Video
Embodied Carbon: The Hidden Cost of Manufacturing
This presentation explores the significance of embodied carbon in manufacturing, presented at the 2023 Manufacturing Insights Conference.
The discussion delves into the impact of manufacturing on global emissions, the rising demand for sustainable products, and the influence of legislation on sustainability reporting. The speakers emphasize the role of data-driven decisions in reducing embodied carbon, showcasing aPriori’s tools to optimize design, material selection, manufacturing processes, and sourcing decisions for a more sustainable and cost-effective outcome. The session underscores the importance of considering environmental factors throughout the product lifecycle and the potential benefits, both in terms of sustainability and financial performance.
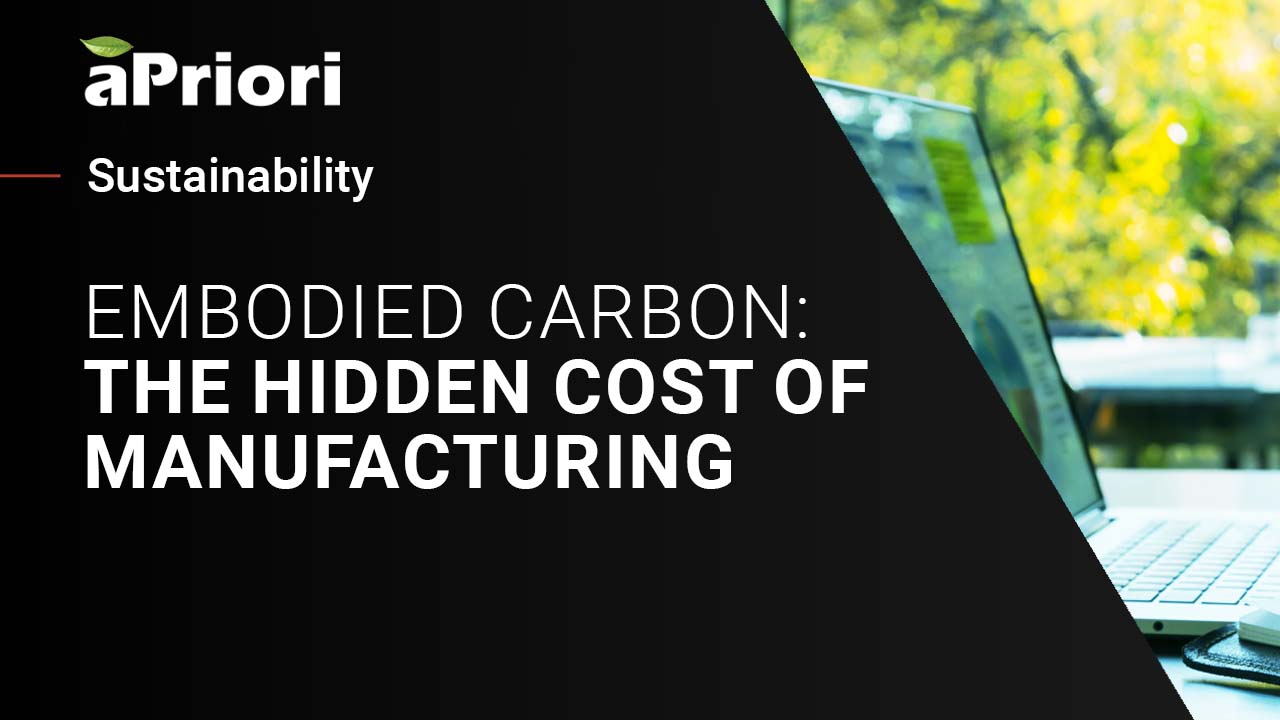
Transcript
Mark Rushton: Hello and welcome to this session from Manufacturing Insights Conference 2023. This one’s on embodied carbon, the hidden cost in manufacturing. This one’s gonna be presented by myself, Mark Rushton, Senior Product Marketing Manager for aPriori and I’m joined by Rodney Burns, who’s a Senior Solutions Engineer at aPriori. So what this session is all about is carbon, embodied carbon and it’s really adding a potential cost due to that into your products. And we’re gonna look at what factors contribute the most to your product’s carbon footprint and be able to analyze that. But what a lot of our customers and you probably want to do is make data-driven decisions to improve product sustainability.
CARBON REDUCTION DECISION MAKING RELIES ON DATA
MR: Now, manufacturing as an industry represents over half the world’s energy consumption and is responsible for over 20% of global emissions and we can really have an impact on that at aPriori and using the tools that we’ve got available, we can help move companies from intent to action. Now, when it comes to intent, 100% of companies in some sectors have already defined a sustainability strategy, but only 40% believe they’ve got the knowledge and capabilities to actually achieve that. And the pressure is coming from a number of different places. Consumers and stakeholders are now actually demanding more sustainable products and maybe some of your suppliers are requiring more sustainable building materials and products. And sometimes they are willing to pay more for them, they will certainly choose a more sustainable product when there is a choice available, but often they’re paying more for a more sustainable option.
Embodied Carbon Impacts and How They Affect Legislation
MR: There’s also a lot of incoming legislation and regulations around sustainability and that’s globally, so recently Brazil have just signed into law the requirement for sustainable reporting, ESG reporting to be compulsory, California just joined, including Scope 3 emissions as part of companies reporting requirements. And the EU has been pushing away, adding more and more regulations lately as well, so it’s really a global initiative that all countries are requiring from big organizations. And up until now, it’s been very complex and time-consuming to actually analyze the environmental impact of companies, all products and the only real way to do it is through a life cycle assessment until now. And those life cycle assessments are based on a lot of averages, a lot of assumptions and you don’t have the detail or the output to really drive any decisions or action. And by not taking it into account sustainability for products or corporate responsibility, you might find there’s a number of hidden costs. So a number of reports have found the certain dissatisfaction of employees can suffer if the company doesn’t have a sustainability strategy. You may have heard the term climate quitting, so that’s where some employees are actually wanting to leave their employer to work for someone with a more sustainable strategy and more sustainable ESG-focused culture.
Sustainability Metrics = Happy Employees & Happy Investors
MR: And you can see not only that, a lot of companies that have satisfied employees leads to better growth and better profitability, so it kind of makes sense that you would also find more sustainable companies are also more profitable. So there is a real business case for Net Zero as we mentioned before, customers and consumers are preferring sustainable responsible companies, 66% in this report and over 90% of manufacturing executives, C-suite executives actually say that ESG programs drive long-term shareholder valuing. Retaining talent is going to help drive financial performance and also the regulations coming in likely to bring penalties and taxes and tariffs in the future as well, which are only gonna affect the bottom line. As I mentioned, sustainable procurement leaders, they’re actually finding that by taking into account sustainability for one reason or another, they are actually becoming more profitable, so whether it’s down to retaining the talent or just having more motivated employees or all of the things add together to reward you with profit. So I think the question “Do ESG efforts create value?” I think that’s well and truly been answered, but it’s beyond planet and society’s benefit sustainable measures do correlate with financial performance from a number of reports.
MR: Bain & Co, the consulting firm, found many connections between sustainability and business results, whether it’s in supply chains, using renewable energy, reducing embodied carbon emissions, employee satisfaction and others. And investors are looking to become net zero as well, so if you invest in a company, you have to report on those investments activities, so by them looking to be net zero, they’re going to put additional pressure on where they’re making investments.
MR: So investing in sustainability potentially with aPriori as well, you’re gonna reduce the risk of any penalties that appear because of incoming regulations, you’re gonna have a much better understanding of where additional global greenhouse gas emissions are coming from. Reducing energy costs goes hand-in-hand with becoming more sustainable, if you can use less energy, you’re gonna have less costs and obviously you’re gonna be more sustainable as a result. Investing in renewable energy as well, whether that’s solar arrays on the roof of facilities that’s gonna save you cost, but also reward you with a lower carbon footprint. And employee retention really does seem to be affected massively by being a more sustainable employer with increased satisfaction. There’s a number of case studies where companies have saved a lot of money hiring new employees just by introducing some very simple sustainability initiatives. So the ROI for today and future generations is definitely going to be there, so for Gen Y and Z, a larger percentage of the economy now, they are actually demanding products that align with their values and sustainability is a top priority. And net zero can have a positive effect that triggers this cycle of investment and innovation and cost savings, they are closely linked, and one can lead to the other and have this rolling knock on effect.
Putting a Price on Carbon Equivalent Emissions
MR: And a number of top companies are using Net Zero as more than just messaging, it’s actually an investment strategy, so it’s more than just a… It’s not a cost burden, and it’s a catalyst for innovation and success. So one thing a lot of companies are starting to do is actually put a price on their carbon equivalent emissions and it makes it very simple to make decisions because you’re putting carbon and cost into the same currency, the same units. So when you look at carbon and cost in isolation, it’s very difficult to make decisions around what’s the most important. So by putting a price on carbon it converts it to the same units as cost and it makes it very easy to evaluate trade-offs. So you can start to look at the benefits and disadvantages of sourcing in different locations or different processes and things like that. And a lot of multi-national companies are using an internal carbon price to do just that, to make the right decisions. And you can see energy companies are really leading the way with companies that are using an internal price. And you can see there’s a lot of other industrial sectors that are following suit. So you can see industrials there, which covers manufacturing is fifth on the list, and a lot with a plan to do so in future as well. And then looking at what price you put on carbon.
MR: Well, at the moment, it ranges based on what industry sector you’re in, so there’s a quite a wide distribution of internal carbon prices and there’s no real formal standards, this is just something that you can put into place to help you with your sustainable initiatives. The two large manufacturers, Volvo and Volkswagen, they’ve got publicly announced internal carbon pricing, so Volvo they are around about $100 per ton of carbon emissions and Volkswagen currently at 60 Euros this year, but they’re looking to increase that. They’re looking at the Pan-Canadian approach, they’re looking at starting with $65 per ton of carbon emissions, but they’re looking to increase that every year to reach up to $170 per ton by 2030, just to really put more influence on reducing carbon emissions.
Demo: How to Use aPriori’s Digital Factories to Reduce Your Embodied Carbon Footprint
Rodney Burns: Our Manufacturing Insights Platform utilizes the 3D CAD or the digital twin to unlock insights into cost and manufacturability. So we use that across the digital factory to automate analysis and generate insights into these aspects and these are insights we can generate quickly to take action and unlock best-in-class products. What we do then, the next logical step is to lay on top the sustainability data as part of the same simulation to get additional data to unlock more opportunities within our platform. When we start to look at parts and assemblies, I was a manufacturing engineer for a long time, almost 15 years, to look at CO2, we would take the traditional cradle to grave approach looking at the big three: the material, the manufacturing, the logistics of the components. But where exactly does that lie? Because we utilize a bottom-up approach, we can use that in our carbon assessment as well as our cost assessment and unlike an additional layer of insight into where exactly the big drivers of carbon are within the process. And I want us to take action into the areas that make the most sense for our efforts and our resources.
MR: So how do we do it? Well, we look at four of the main drivers and material selection is the first one, the actual design, so the geometry of the shape, because we’re reading the CAD model as Rodney already mentioned, we actually take into account the specific geometry of that design. We’ll simulate the manufacturing process and get accurate cycle times and things like that and couple together all of the different sub-processes that go into that and then look at the location as well and that includes the local energy mix/energy efficiency. So material selection, typically it accounts for 80% of the embodied carbon, it really depends on the process and the material, but material usually is a big contributor and the design really does have a significant impact. If you’ve got something that is quite a very long, thin, for example, the cycle times are gonna be very different if it was much more kind of bulky and short and wider.
Manufacturing Process Affects Material Utilization
MR: And the way life cycle assessments (lcas) take that into account is just by looking at the mass. So you can see very different geometries, you’re gonna have the same mass, and so life cycle assessments is just gonna lead to a lot of inaccuracies and less precision. Then the manufacturing process, that really has a big impact on the material utilization, so how much waste comes out of that process is going to determine the overall amount of embodied carbon that goes into the design.
MR: Something else which life cycle assessments don’t really take into account is the wasted material, they’re really just looking at the finished mass of a product. So that really doesn’t go into that, a lot of presumptions. Then the manufacturing location, every country, every region has got a slightly different energy, a different energy mix, so some of their electricity generation could come from coal, gas, nuclear or renewables. And so based on the energy mix, it’s gonna have very different impact based on where something’s manufactured and those first four things is what aPriori calculates at the same time as cost. So you’ve got a really good understanding of what is going into that. The things on the right hand side, logistics, the in use phase, and the end of life phase, so the logistics is usually a very small percentage of overall product carbon footprint, it’s around 2-5%.
How aPriori Can Help to Identify Environmental Impacts and Carbon Reduction Opportunities Per Industry
MR: Generally, if you’re using ground transportation, it does bump up quite like if you start to use air transportation. Now the in use phase varies massively based on industry, if it’s in aerospace, for example, if something’s flying around using lots of fossil fuels, the in use phase is gonna be quite a lot, so lightweighting is important, and then the end of life phase is, again, lots of assumptions, something could end up in landfill that’s completely recyclable or it could be incinerated, so it’s really just an assumption and not something that’s really calculated with any precision. And what we found from customers looking into sustainability, there’s four main stages of maturity or steps along a sustainability journey.
MR: The first one is really looking at satisfying reporting requirements, starting with a baseline, some measure to look to improve upon and measure against. That is really the first level. Then the second level is kind of the easiest step, it’s to really put pressure on to your suppliers and look at a sustainable sourcing approach. Now, this way, you don’t need to change the design or the process or anything like that, you could potentially look for slightly greener materials, with more recycled content, things like that, but the design doesn’t really have to change. So it’s something the sourcing team can do mostly by themselves. And the third level is kind of a value engineering-driven approach, almost like a VAVE kind of approach, where we start to look at different materials, potentially look at tweaking the manufacturing process to be more efficient and things like that, just looking at existing designs to see what improvements we can make.
MR: And then the last stage is sustainable design, so this is the most mature you can possibly be, its designing products with sustainability in mind. Everything mentioned before comes into it, but when you’re designing a new product or re-designing an old product, you’ve got sustainability in mind, you’re looking to use the least amount of energy, so you’ve got the least amount of embodied carbon and you’re using the best materials that you can. And if you start at the end with sustainable design, that is really where you’ve got the most opportunity for CO2 equivalent emission reductions.
MR: So much like cost, you’ll find that at the early stages of design, you’ve got a lot of design freedom ’cause nothing’s really locked into place, you have not made any commitments to tooling or processes or anything like that, so you’ve got a lot of design freedom and that goes for the same with carbon equivalent emission reduction potential as well, there’s a lot you can do to reduce it, ’cause nothing’s really set in stone. As things progress toward to the final sourcing stage, any changes can be a lot more expensive. There is much more of a knock on effect, you might have committed to some parts already, so there’s less design changes that you can make and therefore you’ve got less opportunity for reducing the environmental impact as well.
In Depth Demo: Machined Component’s Embodied Carbon
MR: So now let’s have a look at the contributors to product carbon footprint in a little bit more detail. So if we were to evaluate different manufacturing processes, let’s take this EVCU as an example, it’s a diecast or potentially machined component, we’re looking at the metal component on here, in this case, it’s an aluminium component, we’re gonna use the USA diesel factory as the location for the manufacturing simulation and we’re gonna propose an annual volume of 5500. So which process do you think would lead to lower CO2 emissions? You could look at casting, it looks like a very high energy process compared to machining on the right-hand side, but what do you think would result in the largest embodied carbon? If we look at the material, we’re using the same material for both.
MR: But the raw form of the material for each process is slightly different. So die casting, it’s a more raw form using ingots to melt down so we can get away with a slightly less refined material. When it comes to machining a billet, it’s gone through a lot more processing and it’s got a slightly higher embodied carbon per kilogram. And then when we look at the material plus the processing, here you can see the material really has a big impact, die casting, although it’s got double the energy requirements in this example as the machining example, it’s really down to the material that makes the difference. So why is die casting so small? Well, it’s really because of the material utilization. And when we look at material utilization, the waste is much less when it comes to casting.
MR: Whereas machinings, obviously all the material that’s removed doesn’t go into the product. So a lot more waste, a lot more embodied carbon. And the same is true for cost here as well. So it’s quite a synonymous in this example. Less waste means less cost, so quite easy. And it is all down to minimizing that waste. So you can see the rough mass in the light blue color is what goes into the manufacturing operation. And the dark is the finished you can see that’s exactly the same for both ’cause it’s the same design. But all that extra material leads to higher embodied carbon.
MR: And as we mentioned at the start, materials do contribute the majority of CO2 emissions for a range of processes. So full stop machining, for example. It’s a huge percentage ’cause of that low material utilization. And these are average figures across a range of different designs that we’ve tested. Die casting, again, slightly lower due to better material utilization, but it’s still having a much bigger impact overall. But that’s not always the case. And we’ve gone through a lot of counterintuitive examples where it’s not that straightforward. So for the next section, Rodney’s gonna take us through how we can make the right decisions there.
How aPriori Enables Data Driven Decisions on Embodied Carbon Footprint
RB: Okay. So I’m gonna lead through this session on how we enable data-driven decisions with insight into sustainability to help with making good business decisions from a business perspective. So as Mark mentioned earlier, we can have the greatest impact at the start of the design life cycle is where we have the most chance for change and opportunity. And the further we get through that towards sourcing, the less impact we can have and the higher the cost of change. But we want to review where we’re at today from the, if you recall, the tracking process from sourcing right through to design. And we’ll take a few case examples and we’ll work through them to see how we enable those fact-based decisions in that process. But as I mentioned, we utilize this to help us make fact-based decisions on business problems. So this is a case in example, with a train manufacturer that’s one of our customers.
RB: And this is an example of how we look at the business problems. So we have strategies here to lightweight this for in-process carbon, we need to reduce the weight of the components. There’s increased inflation. All new products must incorporate sustainability principles and reporting into its CO2 footprint. These are all business challenges that we need to address. But we’re gonna do here is we’ve started to look at this from a design perspective, that stage where we can have the biggest impact. And the part in the middle of your screen there is the current design. So it’s a welded assembly and we’re looking at some initiatives around part consolidation, trying to make parts less complex and reduce weight. So in this case, for example, we started off with our baseline. It’s very important to get the baseline correct and as Mark mentioned earlier, we read the geometry and we take that bottom up approach so we can very accurately and quickly determine baseline with for the product, with a high degree of accuracy.
RB: And we can start to look at the weight, the cycle times and the cost, etcetera, all at the same time. But with this initiative, we just wanted to see was there actually economic viability in moving that from an assembly to a single piece component. And you can see here some of the numbers stack up that there’s a cost saving, but more importantly you can see that there’s cost savings attributed towards the carbon itself. If we apply the likes of an ICP, for example, here you can see of a €100 per ton. But also we can leverage other benefits with improvements on the cycle time and reducing the carbon footprint in the process whilst also improving the cost of the product. Here’s another case example of a plastic part with a luxury EV manufacturer, they’re designing next generation products.
RB: So they want to be competitive and be lightweight their product to be competitive in that market space. Obviously the weight of the component helps with the in use carbon which needs to be assessed as well. And they want to make sure that there needs to be quality in their product. So again, it’s business goals, but one of the things we looked at is this was a single piece part and it was driving a baseline cost here of €12.51. And we have a baseline CO2, but this is a counterintuitive one because we wanted to look at this and check for economic viability of moving this to a multi-piece. So in direct contrast to the previous example, they were able to look at this from a multi-piece part, so breaking it into smaller components. And you can see again, in this case, there was cost savings and going in the opposite direction. So they were able to leverage using smaller machines with lower energy usage and injection molding processes for this particular component. So as you can see, it is not a one size fits all process. It has to be done on almost a case by case process. So applying an overall strategic initiative such as part consolidation or increasing parts or reducing part size may not fit all applications. But that’s where we are able to do this analysis very quickly to understand it on that case by case basis.
RB: This scenario I’m gonna walk through is, I’m gonna walk through the entire scenario now. So again, it’s about solving business challenges with those insights into CO2 sustainability and what that means to the business ’cause it’s a trade off on the levers of manufacturability and cost. Every time you do a change to one of those levers, it impacts the others. So where are those levers and what does that mean? So you can see the various business challenges here and auditable improvement in environmental impact. There’s inflation. We need to reduce lead time and all products have a sustainability principle to report on CO2. This particular case example was for a customer that’s in the EU and there’s lots of legislation at present around reporting CO2, particularly around Scope 3, etcetera and i4, CBAM, etcetera. So the first thing we’re gonna do is evaluate the baseline. I’m gonna walk through each of these steps. Once we get an accurate baseline, we want to improve the designs, optimize those designs and then assess for supplier alternatives, for example. So we’re walking through that design to get cradle-to-get process from each of those stages to look at fact-based data-driven decisions for each of those stages and each of those user cases.
RB: So when we started off this particular component, it was a sheet metal component with some chrome plating and we see our baseline cost, our weight example and our cycle times. But fundamentally we see our CO2 on this product. So with a design change, there was an investigation on change in the material from a metal to an acetyl with a decorative plating ’cause we still need to maintain the aesthetic required. So you can see there’s an improvement here on the cost and the weight, which is a major improvement. But you can see we also have lost part of the benefits with the sheet metal process. The cycle time has increased. So this is a high volume part, so this is very important. We moved to a new option to try and see for alternative materials that maybe improves on weight and also on the carbon.
RB: But you can see here it had to be a painted finish because aPriori was able to give insights into the fact that we can’t apply that surface coating to a nylon based material. So it was excluded. We then looked to optimize the process because cycle time was obviously important to the process. And we can see we have a significant improvement, 25% of the cycle time, but more importantly, we’re actually faster than our first baseline product. Then we want to look at the sourcing initiatives. So we’ve now optimized the process from a manufacturing process and design perspective. We now bring in the sourcing initiative so we can start to strategically look where we can source the product, maintaining our carbon initiatives and our performance.
RB: This particular chart shows how we can work through from the design impact by applying a internal carbon price here for each of the stages we’ve just walked through. So what this fundamentally shows is the earlier you can actually make the impact from the designs phase, the greater the impact you can actually have. But this allows you to look at what those trade-offs and cost and carbon impact are together as a whole. So as I said there, just to recap, we’ve evaluated the baseline, identified potential quality issues and cost drivers, we improved the design with the design for manufacture feedback provided. We optimized the process to reduce manufacturability issues and improve environmental impacts. And we were able to then assess suppliers and compare different options in various countries within seconds to try and see where our best sourcing strategies are.
Identifying an Internal Carbon Price Per Component with aPriori
RB: This is a very simple component where it’s gone through an iterative design cycle and we’ve applied an internal carbon price to this particular component. Now, it doesn’t seem very much the cost savings per year here, it’s €600 per year, but that’s only one component. When we scale those estimations across the portfolio of parts, this very quickly starts to add up to some very high numbers. But everyone always focuses on that high number but what does that actually mean? When we look at carbon across companies, every company based on their industry and their region will be allowed a carbon alliance based on their size of company, the industry they’re in, the region around the world they are. But what I’m trying to emphasize here is we need to baseline our carbon to try and offset against some of the potential carbon charges. So if we look at 2023 here, there is the alliance that has been given in the dark blue column.
RB: If we baseline on the gray column, there’s an over allocation of carbon in our industry, we then have to offset that charge either by buying green energy or looking at carbon offsetting initiatives such as planting trees, et cetera, to offset that carbon footprint. But other companies want to utilize the information and the insights that aPriori can give to push into the light blue and generate revenue. And this is where they’re below their allocation and can start to generate revenue by trading their carbon credits on things such as the European emissions trading scheme, for example. And some companies have actually generated quite a lot of revenue in that per year based on the fact that they can give credible results to justify their carbon credits and trade that value.
RB: One of the things we utilize as well is the fact that we can automate and generate analytics reports to identify the carbon culprits, the high components that are contributing the most carbon within a product portfolio. And we can break that down into two aspects, the carbon from the raw material that’s being used in the product and then the carbon generated from the process and see which variables we want to trade off against. So we can look at which products are generating the most in our process from an overall product portfolio side, but then target on where we can impact. So for example, can we impact more on the process? Can I use an alternative manufacturing process, say water jet versus fiber laser, for example, and improve my carbon, but minimizing the cost impact or potentially even improving the cost in parallel to the actual carbon itself as well.
MR: So there you go, some really nice examples. It’s definitely not straightforward to just reduce the carbon as Rodney mentioned some counterintuitive examples as well as the more intuitive ones. So how can we impact emissions in manufacturing? Well, starting with design, designing for manufacturability, optimizing the manufacturing process, definitely gonna help. And that’s where aPriori can help you do both of those. Material selection, as you mentioned, it’s over 80% of embodied carbon depending on the material and the process, we can help with that. We can help you with making the right material choices and looking at the material utilization as well. The process, making sure the process and the routing through the manufacturing facility is as efficient and low impact as possible.
MR: That’s gonna add more embodied carbon, the more processes that you add and depending on what they are as well. And that’s something that aPriori simulates as part of the process. And then the final sourcing decision based on the local electricity mix. What sort of energy generation methods is the supplier buying? And what processes, what sizes of machines are suppliers using to match what they have in their facility? So aPriori always got the full suite to measure embodied carbon along with cost to really enable those data-driven decisions that Rodney went through. That brings us to the end of the session. I hope you enjoyed it. If you’ve got any questions, do get in touch. But thanks very much for joining us.