How Product Costing Software Turns Novices Into Cost Experts
Manufacturing companies understand the importance of applying cost engineering principles across the product life cycle. This can help ensure that product teams meet new cost targets by bringing a cost-first perspective to design and sourcing.
However, companies fail to create a cost-first culture when their cost engineering teams use outdated systems and manual processes. Without modern technology, cost engineers need enough expertise and time to analyze high volumes of new or redesigned products. This prevents them from providing fast cost-reduction feedback to design and sourcing teams.
Today’s cost engineers need simulation and data-driven product costing software. Advanced costing solutions help engineers of all skill levels estimate product costs and share insights across the company quickly and accurately.
This article gives an overview of product costing software and how it enhances cost analysis processes for cost engineers. It also assesses how the software can help create a cost-first culture for companies.
What is Product Costing Software?
Product costing software, such as aP Pro, estimates and captures the cost of new products early in the design phase. It leverages manufacturing cost models and regional data libraries to run accurate cost simulations in real time. Paired together, the data creates “digital factories” to help cost teams identify and reduce cost impacts in designs.
At its core, the software gives companies insight on how to optimize new product costs to maximize margins. The advanced software ensures that companies achieve their product cost optimization goals.
Challenges of Not Having Product Costing Software
Companies give up speed and transparency when using spreadsheets for product costing. For instance, cost engineers must access the files just to perform calculations that are prone to human error. They are also responsible for the upkeep of the files to ensure that they are updated and accurate. This manual process wastes time and prevents design teams from getting quick cost insights into their designs.
Traditional spreadsheets cannot keep pace with the demands of modern product development timelines. Product teams must have accurate, real-time costing feedback to meet their cost targets and time to market (TTM) objectives.
Alongside spreadsheets, there are companies that may use product life cycle management (PLM) systems to store product data. Some firms have siloed PLM systems that are underutilized, making it a challenge for cost teams to find relevant data quickly. Disconnected data often leads to the risk of higher design costs for product teams.
Without the right tools, cost teams lack a baseline level of transparency to know what cost outliers they must prioritize. They are also unable to analyze and manage large volumes of products as their role requires. This is especially challenging for under-resourced novice teams that are expected to make quick cost estimates.
Key Benefits of Product Costing Software
It is reported that 80 percent of product costs are determined in the first 20 percent of the product development process. This reaffirms the importance of having a design-to-cost (DTC) strategy that is supported by data-driven product costing software. Companies that modernize processes such as product costing can boost their team’s productivity by 26 percent.
The algorithms behind product costing software modernize the cost analysis process for all cost engineers. Algorithms use the “digital twin,” or a 3D CAD virtual representation of a product, to extract design features for manufacturability analysis. Digital factories that are derived from real-world manufacturing conditions are also used to provide more accurate cost estimates to teams.
Seasoned cost teams can use costing software to work more accurately and efficiently. They can also scale to handle higher workloads. The software is designed to support the expertise of well-versed cost engineers.
For more novice teams, it is no longer necessary for them to use outdated systems that are prone to human error. Instead, they can make quick and accurate estimates through advanced software with minimal configurations. Below are four ways product costing software can turn novices into highly skilled cost experts:
- Leveraging Real-World Conditions. Digital factories simulate the way real-world conditions may impact product costs early in the design phase. This allows cost engineers to estimate costs based on certain factory conditions, material costs, manufacturing processes, labor rates and more. Put simply, the software uses the real world to provide more timely cost estimates to product teams. It also gives them the confidence to know what products they must prioritize and modify.
- Enhancing DTC. Detailed cost insights allow cost engineers to help design teams create high-quality designs at lower costs. Costing software helps reduce the time it takes to develop a product by 30 to 50 percent by closing the gap between cost and design teams early in the development cycle.
- Running Batch Simulations. Product costing software can be set up to analyze and handle thousands of new product designs at once. Cost engineers can quickly identify cost outliers where the sourcing team is paying their suppliers too much. With more accurate cost estimates in hand, sourcing teams can confidently start fact-based negotiations with strategic suppliers to achieve savings.
- Organizing Cost Data. Cost teams can more efficiently aggregate and analyze historical and current cost data in one central location. They can use these insights to make quick and effective cost decisions as needed. It is no longer necessary to spend time looking for cost data in siloed sources, such as spreadsheets and PLM systems.
Modernize Product Costing to Create a Cost-First Culture
The key to creating a cost-first culture in manufacturing is to modernize the product cost analysis process. Companies must have product costing software to automate and simulate the way costs are estimated in the design stage. That way, cost engineers of all skill levels can make accurate projections and provide timely cost-reduction guidance to product teams.
The Anatomy of Product Cost
Cost estimation is full of challenging uncertainty. Learn how digital manufacturing simulation helps cut through the variance and focus on a product’s true economic cost.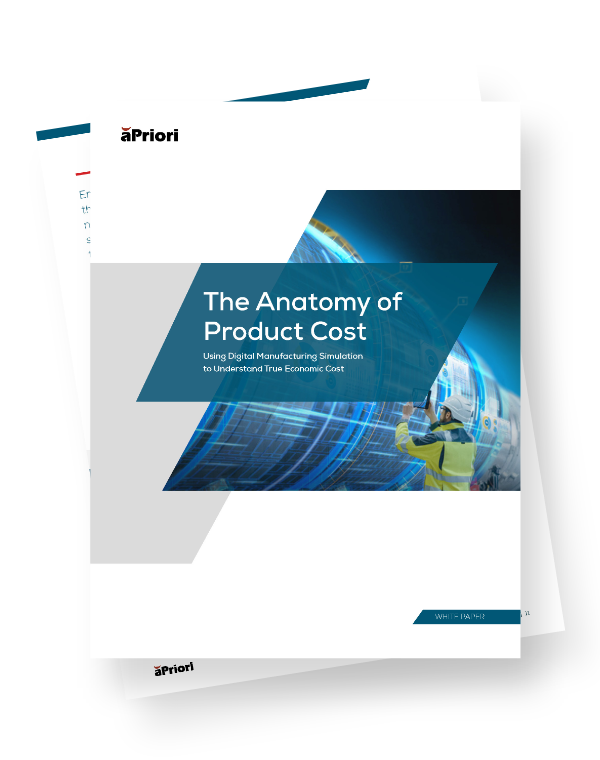