July 20, 2022
Automotive Insight: EV Supply Chain Sustainability
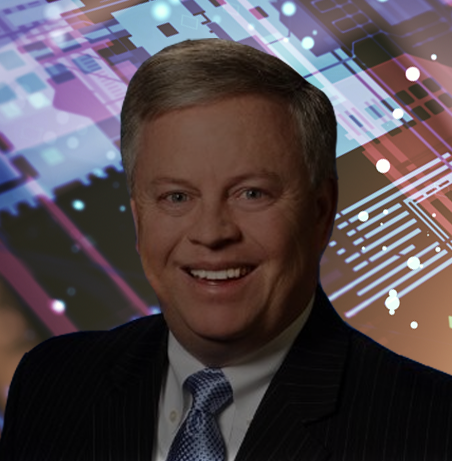
Transcript
Leah Archibald: There’s a lot of promise in the EV market right now. Consumer demand is high. National infrastructure for electric vehicles is expanding at a pace. And don’t get us started on the current price of gas and what that means for EV futures. But at the same time, several threats have gotten executives of EV manufacturers shaking all the way down to their pocketbooks – specifically supply chain shortages and fluctuating costs of raw materials. So how can EV manufacturers weather these risks and compete to win in a rapidly changing automotive industry?
Few people can speak more knowledgeably on this topic than my guest today. Craig McLeod is a veteran problem solver for the automotive industry. He spent 15 years at GM, serving as the Director of Advance Planning, and for the past 20 years, Craig McLeod has been solving tricky problems for automotive manufacturers through strategic advisory roles at Dassault and aPriori. He’s here today to give us a glimpse into the ways smart EV manufacturers are tackling the challenges of this moment and how they’re planning for the EV market of the future. Craig McLeod, welcome to the podcast.
Craig McLeod: Thank you for having me and glad to be here.
Leah Archibald: You talk to automotive manufacturers every day about the challenges they’re facing. Could you just give us a snapshot of the biggest problems they’re currently trying to solve?
Craig McLeod: For the automotive industry right now, it’s supply chain, supply chain, supply chain. There’s really a three-fold challenge in the automotive supply chain. There’s the internal problem of getting raw materials. Every supplier that I’m talking to these days is having trouble getting steel, getting polymers, getting rubber, and of course getting chips.
We also see it externally. Many of the tier one and tier two suppliers are having trouble supplying their customers with the parts they need – everything from seats, to batteries, to extruded aluminum components. There are major issues in all of these areas that especially affect the EV guys.
For EVs, obviously, the most strategic component to source are the batteries and the power train components. Many manufacturers have strategic relationships with these suppliers. But even their strategic relationships are having trouble with supply chain.
The third aspect of what we’re seeing today in automotive is that manufacturers are trying to connect their engineering groups with their sourcing strategy. Maybe they can use a different chip to supply the right kind of controls for the seats or the mirrors. Or maybe they can use a different grade of plastic material to make the same part. That collaboration between manufacturing and sourcing can a major impact on their ability to deliver the end product.
Leah Archibald: Do supply chain disruptions pose more of a challenge to EV manufacturers than to traditional automotive manufacturers?
Craig McLeod: I would say that generally speaking they do. Because the biggest players in the EV space are making many of these components themselves. It’s not like they have five battery suppliers – they have one.
Leah Archibald: They can’t shop around and if one battery supplier shuts down go choose a different one?
Craig McLeod: Exactly. They’re connected at the hip – for good or bad.
Leah Archibald: And that’s because the battery technology is much more challenging?
Craig McLeod: That’s right. They’re highly engineered parts, and they’re not something that the manufacturer can get a second or a third supplier to start making. It’s a very integral part of the car. It’s got structural demands. It’s got capacity demands. So, it becomes very strategic for the OE to continue to manage it.
Leah Archibald: Are shortages in the market hitting EV manufacturers harder because they’re not as big? Maybe they don’t have the bargaining power that traditional manufacturers have?
Craig McLeod: That’s definitely part of it. I’ll just give you an example. For a couple of our customers extruded aluminum has become a big problem. Aluminum has been tough to get as a raw material, and it’s also been difficult to find the right supplier to extrude the stuff and make the parts for our OE customers.
Leah Archibald: Do they need more extruded aluminum because it’s a lighter material?
Craig McLeod: Yes, that’s the major reason the OEs are using it – because it’s lighter, it is going to provide more miles per charge of the battery. So, they’re making this move to extruded aluminum as a major component of frame rails, battery components, and suspension components. But it’s tough because A) there are not many suppliers, and B) the material is tough to get. So, price increases are happening on a daily basis.
Leah Archibald: So, what are the most successful of your customers doing to stay ahead of the supply chain shortages?
Craig McLeod: Great question. The most successful are the ones that are incorporating their engineering groups using tools like aPriori early in the design phase to make sure that they understand how they’re going to manufacture parts, who the suppliers are going to be, and what the cost is going to be. The ones that are using their engineering teams to allow for changes on the fly are the ones that are having more success than the others.
Leah Archibald: And how do they do that, technically speaking? How do I leverage this technology to be able to plan for supply chain disruptions earlier in the engineering process?
Craig McLeod: The big part of that is being able to use tools like aPriori to collaborate between sourcing and engineering. So the sourcing guy can very quickly say: Hey, what if we change this material? Or: What if I’m able to bring this newer supplier on board?
All those different options can be evaluated directly in aPriori, so engineering and sourcing can make sure that a new material or a new supplier can be swapped out in a much faster manner.
Tools like aPriori help drive the collaboration, drive the knowledge, and drive the expertise right into the design of the product so that teams can make strategic changes much more quickly than they would otherwise.
Leah Archibald: Give me a one-minute explanation of how the aPriori tool helps folks do this better than the old way of doing this – which might be sourcing just emailing the design team?
Craig McLeod: Let’s say if you’re the sourcing person and I’m the engineer. We’re in different parts of the country or even the globe, and we need to be able to collaborate and understand exactly what our options are. You can do all of that directly in aPriori at the same time. So if you say: Hey, I want to consider changing this material, I can look at the change in that material immediately and say: Okay, that’s going to pass FEA, that’s going to pass your requirements from a pricing standpoint, and it’s going to pass my requirements from a product engineering standpoint.
To be able to make that evaluation very quickly, on time, and to be able to collaborate in a much more rapid basis by looking at the same models – that’s what aPriori does for you. When you want to make a change, the first thing I do is change that material in the CAD model. With aPriori’s ability to directly read the CAD model, we can instantly see what implications changes to that model are going to have on manufacturing and sourcing. Maybe that new material is going to make the cycle time longer – like from 40 seconds to 50 seconds. With my digital factory models, I can understand that means I’ve got to run the equipment roughly 25% more to make the same number of parts. Do I have the capacity to do that? Does that mean I’ve got to start running it on the weekends? Does it mean three shifts a day? I can do that evaluation very quickly in aPriori’s digital factory. So I am able to make that decision for you very quickly to say: Yes, let’s go change this material – if it’s abundant and we can get it, and it’s going to cost about the same, let’s do it.
Leah Archibald: Are there other opportunities for EV manufacturers that maybe elude the rest of the market?
Craig McLeod: Great question. I would say the biggest opportunity is this whole idea of getting engineering involved earlier, to really get the engineering and sourcing and manufacturing folks all on the same page at the same time so that they can quickly evaluate a new design and make a decision on it. When you have tools like aPriori, you can do that in less than a minute.
Being able to show the manufacturing person what the cycle time is going to be, and being able to show the sourcing person what the difference is between buying this in Mexico versus California versus Michigan, and being able to show them all that information in a minute or less – the teams that are winning are the ones that are quickly collaborating to move forward on what it’s going to take to build that new vehicle.
I’ll give you an example. There’s an EV manufacturer that’s got an office in Michigan, and then they’ve got a manufacturing facility in another mid-west state. They recently had an issue with getting supply of a particular plastic material. They were able to get the cost engineer who was using aPriori in a collaborative session with the manufacturing engineer and the buyer. Together they evaluated a replacement material. The material was a little bit thicker, so it took a little bit longer to process. This created a longer cycle time – from like 35 seconds to 40 seconds. They okayed that with the supplier. They were also able to see that the change in material was not going to affect the design of the part – it didn’t change fit, form or function. With those insights from aPriori, they were able to make a decision and start replacing the old material within 24 hours to the plant.
Leah Archibald: Wow. Talk about quick turnaround time.
Craig McLeod: Exactly. It was a matter of them getting in a collaborative session, making the changes in aPriori, running the new part in aPriori, getting the verification on the cycle time, and then moving forward. And that was just one quick example. It’s happening every day.
Leah Archibald: So, we’ve got to stop thinking about electric vehicles as having less get-up-and-go than gas-powered vehicles. Because I hear a log of get-up-and-go in this example that you just told me!
Craig McLeod: Yeah, they’re 0-60 in three seconds. It’s pretty cool.
Leah Archibald: Craig McLeod, this has been a real pleasure. Thank you for joining me on the podcast today.
Craig McLeod: Thank you very much, Leah, it’s been my pleasure and I look forward to talking again soon.
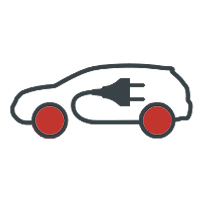