MIC 2023 Takeaways: The Rise of Digital Twin Software
Key Takeaways:
- End-to-end digital twin software is empowering manufacturing leaders to transform their operations
- Manufacturers are using digital transformation to increase sustainability and resilience while addressing inflationary pressures
The Full Article:
Digital transformation. What does it mean and how can it impact your organization? In broad terms, it’s a strategy to apply digital technologies such as automation, simulation, and collaboration to streamline business processes and innovate quickly and confidently. Successful digital transformation relies on integration with existing systems and using the connected enterprise to apply real-world data analysis to navigate dynamic market changes successfully.
In her opening remarks at our recent Manufacturing Insights Conference (MIC), “Digital Twins Reimagined”, aPriori CEO and President Stephanie Feraday spoke about challenges that companies are facing in getting value from their digitalization investments. (Watch the full digital twins presentation here.) To illustrate this point, Ms. Feraday cited a Harvard Business Review article that noted, “While 89% of large companies globally have a digital and AI transformation underway, they have only captured 31% of the expected revenue lift and 25% of expected cost savings from the effort.”
So how can manufacturers implement and advance their digital transformation initiatives to generate short- and long-term returns? To answer this complex question, aPriori assembled manufacturing executives, geopolitical strategists, and members of our team at our annual MIC conference. Based on the variety of perspectives shared at MIC, we’ve highlighted five takeaways from our conference below:
Takeaway #1: Improving Efficiency and Productivity is Key to Success
Risks including inflation, geopolitical events, supply chain disruptions, and labor shortages are influencing business transformation along with disruptive drivers like sustainability. The enabling driver in this transformation is advanced simulation including digital twin technology (a virtual representation of a product design, manufacturing process, and factory). To achieve efficiency and productivity as well as mitigate risk, digital twin technology can:
- Fast-track product development by leveraging design guidance that reinforces best practices
- Automate design analysis processes to ensure cost and manufacturability impact at scale
- Utilize real-time data visibility with cloud architectures to improve accessibility and greater collaboration across the organization and product development teams
When all three digital twins are utilized, they create a framework that fosters greater communication and information flow between the digital and physical worlds. It is known as the digital thread.
Takeaway #2: Digital Transformation Can Influence Corporate Strategy
Digital technologies, and the transformation opportunities they offer, can wield profound influence on an organization’s leadership by:
- Delivering accurate and detailed cost vs. CO2e analysis
- Streamlining operations and boosting workflow productivity
- Enhancing collaborations across product development teams
- Mitigating sourcing risks and improving supply chain management
- Developing higher value products more sustainably and profitably
- Innovating faster and accelerating time to market
Digital technologies can improve essential buy-in at the top; thereby improving critical functions across the organization. Product development teams can simulate the entire product design and manufacturing process in a virtual environment (3D model / digital twins). With aPriori, for example, teams get actionable insights to ensure they are reaching their cost, time to market, and other key performance indicators (KPIs).
Takeaway #3: Digital Twin Technology Accelerates Procurement Transformation to Unlock Value
Building a resilient and agile supply chain remains a priority. Digital twin software can:
- More efficiently navigate the supply chain
- Mitigate geopolitical risks that can bottleneck it
- Provide access to crucial supply chain data from technologies, improving supplier relationships and negotiations
- Reduce quoting times and achieve significant cost savings
Equally important, digital twin software enables a more proactive approach to supply chain management early in the product development lifecycle and cross-functionally.
Takeaway #4: Sustainability is Quickly Changing the Digital Landscape
As we move toward global ESG standards, there are steps manufacturers can take to meet sustainability initiatives. Digital twin software can support this effort to address increasing product competitiveness and fast-changing customer behaviors and preferences. Leverage digital twin software to:
- Conduct “shift left” evaluations of cost and carbon. Such evaluations are conducted in the beginning stages of product development and along a left-to-right timeline. As a result, it enables the most significant reduction opportunities early in product development.
- Leverage and combine a should cost methodology for carbon. “Should carbon” allows for a faster, more precise CO2e evaluation, while enabling trade-off analyses to balance the business requirements with sustainability.
- Design to ensure sustainable and profitable manufacturing. It can be a complex process since it can be both intuitive AND counter-intuitive. Data is helpful, but collaboration is essential. Digital twins can bridge both.
- Gain insights from a wide range of stakeholders to fast-track the decision-making process and time to market.
Transparency is critical when it comes to carbon data. Global green guides/green claims directives as well as auditability help to prevent greenwashing. Digital twin software solutions like aPriori automatically explain the logic behind that data and can help guide and support product line goals.
Takeaway #5: Addressing Labor Shortages Requires Complementary Recruitment Strategies
Speed is essential in addressing engineering skills gaps effectively. Digital transformation can facilitate this effort with enhanced collaboration and optimization of product/price performance during the design cycle. Digital twin software can:
- Ramp up skills to meet the increased industrial manufacturing demands via automated methods of education and training
- Utilize automation and other digital technologies to compensate for labor shortfalls and reduce downtimes. Digital twin software can reduce supplier quoting times and enable fewer workers to oversee more rudimentary functions
- Improve onboarding efforts through cloud collaboration that produces and stores more reliable institutional knowledge
Digital transformation solutions allow manufacturers to scale faster and more effectively to meet ever-increasing demands. The workforce is a critical component in this effort.
Optimize The Product Lifecycle With Digital Twin Software
To be competitive, agile, and grow, manufacturers must do more than optimize their product development. They must move from product optimization to true business transformation to make informed decisions in real time to gain a competitive advantage.
Cloud-based digitalization strategies can have a transformative effect on business. Deloitte reports that companies that communicated their digital strategies in their financial disclosures saw a significant positive impact on their valuations.
The aPriori Manufacturing Insights Platform helps manufacturers meet today’s challenges by connecting teams and their product data – including design and cost engineering departments, sourcing and procurement teams, sustainability groups, and suppliers.
Can Digital Transformation Have A True Impact?
See Why Frost & Sullivan Named Us The Leading Digital Manufacturing Solution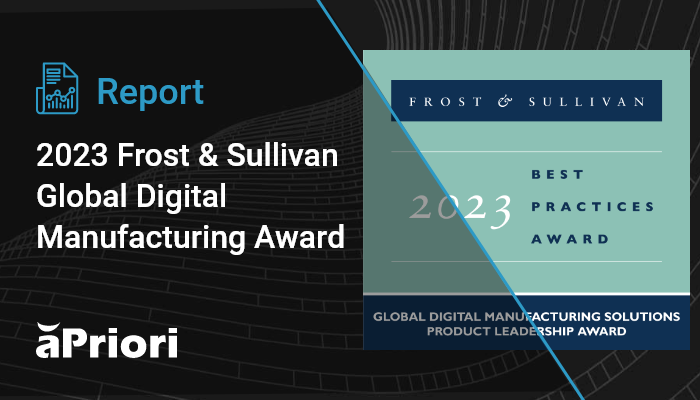