Video
How to Calculate and Track ROI With aPriori
Evaluate tangible ROI with aPriori using the basic cost avoidance and spend analysis value-tracking report covered in detail during this presentation.
We’ll share how to:
- Capture the value of your aPriori deployment
- Track value in aPriori today
- Identify targeted areas for improvement
- Plan enhancements for ROI tracking
Learn about current and future aPriori Cost Insight Report offerings for tracking value in sourcing and design engineering use cases.
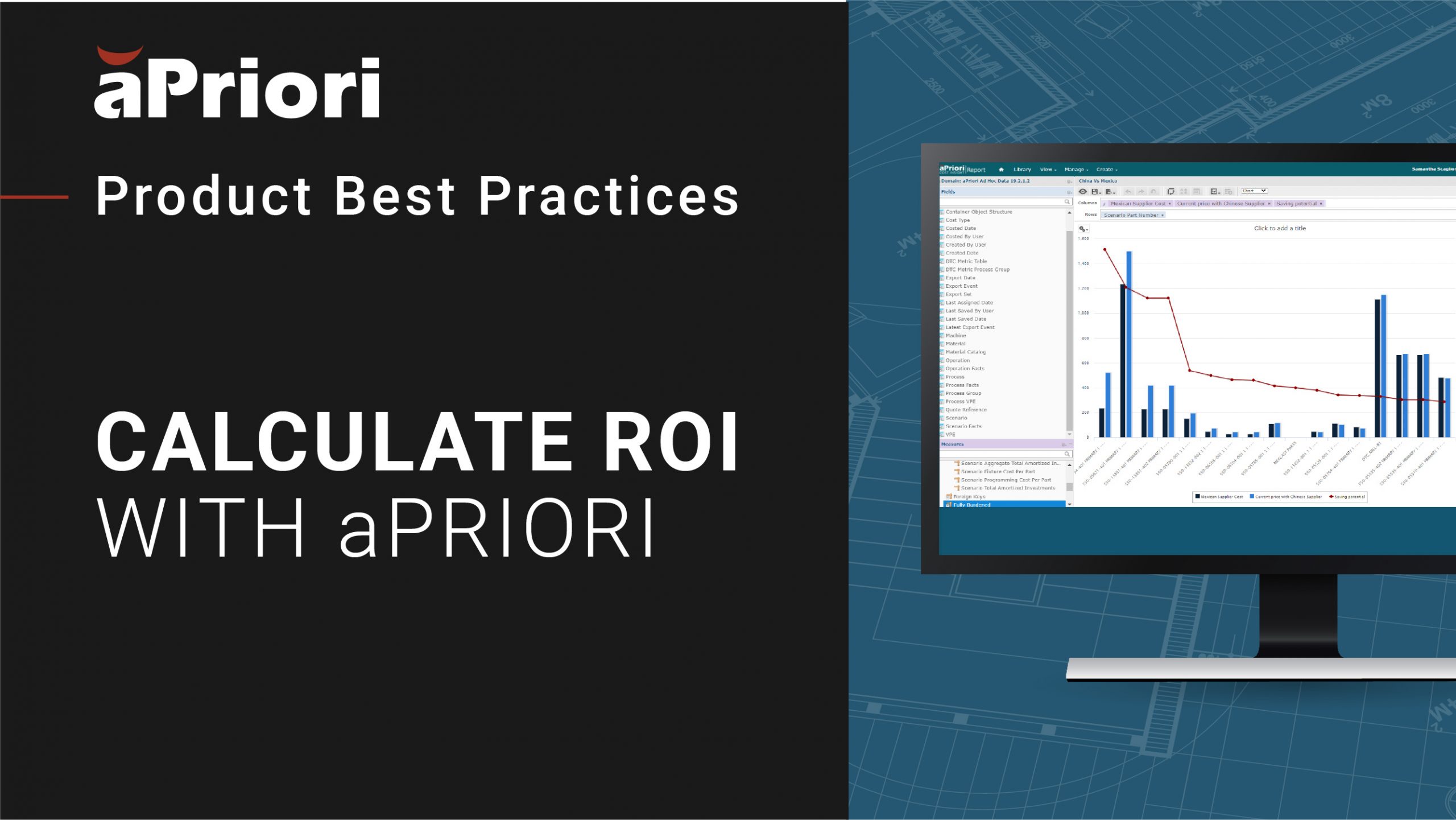
Transcript
David Gay: Hello, everyone, and welcome to the aPriori Value Tracking session. My name is David Gay, and I am a manager here at aPriori. I’m joined by Cecily out of our Product Team, and I’m part of the Customer Success team here at aPriori. Before we begin, a few housekeeping notes, the attendee lines will be muted throughout the session. We will be taking questions throughout the presentation utilizing the chat panel on the event website, not the Zoom chat. Please enter any questions you have in the costinsight.com chat panel. We will answer as many questions at the end of the session as possible; you can also feel free to schedule a meeting with us via the meeting scheduler on the event website. On the event website, near the chat panel, choose “People” and select one of our names to schedule a meeting. Alternatively, you can contact us via email; we will share our email details at the end of this session.
DG: We have uploaded a PDF of today’s presentation, which you can access in the file panel. So, let’s begin. So, the first thing I want to go through is quickly, just the agenda. Today, we’ll be going through how to capture the value of your aPriori deployment in some of the current charts and visualizations we have, understanding how to track value within aPriori today, looking at how we target our improvements for our product to make sure you’re successful as a client. And then lastly, we’ll go through some planned enhancements and then ask for your feedback as we’re working together on this value journey.
DG: Today, each of our clients that are on the cloud have upwards of 500,000 scenarios, and each day they’re creating thousands of new scenarios through Cost Insight, generating some of the automation. The question that a lot of our clients have is, “What next with all this data?”
DG: This data provides immense value for our customers and helps them solve their business problems, but without an automated way to analyze the dataset and metrics, our customers are challenged to quantify the impact that manufacturing simulation has on their product development process. We’ve been working with our customer base in our product development team to understand what value tracking reports we have today and how are we going to enhance those value tracking reports to make them more automated so that you, as a client, can provide better insight on where manufacturing simulation has impacted your business. What I’d like you to do today is to look through everything we’re going through, when it comes to the new enhancements that we’re thinking of, look at what we have today, when it comes to value tracking, both in sourcing and in design, and what we’ll be asking of you is based off of that, we’ll have two different options that we are looking at enhancing in our product, and we’d love to get your feedback. What you’ll notice is, you’ve already, within the session, you’ll already see a poll that I would love you to go through at the end of this presentation so therefore we can understand what is most impactful for you and then how can we improve our software in the future.
DG: So, with that, I’m going to pass it off to Cecily, and then we can go through some of the enhancements we’re working towards, and we’ll work through some of the technical understanding of what we’re doing in value tracking. So, off to you, Cecily.
How the aPriori Algorithm Delivers Value Tracking Reports
Cecily Power: Thank you, David. As he mentioned, I will now cover two key, out-of-the-box value tracking reports that aPriori offers today through Cost Insight Report. So, tracking value in aPriori today, the basic cost avoidance and spend analysis reports are our available value tracking reports. The basic cost avoidance report is built for a design use case, where a design engineer is using aPriori products to reduce cost and improve the manufacturability of a component and would like to capture cost avoidance accrued over the component design process. The spend analysis value tracking report is built for a sourcing use case, where a sourcing team is negotiating cost reduction of the components’ quoted cost and would like to capture the aPriori-driven cost savings realized during the negotiation process.
CP: There is certainly potential for improving aPriori’s existing value tracking reports. An area we have targeted for improvement is the complex user workflow that requires scenario renaming. For both the spend analysis value tracking and basic cost avoidance reports, the user must use specific scenario names in order for the component to be included in the reports. This scenario renaming process is time-consuming, and we value the design engineer’s time and would not want a scenario rename process to be a barrier to report usage. It’s a manual task; manual tasks leave room for error. For example, if a scenario is not renamed correctly, or it was forgotten to be renamed, that component could be missed or not included in the report. And finally, the concept of scenario renaming prevents design engineers from using scenario names for their own purposes, such as, for variations of the same part with different annual volumes.
CP: Now, I’m going to walk you through our currently available spend analysis report; I will point out how the user workflow requires scenario renaming, which is an area for improvement. I’ll then, on the next slide, show how aPriori has enhanced spend analysis in a second iteration of this report, available later this year.
Capture Cost Savings With aPriori’s Spend Analysis Reports for Sourcing
CP: Spend analysis is an out-of-the-box report that tracks cost savings in a sourcing use case. This report allows a sourcing team to track true aPriori-driven savings realized through the component cost negotiation process. We define cost savings as the difference between a base and final quoted cost for each component in a sourcing project. The expectation is that the user engages with the aPriori products between the base and final quoted costs to understand and use component should cost to negotiate a final cost that is reduced.
CP: So, how does the spend analysis report work? For each component the user wants to include in the spend analysis report, they must name one scenario “base,” meaning it contains a field with the base quoted cost, and name another scenario “final,” meaning it contains a field with the final quoted cost. The user then creates a project representing a grouping of components to be sourced. That project contains two roll-ups, one of the base scenarios and another of each component’s corresponding final scenario. The user then continues to create other projects structured the same way. And then, each of these sub-projects is rolled up into an overall sourcing project. The difference is calculated between the base quoted cost and the final quoted cost for each subset, and it is aggregated across the entire sourcing project. So, in summary, the first iteration of this spend analysis report calculates total aPriori cost savings across a sourcing project, but it requires specific scenario names. The user must rename two scenarios per component to base and final.
CP: So, in response, we have improved the spend analysis report by allowing a single-component scenario to store both base and final quoted costs. We did this by adding a user-defined attribute field to each scenario so that the final quoted cost could be stored in the same scenario as the base quoted cost. With only one scenario required per component, there is no longer a need to give scenario-specific names, and this has the added benefit of freeing up the scenario name to be used by the design engineer for their own purpose.
CP: Similar to the old version of the spend analysis report, the basic cost avoidance report is effective at value tracking, but it does require specific scenario names. So first, I will talk through how the existing basic cost avoidance report works, then I will provide a preview of two ways in which we plan to enhance the cost avoidance report like we’ve done with the spend analysis report.
CP: The basic cost avoidance report tracks cost avoidance in a design use case that allows for both the design engineer and manager to track cost avoidance accrued over the component design process, both on a component level and aggregated. We define cost avoidance as the difference between a user-defined initial and final scenario for each component. So, how does the basic cost avoidance report work? Design engineers must name an initial and final scenario for each component they’d like to include in the report.
CP: Cost Insight Report surveys all the costed components; it looks for an initial and final scenario for each component, calculates cost avoidance on the component level, and then aggregates cost avoidance across all costed components. So, at a high level, the workflow would look like this: a design engineer uploads a fully featured component to an aPriori product, let’s say, in this example, Cost Insight Design, titles the scenario “initial” and then costs the component. The design engineer then saves the same component under a new scenario name called “final” and proceeds with applying cost-reduction and manufacturability feedback to the component. Then a customer’s regular export schedule will move these tagged scenarios to the reporting database, where the basic cost avoidance report will pick them up to calculate cost avoidance.
CP: So, in summary, the basic cost avoidance report calculates total aPriori-driven cost avoidance but requires specific scenario names. The user must rename two scenarios per component to “initial” and “final.” The Cost Insight Report product team is already exploring enhancements to the basic cost avoidance report, so next, I will provide a preview into what the product team has in store for the next iteration of cost avoidance reports.
CP: The next-in-line report is an automated version of the cost avoidance report. One where there’s no prep work required from the design engineers, meaning no tagging of scenarios or naming of scenarios as “initial” and “final.” So, this report directly addresses the concern with scenario renaming. In the automated cost avoidance report, cost avoidance is calculated as the difference between the highest cost and the latest costed scenario for each component. Cost Insight Report would be able to select the highest cost and latest costed scenarios automatically from the reporting database so that the design engineer never has to indicate which scenarios to choose for the cost avoidance calculation. We use the highest as the starting point because it likely represents when the component is first fully featured.
CP: With automatic scenario selection, we eliminate the need for scenario renaming and allow the scenario name to be available for other purposes. And again, no prep work is required from the design engineer. The workflow for this report would be minimal, so it would start with the user uploading a component to an aPriori product, let’s say, Cost Insight Design, using any scenario name. The user would then iterate on the component design using a consistent scenario name and applying cost and manufacturability feedback. When the automated cost avoidance report is run, the report and aPriori algorithm calculate cost avoidance as highest minus the latest exported scenario cost for each component. It will then aggregate cost avoidance across all costed components as well as annually.
Utilize aPriori Cost Avoidance Reports for Initial and Final Component Designs
CP: Another report concept is a version of the basic cost avoidance report with the more advanced ability to calculate cost avoidance throughout the component design process. So, this report addresses both the concern with scenario renaming and another concern with cost avoidance not being calculated at a time and aligns with the component design process. And a note here, any bullet that is grayed out is a feature this report has in common with the automated cost avoidance report. So, focusing on the second bullet here, cost and manufacturability feedback is intended to be incorporated throughout the component design process, resulting in many instances of cost avoidance between a component’s initial and final design.
CP: Our basic cost avoidance report calculates cost avoidance once per component at the end of the design process. We have received feedback that design engineers and managers would benefit from tracking cost avoidance earlier and throughout the design process. So, in the advanced cost avoidance report, the cost avoidance is calculated as the sum of a component’s cost avoidance instances. The workflow for this report does require the design engineer to capture multiple instances of cost avoidance during the component design process. So, to make cost avoidance capturing as easy as possible, we would implement buttons in the aPriori application user interface, so Cost Insight Design, aPriori Cost Insight Source, to allow for the capturing of cost avoidance within a couple of mouse clicks. No scenario selection is required.
CP: So, an example workflow would look like this, a user uploads a component to an aPriori application, let’s say Cost Insight Design, using any scenario name. When they’d like to start capturing cost avoidance, they’d click a start button and then iterate on the component design, applying cost and manufacturability feedback. When they’d like to finish capturing the cost avoidance, they’d click the finish button, and cost avoidance would be captured between start and finish. And Cost Insight Design would add this value to a total for that component so that when the advanced cost avoidance report is run, it calculates the total number of cost avoidance as a sum of all the component’s cost avoidance instances throughout the design process.
CP: Because scenario selection here is done through UI buttons, we eliminate the need for scenario renaming and allow scenario names to be used for other purposes. Also, we enable cost avoidance to be captured throughout the design process, providing earlier insight into savings. And lastly, we minimize the user workflow by creating a two-click cost avoidance capture in the aPriori application user interface. So, that completes my overview and tutorial of how the aPriori algorithm tracks value today and what we have planned in the near future.
CP: We are very excited and motivated to enhance the user experience of our value tracking reports, and we look forward to hearing feedback from you. So, with that, I’ll pass it back over to David to wrap up and then move into a Q and A session. Thank you.
DG: Thanks, Cecily, I appreciate it. So, as stated earlier, we have a poll within the session; you should be able to see the two options that Cecily has just provided. And in the poll, we’d like you to tell us what is most meaningful to you as a client. If you’re unable to do the poll in this session, we would love it if you could just email either of us what your best option looks like for you as a client. Also, thank you for attending this session, don’t forget if you’re a customer of aPriori to write a review of aPriori on any of the leading software review sites, including G2, Capterra and, or TrustRadius, to be entered into a contest to win some great prizes. Thank you, and have a great day.