August 24, 2022
Manufacturing Tech that Wins No Matter What
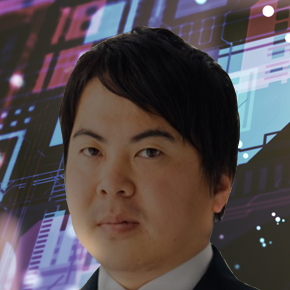
Transcript
Leah Archibald: What if your choice of tech investment didn’t have to be an either-or decision? With the current range of solutions available to manufacturers today, an executive no longer has to choose between one tech ecosystem over another. Today, aPriori can work with Siemens and both can integrate with native ERP, PLM or BI systems to round out a manufacturer’s insight.
My guest today has insider knowledge on how this works in the world’s most mature manufacturing market. Masatoshi Fukatsu worked for Siemens in Japan from 2014 to 2022. There he sold and configured PLM systems for automotive OEMs, second tier automotive suppliers and heavy equipment manufacturers. Before Siemens, Masatoshi spent a decade managing costs in the Japanese automotive industry. His work benchmarking global cost data closed the gap between budget projections and sourcing costs at Nissan.
He’s here today to talk about technology investments that deliver ROI, no matter what. Masatoshi Fukatsu welcome to the podcast.
Masatoshi Fukatsu: Thank you inviting me.
Leah Archibald: How do you see manufacturers today making a decision of what technology solution to implement?
Masatoshi Fukatsu: For manufacturing companies, their technology solution investment is getting changed. Previously they invested in engineering chain management or PLM solutions. For supply chain management, they invested in ERP systems. But recently – for the last five or seven years – I have seen them invest based on industry 4.0 concepts, or data set realization. So, they invest now to bring the whole big manufacturing process into their development.
Leah Archibald: Tell me more about what you mean by industry 4.0. What are companies trying to do when they’re focusing on industry 4.0? And how does that change the solutions they’re choosing to invest in?
Masatoshi Fukatsu: Previously companies invested to improve their enterprise data. The investment was from an IT perspective. With industry 4.0, now companies are investing to transform themselves – not only to manage data – but to evolve business processes to create more innovative products.
Leah Archibald: What you’re saying is that instead of focusing on one area that manufacturers want to use a data solution for – say PLM – now the manufacturer is looking to manage their process end-to-end, having one data set that helps them gain insights all the way through the life cycle management.
Now let’s talk about the aPriori solution. What is the value proposition of aPriori versus its competitors?
Masatoshi Fukatsu: It’s no longer sufficient to focus on only the one area, for example, costing. Because to optimize the cost, the customer now finds they need to discuss alternative materials and assemblies – and that is a design problem. This is only possible in the aPriori solution, which provides manufacturing insight as well as sustainability and costing. A customer can apply this information from one database to an end-to-end development process. This multi-department solution is only possible through aPriori.
I had eight years of experience as a cost engineer for an automotive supplier, before I moved to an Auto OEM where I also did a cost engineering job. Our problem was communicating with different teams to get to an estimate. We would always start by receiving a drawing or some specification information from the engineer. We would start the discussion with the engineer, and sometimes start a rough estimation. After that, I would discuss with the purchasing department to evaluate supplier cost. After that, the problem always was how to go back and collaborate with the engineering team. Engineering didn’t want to work on cost because they had a lot of other tasks and responsibilities. They don’t want estimate, because it’s a very tough discussion that requires a lot of collaboration with other departments. It was hard for my team to go back and forth between purchasing and engineering to get to an accurate cost. aPriori can support this process because engineering can easily estimate the cost with limited input and no outside discussion. aPriori provides detailed cost information by extracting the geometric cost drivers from the CAD model. That makes it very easy to estimate the cost with accuracy.
Leah Archibald: When you’re trying to explain this to new engineering teams, how do you demonstrate the ROI they’re going to get from implementing a solution?
Masatoshi Fukatsu: To focus on ROI, we have to break down what the ROI consists of. There is the cost reduction that they can achieve from each part or a component. There is also the workload savings – reduction in workload from the current business process to the new business process with the solution. For this you can measure how many engineering change order they can reduce with the solution. We often see that with the solution yielding a 20% cost reduction, 40% of cycle times are shortened.
Leah Archibald: So that’s the cost area of it. You also said that what you like about the aPriori solution is that it’s not just costing – it includes sustainability. Do you see manufacturers specifically in Japan looking towards sustainability?
Masatoshi Fukatsu: In Japan, many companies and also the government are reaching towards a 2050 target of achieving Carbon neutral manufacturing. To achieve carbon neutral, you have to look at how much electricity each department is using. You have to look at the carbon footprint of new products. aPriori can do both of these.
Previously no one knew the carbon emissions for their parts and products. Now they have to start CO2 calculations. aPriori can provide the baseline calculation of CO2 emissions so that companies can start the discussion on future sustainability. This will be a powerful tool for all manufacturing companies in Japan moving forward.
Leah Archibald: Let’s say a manufacturing company purchases the aPriori system because they want to start tracking their CO2 emissions to get to zero net emissions by 2050. How can the aPriori solution integrate with other solutions that a company may already have on hand? Let’s say they have a Siemens CAD system or some other PLM solution in place. How do they work together?
Masatoshi Fukatsu: That is a benefit of aPriori – it integrates with other systems. It can store and work off of the same data. For example, a PLM system or supply chain management system is often called the backbone of a company. In that case, all engineering data is stored in that system. The fact that aPriori works off of data stored in this system is a huge benefit for the customers. For example, when an engineer changes their design and updates that data in the PLM system, aPriori is executing the cost models and computing the manufacturability of that part, and then emailing that information back to the engineers or managers.
Leah Archibald: I bet it’s huge to say: Look, you don’t have to change your whole PLM. You don’t have to change the system everyone’s familiar with. We’re just going to have aPriori running in the background and then you’ll get an alert when a cost of a particular design is too high or when the carbon footprint of a particular new product is going to need to change.
Masatoshi Fukatsu: Yes, currently companies are looking not for a standalone solution, but for an integrated solution across their departments. They are very conservative, so they tend to spend a lot of money to maintain their legacy tools. aPriori gives them a lot of opportunity to accelerate their activity and to increase efficiency. This is what I’m trying to bring to Japan in the future.
Leah Archibald: Masatoshi Fujitsu, thank you so much for talking to me on the podcast today.
Masatoshi Fukatsu: Thanks so much.
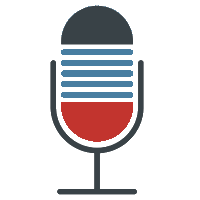