September 6, 2022
What is MBD?
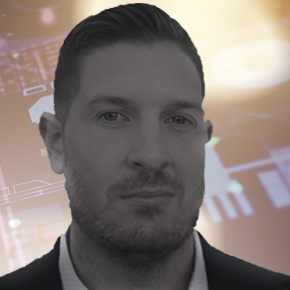
Transcript
Leah Archibald: Model-Based Definition: What is it? And how can it help you?
Another guest on this podcast, Jody Markopoulos of GE, said that manufacturers who want to reap the benefits of digital transformation need to have a single source of truth. According to today’s guest, that key source of data can come from MBD, or Model-Based Definition.
What is MBD? And how can it help you?
Christopher da Rosa has been working with 3D CAD modeling for over two decades, designing across multiple industries including industrial equipment, manufacturing, robotics, aerospace, and defense. He is passionate about empowering design engineers to create robust digital models that can be used to streamline procurement, reduce redesigns and speed time to market. Christopher da Rosa, welcome to the podcast.
Christopher Da Rosa: Thank you.
Leah Archibald: Educate us a little bit. What is model-based definition?
Christopher Da Rosa: Model-based definition is essentially the practice of leveraging the 3D CAD model as your single source of truth. It’s moving away from traditional workflows, if you will, where you had a 3D CAD model, you then created a two-dimensional detailed drawing, and then you would use that to manufacture a product or component. With MBD, it’s the practice of embedding PMI data – which is Product Manufacturing Information or your tolerances such as GD&T – all that is embedded at the 3D CAD model level.
Leah Archibald: I want to stop you, because I didn’t realize this was something that had to happen. So, the way that design engineers had been working is you would create a 3D design and then you would go back and create 2D drawings of that 3D design?
Christopher Da Rosa: Yeah, it sounds crazy, right? But that’s how we did it. And that’s how we’re still doing it across many different industries.
Leah Archibald: Tell me about your journey from taking these 3D models and rendering them as 2D drawings, and then transitioning to MBD.
Christopher Da Rosa: I was a design engineer for several years, and I don’t want to say I’m lazy, but I always like to say there’s a better way of doing things.
Leah Archibald: You’re efficient.
Christopher Da Rosa: I’m efficient. That is the greatest word for an engineer. We can model very efficiently, but then when it came time to doing detailed part drawings, that is a bottleneck because you have to go through a rigorous process to get those drawings released. Saving that time was something I always strived for as a younger engineer. Then I became a CAD manager, and that’s when I was in a position to take on the responsibility of that cultural shift to restructure our CAD practices to MBD.
The foundation starts at the CAD practice level. Next, it evolves into training. GD&T is a big part of model-based definition.
Leah Archibald: Tell me what GD&T is.
Christopher Da Rosa: GD&T is Geometric, Dimensioning and Tolerancing. It’s the application of tolerances that are defining the critical features of a component, and those critical features may drive different manufacturing processes.
Leah Archibald: I imagine that can take a big load off of sourcing’s shoulders. If they have everything in the model, they could go straight to getting a quote without having to circle back and asking design engineering about every particular tolerance.
Christopher Da Rosa: That’s very true. That goes back to my definition of the benefits that I saw: the biggest benefit was the product release cycle. The drawing release cycle phase of it is the bottleneck. And oftentimes it was sourcing waiting for us to get a part to release to allow them to have the proper data to go get their quotes for purchase. If you set the foundation with model-based definition to apply all of your PMI data – all your tolerancing – you can then create automated workflows to generate these other tools needed downstream. One of those tools is a 3D PDF. Another is a STEP file. When you’re sending a component off to a machine shop what they want is that STEP file, because what they’re going to do is plug that into a CAM system and they’re going to understand everything about that particular design, how it needs to be manufactured.
Leah Archibald: Can you talk about some of the other downstream benefits of MBD?
Christopher Da Rosa: I’d noted CAM software to support things like CNC machines. There’s also inspection equipment. CMM machines – Coordinate Measuring Machines – can automatically inspect a part in terms of quality based on the GD&T and PMI. When you think about what aPriori could do, it’s huge. Because aPriori can automate things like getting your should cost analysis, getting design for manufacturability insights, getting a report on sustainability, all automated through a workflow in your PLM. Not only are you going to be quicker to product release, but you’re going to have a more cost effective design, manufacturability friendly and sustainable product in the end.
Leah Archibald: What would you suggest for engineering teams who haven’t yet started their transition to MBD?
Christopher Da Rosa: I suggest get started. But it really does take having someone to help drive it.
It takes a leader, especially if you’re starting from scratch. There needs to be a lot of understanding of where you stand currently: looking at your practices, looking at what data attributes are needed, how do you map that to other, what I like to call, travelers. To have a true single source of truth, there’s a lot of attribute mapping because you want all the data sets to live with the CAD model and to travel with them throughout the life cycle of the product as it goes to release.
Having that experience, I do understand the challenges. So, any time I talk to anybody who’s in the middle of that challenge, I fill them with encouragement when I show what we do at aPriori. What you can really gain from it, is huge.
Leah Archibald: So, the end of the day advice is: if you haven’t started, get started, because what’s on the other side is a whole lot of automation, that leads to a whole lot of savings on cost and savings on time in the end.
Christopher Da Rosa: That’s it.
Leah Archibald: Christopher da Rosa, thank you so much.
Christopher Da Rosa: Yeah, this was fun, I appreciate it.
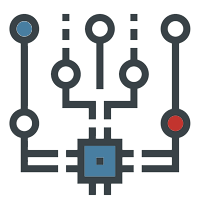