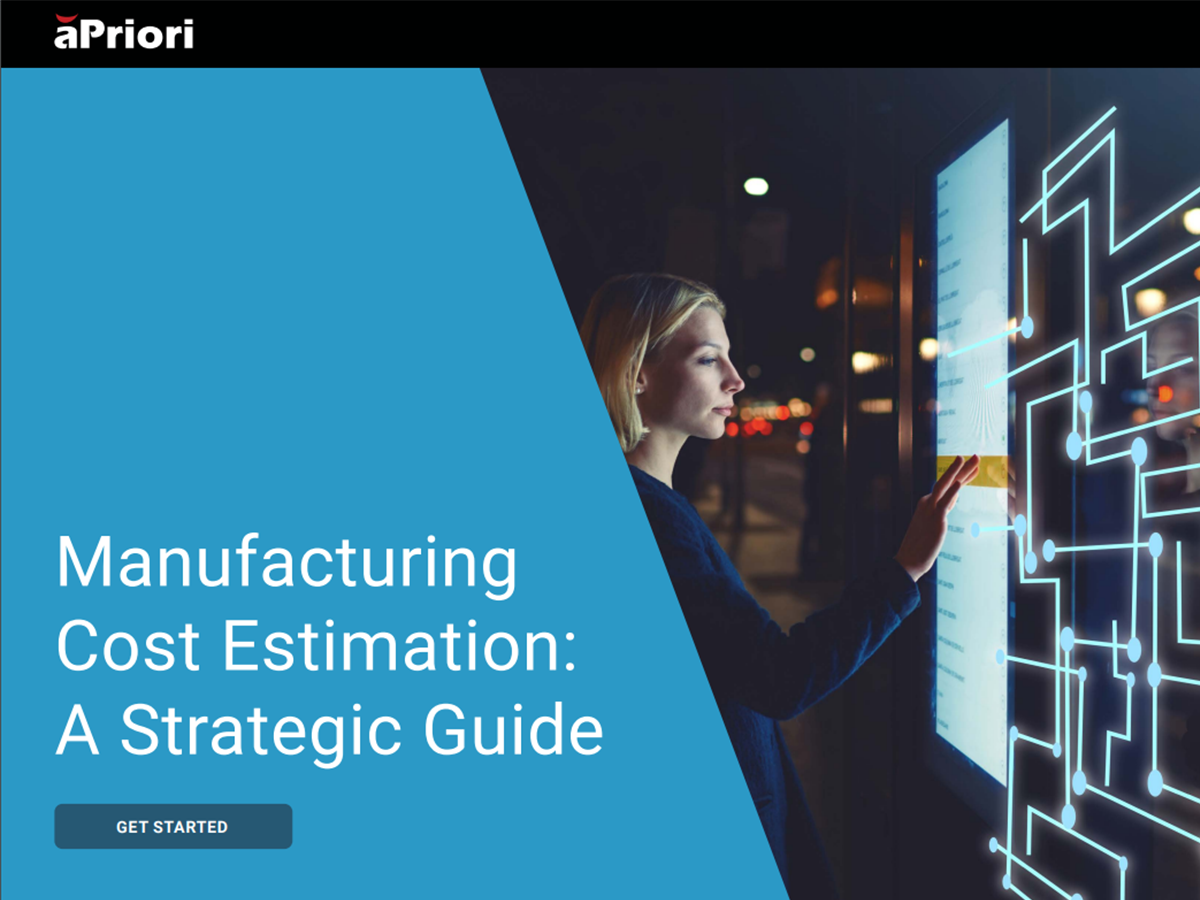