5 Ways a Top Medical Device Company Optimizes PCB Electronics Manufacturing with aPriori
Key Takeaways:
- Advancements in cost estimation empower a top medical device company to secure greater savings in PCB electronics manufacturing
- aPriori’s game-changing manufacturing insights platform helps the company streamline electronics manufacturing, improve business decisions, and cut significant costs
The Full Article:
For many global medical device manufacturers, optimizing printed circuit board (PCB) electronics manufacturing is essential for launching cost-effective, high-quality new products on time. As electronic components become increasingly complex, organizations must embrace advanced manufacturing costing approaches to mitigate expense pressures, accelerate time to market, and drive profitability.
In our recent case study, a leading multi-billion global medical device manufacturer based in New Jersey addressed these challenges by adopting aPriori’s automation-driven, precise cost estimates. Explore the five ways this organization used aPriori to streamline PCB electronics manufacturing, enhance business decisions, and achieve an impressive 25x return on investment (ROI).
Company Overview and Major Challenges
Established in 1897, this U.S.-based company is a global leader in the supply chain for medical device and equipment manufacturing. With more than 70,000 employees worldwide, the company manages an extensive product portfolio that includes many complex devices with electronics, including flow cytometry systems that require PCB fabrication.
Before implementing aPriori, the company encountered various challenges that hindered its ability to “right-size” its costs and value proposition. These obstacles included the following:
- A lack of detailed cost breakdowns to inform supplier negotiations and capture substantial savings
- Persistent cost pressures and inconsistent early product development estimates for several complex designs
- Limited cost transparency when outsourcing printed circuit board assembly (PCBA) and production operations
- In-house skills and knowledge gaps in PCB manufacturing, resulting in an overreliance on external circuit board and wire harness fabrication
To address these problems, the medical device manufacturer implemented aPriori’s precise cost estimation capabilities to maximize expense savings effectively. Here are five ways the company capitalized on the power of aPriori:
- Perform Should Cost Analysis for Precise and Granular Estimates
- Use Matrix Costing for Concurrent Evaluation of Electronic Products’ Costs
- Leverage Detailed Cost Data for Effective Fact-Based Supplier Negotiations
- Address the Skills and Knowledge Gap Challenge with Digital Technology
- Eliminate Silos and Boost Cross-Functional Collaboration in Cost Management
1) Perform Should Cost Analysis for Precise and Granular Estimates
The medical device manufacturing company leveraged aPriori’s automated should cost analysis to calculate and break down the various expenses associated with PCB production. These expenses include critical factors such as raw materials, labor rates, overheads, facilities/tooling, and electronics manufacturing processes.
Moreover, the manufacturer’s utilization of aPriori’s should cost estimates provided its value engineering team with the ability to:
- Directly evaluate 3D computer-aided design (CAD) files to generate a digital twin of the complex part or the PCB design being modeled, considering factors such as product geometry
- Determine the “true” and actual production costs of intricate PCB components
- Uncover more cost-saving opportunities that can be realized during data-driven supplier negotiations, ensuring a fair price on electronics manufacturing services (EMS)
2) Use Matrix Costing for Concurrent Evaluation of Electronic Products’ Costs
The company’s value engineers employed aPriori’s matrix costing module to configure and simulate multiple manufacturing scenarios within a single workflow. They entered key production details, including locations, annual volumes (high/low), and batch sizes, to automatically run these simulations.
With aPriori’s simulation-driven module, value engineers generated detailed cost reports and compared simulations, selecting the scenario with the lowest fully burdened cost. Additionally, matrix costing enabled them to inform make vs. buy decisions and improve the management of mature product lines.
3) Leverage Detailed Cost Data for Effective Fact-Based Supplier Negotiations
Actionable and precise fact-based data is an output of should cost analysis. These data-driven insights enabled the medical equipment manufacturer to support its case for cost savings during collaborative supplier negotiations. Consequently, the organization was able to confidently right-size costs, ensuring fair pricing for the components used in its complex product designs and associated production processes.
4) Address the Skills and Knowledge Gap Challenge with Digital Technology
aPriori not only elevated value engineers’ cost optimization success but also provided them with actionable design for manufacturability (DFM) insights early in product development. This enabled the company to make cost-effective design decisions from the outset, eliminating downstream issues in product development without needing to hire additional PCB specialists.
With aPriori, even the most novice in-house engineer can become an expert in product costing and design through actionable, accurate, real-time manufacturing insights.
5) Eliminate Silos and Boost Cross-Functional Collaboration in Cost Management
aPriori broke down silos across the product lifecycle, bridging the gap between the manufacturing company’s design, cost/value engineering, and sourcing and procurement teams. Consequently, the unified team could access and share critical manufacturing data within a single platform, standardize costing approaches, and enable rapid decision-making.
Attaining a 25x Yearly Return on Its aPriori Investment
The medical equipment manufacturer realized an annual ROI of 25 times its investment in aPriori. Further, the company found that this ROI remained consistent across its various product categories and spending levels. aPriori proved to be a game-changer for the organization, enabling it to maximize savings, improve ROI, and foster continuous innovation in the medical technology manufacturing sector.
Read our latest in-depth case study below to learn more about the company’s electronics manufacturing success with aPriori.
Leading Medical Manufacturer Achieves 25x ROI with aPriori's PCB Cost Optimization
Get all the details about how a top medical technology manufacturer boosts cost efficiency and achieves 25x ROI on its aPriori investment.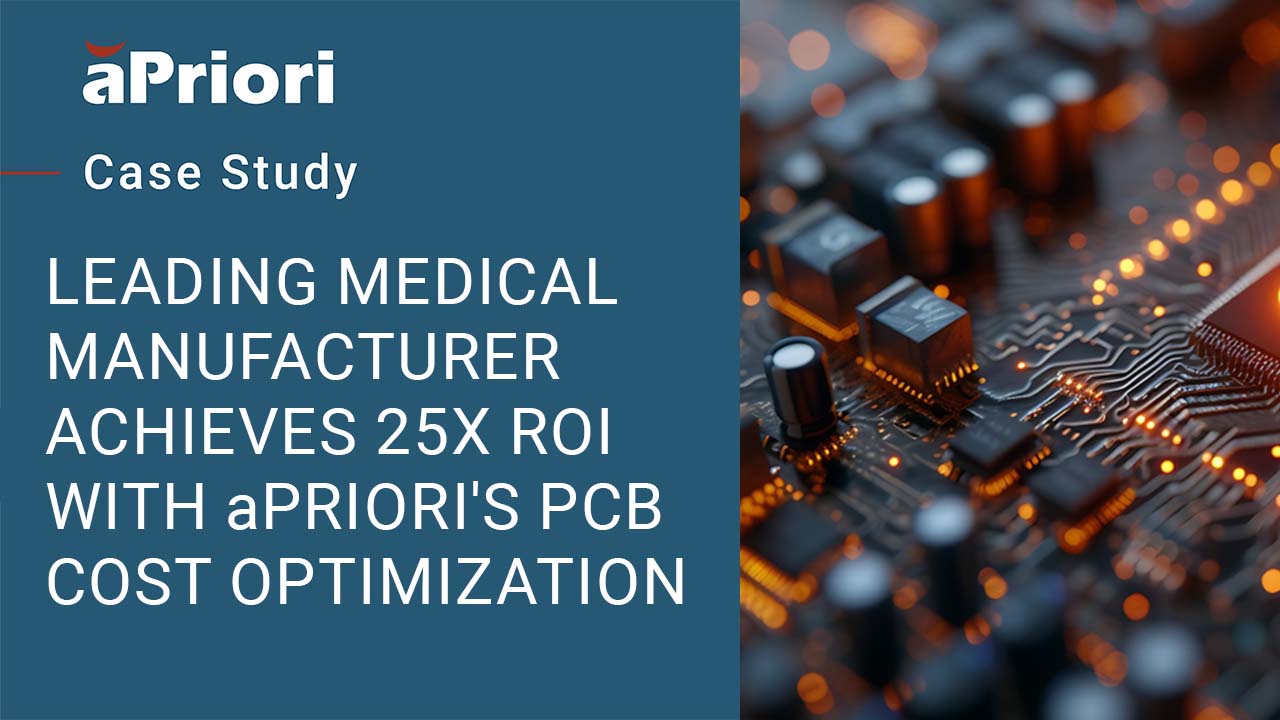