Video
How GE Appliances Uses aPriori for Should Cost Modeling
Delve into the insightful video presentation as Jill Snyder, Cost Engineering Director at GE Appliances, shares the transformative journey of implementing aPriori and Should Cost Modeling.
Uncover the challenges faced and strategic steps taken to embed these practices into the organization, enhancing cost management and supplier relationships. Gain valuable insights into the role of Should Cost in driving sustainable profit margins and optimizing material costs.
This video offers a comprehensive case study, revealing key lessons and best practices for effective cost engineering.
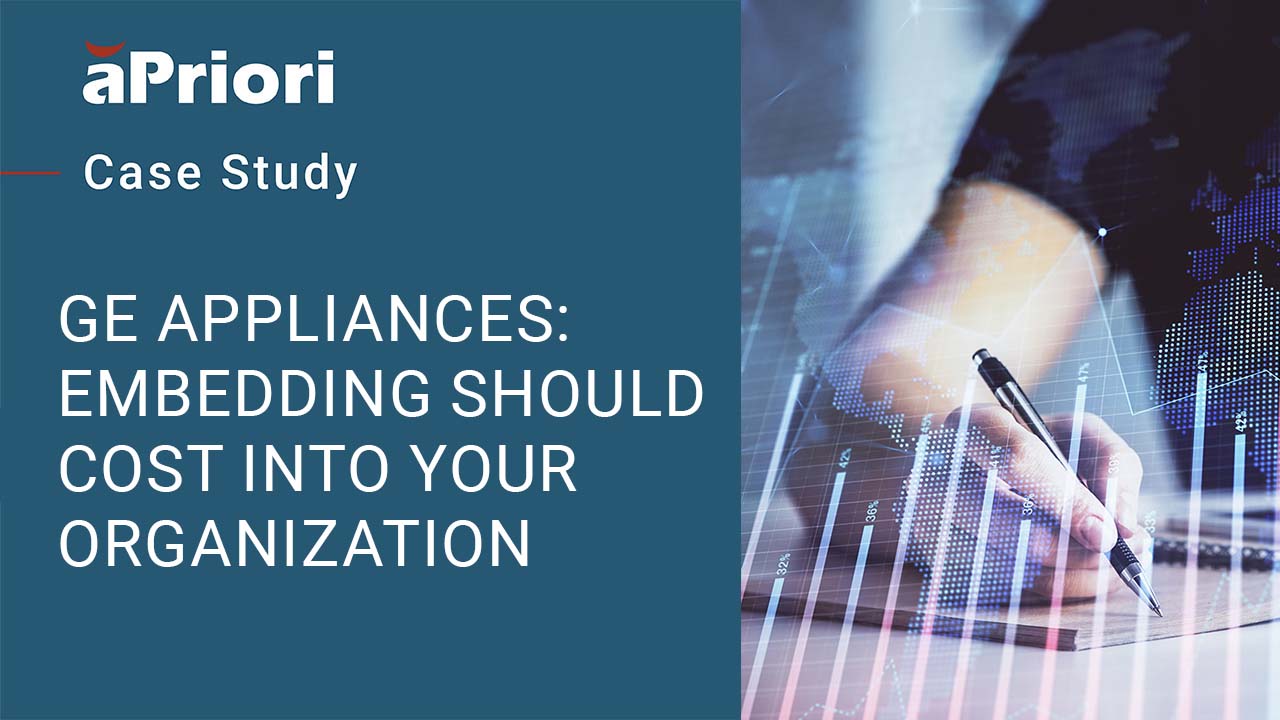
Transcript
Cost Management Leads to Cost Reduction
Jill Snyder: Thank you all very much. I’m thrilled to be here today with you all, presenting on a topic that I love, which is aPriori and Should Cost Modeling. So just a quick introduction of myself. My name is Jill Snyder, I’m the cost engineering director for GE Appliances. I’m an electrical engineer by degree, and I have a Master’s of Business Administration from Indiana University. And if you look at my background, this is kind of what we look for in a cost engineer, we want someone who has experience in design, we hopefully have someone who has experience in sourcing and supply chain, and we also want someone who has experience in manufacturing, whether it’s through supplier quality or another avenue, and the reason that’s important to us is we want our cost engineers to have a knowledge base around the parts they’re costing and cost drivers, I can teach anyone how to use aPriori it is very intuitive, but again, I really want them to have that core foundation skill set. Now, with that being said, I would like to introduce you to GE Appliances through this short clip, showing our family of brands, and to give you insight into the diverse portfolio of products and the millions of parts that we source.
Now you all can see why I love appliances so much. Now, aside from getting you to fall in love with our appliances, the other reason I wanted you to watch that video is so that you could see the complicated parts and assemblies that we are challenged with costing every single day. Now, to give you a few more details about GE Appliances, our economic impact can be felt throughout the United States, and especially in our five states where we operate our manufacturing facilities. Our national footprint began in our corporate headquarters and our largest operation in Kentucky, it ripples throughout our expanding manufacturing operations in Georgia, Alabama, South Carolina and Tennessee. Our US operations continue to grow as we invest in the company and serve our consumers and our customers. To meet this growing demand, we increased output at our 11 US manufacturing sites and micro-facilities to be able to build more than 2500 appliances an hour. Through our robust nationwide delivery network, we were able to provide an appliance every 13.8 seconds to our customers. And as you can see here, we procure 3 billion parts. We’re proud to call Louisville, Kentucky our home for the last 70 years, developed on 750 acres of land. Appliance Park was one of the first industrialized parks in the US and established in 1951. Our headquarters in Louisville was also our primary innovation center, where we have more than 1600 engineers working to find a better way. This is also our largest manufacturing site, which has five different facilities.
What is the Role of Should Cost in Your Organization?
So, now what I want you to think about is, what is the role of Should Cost in your respective organization? Is it for validation? Accountability? Checks and balances? Supplier negotiations? Metrics? Cost structure? Is it framework, oversight, governance, reference or “source”. The answers to this question could vary by company as well as implementation phase, what I’ll ask each of you is to keep an eye on what your goal is for Should Cost in your organization as it could potentially change and evolve over time.
So what do you think is involved with implementing aPriori, and what should be done to embed it into the organization? As we looked at embedding aPriori Should Cost into our organization, I chose to look at it with the framework of change management, because what we are working to do is to make lasting change in our organization, because with aPriori, we are truly changing the way people design and source their parts.
Supplier Relationships, Material Costs, and Cost Models
Now, while the steps in the change management process are generally the same, they may vary in duration and can be broken down into smaller steps as required for each organization and implementation. I will focus the majority of this presentation on steps two, three, and four, because as we’re all here today, we all definitely know we need aPriori in our organizations. At GE Appliances, we implemented aPriori mid 2020, it was a very challenging time to implement Should Cost as travel to our suppliers was limited or even non-existent. However, this required our internal relationships and relationships with our suppliers to be strong. And I’ll speak more about that later on, as well, we lean on the strengths of the individuals and knowledge base of the aPriori team who have been great to work with throughout this process. We focused the second half of 2020 on our sprint activities, raw material library, learning the tool and growing the team, to a team of four, who support those 1600 engineers I spoke about earlier. Our goal at GE Appliances is to cost as many purchase parts as possible, we did not focus initially on competitive costing, and we did not focus initially on make parts. But as you could see throughout this progression, our goal each year was to grow in our capabilities, to add additional aPriori cost models as well as surface treatments.
Understanding Manufacturing Costs and Key Cost Drivers on Both New Products and Existing Parts
Our goal was to learn each cost model individually before implementing it in the organization. Another key in this overall progression was in 2021, when we embedded Should Cost into our e-RFQ tool. What that means is aPriori became the fourth bid, so when a buyer goes out for quote, they also receive back a Should Cost estimate using that same template, same format that our suppliers do. As well, in 2021, we spent a lot of time on training our internal teams, both our engineers and our buyers, we monitored that in 2022, and then in 2023 did a total revamp of our training, making it more, broke it down into smaller chunks, that way people could watch short videos throughout versus long, lengthy videos. As well, we also focused time in 2023 on upgrading our cost model. Now, if you look at that slide there, you’ll see in 2021, we also focused heavily, and into 2022, on costing as many parts as possible, as we were trying to get commodities under control. Now, like I said in 2023, we were at a normal state, but one thing continues to be the same, and that is that each year or ROI, our Return on Investment using aPriori continues to increase.
Cost Management Case Study
Now, as we talk about change management, it is very, very important that we look at it before action review. Because having a solid plan and pre-work is so important, as individuals in our company learned about aPriori and its powerful capabilities, we got slammed with requests, therefore having the pre-work done in advance will help the team be more successful, so as we start with step two in the change management process, we’re gonna go through and decide what our intended culture will look like, what are our intended goals? What are our intended metrics, and then how will those be measured, and the important thing there is, we don’t want metrics that encourage a checks-the-box approach. As well, how could AP analytics be used for measuring those metrics? Our goal is always to have our cost engineers explain all of their time costing parts, not on spreadsheet metrics, established the frequency of reporting what the Pulse team should be for reviewing those metrics. And for us, the Pulse team was very, very important because it comprised of individuals in key strategic positions in their respective areas. They were able to help us get Should Cost out into the organization in their respective areas. We also include in those reviews our P&L owners as well as had monthly reviews with our CEO.
Product Cost Savings Training for the Entire Manufacturing Team
Next, we will look at what challenges we can anticipate and try to prepare those in advance for the team, and then what aPriori training is available. For us, aPriori academy has been huge. In the past we had to host those videos on our own, and now we can leverage the power of aPriori academy for training plans for our cost engineers. Now, that your before action review has been completed, we’ll focus on three areas for crafting the vision and plan for change, and those are organization-related, project-related, and system-related.
Now for organization-related, I break these into two areas, we’ll talk about resources first, and then we’ll talk about the framework. So for resources, knowing the skills, knowledge and background needed for a cost engineer can depend upon many, many factors. Those factors could include, which aPriori cost models you choose to use, the functional location within your organization of that team, what kind of support team is available to that core team, your CAD tolerance assessment, as well as whether you choose to have a centralized or decentralized approach with costing, and it is okay to go forward with the centralized approach early on to learn the tool and then decentralize later on, but the important thing is having metrics in place to understand when decentralization is important.
The Importance of Cost Engineering to Profit Margins
As well, decide on your aPriori administrator, and for us, one huge key has been lifting the level of cost engineering in our organization. You want to make sure the cost engineering team has the voice that they need and can be heard loud and clear throughout the organization. Now, I mentioned in the power slide that support team, and again, as we implemented in 2020, our support team’s very, very key for us. So as we look at the top there, we had within our technology team, a review of process routings, our internal specification requirements, finish specification requirements, because again, as you saw in that video, finishes are key. Next with our sourcing and procurement team and understanding of the “data sources”, raw material library management and supplier involvement, and that’s where our “transparency in details” in those are so important. With our SQE team, we went through a process of machine capabilities, optimal process flow and good part yields and defaults of those in aPriori. And I did say optimal process flow, because in the end, the goal is not to mirror that supplier’s quote, but rather give them a goal of what to achieve. From a CAD standpoint, CAD changes required translated into specifications for accurate detailed cost, so therefore, if we cost it apart or if we had a Part, a CAD model that could not be costed, we had that feedback loop back to our CAD team.
So they understood what needed to change in the future, and they were able to put those into specification requirements. Also, don’t forget about your subject matter experts, those can include your internal factory production, design engineers, fellow cost engineers, tool-in engineers and process experts, and even suppliers. A lot of times folks forget to include their tool-in engineers, but those are so very important as well because not only does aPriori give you that part cost, but also that tool cost estimate. When thinking of the support team, don’t lose sight in the project champions and ambassadors. With your project champions seek out an executive sponsorship. Define your steering committee. And again, going back to that Pulse team we spoke about before, the key here is that, these individuals need to be in strategic positions in the organization to be able to help you make that lasting change. Now, as we look at our ambassadors, they’re also very key in this overall picture, because in large organizations, it can be very difficult to keep a pulse on things, therefore, they are so important to give that feedback loop from their areas of the organization. Those can include the support team, design engineers, buyers, and don’t forget about project champions as well.
Now that we talked about the resource side, we’ll spend a little bit of time on framework, and that’s where that vision is so important. But not only is that vision created in a silo, but involving many parts of the organization, assess a competency assessment, do the internal competencies need to change or new ones be created, cross-functional relationships are also very, very key here, assess the strength of those. To find the process steps for hand-offs, so how far will the cost engineer take his or her work? Will they take it all the way into the negotiation phase, a business case or just the opportunity assessment. Also define those roles and responsibilities in access control.
Now, as we look at project-related, it’s very important to assess the product development process for Should Costing. If the product development process is the governance of your organization, then Should Costing as a part of that is key for the process to be the governance and to allow the core team to fall back on that. Robust “data” also needs to be available for the teams to use. Supplier transparency, again, is very, very key with that, and as we spoke about before, the road map involve cross-functional feedback with that roadmap development, assess the training plan for the organization, both for our engineers and for our buyers. Define the communication plan and keep it in the forefront, that is very key to always keep Should Cost as a communication plan in the forefront, in front of individuals. As well as define your implementation schedule and keep that in mind. And communicate that frequently.
Now, as we talk about system-related, aPriori has a great strength and ability to re-CAD PMI. So run assessment and decide what is currently available in your CAD and what you desire to have available, and then work within that team that we defined earlier, to get it to where it needs to be. Also define what should be extracted from CAD versus your PLM system versus the drawing, and which one is a source of truth. Create a request process and report location, because once the organization sees the powerful capabilities of aPriori, you will most certainly be very, very busy. Access data sources available for your cost team to use, those could include P-PAP first articles and such. Also define your raw material library management plan and frequency of updates, and again, assess what aPriori training is available. Now, as we talk about implementing the changes defined in step two, we must start with my favorite quote, A begin with the end in mind. It ensures that the right decisions are made throughout the implementation phase, when taking into account the vision that we created during step two. So again, during this phase we’re working to implement those items identified in step two and as before, as we look at implementing those changes we will look into the same three areas of organization-related, project-related and system-related.
Communicate the Goal for Should Costing Across the Organization
Now, for anyone who knows me, knows that any conversation when talking about change, I would always start with if I had a dream, because I do believe as we’re talking about whether it’s defaults or any cost model changes is so very important that we make sure that that end-vision is known and always communicated multiple times, that will ensure that we all make the right decisions for the end-game. It is also important that the organization understands through cost language, that aPriori is a CAD-based costing system, not just a spreadsheet that initially was hard for some folks to transfer over, so I always started every training that we had internally with that cost language, that way I ensure that that language became natural throughout the organization. Also again, review those competency changes or create new ones. Now, as we talk about the project-related task, so again, the product development process changes that we did probably is step two will be implemented, which also again makes it much easier for adoption. Continue with the Pulse team meetings, it is again, very important that Pulse team is comprised of organizational leadership that can make lasting change and has an influence on tool usage in their respective areas.
So again, for us, those Pulse team meetings included, again, our CEO and our P&L owners, that way they can ensure that it was used in all of their product lines. As well, we also had a quarterly report out through our global sourcing council, which was comprised of our other businesses within the Haier company, as well, utilize AP analytics for those reports, and again, be careful of metrics that encourage that checks-the-box approach. Evaluate the road maps that we created before for any changes that need to occur. So as we talk about system-related, I purposely put this here because once you start to use aPriori you will realize that there is a wealth of information available to you. So have a plan on what to do with all that data. Defaults for us, being able to increase the number of parts that we cost, we had to have certain defaults that also helped our accuracy whenever we were using the tool. The goal is to be able to get the same part to multiple people and get the same result. Again, define your raw material library management, access control and data sources, implement customization, PSO defaults, and then we define standard operating procedures, so that way we insured again, that two different people could cost the same part and get the same result.
So any of our key learnings would go back into a standard operating procedure. And define those mandatory fields in aPriori, do it early. Don’t wait until later on. Now, as we look at that final step, which is embedding the changes of the company culture and practices, the main purpose here is to audit for back-sliding and adjust as necessary in order to continue with embedment in the organization. Do we need to change any of the goals or metrics? Is a cost culture that we identified early on, present? Are we continuing to stay relevant, and are we continuing to stay in the forefront. Then also reassess what to start, stop and do more of. So we’ve truly had amazing growth in our organization, after using aPriori in the realization of our ROI goals. Once it’s embedded in the organization, it is truly difficult to understand how you operated before using aPriori. And I truly hope the same for all of you and your receptive organizations, and thank you again for this opportunity to speak today, and I enjoy the rest of the conference.