Video
The Green-Golden Ratio: How to Design for Sustainability and Profitability
Reduce carbon emissions, meet product sustainability goals, and increase profitability all within aP Design. In this session, we walk you through some interesting product design scenarios and look at how you can make data-driven design decisions to increase profitability while ensuring sustainability. Designing for sustainability and profitability involves integrating principles that not only reduce environmental impact but also contribute to long-term financial success. The “Green-Golden Ratio” concept suggests finding a balance between environmental sustainability and economic profitability.
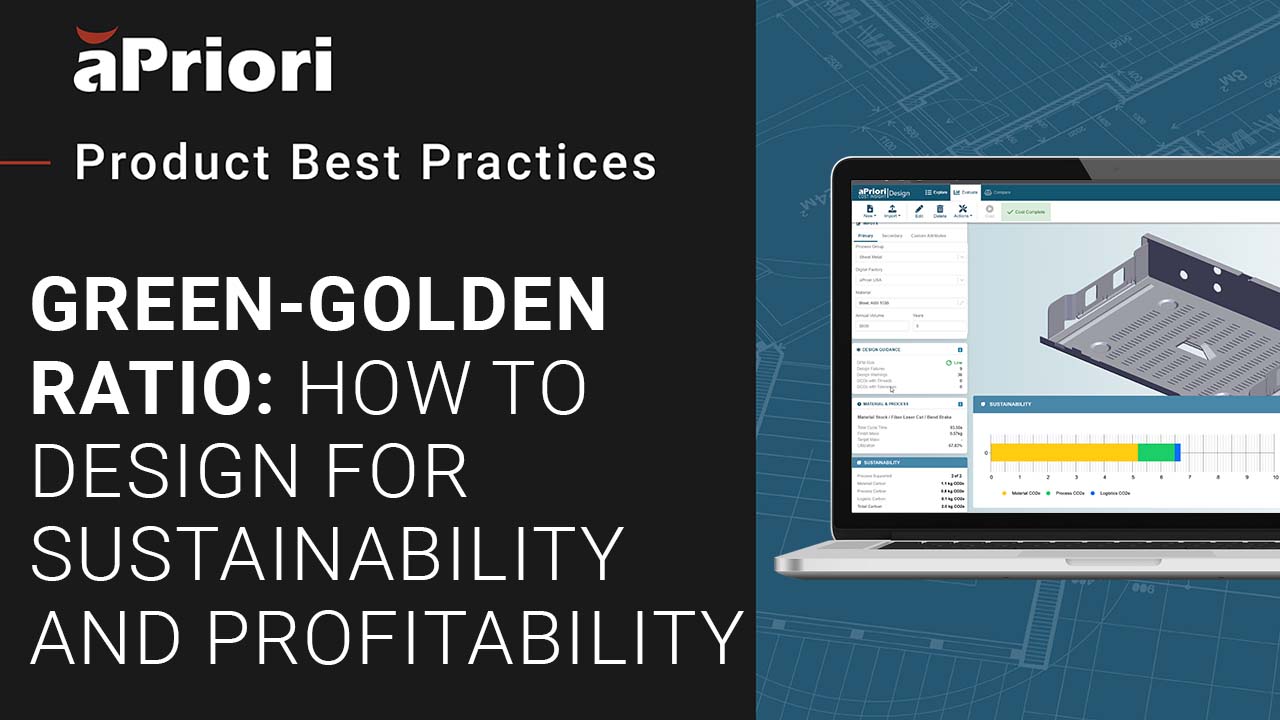
Transcript
Dave McDermaid: Hi, and welcome to this session on The Green-Golden Ratio, or How to Design for Sustainability and Profitability. My name’s Dave McDermaid. I am a director of Solutions Engineering for aPriori and EMEA. I have been working with customers and potential customers on exactly this, the balancing act between sustainability and profitability or product cost. Let us start with the title of this session, the Green-Golden ratio. There are two elements to that title. First part is green. That is easy. That is to do with sustainability. Sustainability is a relatively new concept, especially compared to the golden ratio. The golden ratio is billions of years old. It is a number, and this number is found in crystal structures, in the shapes of animals and creatures and life on earth. The way rabbits breed is based on the golden ratio. So let us explore that first of all. What is the golden ratio? Well, this is the shell of a Nautilus. And for those who know this, it is somewhat synonymous with the golden ratio.
Sustainable Design
DM: The shape and structure of that shell is based on that golden ratio, that number, and as are many other forms of life. The number, the principle is quite straightforward that whatever was previously built in this structure will be added upon in the next evolution of the shape of the shell. And how do we calculate the golden ratio? Well, we need to look at what is known as the Fibonacci sequence. This is a sequence of numbers that begins with zero, nothing. And then there is something, one. From something… From nothing to something. This is why the Fibonacci sequence and the golden ratio is also brought up in conversations and teachings and scriptures around divinity, from nothing to something. And then what we do is we add those two together to get a new number. Then we take that new number and its previous number, one and one, and add those together to get the next number in the sequence, two.
DM: Then one adds two equals three, two add three equals five, five add three equals eight, and so on and to infinity. And that is the Fibonacci sequence. The ratio between each of these numbers and its predecessor can be calculated. And the easiest way to show this is with a little demonstration in Excel. So in Excel we will copy the Fibonacci sequence, so we have nothing, and then we have one, and the next number is equal to that number plus the previous number before. And expanding that out, we have the Fibonacci sequence that goes on into infinity. The ratio between each of these numbers and its predecessor can be calculated. Equals that divided by that number there. And then if I continue that sequence of finding the ratio, you will see that we start to trend or tend towards a consistent number. Very quickly, it moves towards this number here, 1.618 something, something, something.
Carbon Footprint
DM: And that is the golden ratio. The golden ratio is defined as one plus root five over two, which in approximation is 1.62. The Green-Golden ratio is some other number. Perhaps it is this one that creates a relationship between the balancing act of making sure something we design is affordable and sustainable at the same time. And that is what we will explore in this session here. We will start with that balancing act, how we juggle between profitability and sustainability and the challenges of doing that. Then we will look at some examples of how we actually make an impact on carbon without compromising cost or complexity, how we try and strike that Green-Golden ratio. And lastly, we will look at how we identify opportunities with aP Analytics to find out where the best ones lie, perhaps even finding our own version of the golden ratio that we can use as an analytical tool.
DM: This diagram represents the three scopes for carbon reduction for manufacturing companies today. And then there are many opportunities and focal points for those companies. Like for example, giving all the workforce bicycles instead of cars can have an impact on the carbon footprint of that company. But the biggest area and the most significant ones for manufacturers of discrete products is around these two big areas here, the carbon footprint of purchased goods, things they procure from the supply chain and the use of the products. And those two elements form production CO2 and through live CO2. But it is a balancing act, and they can trade off different elements of the design or the manufacturing process or the manufacturing location to impact those things. And that balancing act is dependent on many factors. So for every industry, they have different pressures and constraints, and the way in which the product is used in the world is different too.
Energy Efficiency
DM: The material and the location manufacturing. The manufacturing process also have an impact on production carbon and through live carbon as well. And the physical design as well. The shape, the size, the volume. These are all the major elements. And what comes out of the process is different varieties of manufacturability, complexity. The weight of the products impacted by all these things, as is the energy efficiency. You can design something to be more energy efficient, but well, how much production carbon is required to do that. And each industry, like aerospace for example, dependent on the material they choose and the process they use to make things and the design of those shapes, the weight can be impacted, which has a significant impact on through live CO2. But as the aerospace world moves into eco fuels and perhaps even electrification, then they will be feeling the same pressures that other companies do, like the world of electronics and consumer goods, where they may be more focused on the production carbon. This balancing act has to be conducted with thousands of variables, including the design itself.
DM: But coupled with that is another layer of complexity in the whole equation. And it is the other part of sustainability because companies need to be sustainable with their products but they also need to be sustainable as a business. They cannot afford to make things really expensive to combat carbon footprint. And just the other week I was speaking to an automotive manufacturer who wanted to talk to us about just analyzing and understanding and reducing carbon. They did not want to look at cost, just the carbon element. But the two are coupled together so much so my suggestion to them was to build all their cars from carbon fiber and titanium. To lightweight the cars to impact through live CO2. Of course they could not do that because the cost of the cars would be unaffordable.
Design For Sustainability
DM: Therefore the two are coupled together. And if we compromise the cost to try and achieve carbon targets, then we are not going to be around very long as a business, and therefore we’re not even existing to be sustainable in the world. So that is the complexity challenge we are up against. So how do we use aPriori to make an impact on product carbon without compromising costs or at least striking that balance between the two. How do we use the manufacturing insights? Well, I am going to look at a couple of examples. I am going to start with one where we are going to design for sustainability, but we are going to design with the real world in mind. And in this example, we are already engaged with the supplier, and we need to stay with that supplier. It is no use finding the optimum manufacturing process if we cannot find somebody who actually has that optimum process.
DM: In this example, we do not want to change our supplier. They are a key supplier that produce parts regularly. And when the world gets disrupted, they maintain their supply chain because they are a good company. We want to work with them. But they happen to have slightly bigger machines, which is fine by us. We can then start to think about sustainability with respect to that actual company. Now, to go through this example, I am going to start off in aP Pro. And I am doing an aP Pro because what we are going to look at here is a combination of design concerns. And design ideas as well as manufacturing and cost engineering type activities. And aPriori professional is the place to go and look at that.
DM: So as I said on this part, we already have a cost analysis done that is based on a slightly bigger machine than is required. And that therefore forms our baseline for anything we want to do around sustainability improvement. The places that I look for sustainability improvement are actually all over aPriori. For example, I can see a material utilization up here of nearly 80%, which is not very good because we’re regrinding and wasting material in the process. I can see the breakdown of different parts of the process here. We are just doing all injection molding. So that is the biggest contributor. Then my sustainability tab, I can see the contribution from material and from the process. And actually there is a significant element from the process itself. I can also see different materials of different grades that I can choose from. That are more sustainable.
DM: So these are the obvious things to go and start looking at. From a design guidance perspective, there are manufacturing issues that are driving the cost and therefore the carbon in the wrong direction. For example, we have violated some maximal wall thicknesses here on this component. We are up to nearly thirteen millimeters thick when aPriori is suggesting a maximum of three and a half for this grade of material. And in aPriori, we can see where those are. So all the material thicknesses above four millimeters, say, aPriori can show me them. And on this part, you see all the red dots represent wasted material and wasted process. But also it represents where perhaps the design needs to be that thick to be structurally sound. But well, let us find out because that is just wasted carbon, wasted money.
DM: Also in here are a list of different materials that impact the production cycle time. So for my grade of material, ABS, here are other ABSs that have significantly less cooling time. They are more expensive per cubic centimeter. But perhaps they are more carbon efficient or cheaper to manufacture. And it is not always the obvious choice for design people that cheap material equals cheap production and lower carbon. It is a complex equation. APriori is also showing me where additional carbon and cost is captured in the design of the tool itself. So based on my design, the tooling is going to require some extra lifters to make my features in my design. So there is a whole bunch going on in there and lots of factors I can impact on the design. So the first thing I am going to do is redesign the component to account for some of those facts. My new design looks like this here.
DM: This is my new design. I have two rips instead of one, and I do not have those undercuts. I have managed to level out the wall thicknesses to make sure they are still structurally sound. And comparing the old designs to the new design. Well, on the right-hand side there is a new design. As you can see, the carbon has come down nearly 15%. So reduced carbon. And the cost has come down nearly 20%, somewhat. It is not always as simple as that, as I am about to demonstrate. So also suggesting the design feedback was changing the material type. I am going to select a glass-filled material as was suggested and just set that cost off and running, get it re-evaluated. The new material contains glass fiber.
DM: And according to aPriori, this will cool a lot quicker in the tool. It is a more expensive grade, but I now have a balance between the cost of the material and the cost of the manufacturing process and the carbon of the material and the carbon of the manufacturing process. It is a complicated equation. I do not need to worry about it. I just let aPriori sort it out. And within a few seconds, aPriori has produced a new answer. There is lots of ways of exploring the difference from one design to the next, but in aPriori, we have introduced a new feature so you can plot various things like fully burdened cost versus total carbon. So as you can see here, the purple bar shows you, my cost. My cost has come down. Unfortunately, my carbon has crept up a little bit. Not by much, but some. My goal is to reduce both, or at least compromise between the two.
DM: So far so good. Another area which we can impact the manufacturing carbon and the cost is through the design of the tooling itself. So either working with a manufacturing engineer or just as a design engineer who has some awareness of manufacturing options. Let us say we change to a multi-cavity tool. And this is quite a low volume part, but well, we can at least try to see what impact it is going to make. So we are going to go to a two-cavity tool. Again, the analysis goes off to run. And just for people who have not been using aPriori, while it is doing this analysis, it is doing all the hard math in the background. I could be getting on with thinking about other more important things like the next design iteration or be working on the drawing for this component. So I now have a new data point on my graph. And it changes to total carbon. And you can see now that my cost has come down but my carbon has gone up significantly. Now that could be my new manufacturing strategy. And to solve the carbon problem, I might want to start thinking about supply region. So for example, if these are the constraints we are really stuck with from a design and manufacturing perspective, then I could look at lower carbon regions like say Sweden and rerun the analysis in there to see what impact a different zone is going to have.
Design Process
DM: Now we are not suggesting here that the design teams make decisions about manufacturing location, but we can very quickly, just within a few seconds, understand if we can solve our cost or carbon problem with going to different regions of the world. If that is the only answer, we take that to the procurement teams early in the design process. That is a very powerful insight that can support more strategic decision making. So now when I plot the graph, you can see that my carbon is starting to come back within check again, we are coming back on the carbon front. So I could offset carbon by moving manufacturing to Sweden but maintaining my lower cost or somewhere in between. In fact, we have looked at lots of different options including a hot runner system. So we actually have a variety of different manufacturing design options to look at. And the easiest way to look at this is through aP Analytics. So along the bottom are all the different design and manufacturing options. And now I am plotting from left to right, the carbon drop. So we are focusing on carbon here. So from left to right we are reducing carbon and the blue bar represents the cost of each of these. So with respect to my Green-Golden ratio, it is somewhere in here. There is a balance between cost and carbon that I can choose.
Pick The Right Option
DM: Low carbon over this side, and low cost over here. Where do I pick the right option? We will come back to that later on. In this example, we are going to embrace some opportunities that come our way, especially in this case where weight is not critical for this component. My component is a flywheel. Here it is in aP design. Now the flywheel’s job is to store energy as a rotating mass. So the distribution of weight is not as important as the weight itself. Now we have some physical constraints in our product but weight is not that critical, shall we say. If I look at the sustainability information inside aPriori, I can see most of the carbon footprint comes from the material itself and a little bit from the manufacturing process. So if I want to impact sustainability of this part, then I got to focus on material. Going to my material selection window. The chosen material is a cast aluminum, it is our standard approach to things in our company, we have been doing it for years. And aluminum has a carbon footprint of 13 1/2 kilograms of CO2 equivalent to per kilogram of aluminum. So what other materials could I use?
DM: Well, if I sort this list here by emission factors, you can see right at the top of the tree are grades of steel. And these grades of steel have 1/10 of the carbon factor of that grade of aluminum. And there is lots of other considerations when we are using steel, like for example, the casting process is going to be more intensive because it takes a lot more energy but by how much? Steel is stronger, but it is heavier also. So can I redesign it to accommodate heavier weight to distribute the weight properly and make sure it is strong enough still to do so? And this is the design that I have produced. And remember I am now using a sand-casting process. So I can be a lot funkier with the design and create more organic shapes that allow me to distribute the steel as widely as possible. And when we are trying to maintain the same rotating mass, it becomes a bit of a design challenge to do that.
DM: But it is easy for me to do that in the CAB tool. It is also easy for aPriori to do the analysis of the cost, and the carbon, and the manufacturing process. And you can see here our carbon’s come down quite significantly by using that material. And now the process is more important than the material itself. I need to make sure cost is not compromised. So let me compare these two side by side. So the first thing we will see here is that the carbon has come down nearly 73%. That is a huge reduction. Imagine if we could do that everywhere in our products. Or with the cost. Well, the cost has crept up 3.3%. I am quite certain we could live with a 3.3% increase in cost for this part given the carbon footprint reduction. In fact, for some companies that small increase in price can be easily justified and accommodated by their customers when they’re selling greener products. But how much is a reduction in price that we can accommodate. Where is that Green-Golden ratio?
DM: Of course, aPriori is good at telling us where we can look for opportunities to improve carbon or cost on piece parts and assemblies. But in our organization, our products have many components in them and we have many products. Therefore, where do we begin to look for these opportunities? Well, we use aP Analytics. Because inside each manufacturing insight are many more insights we can use to classify and filter and plot reports to point to opportunities. Opportunities for just pure cost and carbon reduction. So this first graph we look at has, up the vertical axis, cost per kilogram of the part. On the bottom axis, CO2 per kilogram of the part. And the size of each of these bubbles represents manufacturability score. So big bubbles are complex and difficult to make. And we could factor that into evaluation of extra process, extra complexity, which equals cost and carbon.
DM: The ones over the right-hand side here like this one, contain more CO2 per kilogram of parts. So these are consumers of CO2. This is where I start my carbon reduction. And the components high up over here are ones that are more expensive kilogram. These are my focal points for cost reduction. And once I fix one problem over the right-hand side, I can start to narrow my search down. And of course somewhere in here is the balance between cost and carbon on these components. When it comes to carbon reduction, I can plot all the components I am interested in on a graph like this, where the vertical axis is now the material footprint from carbon, on the bottom axis is the process footprint, CO2 process.
Product Development
DM: And each component can then get assigned to a quadrant based on analysis as done by aPriori. The ones up the top right-hand corner are the biggest contributors to carbon. And I can see whether this is provided through process or material. Once I have addressed these components, reduced the carbon by doing what I have just done a few moments ago, I can then focus on some of the lower hanging fruits and continually chase carbon through the product development process or as we move towards our 2030 targets. These components over here are all about the process footprint. These components are about material. And I can bring in the right teams, whether they are from the manufacturing world or the design world to help solve some of these problems.
DM: So we can now not only find opportunities, but then start to classify them. So we engage the right people to solve the problem. Now manufacturability is something that aPriori understands, and it looks for Design for Manufacturing issues. These can also be found as well and they point to wasted energy. There is a relationship between energy and manufacturability of course. So we take a process group, like say machine components, and we plot all the parts on the vertical axis as cost. Along the bottom we have weight. Then there is a trend of cost per kilogram, as we saw earlier on. And above that trend are the components that are consuming more cost and potentially carbon. But they are also the size of these bubbles. And the color of these bubbles represents cost and manufacturability.
DM: So purple bubbles that are big above this line, are more difficult to make and highly likely to contain more carbon in the manufacturing process. There is another source for identifying cost and carbon reduction in the process by looking at manufacturability. But the biggest challenge is that when we look at cost and carbon, they are not the same thing. We are trying to compare apples with oranges. So the world has found a way of handling that. We call this internal carbon pricing or ICP. The idea is that we put a price on the carbon footprint. And that price is a real price for some people. For example, if we are importing materials into the EU from outside, we have to pay a tax.
DM: Or if our carbon footprint is too high or we do not achieve our sustainability goals, then we pay higher rates of interest on loans. All of the things ultimately cost money in the business. One of the biggest ones, of course, is if we do not meet our carbon targets, our revenue is going to be impacted, our sales will drop. Especially if we are a company that is focused on it. So in aPriori, we can plot this. On this graph here, we have a component that is manufactured in many parts of the world, from Europe over the left-hand side over to some of the Asian countries here. And if I plot the carbon footprint for each one, then you can see it ranges from a low footprint over Norway, high over in India.
DM: In fact, it is over double in India now. The cost of manufacturing in each of these regions is represented by the blue bar. So as the CO2 goes up from left to right, the cost seesaws up and down. Within the digital factories are other pieces of information, like the region of the world that we can use to calculate the ICP factor. And the equation of that is different for each company, and we can just modify that within aP Analytics. And now I am looking at a pure plot of the real ICP cost of these components. And now the red line tells me where I should start thinking about manufacture. And Hungary and Slovakia are kind of the obvious targets because they are local to me in Europe, for example, in my case.
Sustainable Products
DM: But here, Brazil is a very interesting region. Their costs are relatively low, but their carbon footprint is also. And it makes it a very attractive place for us to go and get things manufactured. And I can start to think about my business strategy with Brazil in mind, especially if I am manufacturing in different parts of the world. How could I work with major supply through Brazil to keep my carbon footprint low without impacting cost? Because the real reason that companies are in business clearly is to be profitable, is to make money. And the green companies are the ones that are green and profitable, because, as I said earlier on, if they are not profitable, they do not exist. They do not exist to be green. This balancing act between being sustainable as a business and being sustainable as a company with sustainable products, this balance is only becoming more important, certainly in the years to come. And aPriori is going to help us find that Green-Golden ratio.