What Inflationary Pressures Teach Us About Cost Analysis
The COVID-19 pandemic, supply disruptions, and other inflationary pressures continue to fuel global inflation and its effects on manufacturing firms. No company, regardless of size or industry, can completely sidestep the negative effects of the current and unprecedented inflationary environment. According to a PWC survey, 91% of manufacturers have felt the impact of inflationary pressures since 2020.
The alarming statistic demonstrates the extent to which a single inflationary pressure can affect most manufacturing companies today. As the current inflationary environment persists, more manufacturers will face increased raw material and production costs.
Maintaining low inflationary costs is critical to an organization’s success and profitability. Manufacturers require a dedicated costing department equipped with digital manufacturing insights to combat rising inflationary pressures and achieve cost goals. At its core, firms can counteract inflationary costs by digitalizing, accelerating, and transforming cost analysis procedures for today’s inflationary environment.
In this article, we define inflationary pressures and explain how they are taking a costly toll on the manufacturing industry. We also look at how costing departments may leverage manufacturing insights to modernize cost analysis and help firms make informed decisions.
What Are Inflationary Pressures and How Do They Affect Manufacturing Firms?
Inflationary pressures are the underlying and major causes or drivers of today’s inflationary environment. These pressures have caused lopsided supply and demand conditions, pushing manufacturers to increase production to meet or exceed rising demand. Further, present inflationary pressures have raised overall price levels due to a lack of supply.
Inflationary pressures happen when different variables or disruptions push manufacturers to adjust and respond to ever-changing supply-demand economic conditions. According to Deloitte, an inflationary pressure can be classified and grouped into three categories:
- Disrupted Supply Chains. Port congestion, transportation challenges, and major events such as the war in Ukraine and the pandemic contribute significantly to disruption. Manufacturers have been pushed to consider alternative, readily available materials or substitutes to develop their products during supply chain disruption.
- Constrained Manufacturing. First, due to material and component shortages, manufacturing firms are unable to effectively produce tangible goods for end users. Second, there is a workforce deficit relative to current demand due to pandemic lockdowns and early retirements. Transportation personnel, such as truck drivers, who are responsible for delivering goods on time, are among those in short supply. Finally, a severe European energy crisis has resulted in substantial energy price increases that have halted production across nations.
- Mismatch Between Supply and Demand. The combination of rising consumer demand in developed nations and limited supply in Asian manufacturing hubs contribute to price increases. Manufacturers must strategize to meet and achieve supply-based objectives in relation to strong demand.
How Are Firms Responding to the Effects of Inflationary Pressures on Cost Analysis?
Today’s manufacturing firms are employing highly effective methods to combat and manage rising costs due to high inflation. For instance, the Federal Reserve reports that 80% of manufacturers are passing on rising costs to customers through higher prices.
It is critical to note that companies may tarnish customer relationships by imposing arbitrary, reckless price hikes to combat inflation. Passing on costs to end users is only an effective strategy when price increases are planned and proportionate to inflationary conditions. While efficient, passing on rising costs to consumers is not the only way to manage and respond to inflation.
Companies can reduce inflationary costs and uncover cost-saving opportunities in the real-world inflationary environment by digitalizing their cost analysis processes. A digital manufacturing insights platform enables a manufacturer’s costing department to modernize cost analysis through automation, agility, and estimation accuracy. The right manufacturing insights platform converts analog, labor-intensive cost analysis operations into a powerful, highly transparent inflation-combating procedure.
Why Should Costing Departments Leverage a Manufacturing Insights Platform to Fight Inflation?
As inflationary pressures continue to emerge, a manufacturing costing department requires the right resources to keep pace with volatile conditions. Cost specialists can generate precise estimates and provide cost-reduction guidance using the following capabilities and modules of a manufacturing insights platform:
- Real-World Digital Factories. Cost engineers can make cost projections based on real-world “digital factories.” These factories consist of regional supplier data libraries and manufacturing cost models that are cognizant of the current inflationary environment. Together, the capabilities enable cost specialists to adjust manufacturing processes and routing rules, as well as leverage material libraries and regional labor rates. The objective is to identify the most cost-effective location for manufacturing a product using low-cost component substitutes and production methods.
- Design for Manufacturability and Cost (DFMC) Insights. Cost engineers can view the cost implications of different product designs in real-time. Designers receive cost-effective design feedback to ensure that their product designs are optimized for cost and manufacturability from the start. This reduces the risk of costly late-stage engineering change orders (ECOs), which slow down time to market (TTM).
- Design for Sustainability Calculations. Costing departments can track the material CO2, processing CO2, and energy consumption used to develop a product component. Product development teams can use these insights to strike a balance between product cost, performance, and sustainability targets.
- Matrix and Bulk Costing Modules. Matrix costing workflows can be launched to estimate the cost of a single product component based on multiple production inputs. Bulk costing, on the other hand, allows cost engineers to generate quick, detailed cost estimates for multiple parts at once. Cost specialists can compare the module’s generated should cost projections with the supplier’s rising prices to identify component cost-saving opportunities.
Manufacturing insights platforms, such as aPriori, streamline cost analysis processes through simulation-driven cost estimates, cost transparency, and real-time reports. Digital manufacturing insights, at their core, enable product development teams to mitigate inflation and other risks that reduce profits.
Key Lessons From Today’s Inflationary Pressures
The importance of automating the cost analysis process is reinforced by major inflationary pressures like labor market shortages and rising costs. Cost engineers need automation to produce up-to-date estimates based on the real-world, ever-changing inflationary environment.
Traditional cost analysis methods are simply insufficient as they fail to account for the impact of high inflation on manufacturing. That is why a recent PWC Pulse Survey found that 60% of manufacturers look to capitalize on digital transformation initiatives. More manufacturing firms believe that digital transformation allows them to:
- Improve operational agility and decision-making during high inflation.
- Develop new cost-effective, highly functional products more quickly to meet TTM objectives.
- Fulfill and mitigate strong customer demand pressures.
- Better manage supply chain volatility and other inflationary risks.
Conclusion
The current inflationary environment has changed the way manufacturers think about procuring raw materials, developing products, and delivering goods. To combat high inflation, companies must adopt a powerful, digitally transformative approach to identify cost-saving opportunities that lead to profitability.
CASH BURN: MANAGING CASH IN A DOWNTURN ECONOMY
In the face of economic headwinds, manufacturers have to maintain their most precious resource: cash. Quick decisions can protect manufacturers from cash burn and turn an economic crisis into a competitive opportunity.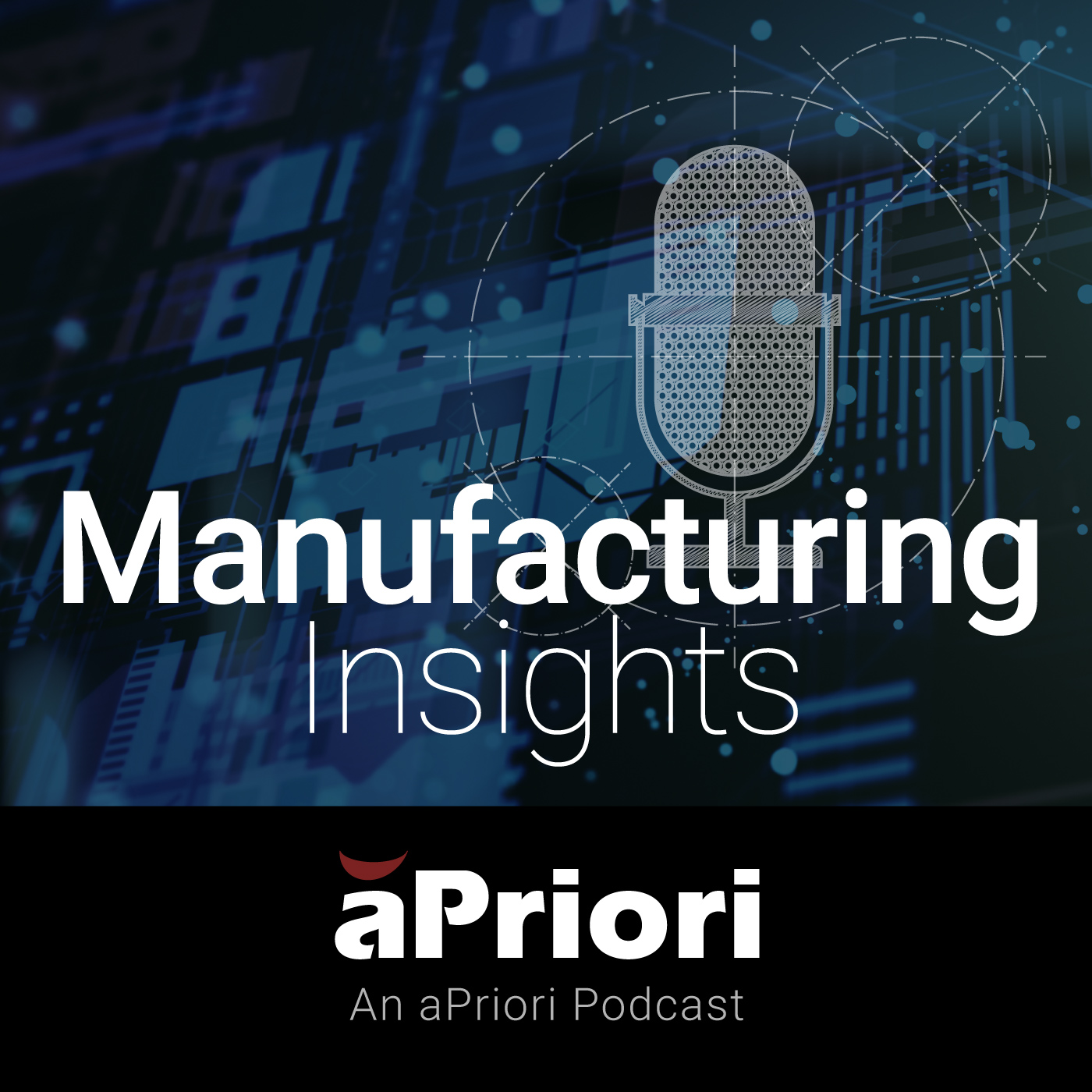