Your Should Cost Estimate Is NOT 100% Accurate, But That’s Okay
Key Takeaways:
- Should cost and cleansheet models provide real value as a point of comparison across product lifecycle development
- Cost assumptions determine the disparity between should cost and quoted prices, providing opportunities to close that gap with a redesign or process change, different materials, or during supplier negotiations
The Full Article:
A product’s underlying key cost drivers can be complex, especially when relying on out-of-date cost information or factoring in outside influences such as inflation or supply chain disruptions. These changes can influence everything from material and manufacturing costs to labor wages near and far from a manufacturer’s operations. Moreover, supplier quotes can vary drastically, and many suppliers are reticent about revealing how they arrived at their prices.
The Question of Accuracy
The accuracy of a should cost estimate often comes into question when implementing such a process. If you should cost a given casting part at $100, its actual cost could be $71 or $132, a variance of nearly 30%. However, does that mean the should cost estimate is worthless due to its perceived inaccuracy? To answer this question, let’s have a look at the components of a part cost.
Material cost, including utilization, process and handling cost, indirect overhead, and the supplier’s target margin, all determine the part’s market price. Often, a part’s cost contains a lot of noise related to market conditions and whether or not the supplier wants the business. If the same part is sent to three different suppliers, an inherent variance in each supplier’s quote can be +/-40% or more.
The goal of the should cost estimate is not to get the most accurate cost but to serve as a valuable point of comparison between the assumed and actual prices.
What is a Should Cost Estimate?
A should cost estimate or should cost analysis calculates the ideal cost of a product, component, or assembly. The bottoms-up approach is based on the estimated cost for materials, labor, overhead, and manufacturing processes while ensuring a profit margin. This estimate provides a theoretical benchmark for what a product “should cost” based on best-practice conditions.
Moreover, it is a benchmarking foundation for more effective supplier negotiations, internal reviews, cost comparisons, and determining what a specific part should cost. It should factor in current market costs (which can fluctuate due to global inflation of material costs, regional labor rates, volumes, manufacturing processes, machine types, and more).
Cost may change significantly over the product’s development timeline. Those cost variances could be related to raw materials inflation, processes, machines and cycle times, or the supplier’s quoted price during negotiations. This quoted cost is then compared with the should cost estimate.
Cost assumptions actually supplant the final price because they determine the gap between the expected cost and quoted prices. The assumptions provide opportunities to close this gap during product development and supplier negotiations.
What is Cleansheet Costing?
Cleansheet costing is a specific approach within should-cost modeling. It aims to determine the true cost of a product or component by analyzing all cost elements in detail. However, rather than relying on traditional cost methods that get numbers from suppliers and others to create the cost sheet, the cleansheet method starts from scratch, breaking down costs into raw materials, manufacturing processes, labor, and other factors. It results in a more accurate picture of costs based on best practices, enabling organizations to identify areas of improvement.
Where should cost estimates provide high-level cost metrics, cleansheet costing gets more granular with those costs, substantiating the accuracy of should-cost estimates by ensuring that all relevant cost components are considered.
Moreover, it provides design and manufacturing optimization opportunities. Knowing where and how to identify critical missing data (and then making educated guesses for the gaps) is key to creating and utilizing the cleansheet approach.
As a result, organizations can more effectively negotiate with suppliers, make more impactful cost reductions, and optimize design, production, and other operational aspects. Ultimately, it helps close the gap between ideal cost assumptions (which can be modified if necessary to consider various production volumes, scenarios, materials, etc.) and what is actually paid. Here are four steps to developing a robust cleansheet cost estimate:
- Outline how the manufacturing process will flow. Digital factories are an optimal solution for this process since they can virtually replicate a manufacturer’s physical facilities. If products are to be made elsewhere, a digital factory can also be reproduced for that facility. What-if scenarios can be run for products that have not yet been developed.
- Add as much detail as possible to the cleansheet. Data should include required raw materials from the product’s bill of materials (BOM), equipment, tools, labor used, cycle times, each manufacturing process, etc. Again, digital factories can aid in this process. The more data input – whether it’s based on previous production or just estimations based on supplier feedback – the more accurate your cleansheet costing.
- Use up-to-date material, equipment, and labor costs. Ensure that you have access to cost updates to calculate and compare total manufacturing costs by region for greater accuracy.
- Include direct and indirect overhead. Consider the appropriate profit margin if production will be outsourced to a supplier. Use a bottom-up approach to factor in indirect costs such as facility operational expenses, equipment usage (including rentals, R&D one-off investment amortization), and taxes.
Leveraging aPriori to Create a Should Cost Estimate
A should cost estimate helps get closer to the total cost of a product, part, or assembly. It also can be optimized throughout product development:
- Cost reduction and improved profitability: A should cost estimate leveraging digital manufacturing insights can identify cost outliers throughout product development, particularly opportunities early in the design stage. For instance, those insights might reveal that a machining process is cost-prohibitive. A solution like aPriori can offer alternative, less expensive processes or materials. Such data can substantiate new product creation with management, and serve as a springboard for supplier negotiations that can lead to significant cost savings.
- Design acceleration: A solution like aPriori provides direct 3D CAD file analysis. It ensures design engineers can iterate design alternatives early and quickly, lowering costs and ensuring timeliness when going to market. Manufacturers should also look for a digital manufacturing solution that can be fully customizable to their production facilities and/or supplier specifications and simulate many manufacturing processes. aPriori offers 440+ models. Both facilitate more accurate should cost estimates for components rather than waiting on suppliers to quote prices weeks later.
- More informed sourcing and supplier negotiations: Understanding what a product or component actually costs to make can pave the way for faster decision-making. Knowledge is power, especially when it comes to negotiations. Procurement teams going into supplier negotiations with precise product or component cost data stand a better chance of reducing their overall costs. Typically, the true cost of a product or component isn’t so clear-cut. Adding to the mystery, suppliers are rarely forthcoming about their quoting process and what is included in each (processes used, age and capacity of machines, etc.). Armed with the facts, quotes from suppliers can be challenged and openly questioned if big deviations occur from the cost estimate, including reasonable assumptions on the margin compared to the quote.
- Faster, more strategic decision-making: You want to get the most accurate should cost possible for better, faster, and more strategic decision-making. One way to do so is through the cleansheet approach. It calculates the should cost at each product development stage and starts with a cleansheet. It is populated with a fully optimized manufacturing scenario, not just the reverse-engineered cost structure of an existing manufacturing process.
A High-Fidelity Method to Calculate the True Economic Cost
The ability to automatically simulate the entire production process with a digital twin CAD model can get manufacturers closer to the true economic cost of a product. aPriori’s Manufacturing Insights Platform can support this effort. Cost reductions are about relative, not absolute, changes. A high-fidelity method more precisely calculates the true economic cost of a product, component, or assembly. Knowing the necessary production resources is essential. aPriori facilitates this process, identifying the issues that can influence the true cost and profit margins including supplier relationships.
More importantly, product development teams can get a should cost big picture AND ensure that they maximize their design, manufacturing, cost, and sourcing opportunities.
Your Ability To Cost Is Only As Good As Your Solution
Learn how aPriori can help you calculate more accurate cost targets for purchased products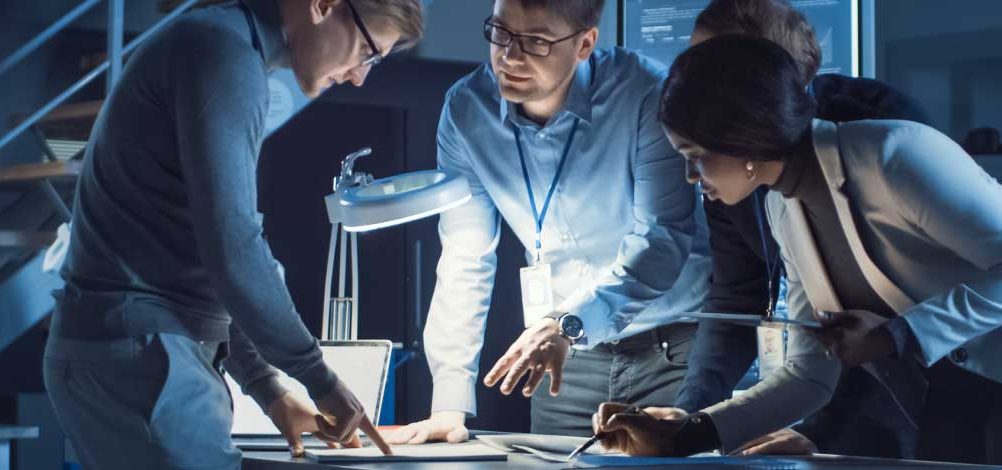