How Signify Captures Savings With Automated Should Costing
Key Takeaways:
- To remain a leader, Signify procures parts at the best price, quality, and availability
- Automation enables rapid “should cost” calculations for added savings
- The future of procurement: Controlling costs and contributing to a more sustainable world
The Full Article:
For more than 130 years, Signify has been brightening where people work, live, and play—and points in between—with lighting products and solutions. The leader in the lighting industry generates nearly €7 billion annually from its venerable brands, including Philips, Color Kinetic, and Interact. Signify also offers light fidelity (LiFi) and connected LED systems that communicate and share valuable data through wireless networks.
The lighting manufacturer’s innovations are designed for consumers, professional customers, and the Internet of Things (IoT). It also provides lighting-based components for professional applications in the original equipment manufacturer (OEM) market.
Signify is committed to making an ethical, lasting impact on the world. It has 100% carbon-neutral operations and aims to double its positive environmental impact by addressing six of the U.N.’s Sustainable Development Goals (SDGs). This allows the manufacturer to continue building a path toward brighter lives and a better world.
Business Challenge: Balancing Procurement Speed, Cost, and Quality
Signify is focused on procuring the most sustainable, advanced, and cost-effective components for its extensive product portfolio. Importantly, it wanted to ensure it could vet supplier quotes quickly to uncover more cost-saving opportunities.
To maintain its position as an industry leader, Signify knew it needed to optimize its procurement strategy through digitalization. “Signify has been engaged in an intensive digitalization program for several years,” said Arnold Chatelain, Transformation Program Director for Signify. “Our goal is to use state-of-the-art tools to transform the role of procurement…and automate should cost analysis to identify the parts that can be negotiated with suppliers.”
The company needed a systematic, automation-driven should cost analysis tool to challenge more supplier quotes quickly and accurately. The ideal technology would provide Signify with the cost-based intelligence required to procure components at the best price, quality, and availability.
“Automation unlocks a great potential of doing more should cost calculations to challenge way more quotes. This is something we needed.” – Robert Ottens, Design for Excellence (DfX) Manager for Signify
Enter Automation: Should Cost Goes Digital at Signify
Signify selected aPriori in 2017 as part of its procurement strategy. It uses aPriori’s automated should cost analysis software on the cloud to unlock granular, accurate insights into a product’s total cost structure.
aPriori’s should cost estimates serve as a benchmark for determining fair market costs for several buying and manufacturing processes. “If our suppliers do not reach these benchmarks, we can have a constructive and fact-based discussion to understand the root cause and take the right action to remain competitive,” said Luc Broussaud, Global Head of Procurement for Signify.
Since deploying aPriori, Signify has gained the cost breakdowns and actionable guidance required to build better, cost-effective products in less time. With aPriori’s should cost analysis tool, the lighting manufacturer can:
- Identify and address underlying cost drivers. aPriori considers real-world factors, including labor rates, raw material costs, and overhead expenses, to provide early visibility into a product’s underlying cost drivers. Signify can now identify the factors increasing product costs and respond by making highly informed, cost-effective redesigns.
- Increase should cost efficiency and coverage. Automated, simulation-driven costing capabilities allow Signify to analyze thousands of part designs quickly and simultaneously.
- Improve supplier negotiations and sourcing decisions. With granular should cost estimates in hand, Signify can inform supplier negotiations and collaborate on cost reduction. The company can also enhance strategic sourcing decisions and cultivate relationships with suppliers with the most efficient production capabilities.
Automation in Action: Using aPriori’s Should Cost Analysis Tool
aPriori’s should costing solution makes it easy for Signify to analyze the cost of a part or an entire group of components. aPriori threads three digital twins together—product, process, and factory twins—to automatically provide end-to-end visibility into accurate, real-world cost insights. Using aPriori’s economic-specific Regional Data Libraries (RDLs), Signify can also create a digital factory for each supplier and generate cost estimates for 87 regions.
Here’s how aPriori’s should cost analysis tool works:
- The platform automatically analyzes the 3D CAD models checked into Signify’s product lifecycle management (PLM) system. In just minutes, aPriori will deliver transparent cost, manufacturability, and even carbon dioxide equivalent (CO2e) calculations through the digital factory twin.
- To identify savings opportunities, Signify compares aPriori’s automated should cost breakdown reports with suppliers’ quoted price increases.
- Signify leverages aPriori’s insightful cost forecasts to conduct collaborative, fact-based supplier negotiations and get the best price on components.
Signify also uses aPriori to gain early, actionable design guidance to make informed product iterations quickly. “You can ask for a should cost calculation and also get design feedback,” said Ottens. “It’s almost like charging your car and getting it washed for no additional fees. aPriori gives you design feedback insights to optimize products for manufacturing and cost.”
With aPriori, Signify can eliminate the risk of costly, end-stage engineering change orders (ECOs) by optimizing designs early in product development. As a result, the manufacturer can bring its quality, sustainable, and cost-effective lighting innovations to market faster.
Signify Achieves an 8x Increase in Parts Analyzed
Signify can now perform over eight times as many cost calculations as before using aPriori’s automated should cost analysis tool. “Before, it was only possible to calculate the cost of 1,000 parts,” said Ottens. “With automation, we can now do 10,000 plus calculations, which means that cost masters will go from analyzing 300 to 3,000 plus parts per year.”
This year, Signify will execute its SCAN Signature Program to extend the use of aPriori’s should costing tool to research and development (R&D). The SCAN program also aims to make should costing a savings contributor visible to management.
“We are executing the SCAN Signature Program to get should costing in the DNA of procurement and R&D,” said Ottens. “Requests will go up, reporting is executed in our systems, and then management will see the return on investment visible.”
Signify also plans to use aPriori’s Sustainability Insights to help reduce its carbon footprint this year. Ottens notes that Signify intends to add more commodities, move toward complete assemblies, and improve its carbon footprint at the drawing board. This will enable Signify to maintain and promote a robust Design for Sustainability (DFS) culture across its product development team.
As demonstrated, aPriori’s automated should cost analysis tool supports Signify’s ongoing commitment to creating a better world through innovation and increased sustainability. Global manufacturing powerhouses like Signify now have an advanced, transformative cost modeling solution to balance the environment and profit margins.
How to Build a Costing Department
Hear from Kearney to learn how to develop a costing team to get to market faster and with greater profit.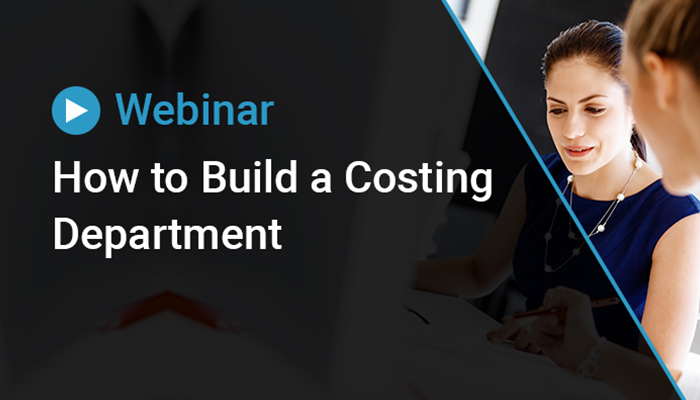