Video
Sustainable Design: Does It Have to be More Expensive?
Did you know that 80% of a product’s environmental impact is determined by its earliest product design? That means if you create a sustainable design from the start, you can solve your sustainability goals, all while meeting product cost targets. All this is possible (and easy) with aPriori’s sustainable digital factories. aPriori’s sustainability features provide actionable insights on sustainable product design, manufacturing, and sourcing from when you import your CAD model to when your part is manufactured.
In this session, we will demonstrate how to design sustainable, high-performance products without increasing costs.
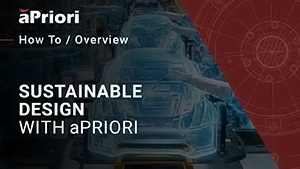
Transcript
Gibson Peters: Hello, my name is Gibson Peters, and today we’re gonna talk about sustainable design, and does it have to be more expensive? I’m the product manager here at aPriori for Sustainability. So really excited to talk to you about what we’re doing with sustainability and how we’re designing it through the impact and help you make actionable decisions when it comes to sustainability. So, quick agenda here, I’ll go over what we’re calling Should-Carbon, talk about how we model cost and carbon together, and what are the benefits of using those two metrics side by side. Then finally, go through three examples of balancing cost and carbon and summarizing that up at the end.
aPriori Enables Action, Not Just Measurement for Product Design Processes
So first, I think, as cost professionals here, we look at a lot of 80% of the cost impact of a product is determined in its design phase and really see that very similar, 80% of a product’s environmental impact is determined early in that design cycle. So how can we really start to address it when it comes to sustainability? When we look at sustainability in aPriori, we’re really leveraging what we already do. This might be very familiar to many of you, but we take that CAD drawing, we extract the geometry from that CAD drawing. We select the digital factory. We do automate analysis, we insight review, and then help you take action to create that best-in-class product. And with sustainability, we’re not doing anything new. We’re taking cost and manufacturability that we’ve been doing for 20-plus years, and then we’re adding sustainability and carbon on top of our existing platform.
And the whole goal is to help you enable action and not just measurement. We’ve really targeted, identified three different personas very similar to our existing personas when we look at what different customers want to do when it comes to understanding carbon in their product. We start with sustainable sourcing. And we look at this as more towards the design cycle later in that design cycle towards final sourcing. Minimal design changes, supplier carbon impacts of carbon footprint, supplier selection, material sourcing, make versus buy decisions, and supply chain impact. And the other thing that we find more and more is helping customers understand their supplier’s CO2 footprint when the suppliers don’t have that handy or not have that information available. So really helping them, if we have that CAD drawing, we can help them start the discussion with the supplier about how much carbon is in their existing product.
And as we move a little bit further into the design cycle, looking at sustainable manufacturing, some changes to existing parts, we’re looking at creating that baseline cost versus carbon trade-offs, identify low carbon process routing, and identifying outliers so we can really understand where the carbon is coming from in that product. And then finally, we’ll look at an example for sustainable design. It’s a new part, kind of blue sky looking at cost versus carbon trade-offs, trade-offs between shape, weight, and materials. Maximizing product circularity through the design process and identify reuse opportunities early in the design cycle.
Implementing aPriori for Product Cost and Carbon Savings
So as we looked at and mentioned the three different examples targeting sustainable sourcing, How do I make sourcing cost versus carbon trade-offs? We’re looking at sustainable cost engineering, how cycle time drives cost, and carbon savings. And finally, looking at sustainable design, how manufacturing processes and material can really lean to cost and carbon savings together. When we look at cost and carbon through our platform, we see that there’s really four main levers that we can pull. One is shape and material, shape and geometry. The second is material, followed by manufacturing process. And finally, location and energy mix used to make these products. And the other thing we find is these are all very dependent on each other. So if I change the geometry and shape, I can change my material, then I can change my manufacturing process. So really helping you understand how these different levers are pulled and can be managed in a way to reduce cost and carbon along the way.
And not only is there these levers exist, but they also change as we go through the design cycle. So early in that design cycle, you can change your geometry very easily, but later in that final sourcing, it’s really hard or very costly to change that design. So the size of those levers really changes throughout this design cycle. And the cost to make those changes is pretty drastic from early in the design cycle to later in as we get to final sourcing. What we do today, and to refresh everyone’s memory about should costing and why it lends itself so well to carbon or should-carbon. Today we’re taking a looking at material, tooling/setup, manufacturing process, assembly, labor to create a should cost, which is not always exactly what quota costs are, but very similar to what quota costs are and how do we … the way we’ve been estimating that really lends itself to calculating carbon for our customers.
When we look at should-carbon, we’re looking at many of the same variables. We’re looking at material focused initially and the manufacturing process within the material. We are looking at rough mass, regrind/remelt, waste material, and material CO2 factor to get that material carbon. And so we already understand rough mass, regrind, and waste material really just adding that final variable of material CO2. And then similar, when we’re looking at manufacturing process, we already have a really great understanding of cycle time, energy use. And then we’re just layering in the electricity carbon mix factor to help understand the process carbon. We add those two together to give you the total CO2 or total carbon of the individual part.
And what really makes us unique is we’re this bottom-up approach when it comes to carbon analysis. You can see here on the right we’ve got the power, time, and injection molding. We know how much time the injection process uses and how much energy’s used, followed by the cooling time and then the injection time. So we have a really granular understanding of the energy that goes into making an individual part. So this really feeds into our unparalleled understanding of the manufacturing process, something we’ve been doing for the past 20 years. The other thing that really makes us unique is the way we are able to calibrate and configure our factories and give you price and carbon trade-offs at the same time. Well, we’ve been giving you forever is costing and cost … price and cost information. But to have that side by side with cost to help you make those trade-offs in real time, I think, is a really innovative way to help you iterate and find ways to iterate towards products that both help you reduce costs but also carbon as well.
How Customers Use aPriori to Improve Design Strategies and Address Climate Change
Some of the ways our customers are using aPriori today to reduce carbon, we’ve got a global truck manufacturer helping them create a baseline for existing products. I think everyone is starting here to create. How do we better create that baseline for our customers and automate a lot of that? And then they’re looking at the environmental impacts of replacing the metal components with plastic, which is a great way to reduce carbon. Then we’re looking at automating the creation of CO2 baselining for existing products for another automotive supplier, but the equipment, the design teams to give them insight to designing and thinking about how do we design products for circularity, simple things to start, like, Is this plastic I’m using recyclable or not? And then finally, we have a number of customers that are using aPriori to work with their customers to identify the environmental benefits or the carbon benefits of using recycled products or lower carbon products in their design cycle and how it actually would work that lower carbon product in their existing products.
And when we look at our customers, there’s really a range of maturity out there when it comes to sustainability. I would say the vast 90 to 95% of the customers I’ve talked to thus far have been really starting to wrap their heads around what sustainability and carbon mean and how they’re gonna go about calculating it. So everybody out there is looking to create that baseline, and along with creating that baseline, is gathering the information from their suppliers, which we can really help facilitate with our existing platform. And then we start to move down sustainable sourcing. How do I make this existing product more sustainable with minimal design changes? Is there a better supply or a better routing? Or what are renewable energy and energy efficiency? How does that impact the CO2 of this individual product? As we look further up that design cycle, we’re looking at making existing products better. Can we tweak things and have the same functionality? And then, finally, I think this is where everybody wants to go in the future, but helping design products with sustainability integrated. So starting with sustainability in mind, really, really in that design process.
Focus on Material, Location, and Energy Consumption for Sustainable Sourcing
And we’re gonna go through those different examples. For this first example, we’re gonna start with an example of final sourcing. So a little bit later in this design cycle… Here are the four levers we talked about before. For this example, we’re gonna focus on material and location and energy mix. So we look at our side door panel here. We’re gonna look at it across four different digital factories, China, Eastern, Western Europe, and the United States. So right now, we’re manufacturing this product in China for a little under $18, and it has 9.4 kg of CO2, but evenly split for this product between processed CO2 and material CO2. And when we look out, we can see China has a lot of carbon and a lot of coal in its electricity mix. So if we can move outside of China, maybe to Western Europe or the United States, we can reduce our process CO2 quite significantly.
But what are those cost trade-offs? So we’ll look at that in a little bit more detail. And now, when we look at the different regions, we can see this is the energy mix in China, Eastern Europe, the United States, and Western Europe. China has the highest, where about 75% of the electricity generated is from coal. Eastern Europe has the next, where about 50% of its electricity is generated from coal. United States, about 25, and Western Europe, about 12%. So really, those are the main things driving that process CO2 and something you can modify to change where you’re making this product without really doing many modifications to the product. So we run this product through aPriori. We can look at the cost versus carbon by location. We can see China, where we’re currently manufacturing. It is under $18 and 9.4 kg of CO2.
Eastern Europe has less carbon and less price, surprisingly. So we wanna look at that in more detail. And now, we look at the United States, which has the highest price and second lowest CO2. And Western Europe has the lowest CO2 and second highest price. So I think one of the things people struggle with is, How do I start looking at comparing these different scenarios side by side? And what people are increasingly doing, and I think is really exciting, is applying a cost to carbon. And the hard part is really coming up with that cost of carbon. But I’ll show you just how you can use the cost of carbon to make some of these analyses and trade-offs much easier. First, just to introduce the topic a little bit about putting a price on carbon. One, it’s fairly simple. The math is really simple and straightforward. It’s a dollar per ton of CO2. You can monetize the carbon risk mitigation and risk reduction, mitigation and risks, and prepare for a variety of carbon regulations. If it’s a carbon tax, if it’s a carbon trade, they all fit into this paradigm of a dollar per carbon, it allows companies to evaluate trade-offs, and then finally, the price can vary by location. We can have a different price in India versus Canada versus Norway. And really looking at those trade-offs side by side.
This is just to give you a little background. I think more and more people are starting to look at using carbon pricing. According to the Carbon Disclosure Project or CDP, about 1,400 multinational companies are factoring carbon into their business plan. And Mckinsey estimates about a quarter of companies indicated they’re using internal carbon charge or carbon price, and an additional 22% plan to do so in the next two years. And this is based on 2019 data. So you can see there’s a range of companies looking at the price of carbon. And really, there’s a wide range of values that folks have come up with. This data is a little bit old, from 2019, but you can see some companies are at $100 per ton of CO2, and other companies are all the way down in the single digits.
And there’s no right or wrong answer. And I think once you’re able to look at these trade-offs and use the price of carbon, you can really see how that impacts different decisions. There’s no formal standards. A lot of these are internal. You can see Volvo has stated they have an internal price of carbon of 1,000 SEK, which is about exchange rate has fluctuated a fair bit, but roughly about $100 a ton. Volkswagen has a current price in 2023 of 60 euros, but they’re looking at increasing that over the next three years to about 100 euros per ton. And then Canada has regulation that starts at $65 a ton and is looking to ramp up to $170 a ton. So just to lay the groundwork and help people understand there are ranges, there’s no right or wrong answers, but I would say the trend is in the future that people expect the carbon price to increase, not decrease in the future.
So if we take about $100 a ton, which is currently on the high side, and apply it to the carbon, we’ve calculated for different suppliers, China, that 9.4 kg of CO2 translates to about $0.94 or 94 cents of additional cost. Eastern Europe’s 82 cents, United States’ 71 cents, and China’s 50. So now not only do we have a carbon amount, we have a price where we can start comparing these different scenarios to each other. And when we layer these carbon prices on top of the cost to manufacture the part, you can really start making some very easy comparisons. So it looks like China is higher than Eastern Europe and the United States, and even though they have a lower CO2, it didn’t overcome the price. The lower price is associated with manufacturing in Eastern Europe and the same in Western Europe.
So really looking at the cost and applying this cost of carbon, Eastern Europe is the low-cost supplier. And then when as we were talking to our supplier in Canada, they were like, wait, wait, I didn’t realize carbon was that important to you. Let me go out and let me see if there’s something I can do. So they went out, and they said, okay, well, I can increase my price 5%, so I go up to $18.77, and that allowed me to draw up my CO2 as 6x. So from going from 9.4 to 1.5 kg per part. Do I keep my business with you? And you’re like, Well, let me see. Let me run the numbers and see what that means. And when I run the numbers, I can see the green China option. We’re calling it at $100 a ton. We can see it didn’t really impact or make a substantial difference between our China without the green or low carbon initiative versus the option where we had the standard with high coal for electricity and the option where we had the low or green China option.
With that reduced reduction in CO2, we can see Eastern Europe came out ahead even applying that price and seeing that big reduction in carbon from our China suppliers. So even though our China suppliers wanted to keep us and they worked really hard to reduce their CO2, it wasn’t enough to overcome the price at $100 a ton for Eastern Europe. Now, in the future, this is the nice thing about putting a price on carbon: these things are flexible. So, it if went up to $200 or $500 a ton, we can run this analysis again really easily and see if that’s still the right decision in the future. So that’s just a way to look at different suppliers but also, as you think about making some of these decisions, how you could use the price of carbon. And that’s something we’re working on incorporating into our platform.
Sustainable Cost Engineering for Eco-Friendly Product Design Operations
So looking at sustainable cost engineering, our next example, we have the same levers. We look at geometry and material this time as our primary levers. In this design process, we’re really focused kind of in that middle part. We can make some tweaks and changes, but we’re not fully redesigning this part. So it gives us some freedom, but it’s not like we have the ability to completely redesign the part. So we have this example part, one example part, three options, or three iterations. We’re going to start making this part in the United States and using ABS. So to create that baseline, we go through and create the baseline. We can see our part cost is just under $4. We have cycle time and then our energy used, material, and process. Again, it gives us a really good baseline for what is going into that part. We do our DFM analysis, we find that there is a really high cooling time associated with this part. It’s really thick in the midsection, and we know cooling time equals cycle time equals cost equals process time. So anything I can do to reduce my cooling time or reduce my cycle time will really have a significant benefit when it comes to looking at cost and process carbon.
So I do a little analysis. I can see the cooling times are high because I have more material in this midsection here and then these ribs. So how can I go back and design this part to reduce that cooling time? So I go back. I look at reducing that cooling time in the midsection in the rib. I make some design modifications. I add some lift bundles, which increases our tooling investment associated with this part, but it reduces my cooling time and carbon emissions and cost as well. So let’s see how that compares together. So we can see our cycle time went down 41%, which is great by adding those lifters. And not only did our cycle time went down, but our part cost and total carbon went down almost 30% as well. So this is a great example of driving down cycle time and its impact on cost and carbon together. But I still think there’s more I can do to reduce the CO2 and cost in this part. So let’s go back, and we’ll look at a split rib design that we were thinking about. So, the good thing is it reduces our investment from the last iteration because we no longer are required to lift bundles, and it’s really focused on reducing cooling time and carbon emissions.
So the con is from the original design it still has a slightly larger investment, but let’s see what it does with our overall cost. So cycle time is great. We’re able to reduce that by another 64%. The part cost went down 53%, and then our total carbon went down 40%. Just another example of how we can drive down cycle time using design to drive down cost and carbon at the same time. But are there other things we can do? Well, one of the things we can do still is look at material. So we want to look at PET with 30% glass. It’s a little bit more expensive material, but I can see my cooling time change is 82.5%. So if I’m really focused on cooling time, this is something I definitely want to investigate to see the benefit of driving down that cooling time. And it also has the benefit of having a lower carbon factor of 30% lower than ABS. So we can take a look at how significantly this really drives down our cycle time by 93 percent from where we started. Our part costs are down 72%, and our total carbon is down 53%. So this just really is a great example I think of how especially when you’re looking at process, cost, and carbon can go hand in hand.
If I’m able to reduce cycle time, I’m able to reduce carbon, process carbon in particular. So it just goes to show you that cost and carbon can be reduced simultaneously. And finally, in our last example, we’re going to be moving a little bit more onto the blue sky or the early design phase. We have our same four levers looking at geometry, material, manufacturing process primarily, and What can we do to reduce the impact of our cost and CO2 together? So as I mentioned, we’re going to focus more on the early design phase so we’ll have a little bit more design freedom, and we’ll be able to look at different things as it comes to making this part. So here’s our example part. It’s a flywheel. It’s die-casted. It’s made in the United States. It’s made from aluminum, and it has a relatively small volume. So our initial design is it has 1.7 kg of CO2. It weighs 0.2 kg, and it costs just under $4 to manufacture. What we’ve heard from our friends in corporate is they really want to reduce carbon in this part by 20%. So this is part of a larger part, but this is the biggest component driving CO2 in the end product. So they want to keep functionality the same. So they want to be able to maintain weight within plus or minus 10%. And they’re okay with a little price increase, but we need to keep it below 10% if we hit our carbon reduction by 20%.
So let’s dig in and really see what we can do to hit these targets. So first, let’s do the analysis and say okay, Where is the carbon in this product? And it looks like the majority of the carbon in this product is in the material. So that’s something I really want to look at reducing as part of my initiative. That’ll probably be the easiest place to save some carbon. So that’s creating that first carbon baseline. I know the supplier does not have access to low-carbon aluminum. That’s always an easy win for reducing your material is looking at a material with high recyclability and lower carbon. So what are my other options? As I look at a baseline, here is my carbon. The key variables are 1.7. The key weight is 0.2 kg, and the weight or that it costs $3.93 to manufacture this part. So I really like looking at cast iron because it has four times less carbon than aluminum. It’s 2.6% more dense, and it has a lower cost to manufacture. But I can’t make those weight requirements with the current design. So are there things I can do in the design to take weight out of this product and still meet the requirements?
So can I reduce the volume, keep the weight and functionality the same, use more complex geometry to save material, and reduce carbon? What I want to do is look at sand casting and really look at a more complex geometry to solve this problem. So I go back in. I look at reducing that part’s geometry so that I can use sand casting and keep my weight roughly the same. So using that new geometry, I can see I’m able to reduce my carbon, which is great, by 65%, which is fantastic. Far exceeds the goal of corporate, which is a 20% reduction. So really excited about that, but How does it compare to the other metrics I laid out? So I can look at my material CO2. We saved a 73% reduction in my material CO2. My process CO2 went up a little bit. It went up 37%, but my net gain was a 65% reduction in carbon which is fantastic and far exceeds the goal that the company laid out. Was I able to meet my weight targets? Well, my weight was plus 10% which falls within those guidelines and the specifications we had of keeping the weight roughly the same. But finally, I guess the proof’s always in the pudding when you’re coming at costs. Were we able to hit our cost targets? And it looks like, yes, we’re able to reduce our CO2 by 21%.
So this is a great example I think of highlighting how you’re able to look at things and change these different levers when it comes to cost and carbon. Changing the geometry, making it more complex, but we’re able to switch from a higher-cost material of aluminum to a lower-cost, lower-carbon material of iron. So it really allows you to start to think about how do we start moving these levers around and seeing these results so that we’re able to reduce cost and carbon at the same time. So just to wrap up, I think one of the things that really excites me about what we’re doing here it’s that bottoms-up deterministic approach to calculating material and process carbon alongside with cost so that you can make those trade-offs like, Oh, Is it worth reducing my carbon 50%, 5%? And what does that impact on cost? I think we’ve seen time and time again the other thing that really surprises me, coming into it, I think a lot of people assume that reducing carbon means you need to pay more, and we’ve just seen more and more examples that yeah, definitely some cases especially when you’re in sustainable … when you’re in the sourcing side or sustainable sourcing, there’s not a lot of degrees of freedom.
Achieving Cost Savings and Net-Zero Emissions is Possible
Usually, you’re going to have to find lower carbon ways that are going to be more expensive, but as we see more and more pushing things into sustainable engineering, our cost engineering and sustainable design is you can make a lot more trade-offs and be smarter about things like driving down cycle time, you’re just driving down that process CO2 and then looking at different materials shapes and new automotries, pulling these levers in different ways that really help you optimize cost and carbon. So that’s all I had today, but really I’m excited to see how cost and carbon do not always drive carbon higher or reducing your carbon doesn’t drive the cost higher. And looking at innovative ways and helping customers make this transition to a low-carbon environment is really exciting. So thank you for your time, really appreciate it, and we look forward to hearing feedback you have. Thank you.