Video
How to Measure Cost Avoidance
In this presentation, Emily Matsco and Abe Chaves from aPriori discuss strategies for measuring and implementing cost avoidance in product design. Emily outlines how aPriori’s tools can be used to identify and quantify cost avoidance throughout the design process, particularly focusing on the design use case. She explains the basic and automated cost avoidance reports available in aPriori, which compare different design iterations to measure cost differences and adjustments. Abe then demonstrates how to track the progress of cost and weight over time using aP Analytics, highlighting the ability to analyze individual parts or assemblies at various stages of the design process and also how to track manufacturability issues.
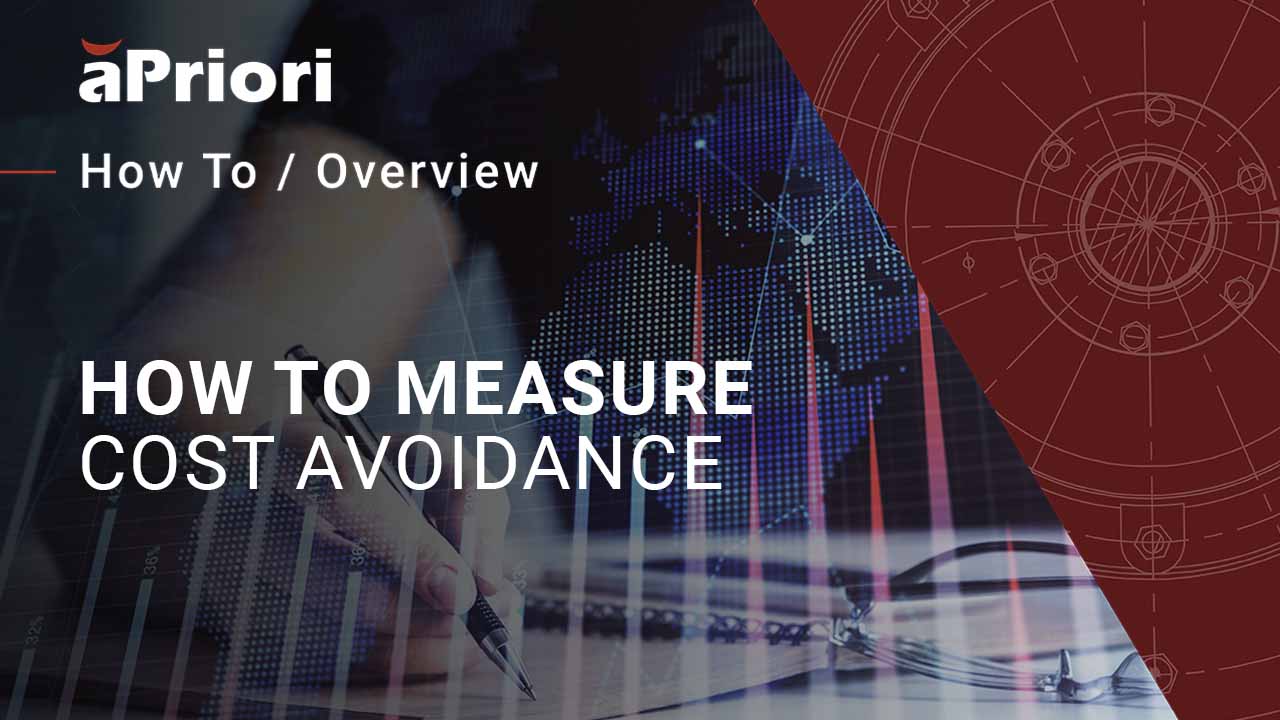
Transcript
Emily Matsco: Hi everyone. Today we’re gonna be talking about how to measure cost avoidance using aPriori and some of its available resources like our tool, aP Analytics. My name is Emily Matsco. I’m a senior expert services consultant at aPriori, and I’ve been in this role for almost three years now. Working with a variety of customers to address different use cases, including the cost avoidance and design use case. And then later on in the presentation, you’ll also hear from my colleague Abe Chaves, who is a principal consultant here at aPriori. And he’ll talk a little bit more about some of the the custom reporting options we have available for cost avoidance measures.
EM: So getting right into it. To introduce this topic, we’re going to start with an introduction to cost avoidance. What is cost avoidance and how we’re going to be defining that today as we, we talk through some of the tools available and also the use case where cost avoidance is going to be applicable. Then we’ll move right into aPriori’s out of the box reporting solutions that are available to assist in measuring cost avoidance. And we’ll wrap up with some custom reporting options, that have been used by customers in the past to measure cost avoidance as well as DFM risk.
How to Use aPriori for Cost Avoidance Strategies
EM: So starting off, what is cost avoidance? And really cost avoidance is going to apply to kind of one of our major use cases here. So as we know, aPriori has a few different applications and use cases, two of which being sourcing and quoting where sourcing is, where aPriori is used to identify cost outliers and really guide negotiations. And really how we’re measuring success with insourcing is going to be realized savings with quoting, we’re using aPriori to derive product quotes, and our success measurement is going to be increased revenue or decreased turnaround time for a quote. But really where we’re gonna focus this presentation on and where cost avoidance is going to be, a big component is the design use case. So as design engineers, we can use aPriori to identify DFM risks. So design for manufacturing risks, conducting trade studies and drive design iterations, as well as design out some of the unnecessary costs that we sometimes see. And so, the success measurement for the design use case is actually going to be this cost avoidance that we’re talking about. And really what that is, how much cost we have, or how much have we reduced the cost of the design from the initial,to final design and throughout these iterations.
Cost Saving Measures in the Product Design Stage
Cost avoidance can capture cost reduction from preliminary design to final design, as well as within the design process at different stage gates and, and checkpoints. And when we talk about this design process, I’m going to walk through what that looks like as a full process. And really what we’ll be using today to guide this discussion of cost avoidance analysis is a pretty boiled down version of what we might actually see in the design process. So within these three categories, in real life, we’re going to have different stage gates and design checkpoints and more formal, different categories. But for the case of this presentation, we’re really going to focus on the three main stages being preliminary design, which is where we’re going to see some of our requirements scoping and initial design development. And so as an example, this might be, just a prototype phase. We might not necessarily have CAD files, it’d be like having a paper airplane when you’re tasked with designing an airplane.
EM: Then we’ll kind of get into this iterative process and start conducting our trade studies. Maybe we actually have a CAD model at this point, and as we know, as design engineers, we can all maybe be a little bit overzealous. So when we’re starting out this process and add every bell and whistle under the sun, and really what aPriori can help do and what this cost avoidance measurement can help do is, is drive some of the decisions to design out cost increases that a lot of those nice to have features but maybe aren’t required kind of add to a design. So, during these iterations, aPriori can measure the delta between different trade studies, help drive some design to decrease DFM risk cycle time and so on and so forth. And, as an example, it’s like going from our paper airplane that we started with to now our rocket ship. And so what we want to use aPriori for is to get from that rocket ship to our final design, which would be, somewhere in the middle, kind of a standard airplane maybe using aPriori feedback we can get to this point. And then between our rocket ship and our airplane, we can measure some of that cost avoidance that we were able to successfully design out, using aP and then also kind of attributing our success, or quantifying our success with that cost avoidance value.
Benchmarking Your Project’s Cost Over Time
EM: So tracking your cost project’s cost avoidance over time. So shortly, I’m going to actually jump into our aPriori Analytics tool to walk through how to actually measure cost avoidance using our out of the box reports. But before I do that, I just want to introduce the two scenarios where we’re going to run these reports. So aPriori does have two out of the box reports available for cost avoidance. The first one is really going to address what is the difference in cost between the initial and the final scenario. And so it’s going to compare two design versions after making design changes and conduct straight studies. So that’s in using airplane example, that would be like saying, okay, we started with a rocketshi and now we have our final design, so bottom line, initial to final, exactly what is the cost difference there over the entire course of our design, design phase and iteration phase.
EM: And so really that’s just going to compare A to B, and that’s going to be that first report that we walk through. The second report is going to be a slightly more automated, cost avoidance measurement tool. And so that’s going to be similar to looking at, okay, we have one, scenario, one situation. We have our first design, we have now made changes to it, let’s run this report, right? And then we make changes to it again. Okay, let’s see how much additional cost avoidance, what is the delta between our third iteration and the original design we had? And you can run it constantly on at these different stage gates throughout the process. So again, using our airplane example, say you have your initial rocket ship, you make a couple material changes. So then you run this report and it will give you just a cost delta between the most recently costed scenario of this part to the highest cost scenario of this part.
And then we will actually be implementing some design changes from there. Change the CAD model a little bit, maybe remove some of the extra, those bells and whistles we were talking about. And then we can run this report again. And now we’re going to be comparing that let’s say third or redesigned part to this, to the highest cost version of whatever that was. And so I’ll walk through exactly how to run these reports and what they look like, but those are the situations. So, the first report we’ll talk about, like I said, we’ll really just be comparing, design one to design final, and then the second one we’ll talk about, we’ll be really comparing kind of, or give you the ability to compare, or measure cost avoidance intermittently throughout your iteration process. And so just as an introduction, this is what the report’s going to look like. Again, I’ll jump into our aP Analytics in just a second here. But really kind of what this all boils down to is based on cost differences between scenarios in aPriori. Both the basic cost avoidance and the automated cost avoidance reports will calculate total and annualized cost avoidance across components.
Examples of Cost Avoidance
EM: So with that, I am going to move over into our, reporting tool. So you guys should be familiar with our aP Analytics platform. And so these reports, as I mentioned, are going to be in our out of the box reporting folder. So if we open that up and then if we just search for avoidance here, we’ll see two options. And so these are the two options I was just talking about are just introducing. So we’ll start with our basic cost avoidance report. And the basic cost avoidance report is going to display cost avoidance across all components in the reporting database that meet the prerequisites. So whereas some out of the box reports we’ll see, you’ll run on a very specific rollup or a specific export set. The basic cost avoidance based on the parameters given will take any and all scenarios from the reporting database that match the prerequisites.
And those true prerequisites are a consistent part number, and scenario types. So you can’t compare a part to an assembly say. And then the second one is that the part has to have an initial scenario and a final scenario. And so the scenario name has to very strictly be initial and final to compare across. So aPriori will go into the reporting database, say, okay, I found this part number. It has an initial scenario. If it also has a final scenario, it will output the results of the cost delta between those two scenarios. And so when you’re setting up this report, you do have a few options here with your input. So you can change the earliest cost date of that final scenario and the latest cost date. The latest cost date will always default to today or today’s date and time, but you can always change the earliest cost date.
So maybe you only want to evaluate parts that you’ve costed over the last week or month or three months. Either way you have, you can change that to limit the amount of data being pulled in. And then the cost metric, of course, you can compare piece part costs, fully burdened costs or our total variable cost within aPriori across these scenarios. And then, you can, currency code sort order, all of those kind of standard options there. But setup is awfully easy. You can just hit okay here and aPriori is going to come up with this list, which shows you the parts that had that initial and final scenario available, and we’ll sort them based on annualized cost avoidance. So this top row is gonna be our, highest cost avoidance for the year at a hard savings of $1.5 million. And this little asterisk to the left shows us that they have different costing inputs.
So maybe this cost avoidance is just driven by a change in, annual volume or a change in material type. And so all of the inputs that you see here in this chart, digital factory, process group, material composition and annual volume, that is all, coming from the final scenario. So the scenario, the part with scenario named final, well, I’ll put the cost inputs here, and so you can see kind of where you landed on the final design. And then you’ll also notice, down at the bottom we even have a part that maybe went up in price and maybe that was driven by a material choice or some tolerance requirement that we didn’t have in our initial design. But overall we’re kind of net positive here with our cost avoidance between our initial and final scenarios of these parts.
So again, this is really just comparing, okay, we have one part number with its scenario name initial. So that’s that, that rocket ship, that first part, or first CAD file that you have going through the design process. And then comparing it to the final design, which is our airplane. We finished this, we’re going to customer design review, we’re ready to go to production, what have we improved on? And that’s where you’ll see the annualized cost avoidance. All right, and then going back, so our second scenario that I touched on was this, is going to leverage the automated cost avoidance report. So where I was talking about, the first one we went through is going to compare part or scenario A to scenario B and just give you a delta. The automated cost avoidance report can be used a little bit more easily when you’re trying to do pretty rapid iterations on a scenario and a part.
And so, with the automated cost avoidance report does is it also displays cost avoidance across all qualifying components. And the prerequisites for this, report are a little bit different. It has to be the same part number and scenario type again. So you can’t compare parts to assemblies. You also have to have consistent scenario names across the same part number. So whereas in the last report, the scenario names had to be something very specific. This you can name whatever scenario name you want, it just has to stay the same. And what aPriori is going to do is from the cost exports that it has, it’s gonna surge all parts in the database based on the parameters and the constraints we give it. And then say this is the latest cost scenario, just the most recent cost data compared to the highest cost scenario.
So the scenario, that aPriori says, okay, this is the highest cost in our reporting database that we found for the same part number and same scenario. And so this does have a few more setup options with the report because we can set a few more parameters here, and because we’re not specifically looking for those very specific scenario names, we’re looking for any scenario name. This kind of limits what gets read into this report. So, as an example, you can sort based on component type; we’re just gonna do parts today as an example. And then you can also filter based on if the costing inputs match. So, if you only want to compare parts that are in the same process group from the reporting database, you can select that. You could also select based on, material composition.
So say you don’t want to compare parts where material inputs are really driving some of that cost avoidance. You really just wanna get some cost avoidance data for the design itself. You could select okay, every component must have the same material composition. Today we’re just gonna go through process group and then excluding cost failures, that just cleans up the data a little bit and then costed by full name. And so this feature I do really like the costed by full name because you can filter based on who is actually analyzing these in aPriori. So as an example, if you’re a project manager for a design team and you have, let’s say four people on your team all kind of responsible for sub-assemblies within a larger program, you can filter on either each of them individually to look at the parts that you know is just part of one sub-component.
You can also look at the parts that are, costed by all four of those individuals or say you just wanna see everything that’s been costed in that environment. You can also kind of not filter on this. For the case of this example, I am gonna filter on just parts I have costed instead of the, entire, aPriori organization. And then, again, I am going to filter based on process groups. So I only wanna look at sheet metal parts here. And then you can also filter on the digital factory. I’m not going to today, but we do have all of those available. And of course, if you have custom digital factories for your organization, those will show up here as well. And then we’re just gonna click okay.
And so you’ll notice, again, sorted by annualized cost avoidance. And we have one really good example of, this component is showing a $1000 in cost avoidance, potentially driven by cost inputs. But what that’s saying is, okay, we have this component name and we had a scenario and that initial scenario was, or whatever the name of that scenario was. In this case, I know it is initial, the highest cost that we saw in the reporting base was this 17 cents, but then the last cost we did on this part was actually only 11 cents. So that’s where that cost avoidance comes in. And again, this is because you don’t have to have a really strict scenario naming convention and can name it whatever you want. This makes running this report as you make kind of more nuanced or, smaller changes to a part throughout iterations makes it really easy to run, pretty frequently. So you can kind of get a checkpoint or just kind of a gut check on where you are with your design at different, points throughout the process. And next, I am going to hand this over to Abe, to talk about some of our custom reporting options that we have using the AP analytics tool to measure cost avoidance.
Examples of Cost Savings Strategies Using Automation
Abe Chaves: Thank you, Emily. For you guys that are design engineers in the audience, would you like to see how your design is progressing in terms of cost and weight throughout the design process? I will show you how to track the progress of your aPriori project throughout all those iterations that Emily was talking about, right? And I’ll show you how to do it automatically and how you can call the scenarios anything you want. You don’t have to call it initial and final, and you can actually name the component that you are designing and that you are going to track anything that makes sense to you and your management, right? So if you are responsible for designing an assembly and the name of the assembly, obviously you have a CAD number for it. And it is just some, 8508001 for example here. You can just call it luxury car seat or that may be F-150, front bumper assembly, whatever. It makes sense so that people know what is it that they’re looking at. And then you’re gonna be able to drill down into the parts of that assembly so that which ones are the biggest contributors to either weight or cost, right? And what to attack. Okay? So let me show you how that’s gonna work in the product so you can get to a tangible financial benefit for your company.
So again, we’re taking you here to the aPriori Analytics product. You are going to go into the ad hoc views because this report doesn’t come out of the box, but we can create it for you easily enough. And if you have Expert Services, that should be a fairly short task. We have called this report “custom weight tracking over time.” And so the report will show you the cost and the weight of an assembly as it moves through different time periods. Here on the black bars. Here are your future cost and those, the scale for that is over here on the left. And the red bars are the weight and the scale is over here on the left. And you can look at each one of these independently. So I can turn off weight and look at just cost and see how cost is moving over time, or I can turn off the cost and see the weight and see how the weight actually increased in the beginning and then we figured out how to get it back down again, right?
You can see that my time periods are here are daily, and that’s just because I have to create a set of data and then make changes quickly. But you can actually make this grouping you can make it daily, you can make it yearly, quarterly, monthly. You can go all the way down to hourly or by the minute, which obviously you don’t want to do. But what the system wants to know is, what do you want me to plot? So, if you are plotting this monthly, do you want me to plot the maximum cost over that month, the minimum cost over that month, the average, or the maximum weight? The minimum weight. And so you simply would right-click, and then you could change what it is that you want the system to plot. Over here you can also see here that I have selected a time period. So you can say over the last six months or next year, I want to see how my component has been tracking over the last six months, monthly, basically, or over the last year quarterly. And then, as promised, you can look at the assembly, or you can look at the parts inside the assembly. So I can select the part, and I can select apply.
And now what I’m looking at is exactly the same example except that I’m looking at the parts inside of it. So you see more, more data points within the same time periods over here at the bottom. And now, right now it becomes more useful to actually turn some of this off so that it makes it more clear ’cause it’s a little confusing when you have more data. So now I can, I can turn the weight off and see how the weight, how the cost progress, and I can see that obviously in the beginning this were my two most, my two highest contributors to cost. And if I’m an engineer and I’m trying to cost reduce this component, this is very useful information ’cause now I know if I really wanna make an impact, I don’t go after this components over here that’s not gonna do digitally, right?
AC: I want to go after the ones that cost the most and that’s what happened, right? So I went after those, then I went after some of the little ones, and then I went, after this big one over here, right? And you can see how the weight, progressed. I did reduce the cost, but I increased the weight in doing that. And so I had to somehow figure out how to reduce the weight at the end. And so you can see both how your cost on your weight is progressing through time.
AC: So this is for an assembly. I can also look at a collection of parts because sometimes you’re responsible for single parts, right? And you’re responsible for a collection of single parts. So you might, for example, be the engineer that’s responsible for all the castings inside a product, or all the machine parts inside a product instead of a sub-component or a sub-assembly. And so what you can do is, this is just a collection of machine parts basically. And I can look at them at outside the part level, at the whole rollup level. So if these are all the machine parts in a particular product that I’m responsible for, I can see how my collection of parts is tracking, and then I can look at, again, I can look at the part level and see how they’re tracking individually, right? Both in weight and, in cost and weight to lower costs.
AC: Alright, let’s move on. That’s tracking the cost and the weight of a component in time. What about tracking it as it progresses at discrete points in time following your design process, following your design stage gate system, basically. But we can also do that, right? So we can show you how you can, can easily track the cost and weight of anything that you’re designing, at the different stages of your, of your MPI process. This one is not automatic. The other one, all I have to do is basically create that export for the assembly that I was tracking or the collection of parts that I was tracking, the car seat, for example, export it once and at the time that it’s exported, you tell the system export every week, or every month, right? Or every day. I wanna do it every day, but, and then just run the report whenever you want.
AC: Just give it the date range and it runs automatically. So you actually, in this one, you actually have to save an instance of whatever it is you are designing and then add it to a roll-up every time that you save a new one. So that what you’re really tracking is the component as it moves through the stage cage process because you keep adding that, scenario is what we call the instance a scenario to the rollup. And so let me show you what I mean. So this is really what you’re gonna be looking at. This is what I’m going to be showing you. The hitch is just an assembly basically. And I basically saved a copy of that assembly when I went for my concept review and I called it concept release, right? You can call it concept review. And then when you go for your stage one review, I called it, I saved another copy and I called it a stage 1 and I pulled it inside this rollup, right?
You can call it gate 1; you can call it whatever your process calls those stages. And then the last one I did was this, stage 3 release. It could be release candidate, it could be release candidate 1, release candidate 2, whatever you, whatever makes sense to you. The point is, is that every time that you save a stage or you save this instance, you add it to this rollup, and as this rollup grows, you are going to be tracking the cost as it happened, right? So let me show you what I mean by tracking the cost as it happens.
Tracking Cost Savings in Real Time
AC: We’re gonna go to the same spot ad hoc views, and we’re going to select custom weight tracking at stage gate. And you’re gonna see here is the same data in the same format. And I have this hitch here, and I have, instead of having dates over here, what I have is the different stages because what I’m tracking is that rollup, that container that has the different instances, the different scenarios of that, of that assembly in it. And I, so here you can see that in the very beginning, I just as typically happens, I got my concept design. I haven’t put a lot of the, I haven’t done, full FEA yet, I haven’t, maybe put some of the tighter tolerances in and things like that. And so typically your cost goes up and then you have to figure out how to bring that down, right?
And so this is what happened here. And similarly, as I did before, I can look at this at the part level and this one has got a lot more data, so it might be a little more confusing to see. And then obviously the more parts you have, the more crowded this gets at every one of these, stages. But I can just turn one off and I can see how my cost started out low. And you can see that, you can see that this is the last, the last part of the group and then we start all over again. I can see this part got really expensive, right? And then I managed to bring it down a little, but then, it I did something to another part that went up cost. And so I had to bring that down. But you can track the progress here and see how your design is behaving and progressing along. Same thing for the weight.
And so exactly the same data, except that this time, instead of having dates here, I have the different stages and I have something manual to do. I have to save a copy essentially of my assembly or whatever it is I’m designing, at every stage. And then add it to this rollup. That shouldn’t be a big deal, though, because you have to go to this review, and you have to have something to present at this review. So you’re just saving that at that instance in time. You’re saving whatever it is you’re reviewing. Okay? So I was an engineer for seven or eight years, and I know that the quality of your design, the quality of whatever it is you’re designing, takes precedence over cost. We don’t want this type of stuff to happen, right? And so how would you, like, you like to be able to track your manufacturability and quality risks issues over time as your design is progressing and see if they’re, if the more complex your design gets, the more issues you have and what are those issues and what are you doing to resolve them?
aP Analytics Tracks DFM Issues for Cost Avoidance
And so that’s what this report’s gonna do for you. It’s going to allow you to track the number of DFM issues that are present in your design as it moves to time. It is also automatic. You can use the same export so it, the same export that you used to track cost and weight can be used to track DFM issues. It’s just simply a different report that will be applied to the same data basically. Okay? The only caveat to this reports is that the report looks at a group of parts that is made from the same process. So sheet metal parts, machine parts, plastic parts, all will be looked at differently with a different report. So you’re going to have a machining, DFM issues report, a sheet metal DFM issues report, injection molding, DFM issues report.
And that’s because the manufacturability issues of a plastic part are much different than a sheet metal part. And so that’s why you need to run different reports, but you can have different type of parts in the dataset. So I can have an assembly and I will show you that I can have an assembly that has bottom two parts and sheet metal parts and machine parts and plastic parts. And if you put it through the right report, it’s only gonna show you the sheet metal parts when it’s showing you the DFM issues for sheet metal. It’s only gonna show you the plastic parts when it’s showing you the DFM issues for plastic. So let’s see how that works.
Alright, so what I have here is a very simple roll-up, made up of just two different, sheet metal parts. And what the report is doing is it’s looking at that rollup and it’s looking at it at different points in time. I only exported it three times basically. And I made some design changes as I went along. And you can see here that the two parts that I have in the roll-up is this a 801 and this bracket zero. And when I started day one here, I had four hole issues on this one, and that was it. And this one had a ton of issues, had 51 hole issues, which is, by the way, things like the hole might be too small if the parts made it on a turret, for example, or stamped, maybe their holes are too small and the pins are gonna break, right?
So something like that, it had 42% proximity issues, things like, “hey, there is a hole that is too close to a band,” and so it might deform when you make the band right, that it’s a hole that is too close to an edge and it might not be enough meat and it might crack, right? So these are quality risks and DFM issues and risk management, okay? And so I can see that I did something to my designs and instead of fixing this turret, the turret part actually made it worse. So that’s the feedback I get here. In this part, I actually did pretty well. I brought it down from 51 to 27, and my hole issues and then my proximity issues, I brought them down to 12 from 42, right? So great progress there. So then I did something the third day and I brought this one down to four and decided, “Hey, I’m gonna just keep with my old design that that was good enough.”
And this one, on the third day I couldn’t do much more about this issues, but I traded essentially all my proximity issues for six bend issues, which might be, a bend that might be too tight, right? And you might crack the material if it’s not, if the bend is not aligned properly, aligned properly, for example, the lip on a band might be too short. Things like that. Okay? So yeah, I got rid of, all of this proximity issues, but I create a new ones, right? And so I need to keep on looking at this. The point is, you can have a collection of parts or an assembly. I’m gonna show you that hitch again. So if I run this on the hitch assembly, I can see all the parts on the hitch, right? And I can see the if it’s, the type of sheet metal issues that I have on those sheet metal parts, okay?
Some of these parts are not sheet metal, and so they’re not gonna show sheet metal issues. For example, this shaft is a machine part. There is a plastic part in here somewhere. Things like that, right? And so, what I’m trying to show you is that by doing this this assembly is not all made up of sheet metal parts. You don’t have to worry about that. The report will recognize that some of them are not sheet metal and only report on the sheet metal ones. If there were machine issues on, this shaft here and I ran a machining report, I would get issues on that. Unfortunately, this doesn’t have machining issues. It’s a pretty clean design alright we have come to the end of the presentation.
We have shown you five different ways in which you can look at the cost and the weight of your assemblies, and even a way to track the manufacturability of your assemblies of your parts that you are designing, for different use cases. So we hope that this has been practical and fruitful for you. Thank you very much and have a great day.