2022 and Beyond Manufacturing Industry Outlook: Priorities for Navigating the Road Ahead
Tectonic shifts in the economy have reshaped the manufacturing industry outlook and will continue to do so in 2022 and beyond. Ongoing concerns about resiliency, safety, and shifting customer needs will influence business decisions as companies continue to navigate supply chain disruption, economic uncertainty, and pandemic-related issues.
To address these market realities, manufacturers have been implementing digital capabilities to gain new levels of speed, efficiency, agility, and to launch new solutions. And expect the emphasis on digital transformation (DX) to continue in 2022 and beyond.
Below, we’ve highlighted four manufacturing sector priorities based on trends we’re seeing and what we’re hearing from global manufacturers, suppliers, and other industry experts.
1. Calibrate your Strategy for High Impact
Are you digitizing your business to make incremental gains, or are you leading DX to gain a competitive edge?
Companies that envision new ways to support tomorrow’s customer needs can prioritize the resources needed to reach their targeted goals. But manufacturers that don’t have a clear DX strategy often miss the mark, as up to 70% of DX efforts don’t meet expectations.
DX is an ongoing process that requires a strategic vision, a cohesive plan, and ongoing business support. Because enterprise solutions are typically deployed in phases, manufacturers running DX-enabled solutions typically still rely on some manual intervention to use information stored in spreadsheets and legacy systems.
The likelihood of mistakes using this manual approach increases as teams try to track volatile pricing for raw materials and components. Spreadsheets break the digital thread and risk introducing incorrect information to the planning process that can’t be audited or used easily for analysis.
To better manage this fluid element of product development, manufacturers are increasingly prioritizing their DX efforts to incorporate sourcing. This includes making product development stakeholders aware of sudden sourcing changes and enabling them to reassess their options quickly as a team. Individual sourcing teams can also use DX to help streamline and manage an increasingly complex quoting and procurement process. (Watch how Harbec’s automating quoting process accelerates time to market.)
By realigning DX priorities to address their most pressing business challenges, manufacturers can increase the effectiveness of their investments.
2. De-risk and Diversify your Supply Chain
Although some backorders are slowly being filled, businesses and consumers are preparing for supply chain delays through the second half of 2022 and rethinking supply chain strategies. Proactive manufacturers are responding by strengthening relationships with key suppliers to tap into their vendors’ expertise, control costs, and ensure access to critical materials and components. By adopting a strategy focused on shared risk and reward, all parties are incented to succeed based on common goals. Companies with collaborative supplier relationships can outperform their industry competitors by nearly 2X, according to McKinsey.
In this model, manufacturers share their strategies and involve suppliers early in the development process. Real-time digital collaboration enables manufacturers and suppliers to work quickly and efficiently using current digital twin product information, manufacturing simulation results, and should cost benchmarks for materials and production. With this information, suppliers can identify opportunities to improve product designs while OEMs can help suppliers reduce production costs, accelerate operations, and resolve potential capacity issues.
Companies are also expanding their global footprint to increase resilience. Intel, General Motors, and other established brands are increasing their US manufacturing capacity while companies such as EV manufacturer Rivian are opting to expand production in America instead of internationally.
3. Do More with Less (Address the Manufacturing Skills Shortage)
Businesses continue to face workforce shortages in filling technical manufacturing and product development roles. The US National Association of Manufacturers (NAM) projects that unfilled manufacturing jobs will increase from 500,000 in 2021 to 2.1 million by 2030. The lack of qualified candidates, along with employee retention challenges, can have a material impact on companies that don’t have the staff to meet demand.
Automation throughout the product development lifecycle can reduce time-consuming manual tasks and frees teams to focus more time on innovation. Design engineers, for example, can be alerted when a product component doesn’t meet design for manufacturing/excellence (DFM/DfX) specifications, and use automated guidance to make changes before cost engineers review the designs. (See how Spirit Aerosystems captures additional cost savings with DFM.)
Similarly, more than half of a procurement organization’s time is spent on transactional activities, according to SAP. Digital automation, integration, and collaboration continue to streamline and accelerate procurement. Manufacturers are using digital capabilities to evaluate and select supplier quotes in near real-time without sacrificing accuracy. (Learn how Alstom is saving 40% on parts in this video.)
Companies are preparing for the future of work and will continue to invest in machine learning (ML), artificial intelligence (AI), and other technologies to help offset skilled labor shortages.
4. Accelerate Time to Market and Revenues
DT represents more than just new technology, but the allure of new capabilities can overshadow employees’ critical role in driving organizations forward. Programs that look good on paper often fail because they are based on how employees should work, not how teams actually use the tools at hand or address why some teams bypass official processes.
Seemingly small cracks in the product development process may initially only have a minimal impact. But added pressure to work faster, along with multi-team collaboration earlier in the development process, can forge deep fissures that create costly mistakes that will need to be fixed later in development.
To reduce development cycles and increase profit margins, companies are involving sourcing earlier in the design process. Consulting firm Kearney estimates this sourcing strategy contributes to a financial gain of 2X-5X.
But realizing these gains requires employees to work in new ways using new technologies. This includes refining roles and responsibilities to guide added collaboration among teams earlier in the innovation process. Because early product feasibility and concept design phases are more dynamic than later stages, teams need up-to-date product and manufacturing information to work cohesively and reduce risk (e.g., digital twin files, cost benchmarks, manufacturing capacity, etc.).
Companies can realize significant gains when they apply analysis and intelligence to their manufacturing data. In this case, businesses can improve planning accuracy by simulating production based on detailed product specifications, sourcing information, and manufacturing parameters. Using a “digital factory” to simulate the manufacturing process, product development teams can identify the best path to market with confidence.
Navigating the Road Ahead
Manufacturers face unfamiliar terrain as they navigate the headwinds through 2022 and beyond. And as sustainability initiatives including investment in environmental, social, and corporate governance (ESG) emerge as a top priority, digital transformation becomes more critical. The good news is that it will provide you with the guidance to innovate and capture growth for your business.
The manufacturing industry organizations that can adapt quickly and build/expand their digital capabilities with smart factory initiatives will be well-positioned for a competitive advantage this year and beyond.
Learn More
Learn more about the 2023 top manufacturing challenges and how aPriori can help you address them.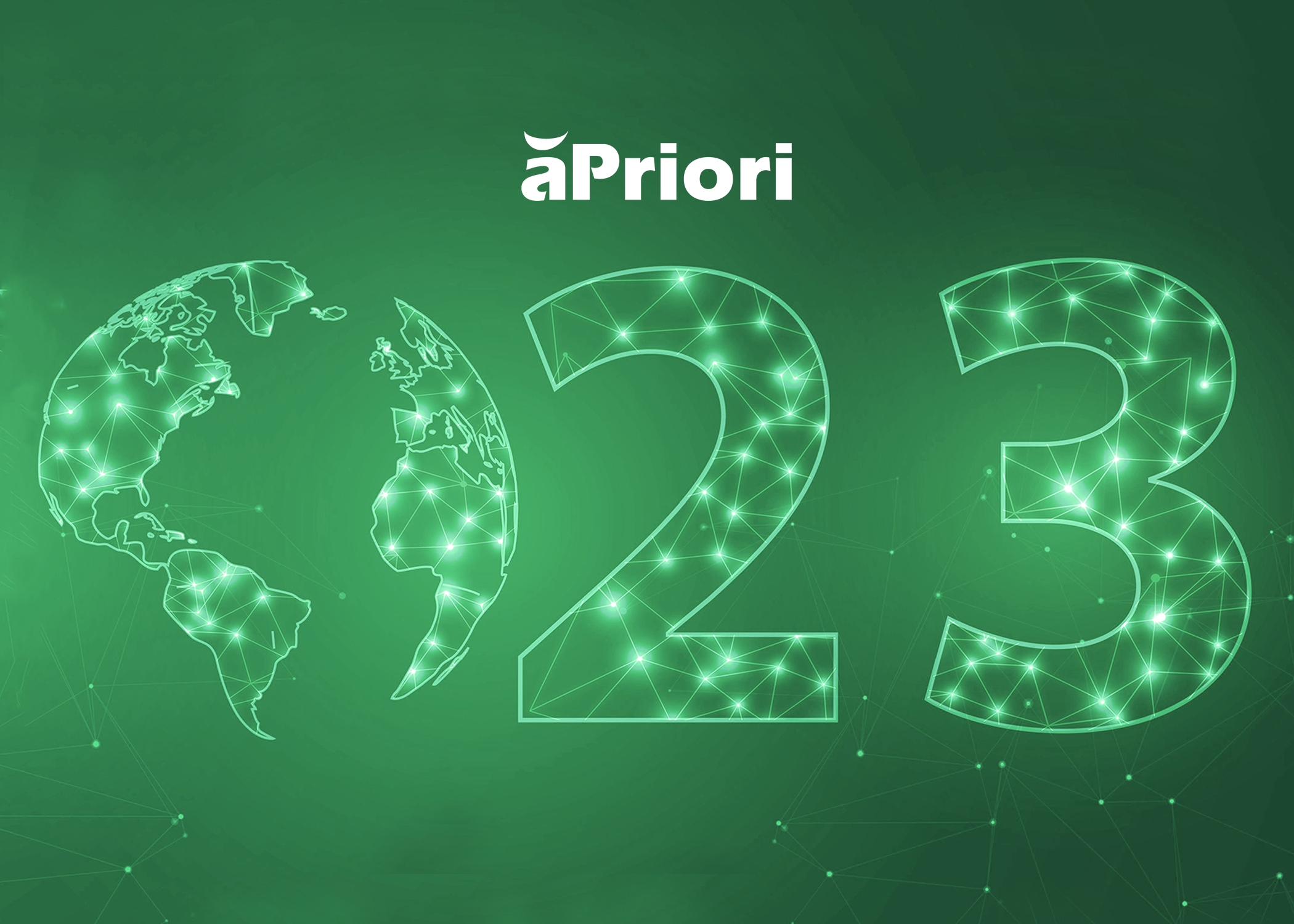