Improving Production Performance with Cost vs. Carbon Manufacturing Process Models
Key Takeaways:
- Cost vs. carbon can be evaluated via manufacturing insights
- Manufacturing insights reduce costs, lower CO2, and improve production performance
The Full Article:
News of climate change appears dire. Many question whether net-zero goals are realistically achievable. Despite the gloomy outlook, efforts are being made where it matters, with steps being taken to reduce greenhouse gas emissions. The United Nations noted that more than 70 countries, including the biggest polluters – China, the United States, and the European Union – have set a net-zero target, covering about 76% of global emissions. More than 3,000 businesses and financial institutions are working with the Science-Based Targets Initiative to reduce their emissions in line with climate science. And more than 1,000 cities, over 1,000 educational institutions, and over 400 financial institutions have joined the Race to Zero, pledging to take rigorous, immediate action to halve global emissions by 2030.
As organizations push sustainability goals forward, ensuring optimization of how products are designed and manufactured is integral to minimizing our carbon emissions and waste while remaining profitable. A holistic approach, where most improvements can be made, ensures both sustainability and profitability without sacrificing manufacturability.
Why Manufacturing Process Models are Key to Cost, Carbon, and Performance
For over 15 years, aPriori has been developing manufacturing process models (digital twins of the manufacturing process) for better production performance. Utilizing these manufacturing process models is crucial; not only to reducing carbon emissions but to keep costs in line while ensuring manufacturability and time to market. To fully harness and maximize its power, manufacturers can:
- Reduce material waste from design through production: With sustainability and manufacturability insights, processes primed for waste reduction can be identified. They could potentially be cut out altogether early in the design stage.
- Decrease energy consumption and sources: Manufacturing insights can pinpoint unnecessary, energy-sapping materials and processes such as long cycle times and focus attention where finding environmentally friendly alternatives will make the most impact.
- Streamline facilities: 54% of the world’s energy consumption is from manufacturing. Manufacturing insights can reveal excess waste and optimize production processes, resulting in less factory time, energy usage, and cost.
A solution capable of identifying material waste, excess energy consumption, or other similar factors in parts design or manufacturing processes can lower CO₂e.
An Example of Cost vs. Carbon Balancing in Action
The automotive industry is a good example of cost vs. carbon for production performance. Lightweighting (optimizing performance vs. weight ratio) is a prime illustration of cost vs. carbon to improve production performance. Many automakers are shifting to lightweighting for electric vehicles. Fiber-reinforced plastic polymers can be used as structural components in and around an electric vehicle’s high-heat areas, such as battery packs and motors. As a result, the electric vehicle is lighter, uses less energy, and is better performing.
Using less material will almost always mean reduced CO₂e. The biggest impact will be in lowering the in-use phase – the largest CO₂ footprint of a product. Manufacturing process models like those developed by aPriori enable design engineers to baseline a product’s environmental impact for reporting and identify CO₂ outliers.
Manufacturers then can optimize components for cost and CO₂ equivalents while ensuring manufacturability and lowering the total cost to manufacture. Manufacturing process models are integral to transitioning from traditional automobiles to electric vehicles before production. The digital factory twin can evaluate CO₂e across the value chain (Scope 3 and from “cradle-to gate”) in these early development stages.
How aPriori Manufacturing Insights Reduce Carbon and Improve Production
There are many manufacturing factors to consider including material waste, machine energy input, etc. It requires a tool advanced enough to consider all sustainable production factors, compute an accurate measure of carbon, and provide improvement recommendations.
aPriori’s Sustainability Insights calculates these factors to understand their carbon footprint impact along with manufacturability and cost. It then reduces waste throughout a product’s creation and lifespan including raw materials and manufacturing processes that impact the environment.
Process mapping helps manufacturers understand how much energy a machine uses throughout the entire operation. Consequently, a manufacturer will get a very precise calculation of their energy usage as well as each machine’s CO₂e output. Even better, these sustainable production calculations can be tailored to specific facilities. For instance, you can calculate carbon outputs and energy usage for a solar-powered factory as well as a wind-powered one, comparing the computations.
Additionally, product development teams can use trade-off analysis to compare designs, materials, and processes for sustainability. With aPriori digital factories, manufacturing teams gain full visibility into sustainability, cost, and manufacturability. More informed decisions can be made to reduce environmental impact based on the analysis. A CO₂e footprint breakdown analyzes and helps implement sustainability actions.
Sustainable production is seamless with other aPriori solutions. aPriori will run calculations in parallel with a customer’s current aPriori solution. Sustainable production will be reportable too. Cost vs. carbon calculations is not limited by the number of parts either. For instance, 10,000 existing parts run through aPriori allow a manufacturer to recost parts and generate a sustainability report concurrently from part to assembly to the complete product.
Sustainable production is integrated with the same calculation as design for manufacturability and design for cost. The user simply answers four major questions:
- What’s my manufacturing process?
- What materials am I using?
- Where am I sourcing materials and manufacturing products?
- What’s my annual batch and production volume?
In aPriori you get feedback for cost, design for manufacturability, and sustainability.
A Solution that Achieves Sustainability and Profitability
One thing to keep in mind is that lowering carbon emissions does not just happen at the production stage. In fact, those manufacturers who view carbon reduction throughout the product development lifecycle stand the greatest opportunity to substantially reduce CO2, keep costs in line, and ensure manufacturability – all without impeding time to market.
aPriori facilitates this capability seamlessly and precisely. Manufacturers gain insights that might not have occurred to them – whether it is the origin of the materials used or each step required in production. aPriori provides these details and recommendations to mitigate the carbon impact without sacrificing profitability.
Sustainability and Profitability Are Within Reach
See how real-time design and manufacturing insights impact cost, carbon & performance.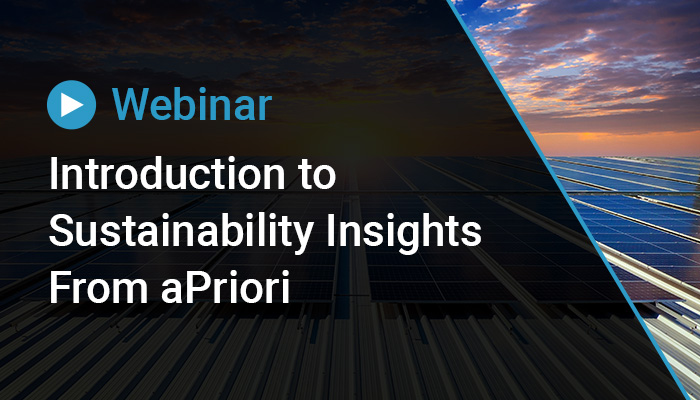