Nearshoring’s Labor Hurdle: Finding Skilled Workers
Key Takeaways:
- Skills Gap is a Major Hurdle: The most significant challenge is the lack of skilled workers with the technical expertise required for modern manufacturing, including robotics, AI, and advanced technologies.
- Workforce Development is Crucial: To overcome this, manufacturers must invest heavily in workforce development initiatives, such as apprenticeships, on-the-job training, and upskilling programs.
- Collaboration is Key: Addressing the labor challenge requires a collaborative effort between government, industry, and educational institutions to develop and implement effective solutions.
The Full Article:
A North American Desire for Geographic Proximity
The siren song of nearshoring – bringing manufacturing back to North America, including Mexico – is alluring. U.S. companies are drawn to the promise of shorter, more cost-effective supply chains, fewer disruptions, lower transportation costs, greater control, and reduced environmental impact. Yet, as they begin this journey, a sobering reality awaits: the overwhelming lack of skilled labor available to staff new manufacturing facilities.
A KPMG survey earlier this year found that 73% of U.S.-based executives said their companies have brought or are bringing back more of their global supply chains to the Americas because of geopolitical and economic uncertainty, including potential tariffs.
A Return to Onshoring
Decades of offshoring to locations such as Asia, and more specifically, China, have taken a toll. Although the immediate benefit might have been cost savings, manufacturing educational and training programs atrophied, leaving a void of skilled workers. Now, as factories hum back to life, they struggle to find individuals with the technical prowess to operate sophisticated machinery, program robots, and harness the power of Industry 4.0 technologies.
Imagine this: a gleaming new factory, a testament to the promise of nearshoring, stands eerily silent, not because of a lack of orders but a lack of qualified hands. Skilled workers are a rare commodity, snatched up by other sectors like technology and healthcare. The talent competition is fierce, and manufacturers must offer competitive wages, attractive benefits, flexible work arrangements, and a workplace culture that values employee well-being.
More than 60% of employers in a recent survey by the National Association of Manufacturers said attracting and retaining talent is a top concern. Source: WSJ
The problem isn’t just about finding new talent. A significant portion of the existing manufacturing workforce is nearing retirement, taking with them decades of invaluable experience and institutional knowledge. Additionally, the pandemic exacerbated the labor shortage as many decided to exit the traditional workforce altogether. This creates a double whammy: a shortage of young talent and a looming loss of seasoned expertise.
Philippe, a seasoned manufacturing engineer, remembers the days when skilled trades were revered. “Back in my day,” he recalls, “high school offered robust vocational programs. You could learn to weld, operate machine tools, and understand the intricacies of manufacturing processes. Now, those programs have largely disappeared, replaced by a focus on college degrees.” This lack of foundational training has created a significant skills gap. Modern manufacturing facilities increasingly rely on advanced technologies like robotics, automation, and artificial intelligence. Workers must be proficient in operating these technologies, analyzing data, and solving complex problems. Stephanie, a recent graduate with a degree in mechanical engineering, was eager to join the manufacturing sector. However, she found herself underqualified for many positions. “While my degree gave me a solid theoretical foundation, I lacked the practical skills and hands-on experience employers were looking for,” she explains. “I realized I needed to bridge this gap through additional training and certifications.” This realization is dawning on many manufacturers as well. They are beginning to recognize the urgency of the situation. They invest in robust apprenticeship programs, partner with educational institutions to develop relevant curricula, and offer on-the-job training programs to upskill existing workers.Building Technological Upskilling Frameworks
Leverage Data As The New Currency To Shore Up Your Supply Chain
Discover how to mitigate supply chain risks, streamline sourcing and improve supplier relations, get to market faster, and lower costs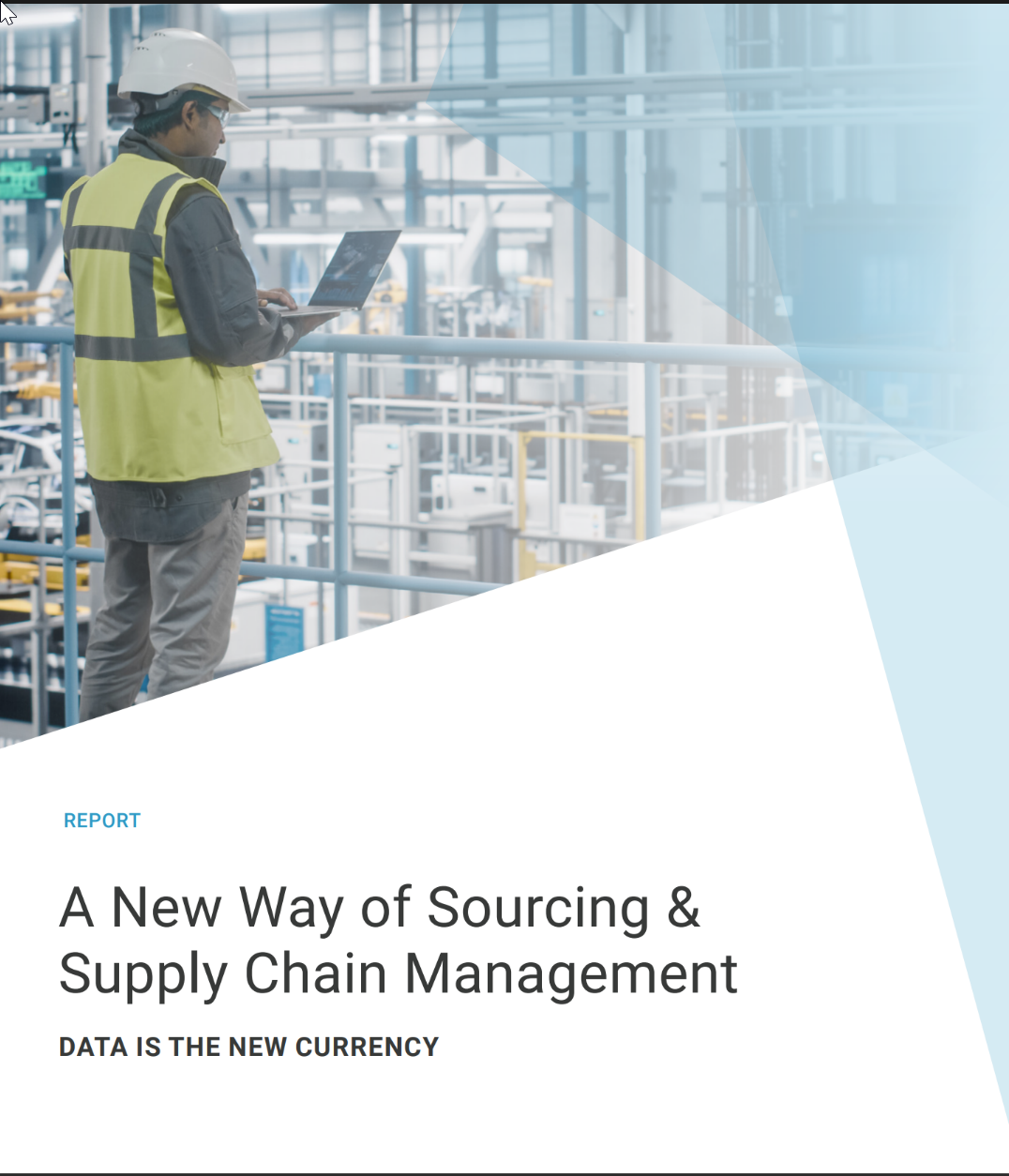