Video
The Race to Net Zero
In this session, aPriori moderator, Karen Gold, interviews panelist from Carrier, Eaton, and Alstom. During this session, they share their company strategies such as reducing carbon footprints, investing in sustainable solutions, and integrating eco-design principles into product development to align with global climate objectives in their race to net zero.
In manufacturing, where significant emissions originate, the panelists explores challenges in meeting stringent emission reduction targets while emphasizing the importance of understanding carbon footprints at the product level.
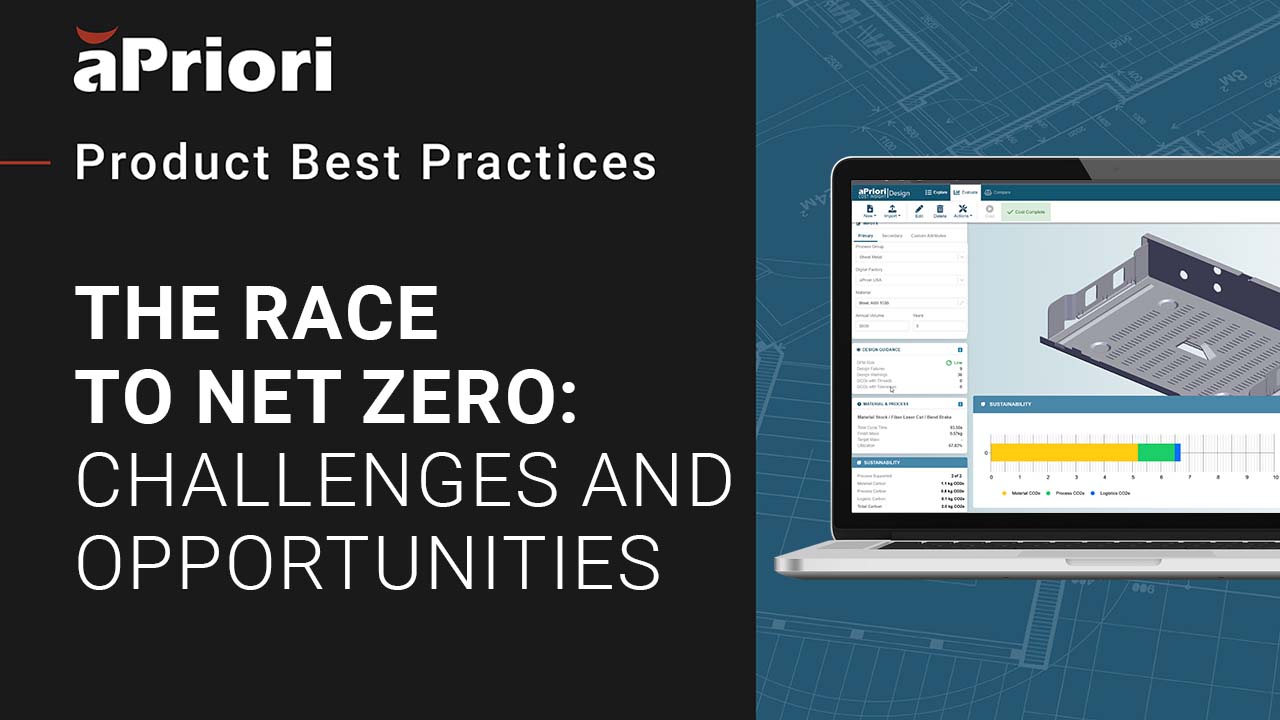
Transcript
Karen Gold: Okay, thanks everybody for coming to our session on the Race to Net Zero. My name is Karen Gold, I’m in the product management team here at aPriori and I’ve actually been with the company for 14 years. So, pretty exciting to be working on new things like sustainability. In the past, I’ve also been involved with aPriori Pro, our manufacturing process models, and our CAD support.
KG: So I am very excited to be here today, and I’m even more excited to welcome our panelists today, all from world leading corporations. We’ve got Tristan Abend from Carrier Corporation, Uyiosa Abusomwan from Eaton Corporation, and Sebastien Girardot from Alstom. And if they look familiar to you, it’s because they have all presented at Manufacturing Insights Conferences in the past for us, and Uyiosa did one just this morning as well as a few years ago. So thank you, gentlemen, very much for being with us today. Very much appreciated. The format today what we’re gonna do is, I’m gonna present a few slides just for some context to set it up, and then we will move over to the panelists. Each one will have the opportunity to present a couple slides about their company and its sustainability goals and then we’ll move to a more interactive sort of discussion, question and answer format. And audience members will get an opportunity to ask questions, so if you hear something you wanna know more about, something that your own company is faced with that you wanna ask them about, please don’t be shy. Just we’ll give an opportunity to raise your hand and we’ll bring a mic around for you.
KG: Alright. So I think we all know that we have to hit some pretty daunting climate action targets to limit global warming and avoid the worst impacts of climate change/climate crisis in the race to zero. We need to reduce our greenhouse gas emissions by about 50% by the year 2030, and we need to reach net zero emissions by the year 2050. And manufacturing companies have a huge part to play in achieving those targets because about a quarter of all global greenhouse gas emissions do come from the manufacturing sector.
But I chose this quote because I think while daunting, the message is it’s still possible. This is from the opening address that Jim Skea, the fairly recently elected head of the Intergovernmental Panel on Climate Change made at New York Climate Week in 2023, this past September. And so the message is, “We can do this, we just need to act now.”
So in today’s talk with our panelists, we will be talking about the challenges that they’re facing. But not just the challenges, but how they’re approaching overcoming those challenges. And then we’ll also talk a little bit about the upside, what benefits they are seeing in their business as they transition to a culture and a practice of sustainability and emissions reduction.
Scopes 1, 2, and 3 – What is the Difference?
Alright. Well, so certainly, one of the challenges manufacturers will have is complying with the current and upcoming sustainability disclosure regulations. And in particular, these regulations are requiring customers to disclose not only scope 1 emissions, the emissions from their sort of direct activities, the operations of the manufacturing plants, their vehicle fleets and so forth. And scope 2 emissions, which are indirect… Emissions are indirectly responsible for through the generation of energy that they purchase, electricity, heat and steam. But also, these regulations include scope 3 emissions. And those are emissions that a company is indirectly responsible for through the activities of their global emissions value chain.
So upstream scope 3 emissions include things like emissions from the materials or parts that they source from their suppliers. And downstream scope 3 emissions include emissions due to the transportation and distribution of the finished product, the in use or operational phase of those products, and also the end of life treatment for their products. So obviously, it’s challenging enough to kind of get your arms around disclosing things related more directly to your direct activities, but then also being responsible for reporting on the activities of your value chain, which is usually hundreds or really thousands of companies, is an added challenge. But it is of critical importance because for most companies, their scope 3 emissions are five times greater or more than their scope 1 and 2 emissions. So being able to report on those and ultimately mitigate them is obviously key to reaching our emissions targets and ultimately, the goal is for a zero carbon world.
Now, on the right hand side of the slide are just some of the regulations that are current or will be coming into effect soon. Europe is leading the charge with its corporate sustainability reporting directive. That is coming into effect in January 2024 and will require about 50,000 companies in the EU to report on their scope 1, 2 and 3 emissions.
But the US is not too far behind. The US Security and Exchange Commission is… We’re expecting the final draft of its climate disclosure bill any day now. It also covers scope 1, 2 and 3 emissions.
The State of California actually signed an emissions bill into law in mid-October. And more are coming out all the time. I think Brazil actually just announced about a week ago that it would have a climate disclosure bill active by 2026. So global climate action is taking place.
And even the international standards like the ISSB standards and the Science Based Targets initiative all concern scope 1, 2 and 3 emissions. In fact, the Science Based Targets initiative requires companies who are setting science-based targets to include a target to reduce scope 3 emissions if those emissions comprise 40% or more of their total emissions. Which as we just noted, is pretty much everyone.
Business Leaders Can Be High-Level Climate Champions
But it’s not just being able to comply with these sort of disclosure regulations at the aggregate corporate level. Manufacturers really need to have much deeper, more granular insight into carbon footprints at the product or even the part level. So we are hearing more and more from our customers that they’re being required to produce some form of product carbon footprint report, if not a formal environmental product declaration, in order to be able to continue to sell to their customers. Or to be able to participate in certain types of projects like green building projects or other public sector projects. The green guides and the green claims directives in the US and the EU respectively. And the UK also has a very similarly named directive. These are anti-green washing regulations. And their purpose is to ensure that companies don’t make misleading environmental claims about their products.
So if you want to market your product as green or ecofriendly or more environmentally friendly than the competitors, you need to be able to substantiate those claims. And if you can’t and they’re found to be false, you can be assessed some pretty hefty financial penalties. And then even understanding things like the EU’s Carbon Border Adjustment Mechanism or CBAM, and a couple presenters this morning talked about that. But it is effectively a tariff that European manufacturers will have to pay when they import certain types of carbon intensive materials and goods into the EU. And that includes iron, steel, aluminum, electricity, hydrogen and also cement and fertilizer. So it’s important and the purpose of this is to prevent so-called carbon leakage, which is when manufacturers deliberately move the production of these carbon intensive items to other regions, lower cost regions that have less stringent climate controls.
But obviously that does undermine our global climate goals. It also makes it harder for European manufacturers who are subject to these tighter climate regulations to compete. So CBAM effectively assigns a fair price on the carbon that you’re importing.
And it’s important to understand that because when the actual… Right now CBAM is in a transitional phase, you only have to report on your import of these carbon intensive goods. But it will go into effect in 2026 and that’s when you’ll start paying those tariffs. So it’s important to understand what the actual landed cost of your imports will be.
And then finally, the final point I make before I turn it over to our panelists is that really it’s not in the end it’s just about reporting. It is really about understanding where is that carbon coming from, what are the opportunities for decarbonization. And so to really have that insight to get the information about is it coming from the material, is it coming from my production method, is it coming from where I’m sourcing the part. That’s where you get the insight in order to really make meaningful decarbonization efforts.
So with that I will turn it over to my panelists. And Tristan, I think we started… We’re going from the left to the right. So I’ve got Carrier.
Introducing Three Manufacturing Companies Taking Immediate Action in Sustainability Efforts
Tristan Abend: Alright. Afternoon everyone. So my name is Tristan Abend. I’ve been at Carrier Corporation now for about four and a half years. Presented last year, was more on a high level of what me and my team do. This year we’re really focusing more on the sustainability side and the use cases that we’ve been getting from it.
TA: Carrier has been around for over 100 years and really it’s broken down into three business units still to this day, HVAC, refrigeration, and then of course fire and security. The one caveat I would say is just, you probably saw recently that we are actually divesting ourselves from fire and security and turning much more into a climate solutions company. In doing that we are actually making a big play now in Europe with our acquisition of Easement Solutions. This is a $13 billion deal that is going to really shake up the market, we believe, and it really positions us well to be the number one leader from a climate solutions standpoint for building solutions. In bulk though, HVAC is still our bread and butter as you can see, and refrigeration is going to grow, going into the future looking at cold chain solutions.
TA: As far as Carrier’s climate goals and climate ambition, for the past couple years, really the part that most people have been most familiar with is our 2030 ESG goals. And the highlight here is our one gigaton challenge, and that really is to reduce our customers’ carbon footprint by one gigaton by 2030. We’ve made great strides in this. We are well on our way to achieving that, as well as getting towards achieving carbon neutral operations throughout the globe and reducing our energy intensity. We are adding onto this now with this year signing up for the Science-Based Targets initiative. This is a initiative that was started a few years ago now that a lot of companies are signing up for, to really get to net zero by 2050. And we are gonna be releasing our targets here very soon and validating them as well.
KG: Alright. Uyiosa.
Uyiosa Abusomwan: Thank you. Hi everyone. Good afternoon. My name is Uyiosa and I’ve been two years now with Eaton as a senior global technology manager for digital engineering. So I’m sitting in here on behalf of our ESG and our experts in this field in sustainability.
UA: So about Eaton. We are power management company about $20 plus billion in sales. We operate in over 170 countries and today we have about 92,000 employees around the world. Just like you mentioned, we’re over a hundred years old and spent a big chunk of that, we’ve managed to stay in the S&P 500. In terms of our businesses, we have an industrial sector that covers our aerospace, our automotive division, which is our e-mobility and vehicle group, which is now just the mobility division. And then we have a electrical sector, which really covers everything from the grid all the way to components that end up using the energy in our devices or our manufacturing plants.
UA: Alright, so for our sustainability, what is shown here is our 2022 sustainability dashboard. It’s really four key pillars here. The first is for us to create solutions that are sustainable. So effectively Eaton is a power management company, so we actually make a lot of components that either manage power directly or consume power. We also have another pillar that’s focused on reducing our footprint. This would be our Scope 2 really, Scope 1 and 2. And then engaging our employees and communities. We believe that we make what matters work, and we are very society conscious. And our employees are, already work in those societies so we’re very conscious of that. And the last is doing business right.
UA: So if I go into just the first two pillars there, for creating sustainability solutions. So from the bottom up, our Scope 3, just looking at where we are today is 23% down since 2018. We’re making significant investment in this area, in swapping out materials, for example. We’re making, reducing the power consumptions of our power management systems.
UA: And also 71% increase in the net sales from the solutions that enable more sustainable future. So effectively, we are investing in the right place to make sure that we support our sustainability global campaign.
UA: On reducing our footprint this is focused on the waste we generate from manufacturing. For example, 75% of our facilities have zero waste to landfills, 8% have zero water discharge, and also 27% reduction in greenhouses since 2018.
Sebastien Girardot: Okay, so good afternoon. I am Sebastien Girardot. I work at Alstom Transport in Paris, France. And Alstom Transport is a big company, and we make high-speed train, regional trains, tramways, metros, all this kind of transport device. And it’s a very big company. We have more than 80,000 employees all over the world, in 250 sites in 63 countries. So it’s a really a major company.
SG: Okay, these are some example of the project we’re working on. In this slide, we can see only the more, only the projects that are more related to the sustainability problem. And you can see that for example, we have some modernization of all the trains.
SG: And for example, we replace diesel locomotive by electric locomotives. And even when there is no electric line on the track, we can work with batteries or even we have some, a new type of product that is based on hydrogen with fuel cells. These are very, very nice new products.
SG: But also for the standard products, I would say, like for example, high-speed train, for example, we are going to deliver very soon the new high-speed train in on the French market, the TGV. And this new generation of train is the fifth generation, will consume 20% less and will embark 20% more passengers for the same lanes and the same top speed that is 320 kilometers. This is a kind of announcement that we do on every project.
SG: Okay. This is a, just a picture that shows you we have a big team in Alstom that is named eco-design, the eco-design team. And this eco-design team is in charge of estimating not only the carbon footprint roadmap of a project of a train, but the whole impact on the planet for this project.
SG: So of course you can see that we have on this, we have the energy efficiency of the train. Of course, this is the first thing that we check. This is the first thing that is requested by suppliers.
SG: But also we also work on materials to try to find greener materials. And also we take into account not only the production of the train, but the life of the train with the consumption, and also the end of life of the train just to be sure that every piece of the train can be recycled. This is something very important and part of our emissions reduction targets plan. And you can see also that we take also into account the noise of the train, because we consider that the noise of the train and the quality of the air inside the train is part of the project.
You can see on the right that we have a project, something at Alstom that we call Alstom in Motion 2024-2025. It’s a kind of guideline rule that we define every five years. And among all the rules that we, the goals that we put, we have these goals related to sustainability. We want to have 25% energy reduction in all solutions we developed.
SG: And we want 100% of the new developed solution to be eco-designed. So this is, eco-design is a new way we use to develop a solution that at each step of the design of the project, we check that all economical and ecological steps are fitful. This is very important. SG: And also we will, we also want to have, to increase the recyclability of the parts in the rolling stock solutions.
How Design, Cost, and Value Engineers Can Impact Corporate Sustainability Efforts
KG: Thank you. Alright. So Sebastien, I think my first question is for you, which is that you are in the Design to Cost department, right?
SG: Yes.
KG: How do you see your mission evolving as it regards sustainability? And how does that interact with the eco-design team that you just mentioned?
SG: Yes. The eco-design team tries to estimate the carbon footprint of a complete project and they use some specific tools to do that and for them it’s very difficult to go at a very low level. For example, they can estimate the life of the train, they know the weight of the train, so they know the mass of the train, but they don’t know the rough mass of the parts of the train. And they don’t know what is the exact process to make each part. So with aPriori we can help this team to have something much more accurate, because we can give them not only the weight of the part, but also the rough mass of the part and we can also give them the cycle time for each operation. And with this information they can estimate the CO2 impact of each individual part, so they can get at the end a much more accurate result.
KG: Thank you. Tristan, last you talked a bit about Carrier and how the value engineering team is helping assess sustainability efforts as well as cost. I’m wondering what you can tell us about that, sort of that higher fidelity estimation and maybe sort of what’s transpired since last year?
TA: Yeah. I think to your point, last year we were still working on the trial version of the sustainability module, so we were really still trying to assess not only the value of what that can bring to us as a business, but also how best to implement it. Now we’re actually in that implementation phase and talking strategy. I think what’s changed as an organization is, number one, we’ve always had sustainability and climate action in our DNA, but we’ve really been in an overdrive phase of adding on infrastructure internally to us to really pursue more ambitious goals.
TA: So now that we have a better team set on up, really what my team has been doing from a services side is helping do that analysis and looking at it from a perspective of can we implement EPDs on as many products as we can, as soon as possible because our customers are asking for them. And helping support the sustainability engineering organization in their overall strategy on best where to do these EPDs and where do they need the analysis and at what time. So I think really the big thing that we’re trying to look at going forward is how can we get faster? How can we improve our accuracy? And what other different kinds of requirements are there going to be, especially in this regulatory environment? Right now we’re really focused on LCAs and EPDs, but what else is coming down the line?
A: One thing that we’re aware of is TM65. That is a really baseline report that we’ve implemented inside aPriori that automatically will give us that information that we can hand to a customer upon request. So we’re really trying to make sure that we stay ahead of the curve as much as possible. The regulations certainly, as fast as they’re coming down, we’re trying to react as quick as possible.
How Digital Transformation Relates to Sustainability
KG: Thank you. And Uyiosa, tell me a little bit about what we all know now that you’re charged with sort of digital transformation. How do you think about that in terms of not just your sort of cost or sort of [chuckle] “Siri, design me a new part,” but how do you think about digital transformation as it relates to sustainability?
UA: That’s a very good question. So I think that for us, for Eaton, we are a power management company that is really focused on making our environment better because we feel that we are responsible in part from distribution to consumption of the energy, right? So for us, digital transformation is going away from a reactive mindset where we are trying to catch up with either governmental regulations or requirements of our customers, to where we are proactive. Proactive in the sense of integrating sustainability in the products we design, in how we design products. From how we source the materials that we’re using, to the power consumption, how we source the power we use in the manufacturing processes.
So effectively, the first part of this is how can we integrate aPriori to our design processes? We’ve been discussing with the leadership of aPriori to see how we can bring that and make that happen, and even did a case study a couple of weeks ago which was very successful.
UA: The second part of that, in terms of from a digital transformation standpoint, is that apart from just being able to design right, we need to be able to communicate that right.
UA: Today, when we get a request for a report, like you said, we’re being asked to provide reports from our customers. Today there is a reactive effort on trying to figure out what are the components used in this part or the systems that are being delivered to our customers and then narrowing down the various levels, one, two, three, of the implication of our product, from manufacturing to upstream downstream.
UA: So we don’t want to do this, continue to do this reactively. And that’s where aPriori also comes in and in-house we’ve developed solutions that actually allows us to go in and do this proactively so that when we integrate our solution with our PLM systems, we’re able to, for legacy components on our PLM systems, we’re able to generate this report.
UA: And aPriori has a very sweet spot there, because if we’re doing design to cost design for manufacturability, and with the aP Generate solution that we’re deploying to be able to automate the coding and manufacturability, the cost of manufacturability estimation for legacy products in our PLF system, we also wanna be able to integrate this so that proactively, we are running in the back-end a solution that allows us to estimate and generate these reports before being asked to do it.
KG: So you’ll have already sort of collected the data just as a byproduct of analyzing the parts, and then you can roll it up across your PLM system as needed?
UA: Absolutely.
[laughter]
KG: And Tristan, that sounds very similar to your goals. I know that you’ve made a big effort to write back some of the sustainability outputs into your PLM system to do the same thing. Do you have any, now that you’re moving more into the implementation, the productization sort of phase of your project, do you have any goals in terms of how much more quickly you can assemble these EPDs or any targets like that?
TA: I think not necessarily. From a goal standpoint, it really varies as much as the product. You have to remember that when it’s concerning EPDs, the time that it takes to create them really depends on, well, number one, how big is the product that you’re looking at.
TA: For example, our Montluel team over in France has been doing outstanding work with EPDs, and at the end of this year we’ll have an EPD for every single product that comes from that factory, in large part because of compliance to France. And what we aim, I think from an aiming standpoint, we hope to get an EPD timeline down to a matter of a couple of months, rather than as much as a year that it can take on some of our very large products. So for us, our goal is to get it down into the weeks rather than months to years that it can sometimes take, but in large part, that also depends on the data. So that’s where aPriori has been a little bit more instrumental for us at least, because a lot of the data that you need for an LCA, a lot of the data that you need to be able to decide on a carbon footprint, is not necessarily information that you can just reach into a spreadsheet and grab. It’s not information that generally organizations have done a great job in keeping track of. So being able to use a tool from a scientific basis to prove out a methodology that is used by aPriori, we’ve been able to really use that data to help seal some of the gaps that we’ve been finding.
Setting Sustainability KPIs
KG: Thank you. Sebastien, I know that the eco-design group, it’s all about continuous improvement and that they sort of set targets at the end of every project they complete a life cycle assessment and they use it to set sort of KPIs and targets for the next project. Do those targets also include goals for sort of streamlining the process, performing these LCAs earlier throughout the design process or any metrics like that?
SG: Yes. In fact, the life cycle assessment is a kind of dashboard that is defined at the beginning of a project. And at the very beginning, they just set in this document all the targets they want to reach in terms of sustainability, CO2 footprint, water pollution or every aspect of the problem. And during the life of the project, they have some checkpoint every month, every week exactly, and they check if the points are fitful. And at the end of the project, we make the final comparison between the final product we get and what was the request at the beginning. There are also some differences. And we use these differences at the end to adapt the new life cycle assessment for the next project. So each time we start a new project, the life cycle assessment is better and better.
KG: Okay. So it sounds like you’re getting pretty adept at that. Do you think there’s still opportunities for improvement?
SG: Oh yes. Of course. We have some challenges in this project. Because you know that a train is a really complex machine. It contains thousands and thousands of parts. And using aPriori or any other product, we can’t cost estimate or carbon footprint estimate every single part. It’s impossible.
SG: So this means that we have to choose the most important subsystems. And we are going to cost and estimate only these important subsystems. And for the others, we are going to make just a rough estimation based on all projects. But we can’t do that.
SG: Of course, we would like to be able to estimate in terms of cost and carbon footprint all single parts, but it’s impossible.
KG: Okay. We’ll return to that later. Gentlemen, I know that you all have worked a lot with supporting sort of design engineering. I’m wondering if you could speak a little bit.
Net Zero Carbon Emission Goals and The Supply Chain
KG: Are you starting to work more with procurement or the supply chain in terms of understanding carbon in your sourced parts and materials? And I’ll send that to Uyiosa first.
UA: Alright. Thank you. So for us absolutely. Interestingly, if I focus on the tool, aPriori, our supply chain team started, we’re the first to start using aPriori before the engineering organization.
UA: And you know, when I joined Eaton the vision before I joined was how do we migrate this, collect this effort, that whether it’s designed to cost, designed for manufacturability and now designed for sustainability early on in the design process.
UA: So yeah, to answer your question, absolutely. Today we have very strong collaboration. In fact, there are several initiatives between our CTO’s organization and our supply chain organization at the senior executive level.
UA: And some of those initiatives revolve around data cleanup to use across the lifecycle. And then there are some initiatives that are focused on design to cost, and now new initiatives focused on design to manufacturability.
UA: So we’re seeing more and more collaborations there.
KG: Thank you. Tristan, what about you? I know you’ve talked, one of your motivations to starting to use aPriori was the difficulty in getting sort of reliable supplier data. Have you… Is that starting to change? And how are you starting to, what are you doing to compel your suppliers to participate more or provide that information?
TA: I would say it’s changed for the better over the past year. I think one disservice that we were doing in the beginning is taking a broad brush to all of our suppliers, where now we’re being much more focused. And we’re really focusing on, well, who are our big suppliers, who are the growth suppliers that we really want to focus on for some of our more key products going forward. And asking them to help us in this. Because in large part, a lot of our bigger suppliers have their own sustainability goals that they are working on. So when it’s concerning some of the information that we need for LCAs or just information that we’re looking at to evaluate from a design standpoint, I think we are seeing better information sharing from our supply base. But in large part, when we’re looking at some of our smaller suppliers, I would say it’s still going to be a few years down the road ’til we get to the point when it’s as free flowing as what we would hope.
Training Your Supply Base on How to Estimate Carbon Emissions
KG: I’ve heard some customers we’ve talked to that are actually involved in training their supply base on how to estimate carbon and how to report on carbon. Are you seeing any of those types of engagements?
TA: Yeah. And in particular, I think too, it’s an education piece on what actually our goals are. Though we think that we release it to everybody in the world, there’s a lot of people that, especially our suppliers, that don’t know what our targets are. And I think educating them on that piece on why we’re making such a big strong argument towards this, and also educating them on why it’s important to us, I think goes a long way to helping them. You know, especially when we’re talking about right now just gathering the information. We’re not looking at this from a perspective of battling one supplier over the other. We just really are trying to do a data gathering exercise at this point.
KG: Sebastien, I know that your design-to-cost team supports both design to cost and also supplier negotiation, sort of fact-based negotiations. Are you starting to, or do you foresee yourself getting more involved in setting carbon targets or other types of goals for your supply chain?
SG: Yes. For the supplier now we are starting working with our suppliers. And at the same time, we want us to answer our FQs and to give us the price of the part and the detailed breakdown of the cost. We now want them to give us also their carbon footprint estimation. And it’s mandatory now.
KG: Oh, it’s mandatory?
SG: No, it’s become mandatory. Because in Europe, especially in Europe, when we deliver a project to us, to a customer, we need to give him this global estimation. So to give this global estimation, we need the estimation from our suppliers. Because almost all single parts at Alstom are made by suppliers. We make assemblies, but for the single parts, except some very complex one, they’re all made by suppliers. So we need this feedback from the supplier. So it will become in the future, maybe not now, but maybe in the coming years, it will be something absolutely mandatory.
KG: Maybe this is for all of you, but are you finding it hard to sort of maintain supply chain resiliency and diversification while also increasing sustainability requirements?
SG: Yes. You know that at Alstom we have suppliers everywhere. And for example, a part that we need in France, maybe we can have a supplier in France, we can have another one in Poland, another one in Czech Republic or in China maybe. So now we want to estimate also the carbon footprint and not only the final cost of the parts. And maybe a part that was cheaper in Poland compared to France, maybe if we include the carbon estimation, maybe it’s not a so good solution. Yes, the price will be lower, but the CO2 impact will be higher. Because you know that in France electricity has a very low impact in France because we use a lot of nuclear plants. This is not the case in Poland, for example. SG: So the carbon footprint for the same operation is higher in Poland than in France. And if it’s done in Poland, you have also to add the transport. So at the end, when you make the final comparison, maybe the product made in France is better than the one in Poland. So that’s why maybe this is going to change a little bit the way we see our suppliers and we are going to more challenge them on that.
UA: So maybe the way I think about this and the way we are addressing some of these topics is we’re not just addressing it from one direction or dimension. And I’ll try to explain what that means. So for example, when we’re thinking about sustainability, we’re not just looking at what’s the cap on emission of manufacturing process or the raw material. That’s one dimension. We also looking into dimensions like what’s the, if we’re just taking stainless steel for example, where is that stainless steel made? And that has a role to play. And then we’re taking that up, so I’m just gonna kind of work up the scale to say, “Okay, from there, the next step is even in the design process effectively, can we do lightweighting?” That’s where my department comes in. I’m part of the Eaton research lab under the corporate office, and where we’re looking at things holistically, not just, “Hey, design-to-cost or the shoot cap on, but okay, what if we can lightweight the product completely and then the system?”
UA: And then if you take that up one notch is like, can we completely move away from conventional manufacturing processes? Can we do additive manufacturing here as, again, as part of our mission target and goals?
UA: And lastly is with our materials experts, we’re looking at, okay, can we use alternate materials for solutions where maybe we used steel in the past. Can we switch to some other materials that are maybe not traditionally used for this component, but then it helps in the overall sustainability goal?
KG: Yeah. Absolutely. Thank you. Thank you. I wanna give the audience a chance to ask some questions if there are. I have a few more, but I don’t wanna take your time. John Allen?
Q&A
John Allen: So John Allen with Benchmark, my background’s 20 plus years in EMS or Electronic Manufacturing Services, aka contract labor. And I know across everything we do, we’re used to working under environmental type regulations. And we all know ISO, ITAR, UL, all of those types of requirements that are placed on us. And in fact, we have to warranty and stand behind with some amount of accountability in terms of our processing.
So one of the things that I’m pondering as we look to be, just to start getting into this carbon monitoring, is how do we deal with the accountability? How do you measure your accuracy?
And how would you defend or warranty your estimated carbon numbers? At some point if you’re challenged, how do you… What’s the science behind it?
KG: Tristan, can I ask you to take that one?
TA: Sure. Yeah, specifically I would package that on up and say, how can we defend ourselves against an audit? The SEC certainly hasn’t come down yet with their entire Scope 3 disclosures, but we know it’s coming and they’ve already come down on Scope 1 and 2. So when we look towards utilizing aPriori, I think chief of mind is how do we use this for an audit? And I think the big thing for us is, number one, where’s the data coming from? A big selling point for us was Ecoinvent. It’s a great partner for us. We’ve used them in the past before aPriori. That’s number one, a huge defense for us when it comes to the info coming in. They’re ISO certified. They’ve been in the space for a very long time. When you look towards the actual physical calculations themselves, I think it really comes down to things that we’re traditionally used to as part of value engineering. Number one. When it just goes through and calculates the weight, is that actually the weight in your physical parts? And is that what you’re showing on your drawings when you’re reviewing this maybe with a customer? I think for us at least, that’s a great verification check that we already have in our process, and we’re utilizing that still. Going further, when we look at the process, you start getting to the point when you, if you start questioning your carbon data to the point of wondering if your process carbon is correct, I think you’d start getting to a point of you’re basically questioning the cost engineering that you’ve been doing all along. So at least when it comes to us, being able to have something repeatable, having something with good data in the background, and knowing that if we ever do get asked about this, we can be very transparent because the aPriori tool itself is transparent. So far at least, when we’ve had these sort of questions come up, we have not had a problem being able to use that as a defense. I don’t know if anybody else wants to go?
KG: Thank you. Looks like we have another question.
Naren: Naren from Danfoss. We’ve been using aPriori for more than seven plus years. So just on the sustainability side, can aPriori sustainability help, from your experience, all three people, can experience to able to get the purchase goods, just what is the carbon? Should carbon of the purchase goods of all your parts? It cannot be designed to your product level, I understand. And of course, the second question is, when you give your shoot carbon to your customers and we do the EPD certification, which internally verified and we have like three years verification. Can the report from aPriori is today agreed by the EU people for them to verify it and it can be a third party verified? Can I submit the report?
TA: I’ll give out the first answer. I’ll let a couple other panelists talk as well. So to your point. When it, when you’re concerning the actual end use of the data, first off, you gotta go in knowing that aPriori only covers that really Section A and a little bit of Section B. Right? I think one of the things that we had to educate ourselves about when we went in and got the sustainability module from aPriori is the fact that it’s not meant to replace your LCA tool. It only amplifies it and maybe makes it faster. I think when you’re looking at a third party, really the aPriori data gets fed into the LCA tool, but after that it looks just like a normal LCA report, right? So it then goes on to your third party auditor and the they can verify it. Now, if there’s an issue, what we have found is that the third parties so far have been enjoying the fact that we’ve been using aPriori. Because for them at least, if there is an issue, it’s really fast for us to make a change. And so we’re able to answer back any questions and validify any of the results that they may want more information on. So at least from a third party standpoint, we’ve been doing really good around that. You guys go if you’d like.
Alex Walker: Alex Walker with aPriori, actually. It’s a little like preface before my question. So with the EU having a net zero date of 2050 and the manufacturing industry being worth $3 trillion as of this year, do you see these companies kind of offshoring more to places like Mexico that don’t have a set date for net zero yet? Or do you see it kind of just maybe them implementing and kind of going with the flow until they kind of find a solution for their net zero targets?
UA: I’ll try to take a stab at this. I think Karen mentioned this earlier in the introduction that there are policies now being implemented to ensure you don’t just offshore by putting some checks on the imports. Right? To make sure that you can’t bypass the system that way. I don’t know if that answers your question. But that’s really it. And that’s why in our policy, in our of pillars, the four pillars I shared for Eaton, the last one there was on ethics. Just making sure that we’re true to ourselves and our community that we serve and where our employees are coming from.So looking within our own ethics as an organization, and also the government is making sure that we cannot bypass the system and do just that.
KG: I have one more question. Thank you, gentlemen. Can you talk a little bit about the benefits you’re seeing to your business as you embrace these sustainability targets?
KG: I’ll let Sebastien take that one first.
SG: Benefits of? Sorry. [chuckle]
KG: As you transition to this culture and practice of sustainability, what sort of benefits are you seeing to your business?
SG: The benefits is, of course, for the suppliers. You know that the suppliers in transportation are very demanding this kind of reduction. Because this is why they buy train. This is why they buy regional trains. They want to reduce the number of cars in the country and they want to replace the car by electric trains. They want this reduction. SG: So of course, the first thing they ask when they want to buy a new train at Alstom is, “Okay, can you guarantee that we are going to consume less electricity than before?” This is the first thing. SG: If we can do that, of course, it’s a real benefit for the supplier. And of course, if we want to win the bid, this is what we have to do.
KG: Yeah, so it’s a fundamental condition of your business, you see.
SG: Yes.
KG: Uyiosa, we were talking just before, and you told me about some interesting benefits?
TA: That’s right. I’ll touch this from three points. The first one is this is great opportunity for us. Because we’re a power management organization. There’s electrification everywhere and that’s our domain.
UA: So for us, we see this as a huge opportunity. And that’s where digital engineering actually comes into play. We just have to streamline our processes to meet that business need, right? From a business standpoint, this is good news for us.
UA: The second part of it is I joined Eaton about two years ago. And one of the reasons I joined is that they are a strong advocate for environmental and societal policies. And really, that was the PR for me, way… Years before I joined the company.
UA: And that’s really who we are in our DNA to make sure that we leave the world better than we met it and enable our customers and businesses to do the same thing. So that’s the second given for us.
UA: The third part now goes to our customers when they win and also our employees. I gave my, maybe in my second bullet there, I said, “Well, for me, we hire, we’re able to hire a lot of people a lot of top talents.” In fact, one of my students just sent me an email yesterday and say, “Hey, I got an offer from Eaton.”
UA: And the reason that this, she was also my TA. I never played any role directly influencing that, but I think that young talents and experts are able to see what we do and what we stand for from a sustainability standpoint and they’re attracted to us.
KG: Wonderful.
TA: I think for us, at least, the big thing is it’s empowered us to play to win. Really, Carrier as an organization going forward cannot afford to be on the sidelines when it’s concerning regulations but also sustainability.
TA: We as an organization make products that, in large part, will set the standards going forward when it’s concerning building energy use. 40% of the emissions come from our systems or systems like them.
TA: So when, as we are going forward, it really is not a choice for us of whether we do it or not. I think the choice is how ambitious do we want to go after this policy of being sustainable first. And for us at least, the more ambitious, the better.
TA: And that really helps empower our workforce. It gives them something to really strive towards. And I think that, in number one, is what you need of some company that is trying to get to net zero, is you need an empowered workforce that feels like you’re actually going towards something.
KG: Wonderful. Well, thank you, gentlemen. That was a great note to close on. I appreciate your time very much today.