Video
DEMO: aPriori’s Additive Manufacturing Capabilities in Action
Is additive manufacturing right for you? Learn how aPriori can help you identify the break-even point for additive vs. subtractive manufacturing.
aPriori supports several additive manufacturing processes, including material jetting (3D Printing), Direct Metal Laser Sintering (DMLS), Selective Laser Sintering (SLS), and Stereolithography (SLA).
In this video overview, we’ll review the benefits of additive vs. subtractive manufacturing, including the potential tradeoff considerations, production volume impacts, complexity impacts, and more. Plus, we’ll show you how additive manufacturing works inside the aPriori ecosystem with a hands-on demonstration.
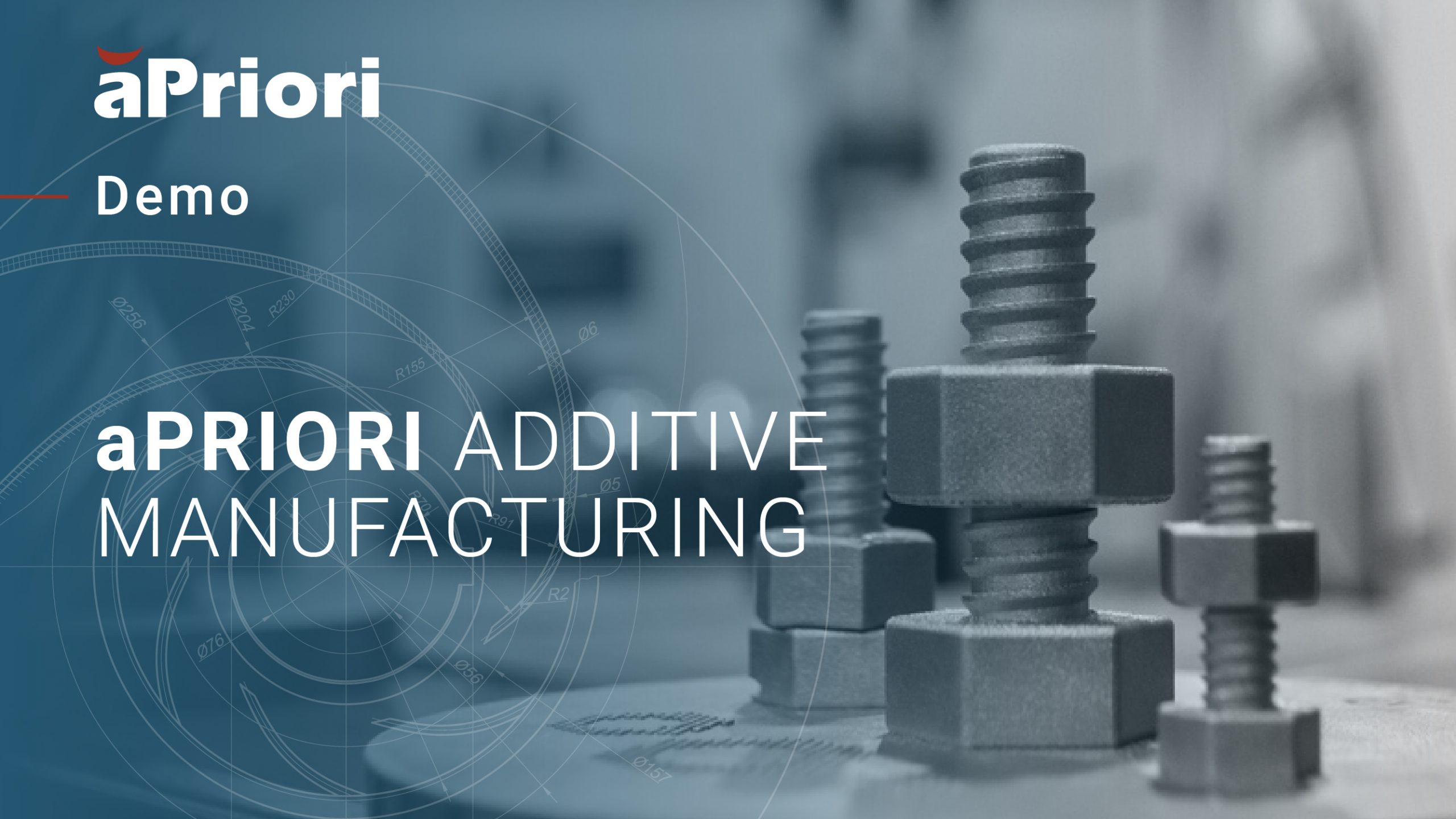
Transcript
How to Break Even in Additive vs. Subtractive Manufacturing
Cormac Eastwood: Today we’re going to discuss additive manufacturing, finding the break-even point with aPriori. My name is Cormac Eastwood, and I’m currently the Product Manager for aPriori Professional. For the last three years, I’ve been working for aPriori in various roles, beginning with expert services consultant and moving through into cost modeling, and finally, in my current role, Product Manager. Previously, I have 10 years of manufacturing experience in heavy industry, working in product development, ranging from sheet metal fabrication up to assembly lines for transmissions. In the agenda today, we’re gonna discuss the additive manufacturing background with three informed decision-making of a brief overview of the aPriori cost model, and then we will find a breakeven point between an additive component and a casting component in a demo in aPriori Professional.
Choosing Additive Manufacturing Techniques Over Subtractive Manufacturing Processes
So why would you choose additive manufacturing? Additive manufacturing gives you design freedom, allowing you to optimize designs while reducing width and maximizing strength. We can decrease turnaround times and reduce investment as there will be no jigs, fixtures, or tooling required. And quite importantly, we can improve our material utilization by only using what we need. Additive manufacturing can be utilized across many industries. It truly gives us design freedom to fix a wide range of problems, problems ranging from medical inserts through consumer products to industrial, aerospace, and automotive. In aPriori, we support four different processes within additive manufacturing. These processes are material jetting, which is what most people recognize as 3D printing. This lets us deposit droplets in a layer-by-layer format and cures by UV light. Typical uses here are for non-functional prototypes, and the materials we utilize are rubber, ABS, polypropylene, or wax casting.
The second process we look at is direct metal laser sintering. Here we use a metallic powder to create a part also printed on a layer-by-layer format. The typical uses here would be checking the fit, form, and function of a new design without paying for an expensive part. And our typical materials here are metallic, as mentioned by the powder. So we would have aluminum, cobalt chrome, copper, dentaurum, and various ranges of steels and titanium alloys. Our third process would be selective laser sintering. So here we use a reservoir of powder, which then gets solidified using the laser, again, being built on a layer-by-layer format. Again, we look at uses here of fit, form, and function prototypes. However, here we use materials such as plastics of nylon, polystyrene, polyetherimide, PS, and PA. The last process we utilize in aPriori is stereolithography. Here we use photo-polymeric resin. Here we use a photo… The last process we look at in aPriori is stereolithography. Here we use a liquid resin as a base to create our part, again, on a layer-by-layer format. The uses for this process would be form and fit prototypes, so if we’re doing a visual check, ergonomic checks, or aesthetic checks.
Making Informed Tradeoffs and Production Volume Decisions
This is similar to our first 3D printing, where we utilize rubbers, ABS, polypropylene, polycarbonates, and other specific materials for stereolithography. So let’s have a check on informed decision-making. What trade-offs do we need to consider for additive manufacturing? If we use traditional methods, we get cheap parts, which may be slightly heavier at high volumes. However, at low volumes, our part cost rises in traditional methods such as machining or casting. Part cost in additive can be high. However, it will likely be lower than subtractive manufacturing methods for the lower batch numbers we talk about in prototypes. If the performance is acceptable and the weight is optimized, typically, these parts can be turned around in a short lead time.
So that turnaround time is a key consideration. As we grow our production volumes, this becomes a key factor in the breakeven point between methods. The higher the volumes, the lower the cost for traditional methods due to machine utilization. Additive manufacturing is not as cost-effective in this regard as your production volumes go into the thousands. Additive machines are cheaper, and cost level off a lot sooner, so there’s less of a cost delta as the volumes grow.
Automotive Example of Additive Weight Reduction and Part Consolidation
Although additive doesn’t have a huge cost delta as the volumes grow, it also doesn’t have a huge cost delta between simple and complex parts. So the flexibility to print detail if required is there for the users. Balances against the machine’s detailed part. A detailed machining part may require a lot of passes, some tool changes, possibly machine changes, which will obviously drive cost up. Subtractive methods will have a greater cost delta between simple and complex. Let’s take this automotive example of additive weight reduction and part consolidation. An automotive company was investigating using additive to support electric car development. So obviously, the lower weight in an electric car, the less energy consumed through the battery. Traditional design in this example had eight components of various different types, plastics, metals, et cetera. Joints increase weight and reduce strength in this eight-component assembly. And also, there’s several suppliers to manage. Using generative design and considering additive manufacturing processes, the designer can reduce the number of parts to one component, making the component lighter and stronger, and also can utilize on his cost journey, aPriori to cost during the different iterations of generative design. This allows the designer to pick the preferred method of additive manufacturing process.
Real-Time Cost Simulation and Breakeven Analysis for a 3D Printer
So what about the aPriori cost model? In aPriori, we look at real-time cost simulation applied to additive manufacturing. Currently, we support four processes, as previously discussed. Direct metal laser sintering, selective laser sintering, material jetting, and stereolithography. Our use cases in additive manufacturing would be early design decision-making, design-to-cost part optimization, and supplier negotiation. The key features here are physics-based cycle time calculations, build direction, so we can simulate different options across different build directions, support structure identification and removal, evaluating our tolerances, evaluating our secondary machining options, material cost tradeoffs, nesting optimization, and evaluating our layer thickness overrides. So let’s have a look at aPriori Professional and demo how we can do some breakeven analysis.
In this demo, we’re gonna cost some parts and additive processes, and then we’re gonna compare them with the casting part of a similar geometry and understand what is our breakeven point. The first thing we’re gonna do is open an additive part in aPriori Professional. Now we’re gonna select additive manufacturing in the cost guide, and we’re gonna select the material for our initial cost. What you will see in the material selection is that we have a process column. So each material is assigned to your process, and the user can, from this point, effectively pick the process they’re using. We’re gonna start off with 3D printing. We’re gonna select an ABS-type material to force aPriori to cost in the 3D printing process.
So now that we have our cost and a completed casting, just gonna have a quick look at the processes under material Jetting. So we have printing, which is our 3D printing, and breakoff, which will break off our support structure. Quite a simple process, material jetting. Now we’re gonna look at our cycle time. Our cycle time currently is around 1890 seconds. And let’s go to our process setup options. Previously I mentioned layer thickness. We’re gonna change our layer thickness value from our default, 0.03mm, to 0.06mm. So our layer thickness is the amount of material deposited in each layer across the bed. So the thicker the layer, the less process to create the part.
So let’s see how that affects our cost. As you can see, our cycle time has now reduced to 1290 seconds. So now, let’s move on to our direct metal laser sintering. I just selected an aluminum material as we’re gonna compare an aluminum printed part with an aluminum casted part. So again, let’s look at the processes involved. So we have metal sintering. We have a powder recycling, which includes sieving and powder loading. Again, we have a breakoff which breaks our support structures. We also have some secondary machining heat treatments due to this being a metal part. These are all default processes added by aPriori. Here we can also see our build direction. So the direction of the arrow shows the direction that the build is occurring on and that we are building.
We can also now see our support structures. Our support structures are shown in pink. And this is a structure from the bed of the table used to build the part in the vertical direction. After the part is printed, the support structures will then be cut off. However, If you find a support structure is not valid in your assessment, you can create a no-cost feature as we’ve just done with SupportStructure2. This will ignore that support structure in your costing analysis. The last thing to check before we do any break-even analysis is our nesting, as mentioned before. aPriori will nest your parts based on the bed size of the machine selected, similar to how we nest sheet metal and stock machining. This will best utilize your machining features.
So now we’re gonna move on to our analysis. Previously, our volume is 5,500. We’re gonna change our volume to a volume of 30, which gives us a more realistic volume for a prototype part. On costing this part, our cost has went from $150. If we just wait for the costing to complete, it has now changed to $360. So again, lower volume, higher cost. Now we’re gonna open a casting part to compare against. This casting part has been designed in the same manner as the 3D printed part, and we’re also gonna cost this with 30 per year. So the cost for this part is $537. So at this point, we would say that aPriori is selecting the additive part as the more cost-effective part.
So I’ve now created a roll-up of each of the parts, the one additive part and the one casting sand part. As we can see, we do have that cost difference, $360 for the additive part, $537 for the casting part. We’re now gonna utilize an excellent report created by our expert services team, which will show us a breakeven crossover part in Excel, so let’s launch the report. So this report will take our basic volume of 30 and will create a table for each of the parts in increments of 30 up three annual volumes. We will then take those fully burdened costs from each of the annual volumes created and create a graphical output, which will then show us the crossover part. So the green line is the decrease in cost in casting sand as the volume increases. The yellow line is the decrease in cost for additive as the volume increases.
Demo Results and Advantages of Additive Manufacturing
As we can see, additive does not change hugely in cost. However, with the greater machine utilization in casting sand, we get a more cost-effective output as we increase volume. As you can see from the mouse cursor, the crossover point is around 60 annual volume. So this gives us the discussion point to go with our cost team and say, “Well, if our annual volume is greater than 60, maybe we consider going back to casting. If it is less than 60, maybe additive is the best way to go.” That concludes our demo and concludes our discussion today.