Transform Product Design Review Meetings Into Fast Design Validations
Key Takeaways:
- Successful product ideation and concept development require early design validations to eliminate risks and accelerate market entry
- Implementing aPriori into the new product development process helps teams overcome design review challenges, such as miscommunication, and streamline critical tasks
The Full Article:
Delays in product design reviews are common in the manufacturing industry. Such delays prolong product launches and cause significant financial losses for organizations across various verticals. For instance, PwC found that automotive original equipment manufacturers (OEMs) can face costs of up to $200 million due to a 12-month delay.
Examine critical design review challenges that prevent manufacturers from delivering high-quality, cost-effective, and competitive innovations on time during the new product development process (NPD). And explore how manufacturers can implement aPriori to validate early design decisions, accelerate internal collaboration, increase time for idea generation, and more.
Overcome Five Major Design Review Challenges Using aPriori Solutions
Five design review issues impact manufacturers’ ability to launch their innovations on time and meet dynamic customer needs, such as:
- Substandard Design Review Quality and Cross-Functional Feedback
- Miscommunication Across the Product Development Team
- Costly Late-Stage Engineering Change Orders (ECOs)
- Leveraging Outdated Design Tools in the New Product Development Process
- Inability to Access Dispersed and Crucial Product Manufacturing Data
In the following sections, we will explore each of these issues and discuss how aPriori can accelerate design reviews, validate concepts, and facilitate successful product launches.
1) Substandard Design Review Quality and Cross-Functional Feedback
Manufacturers lacking quality design review processes struggle to thoroughly assess risks in their product ideas or identify improvement areas early in the development cycle. Additionally, fragmented design reviews hinder teams from gaining feedback from relevant project stakeholders knowledgeable in making high-quality, cost-effective product iterations.
Overcoming this challenge with aPriori: Design engineers utilize aPriori’s automation-driven platform to break down barriers to valuable manufacturing insights. They quickly obtain actionable, precise guidance on product cost, carbon, and manufacturability in a single platform without taking experts’ time and resources to evaluate optimum design concepts.
Designers can employ aPriori’s digital factories to replicate real-world facilities and their functionalities virtually. These digital factories equip teams with nearly 90 Regional Data Libraries (RDLs) and 440+ Manufacturing Process Models (MPMs) to:
- Gain detailed, precise, and early-stage breakdowns of total manufacturing costs, including material expenses, regional labor rates, and manufacturing overhead (direct and indirect expenses, tool-shop rates, etc.)
- Benchmark product cost estimates to identify the most economical regions to source components, manufacture products, and more
- Simulate multiple production methods (e.g., additive manufacturing and assembly casting & forging) and routings with speed and precision
- Break down 3D computer-aided design (CAD) models into geometric cost drivers (GCDs) to accelerate the analysis of part cost, carbon, and optimal production routings
- Transform novice design engineers into seasoned experts with self-service insights based on real-world factors
2) Miscommunication Across the Product Development Team
Many large global manufacturers have dispersed teams across regions, often leveraging siloed technology with limited collaboration functionalities. This inefficiency can result in exhaustive back-and-forth discussions between project stakeholders and cause miscommunications that negatively impact time-to-market (TTM) targets.
Manufacturers can tackle these collaboration and communication problems by implementing cutting-edge digital technologies. According to McKinsey & Company, organizations that implement digital solutions can increase their product teams’ productivity by up to 30%.
According to McKinsey & Company, organizations that implement digital solutions can increase their product teams’ productivity by up to 30%.
Overcoming this challenge with aPriori: Manufacturers can utilize aP Workspace, aPriori’s robust collaboration and task management solution, to bring disconnected teams together in one platform. Consequently, relevant stakeholders can:
- Review 3D CAD files and centralize critical manufacturing data for rapid, more informed design decisions
- Assign scenario tasks and collaborate seamlessly and in real time on product cost, manufacturability, and sustainability
- Ask questions, provide comments, capture feedback, and gain project traceability
- Communicate design intent (i.e., why designers made specific design decisions) and evaluate their feasibility
Building on the power of aP Workspace, aPriori’s aP Generate solution enables stakeholders to configure and act on critical email alerts. These notifications help teams prioritize tasks, such as alerting design engineers about components requiring their immediate attention in aPriori. This data is also fed to the team’s single source of truth, such as product lifecycle management (PLM) systems.
3) Costly Late-Stage Engineering Change Orders (ECOs)
Inefficient design review and validation processes prevent teams from identifying critical product issues early in the development cycle. This results in expensive downstream problems, delayed launches, and the need for engineering change orders (ECOs). ECOs not only require time for product redesign but also jeopardize a manufacturer’s competitiveness, revenue generation, and ability to capture or maintain a large market share.
Moreover, PTC found that 40% of manufacturers struggle to incorporate late-stage design alternations into their product concepts, further prolonging development times.
Overcoming this challenge with aPriori: Forward-thinking product teams utilize aPriori to gain actionable cost, carbon, and manufacturability guidance early in the development process. Moreover, downstream teams can leverage these insights earlier to:
- Rapidly quantify risks and increase resiliency
- Boost agility in evaluating alternatives in material, manufacturing processes, production location, and more
- Reduce the need for costly and time-consuming ECOs that impact profitability
- Minimize quality assurance (QA) and supplier quoting issues, facilitate more efficient design work upfront, and make economical procurement decisions
- Accelerate Request for Quotation (RFQ) times, inform supplier selections and negotiate with the most suitable providers earlier
To further showcase aPriori’s power, watch the video below to learn how to use aP Workspace to accelerate decision-making and achieve product development milestones.
4) Leveraging Outdated Design Tools in the New Product Development Process
Many companies still utilize error-prone, cumbersome Excel spreadsheets to store critical manufacturing data, including design review feedback. However, spreadsheets are limited to text, preventing teams from leveraging 3D CAD models to review and validate their final product concepts effectively.
Additionally, companies employing spreadsheets often face version control issues and outdated data, which cause miscommunication and overall confusion for product development teams.
Overcoming this challenge with aPriori: Organizations can leverage aP Workspace to make crucial manufacturing data available to cross-functional teams, empowering them to collaborate and act on these insights. aPriori presents this data in an intuitive, visual way, enabling teams to pinpoint and solve product issues early, share ideas, and gain rapid design feedback to inform decisions. As a result, product development teams can expedite design review meetings and reach critical milestones faster.
5) Inability to Access Dispersed and Crucial Product Manufacturing Data
Many teams are limited to traditional design tools that fail to tell the “complete story” of a product concept’s cost structure, carbon impacts, and viability. Consequently, teams struggle to accurately present their findings in design review meetings and gather the necessary feedback to create successful product iterations.
Some examples of widely used design tools include a combination of the following:
- PLM systems
- CAD viewers
- Supplier quotes
- Previous product design history
- Business intelligence (BI) reporting solutions
The limitations of these tools make effective decision-making even more challenging for product development teams, slowing down continuous innovation.
Overcoming this challenge with aPriori: Design engineering teams can employ aPriori solutions to automate multiple tasks and increase innovation time. They also gain real-world manufacturing data within a single platform, eliminating the need for extensive market research to inform business and NPD decisions. Designers can even use aPriori to request support from experts and receive immediate responses without the need for time-consuming design review meetings.
Streamline Design Reviews, Eliminate Launch Delays, and Achieve Product Success
Manufacturers transforming complex, misaligned design review meetings into fast product validations position themselves better to eliminate costly launch delays and increase time for innovation. By implementing aPriori solutions, companies can identify and eliminate design risks early to bring cost-effective, high-quality, and sustainable products to market faster.
Product Design: Reduce Cost, Carbon, and Risk
Watch this on-demand webinar to learn how aPriori empowers design teams to optimize product cost and carbon efficiency seamlessly.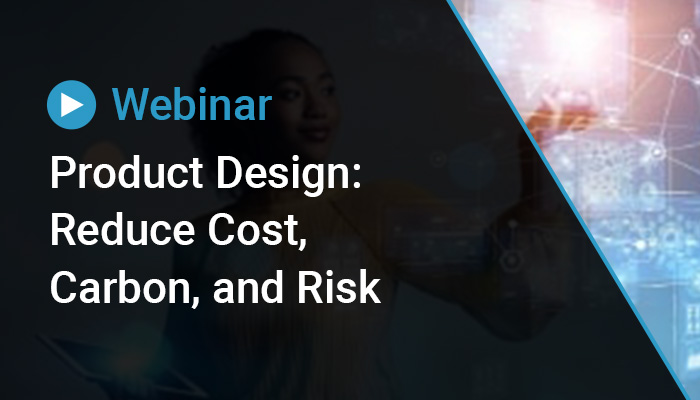