Overcoming Global Supply Chain Issues Through Cost Engineering
Unprecedented regional and global disruptions have had an impact on how companies source their components and manufacture products today. Companies are facing insurmountable pressure from global supply chain issues and must identify viable opportunities to achieve supply chain resilience.
As the supply chain crisis continues, organizations cannot afford to engage in time-consuming, cross-functional back-and-forth discussions to make strategic decisions. They require simulation-driven manufacturing intelligence to receive immediate, actionable cost and design guidance based on real-world global supply chain issues.
Cost engineers complement the capabilities of manufacturing intelligence software with their extensive costing knowledge and influence across the product team. Cost engineering departments ensure that manufacturing software insights are distributed and acted on immediately by their design and sourcing colleagues.
In this article, we will explore what is causing supply chain issues in today’s global manufacturing landscape. We also look at the significance of a cost engineering department in overcoming global supply chain issues that affect businesses.
What is a Global Supply Chain?
Global supply chains encompass all the activities, stakeholders, and resources used in multiple locations to manufacture and distribute a product. Manufacturing companies must follow and address four key steps to accomplish effective global supply chain management, such as:
- Product Design Engineering. Dedicated design engineers create initial product concepts to launch an organization’s product development process. The most effective product designs are optimized for both cost and manufacturability right from the start.
- Raw Material Sourcing. Sourcing professionals must evaluate and select viable global suppliers who provide reasonable prices for critical raw materials. Modern organizations strive to make more ethical and sustainable material and sourcing decisions. Indeed, Deloitte reports that most manufacturing companies aim to significantly reduce their carbon footprint by 2050 to achieve net-zero emissions.
- Product Manufacturing. Manufacturing teams are responsible for identifying and selecting the best, most cost-effective locations to produce a given product component. Companies must consider variables like geographical labor, overhead, and tool shop rates to make more strategic and informed business decisions.
- Outbound Logistics and Transportation. Organizations must compare product delivery methods to determine how their products will be delivered to the consumer or end user. They must also consider the carbon emissions and regional shipping costs associated with each product delivery option. Most manufacturers today are building supply-chain decarbonization strategies to ensure they only do business with eco-conscious shipping companies. According to McKinsey, decarbonization encourages shippers to use alternative fuels to reduce carbon emissions by up to 60 percent.
What is Causing Supply Chain Issues?
Several external factors or disruptions continue to contribute to today’s global supply chain issues, which affect how manufacturing companies operate. These supply chain disruptions have impacted supplier capacity, lengthened lead times, and raised shipping costs in the current manufacturing environment.
The COVID-19 pandemic and Russia’s war on Ukraine have been major events that contributed to the current supply chain crisis. For instance, the COVID-19 outbreak has caused factory closures and a labor shortage, decreasing global component production capacity.
Chip shortages in the global auto industry have stymied automakers’ electrification efforts and cost them $210 billion in revenue. The ongoing Russian-Ukrainian war has only exacerbated the situation, as Russia exports 35 percent of the palladium needed in semiconductors. Ukraine, on the other hand, controls 70 percent of the global market for raw gas materials used in chip production.
According to KPMG, events such as the COVID-19 pandemic continue to affect global supply chains in the following five ways:
- Labor Constraints and Talent Shortages. It is difficult to manufacture and deliver products to global consumers when there are no workers available to do so. Labor market shortages have made it impossible to meet rising customer demand, exacerbating today’s global supply chain issues.
- Global Logistics and Transportation Challenges. Major port closures, such as those in China, restrict the flow of goods into key markets such as the U.S. There is also port congestion, which creates a backlog of shippers waiting to offload a company’s goods on busy global docks. At its core, these global supply chain issues delay the delivery of manufactured consumer goods to the end user.
- Critical Production Delays. It is a challenge for manufacturers to develop a product when they lack all the necessary raw materials. The ongoing supply chain crisis has limited the availability of key commodities and pushed manufacturers to compete for raw materials. This is especially true in the global auto industry, where many automakers are still dealing with unprecedented chip shortages.
- Rising Commodity Prices. As commodity prices rise, some procurement departments lack the transparency and visibility required to make informed purchasing or spending decisions. Today’s global supply chain issues make it difficult for procurement to determine how, when, and where they should purchase materials.
- Overreliance on Limited Suppliers. Many companies have only established business relationships with one single global supplier. This prevents organizations from having a backup plan when global supply chain issues emerge and affect raw material availability. Further, organizations cannot compare supplier prices and are unable to gather these insights by only doing business with one provider. It is crucial to building a multi-sourcing strategy to better combat the supply chain crisis and achieve supply chain resilience.
What Role Do Cost Engineers Play in Overcoming Global Supply Chain Issues?
Cost engineers have the expertise to assess the costs of supply chain options, allowing organizations to make more cost-effective decisions. However, the supply chain crisis has pushed cost engineers to make more immediate estimates to ensure organizations capitalize on scarce opportunities. The need for faster projections has increased the risk of miscalculations and human error when evaluating supply chain costs.
Cost engineering departments require manufacturing intelligence software to expedite the costing process during global supply chain issues. The automated, simulation-driven software provides comprehensive cost insights associated with raw materials, global factories, manufacturing processes, labor rates, and more. Manufacturing intelligence software leverages real-world supply chain conditions and other critical variables to generate highly accurate cost estimates.
The software assists cost engineers in navigating supply chain disruption across three phases: react, recover and reinvent. The three phases are described in detail below:
Phase 1: React
Cost engineers can use manufacturing intelligence software to find cost-effective alternative suppliers if a vendor faces material capacity issues. The software gives cost engineers on-demand insight into the cost implications of all major manufacturing regions of the world.
Cost specialists can simulate the entire manufacturing process of a region to generate should cost estimates. Sourcing professionals can leverage these highly accurate should costs to initiate fact-based supplier negotiations and achieve savings on critical components.
Costing departments can configure the software to produce estimates based on order quantities, material costs, labor costs, and more. These cost insights allow manufacturing companies to diversify and future-proof their supply chain strategies to achieve supply chain resilience.
Phase 2: Recover
Manufacturing intelligence software provides costing departments with automated cost and risk insight into multiple production scenarios or critical assemblies. It also produces comprehensive cost breakdowns for individual components, allowing an entire product team to strike a cost-risk balance. Cost engineers and manufacturing software collaborate to ensure that organizations have the knowledge they need to recover from global disruptions.
Phase 3: Re-Invent
Cost engineers can leverage manufacturing intelligence software to generate real-time cost and manufacturability guidance. These insights enhance cost and design team collaboration to eliminate manufacturability issues and cost drivers in every component design.
The power of manufacturing intelligence software assists cost engineering in identifying more cost-effective and sustainable production processes. The software calculates the carbon footprint of industrial processes such as plastic molding, sand casting, and sheet metal fabrication. These insights are crucial for manufacturing companies looking to reduce their carbon footprint and achieve net-zero emissions.
Conclusion
Today’s global supply chain issues have created uncertainty in the way manufacturing companies produce and deliver their products to consumers. Organizations can overcome the supply chain crisis by having a dedicated costing department equipped with the latest manufacturing intelligence solution.
RISK-PROOF YOUR SUPPLY CHAIN
Learn how to use data to mitigate the cost of disruptions and turn supply chain resiliency into a competitive advantage.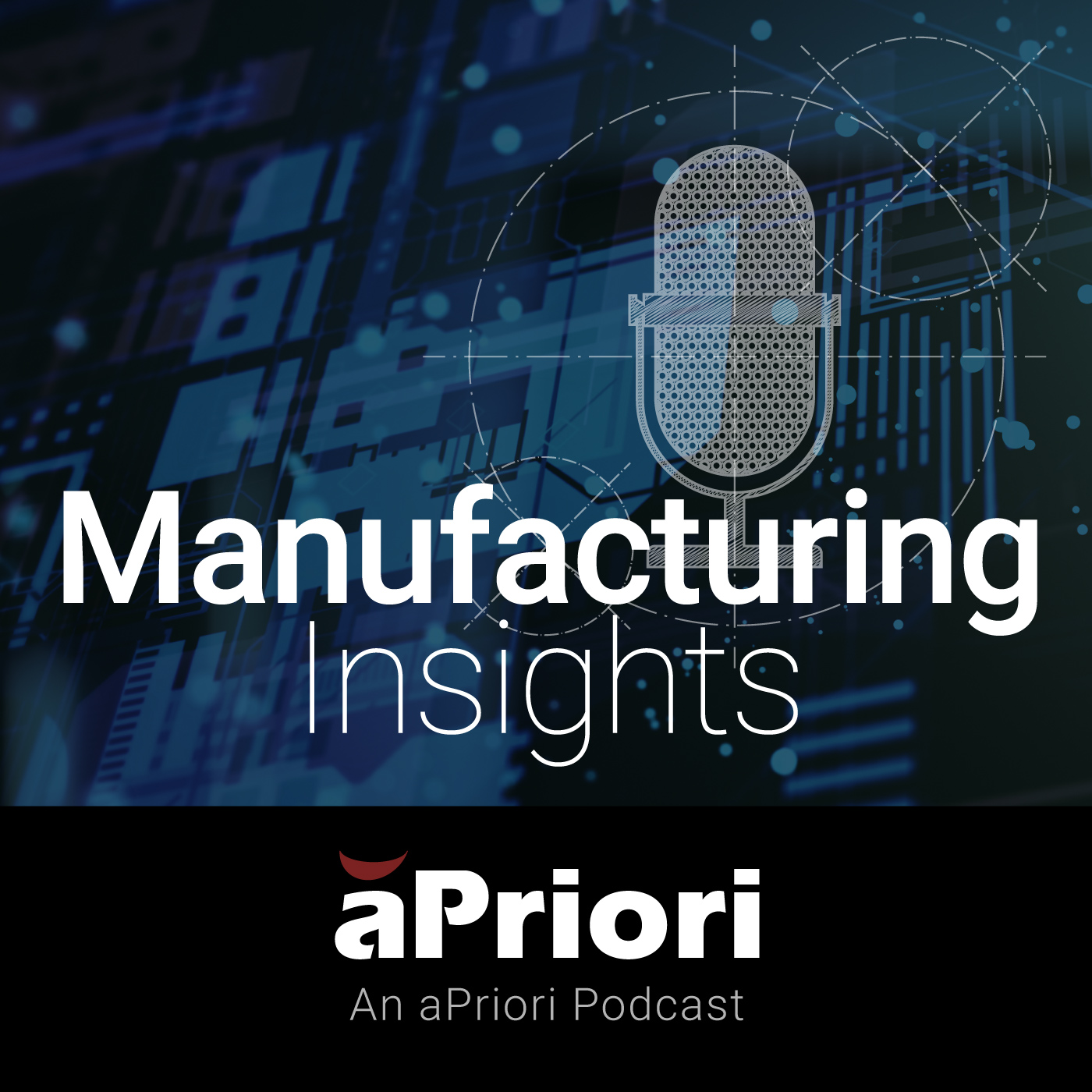