Video
Panel Discussion: Partnering for Sustainability
Join this panel discussion to hear how aPriori has been working with customers to advance our Sustainability solution that tracks CO2e emissions from product manufacturing. Panelists include representatives from the following aPriori customers: Scania, Heliogen, Google, Vestas, and Carrier Corporation. See how top names in the manufacturing sector are utilizing technology to meet – and report on – their green design targets.
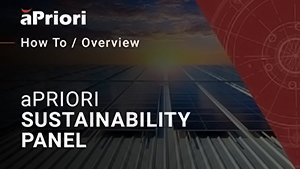
Transcript
Carsten Hochmuth: Thank you for joining us today for this panel discussion on sustainability. We are very excited to be joined by a fantastic group of business leaders from world-leading companies. We have Tristan from Carrier, Bobby Pinter from Google, Jackson Baker from Heliogen, Daniel Rosner from Scania and Brian Lindgaard Jensen from Vestas. Thank you all for joining.
The idea behind this session is we’ll do a quick intro on sustainability and how it impacts the private sector. Then each of our speakers will talk about how they help companies think about sustainability. We will get into the higher level goals around environmental impact. And we will talk about how a sustainability partnership means that we are all working together to achieve those goals.
Sustainability Goals Are Forcing Business Leaders to Track Emissions
Carsten Hochmuth: At the same time that we’re sitting here today, the UN climate summit COP 27 is in its second week. The speakers at COP 27, from NGOs to nonprofits to politicians and those in civil society are telling us that the situation is pretty grim, and that we need to mobilize to take some urgent action to mitigate climate change and accelerate our move to a zero carbon future. Based on some of the latest data from the IPCC summary that just came out in November, the yearly emissions from the global supply chain represent 60 gigaton of global greenhouse gas emissions. Assuming that we want to reach the very challenging 1.5 degree warming goal, we need to take some urgent action. According to the IPCC report the total emissions need to go down to 10 gigatons by 2050 in order to achieve that sustainability goal. So it’s not that much time left to make some very aggressive changes.
Depending on how you look at the emissions and whether it’s just CO2 or total emissions or contributions from energy production, about 24% are in the manufacturing sector. So companies like ourselves here and partners in the private sector play a very important role to try to bring that level of emissions down and to bring that down aggressively. How do we achieve these goals? I think one of the key things is by measuring—understanding all the options—and pursing decision making strategies that reduce both the embedded carbon in the product, and the operational carbon. There’s an example here which is a pretty simple. Imagine a part that in itself has just about a kilogram of carbon coming from the material that was used for it and the production process. It’s a tiny fraction of the 60 gigatons. But if we’re making maybe 100,000 of these, then by selecting different materials, by picking processes, by sourcing where there’s a better energy grid, we can make some significant changes even at the individual part level.
That has repercussions all the way down the value chain. For example, if we were able to cut the carbon equivalent emissions of this part by 50%, at that annual volume we would be saving about 50 tons. So at that point, the numbers become important and make a significant contribution. A lot of recent innovations in sustainable practices mean we can work towards making that number zero for a lot of parts. These are include green materials like green steel, renewable energy to make those materials, and more recycled content. So that’s just one example of how design sourcing and applications of sustainable business practices can help companies reduce emissions. So I wanted to just give that quickly as an intro before introducing some of the panelist intros. Tristan why don’t you kick us off please.
Tristan Abend: Oh, thank you, Carsten. Carrier is pushing sustainability efforts into the HVAC space, with refrigeration a close second and fire and security a distant third.
Just to review what our 2030 goals are, we are trying to achieve carbon neutral operations and reduce energy intensity by 10%. These are two goals are related. Our one gigaton reduction that we’re working on, is on operational carbon for our customers in particular. We are certainly trying to achieve carbon neutral operations specifically our factories, and a lot of that has to do with tracking energy usage. And then of course reducing the energy intensity, we can go further. We can go even bigger now with aPriori at play because now we’re able to track it so much easier than we otherwise would have. So that’s kind of where Carrier is seeing a lot of the play going forward for ESG.
Carsten Hochmuth: Awesome. Thanks Tristan. Let me pass it on to Bobby from Google.
Google Cloud’s Business Model is to Help Companies See the Environmental Impact of Decision Making
Bobby Pinter: Cool. Hi everyone. My name is Bobby. I’m from Google Cloud. I’ll start a little bit higher level than just Google Cloud. I think Google is a company that we probably know and all use in various forms. It has over 9.1 billion user products everywhere from Gmail to Search to Maps. I think what’s interesting about Google’s story as it comes to sustainability is the recognition especially when thinking about the intensive amounts of data centers and data and creating services that really span the globe is we’ve had to think very seriously about how we create the right energy in those systems, how we create sustainability for them. So Google’s goals are really around achieving that zero for itself. And in this process, we’ve achieved certain standards for example around 24/7 carbon-free energy.
As we’ve gone and created all these services and created these capabilities for ourselves, Google Cloud as a little bit more of the commercial arm of Google is really trying to think about, “How do we take this innovation, this thought leadership from Google itself and how do we bring that to some of the other corpus that we work with?” So really our strategy is around three major areas. The first one is around how we build more sustainable development. This is about focusing our business model to bring customers the kinds of cloud services and technology they can use to create new products and services for themselves in a digital capacity. From a carbon free future perspective, we’re really thinking about, “How do we bring a lot of those different energy related insights to them?”
In the cases that we’re here to talk about especially today, how do we bring in this granular information that Google has gained for itself and now bring that to other companies so they can rely on that whether it’s related to energy or water or a wide variety of other kinds of environmental impact use cases. A little bit about some of the the areas that I focus on specifically: decarbonization for us in Google Cloud is very much focused on on digital. Google Cloud is one of the large hyperscale clouds that you may be aware of around the world. We’ve been really focusing on, “How do we help our customers who are using Google Cloud operate with as as much green energy as possible?” There’s been a whole suite of features that we’ve released in the last year or two where you can look up by region the amount of carbon footprint associated with the actual products that you use.
For us that’s the analytics things like BigQuery: What is the environmental impact of your data storage and your computational needs? By showing you the kinds of carbon-related insights that you need for your decision making, we are empowering our stakeholders to make different decisions. We think this is actually quite an important part of our story from that technical perspective. A lot of teams are starting to say, “We talked about cost of carbon today or different carbon budgets, we’re starting to think about machine learning which is very computationally expensive. Should those teams be aware of how much energy is going into running those machine learning models? Should they be aware of where they’re being run, how the energy could be from renewable sources or not?” Those are the kinds of questions that we think are most exciting for us.
The other aspects of our SDGs are around climate resiliency. Some of the portfolio that you may know from Google is things like Google Maps. That’s given us a really strong capability around geospatial and remote sensing. So what we’ve done is we’ve taken Google Maps and Google Earth Engine. We’ve actually created an analytics layer on top of that through something called Google Earth Engine. What’s so interesting here is this gives us this really interesting capability to use all the satellite imagery around in the world and provide insights around deforestation, watershed level changes, crop health, and crop stress. These sound abstract or sound a little bit away from Google’s mission but when you think about what we’re really trying to offer here we’re saying, “How are we going to help the world understand its information?” That goes back to that core mission of Google. And then how do we bring that understanding in a form that’s very actionable to give you the right level of insights that you need right now?
When you’re looking at how would we get information from NASA or the European Space Agency—How could we turn those into insights that could be relevant? For manufacturers, those are the kinds of questions that we’re really excited to help companies make those connections. And then finally, the reason I’m on stage here today is really around this idea of sustainability partnership. Google has a lot of great capabilities and a lot of ability to interact with consumers, but we have real limited touch when it comes to a lot of the work that aPriori is doing and early in the design phase. So what we’re asking ourselves is how do we consolidate all this data together, to be a force for that change within our Google Cloud environment? We want to create sustainability partnership with manufacturers, retailers, vice presidents of sustainability, and other key business leaders. We need to find the right partners who are able to help in these very granular very important steps of decarbonization. That’s it. Thanks.
Carsten Hochmuth: Awesome. Thanks Bobby. Next I have, Jackson.
Renewable Energy Can Help Companies Increase Environmental Performance
Jackson Baker: My name is Jackson Baker. I’m a supplier development engineer at Heliogen. Heliogen’s a renewable energy technology company on a mission to decarbonize industry. Any company that uses renewable energy automatically increases its environmental performance. That will help companies hit their ESG tragets.
At Heliogen, we use concentrated solar systems enabled by AI and thermal storage to deliver multiple products. So specifically direct heat, direct electricity and then also green hydrogen production. To explain a little bit what about what concentrated solar is: if you know how you can sort of burn an ant with a magnifying glass, what we do is put together thousands of those magnifying glasses and point them at a single tower. So in that image in the lower right corner, you can see the tower in the back. If you walk near our field during the day, this is just the test facility. It’s got around, at this point around 600 mirrors, and we can use it to melt steel and you can’t look directly at the spot because it’s so bright, and we’ve been melting all kinds of ceramics and stuff up there.
And what that enables us to do is use those high temperatures to effectively store energy in thermal storage tanks which allows round-the-clock energy storage and collection for anything that you could need. And so one of the Heliogen’s key things is the decarbonizing industry piece. So it’s not just electricity for the grid or anything like that. Our first project in fact is specifically mining, so I think we talked about it’s it’s more than just the energy itself. It’s things like heat. And if we can replace any natural gas processes with hydrogen, we want to try and do that as much as possible. Heliogen has sustainabilities in our DNA. I mean we are a renewable energy company from the get-go and even the incubator, the startup incubator, idea lab that we came from has spawned a bunch of other renewable energy or carbon capture companies.
And so for our sustainability and ESG goals moving forward, we are actively working to develop those because we are a growing company and trying to grow as responsibly as possible. So we already have photovoltaic systems at our primary manufacturing facility in Long Beach, California. We have very effective cardboard and scrap metal recycling programs there, and then on the sourcing side we’re partnering with EcoVadis to look into a more holistic sourcing strategy for us so that we can make sure that our suppliers are sustainable as well. And the last piece is just we want to make sure that not only improving our ESG footprint, but that we can do so against a very consistent baseline. Because like I said, we’re a relatively young company, and so that gives us an opportunity to start off on the right foot as much as possible. It’s not like we’re refining a product that already exists. We’re inventing a completely new one.
Carsten Hochmuth: Awesome, thank you Jackson. Next we have Daniel for Scania.
Sustainable Transport Powers the Retail Ecosystem
Daniel Rosner: My name is Daniel Rosner I work as a Technical Manager Value Engineering at Scania R&D. Just a short introduction of Scania. We are a transport solution provider, and that means that our main offer are heavy trucks and and buses. You have the long haulage. You have constructions. You have suburban as well. We are all around the globe, 100-plus countries. Main office and then a lot of production is in Sweden. We’re quite proud of that we had the last red figures in 1934. The net sales are around $14.6 billion and the R&D spend 0.74. And we’re also a part of the TRATON group where you also have the Navistar, the Volkswagen truck and bus and German company MIN. Sustainability is really important for Scania. We’re driving the customers profitability through sustainable transport and responsible sustainable business.
If we look at sustainable transport, it relies on three pillars: You have the energy efficiency, and that’s basically that we develop more efficient engines or powertrains. We also train drivers how to drive, how they can save energy, fuel. We’re also really good with all the operational data that we have, so we can specify the trucks for the customers, so they really get the best specification that will be best to meet their SDGs or sustainable development goals. Then of course, this is really important— renewable fuels and especially electrification. That’s where I personally work. It’s a really exciting development with battery trucks. We’re also into fuel cells as well and biogas, ethanol fuel as well. And then finally, smart and safe transport, that is all the fleet management, etcetera, that we’re offering the customers. We have so many trucks connected today. I think it’s around 600,000 trucks connected, so we get a lot of data to analyze and support the customers.
If we look at the Paris Agreement, we have committed ourselves to two degrees, actually 1.5 in ambition. So that means that we will try to decrease our carbon footprint with 50% CO2 with 2015 as a start and to achieve that in 2025. From our internal operations, we are currently at 37%, so it looks achievable. Then the second goal, and this is much more challenging because 90% of our carbon footprint comes from when the truck is in use by the customer. And of course we already produce a lot of trucks on the market and they will be there for a long, long time. We have the really ambitious goal of 20%. We are actually only on 4%, so this is a real challenge for us. But for sure, electrification will be a huge driver in this, and it’s hard to tell how fast the change will go then.
Carsten Hochmuth: Awesome. Thank you, Daniel. And to close out the overviews, I have Brian from Vestas.
Brian Lingaard Jensen: Yes. First of all, we are also, of course, are very much buying into the whole transformation of climate and so on. And just some numbers, I think it’s very worth noticing, if we are to achieve the 1.5 degrees in 2050, which the agreement says, we have to deliver right now and install around 300 Gigawatts of clean power in the world every year. That means we are pushing, just continuously pushing the ball in front of us. We need to do something about this. That is our mission in Vestas, that is to be the industry global partner on sustainable energy solutions. We are 29,000 directly employed at Vestas, but we are scaling up through partnerships. And that means we have been able to outsource a heavier of our production. Right now, we are around 100,000. And the scary part seen from our side is, if we are to achieve the targets as the world has set upon us, then we are looking into tripling our business within three years. So we need to do something also, that’s the challenge we are working with. We have around 54,000 turbines spinning out there, every one of them gives around 500 to 700 data points, that gives us, that we have real-time that we can go in and look at what is happening with these, what is the consumption, what does it reduce, the wear and tear and all of this? Then, yeah, we have a revenue of 15.6 billion. The problem for us is that, unfortunately, it does not rain down on a bottomline. And that is the complexity that we’re working in, that we are selling these solutions two year ahead and have to design our products. We are actually flying the airplane while we’re trying to design it and produce it at the same time.
Sustainability, it actually means something for us. At one time in Denmark, we were raving Vikings that looted around the world, now we’ve become more or less hippies hogging around trees. Last year, we were the world’s most sustainable company. And I’m personally very proud about being part of that one. So, what is it then what we do? We want to go carbon-neutral, so we of course are also setting up turbines ourself, making sure that that happens. We want, of course, to push our suppliers to use carbon-neutral energy. But we are also trying to use zero-waste wind turbines. Again, if you take one of the issues that a wind turbine have is that we are using the plates out of glass fiber. And the glass fiber, when you put resonance, it’s a irreversible process. And the way that that has been handled in the past is, here in the US, there is a big hole and we dig a bit further and then you just put in the blade there. You have a lot of these blades buried down.
They’ll be there for a 1000, 100,000 years, they’re not going to go away. That, we are now investing a lot in. And this year we had a breakthrough, so we are able now to tear it apart and re-use these materials. It’s about social responsibility, ESG.
Carsten Hochmuth: Great. Thank you, Brian.
Great overviews, thank you, all. And I think we all share an equal passion for sustainability and I think it’s evident in the presentations. I have some questions that I can ask, but also this is the time now to, if you’d like to ask questions from the audience. A question for Bobby: you talked about Earth Engine. What are some of the data sources and the datasets do you see as valuable in manufacturing?
What Data Sets Produce Sustainability Insights?
Bobby Pinter: We’ve been having this conversation for a couple of weeks between Carsten and I. I think the kinds of datasets that we’re most excited about certainly is in the energy and renewable energy space. I’ll spend just a minute on the difference between 100% renewable energy versus 24/7. I’ll start with 100% renewable energy. It’s the baseline concept many of you may be familiar, in which you add up the amount of energy you’re using from that yearly perspective and then you wind it up against how much renewable energy you’re procuring through renewable energy credits or some other kind of form. Depending on where you are in the world, where we are looking to bring the system now is instead of going from that yearly perspective actually into that hourly perspective. And that’s really an incredible increase in data.
When you’re thinking about your energy consumption versus demand at any given point in time, you may exist a point in which you have contracted for a certain amount of renewables, but the sun isn’t shining, the wind isn’t blowing, and you don’t actually have as much renewable as you need to meet all of your services at a given point, at which point you go to the grid and you purchase any energy from the grid, which will, of course, typically include fossil fuels. What this means for us in this moment is to say, “How do we actually align the amount of energy we use on that given hour with renewable energy?” We purchase through VPPAs and the like, but we also actually purchase hourly time slices of renewable energy beyond that for each of our various regions and data centers. What this has allowed us to do is actually build this energy data platform, which we’ve built for our own purposes and saying, “We need to understand our energy at this very hyper-granular perspective, and then be able to take action on that so that we can ensure that for any given hour, we’re using 100% renewable energy for that given hour.” What that means for us is, as we’ve built out this data ecosystem, is we’re now looking to use this say, for manufacturers.
And I know, green hydrogen, and some of these other topics will be coming up in the room here around, “How will others need to know what their energy looks like for a given hour? How will they need to know an energy grid mix in a very granular perspective? How would they want to bring the data into their own processes and operations?” We’re trying to think about, how would we expose this ecosystem we’ve created for our own usage for our data centers around the world and bring that to manufacturing customers specifically? Another area, and you mentioned that around bringing on Earth Engine, we have this great understanding, for example, of how watersheds have changed and global systems of climate and the earth itself. And a lot of this is through our partnerships with NASA, the European Space Agency and the like. But Earth Engine, as this product is being used by, I think there was like 8000 publications this year alone that cite Earth Engine specifically. This would be the community of hydrologists and other scientists who are actually using satellite imagery to understand the earth itself, they’re creating this rich data ecosystem for everything from “Where is the areas of water stress?”
If you’re in a manufacturing facility that has water-intensive processes, you may need to know how that watershed is changing fundamentally, you may need to make changes to your processes, may need to find different suppliers. All the way ranging to some of the ingredients or some of the materials that you use, the processes for that may change over time. I think there’s a lot of recognition that climate change will happen, but it’s going to happen in a very asymmetric way, where some regions will be affected more than others, some regions will in fact see an influx, while others see areas of water stress and crisis. We’re trying to figure out: How do you balance all of this information, bring in this global system so you can actually run machine learning, various types of insights on that information and then bring it to you as an insight? Because we don’t think at this point it’s very reasonable for any company to say, “Well, let’s go buy time on the satellite, let’s go figure out how to get a satellite that goes over our operations so we can see what we need to know from that perspective?”
So the question is, how do we make that accessible? How do we bring that to you all in a form of an insight, so you can say, “When I’m planning my next manufacturing facility or which supplier I go with, what are these factors I should be considering from, everything from water to those energy grid mixes that we’ve mentioned in here around 24/7?” Those are the kinds of factors that we’re trying to say, “How do we bring all this together and how do we make it easier for you to use in your decision making. ” As we’ve been talking about a lot about today, how do we take all of the options and show that to you and present that so you can use something like aPriori to actually make those decisions together? I think the story for us is, how do we bring as many of these factors as possible that exists outside of the four walls of your facility and do so in a way where you might not have had access or exposure to that and say, “Now that you know that, what will you do differently? How will that impact a lot of the other decisions you make around design choices?”
ESG Goals
Carsten Hochmuth: It’s a good segue to a question for you, Brian. You’d mentioned a number of ESG goals in your overview. We talk about CO2 a lot as a key goal. Outside of that, what are some of the other biggest metrics or measures that you’re looking to, or that you have net zero goals for? Like water or others? What are some of the most important ones for Vestas?
Brian Lingaard Jensen: Again it’s sustainability, it’s also diversity. And it’s, of course, our powers-our power consumption and use of renewable energy. We of course also have our eyes open to watch the water part. All the way to, when we are building and when we are building sites, whatever we are doing, we are trying to simulate how we can have the least environmental impact. And I believe that people will buy more, they will pay a premium, if they can see on our website or on social media that the products are made in a safe manner, that they are made in a safe manner for our planet and so on.
In Denmark, the home country where I’m from, we are regarded as one of the most green countries. Three in the last two years, we have set one turbine up, and I think we have 11 megawatts that we have been able to approve in two years. There is 2 gigawatts lying through the political system to get it through. For us, it’s about, of course, whatever we can do. And that’s why I think that exactly what you are coming up with at aPriori, we are doing the same, which makes this a good sustainability partnership. You can configure the insights to help us build a green turbine. And then of course there are other ESG goals: “How many women do you have in management? How many foreigners do you have?” That’s part of our ESG program.
Again, we believe that diversity that would create more value. Because one of the issues that we have seen is that if you put five equal, the same thinking people in the same room, you will get more or less the same result every time. But if you then add somebody with a bit of different perception, they will begin to challenge your choices. If you add a quality guy he will talk about “Ahh. What about the quality?” If you begin to challenge from the sustainability point of view or CO2 point of view, then our solutions will be different.
Carsten Hochmuth: Yeah, I think it’s very important to look at the overall scope of ESG, and I think as we’re looking from aPriori and how to attack this, we are starting with the thing that we know how to do. We know how to figure out a process and cycle time and material usage. But that is just a little piece of the overall ESG decision-making process by which you identify suppliers, identify vendors, identify where to source. So were thinking about how the part that we do fits into that bigger picture as well. Let me pause here for questions. Audience?
Audience member: Brian, you mentioned only one turbine going up in Denmark. And we know about the elections here in the US and you could have had another election in Brazil that would have had other consequences. And I’m curious, for the first time you’ve actually seen renewables go up in price, since, I don’t know, a long time. So I’m wondering what your thoughts are on that.
Brian Lingaard Jensen: Yeah. There’s no doubt that for a long time, everybody could see the capital began to flow to the renewable companies, so there’s a lot of capital there. When there’s a lot of capital there, there’s a lot of players who want to come in and try. And that has been for a long, long time a bidding game. And then they started with auctions. Then you have to put in auctions and so on, so you saw that the prices simply just went down to about 30%, 40%. And we as a market, we simply could not be able to sustain. We cannot follow technology anti-wise as fast as the market was dropping. What we are seeing now is that we are beginning, as the markets are beginning to mature, we are beginning to also see it’s again, bigger, bigger, bigger, bigger, bigger. When I started we were selling 2 megawatt turbines, now we’re just launching a 15 megawatt. And we are there where we hardly can transport it. We can almost not assembly it. And it is extremely expensive.
But again, it’s a very good business case because what we are seeing now is also the prices are increasing. But we are choosing now, we are also choosing who is it that we want to partner with as customers, where are the ones that are creating value? So again, before, you could say Vestas was trying to be everything for everybody. We stopped. We are turning it a bit around and saying, “We would like to be everything for a few. And then people that want our turbines, they have to buy the standard turbines.” And by that, we are able to begin to get a fair value for our turbines. And also running our testing verification sites. Here we have one turbine in Denmark, where at the same time last year we got one million DKK, I don’t know, it’s 200,000, around €150,000 of revenue on that one. This year for the same tube, the same time, I’m getting 12 times that around. Not having done anything. So the prices are increasing, but are they increasing enough? There’s a lot of money out there on this part, and that has to be somehow leveled out. There’s a lot of stuff happening, there’s a lot of trading going on and so on. But sustainable partnership, making sure you’re not just in for the volume, you’re there for the quality, you make sure that it’s the sustainable businesses that you deliver to.
The Role of Value Engineering in Sustainability
Audience Member: Hi, this is Rushi. A question to Tristan or Daniel. Both of you work as value engineering at great firms. So the question is, whenever we have to go carbon-neutral or de-carbonize, there’s a price we have to pay, like material choices or logistics for altering the supply chain for where we want the part to be produced. Being a value engineering manager, how difficult is it to make those straight-off decisions between cost and sustainability? And how can we find the focal point in order to make those decisions, keeping cost as well as CO2 emissions in mind?
Tristan Abend: I’ll go first. That’s a great question. I think sustainability in particular in my team at least, really has come to the forefront this year, and I think our stance on it hasn’t really changed from a cost point of view. And by that, I mean cost is number one, always going to be as a value engineering team, what we look at first. But where we’re starting to change our own perspective inside my team now, is then no longer do we just look at it from a matrix costing point of view, you look across countries and look across materials, now we look across different combinations for carbon and cost. And that way, we present a plethora of options. I never wanted to be the one to make those choices for product management, I never wanted to be the one to make the choices for the design engineers. What we have always done is presented them with the options of, “You can either go this way or this way, it’s your choice, but you have to understand the implication.” We always present them with the least costs, and we present them with the least carbon.
And very often, I have found so far is that they’re not mutually exclusive. Very often, what we’re looking at at Carrier is moving away from metal to plastic and we see huge cost savings from that, but we also see a huge carbon recovery because of that as well. I never really want to make them mutually exclusive. And I would say most of the time, we don’t see cost increase due to the carbon removal. Now where we are seeing cost increase due to carbon removal is more so in design, and specifically, refrigerants. Something that doesn’t get talked a lot about is, we have container units out on the sea right now, that use CO2 as a refrigerant. Now, that has a GWP of 1, it’s an incredibly good refrigerant for the environment. Now here’s the dirty little secret, it’s awful as a refrigerant, from a performance standpoint, we have to have such a high pressure in order to make it work, that we actually have to have very often two compressors on the system rather than one. That’s a huge increase in cost that we have to put into the system, but you get a huge carbon payback for it.
And those are some of the operational decisions that we have to make very often. And that does put more pressure on a value engineering team, because now we have to go out and we have to find different ways, more creative ways to get the cost out in order to count for the carbon. But if I can maybe just add to that, from my perspective, being the value engineering team, part of your responsibility too, is to paint the picture. So from my perspective, one thing that’s really worked well when it comes to this conversation is showing energy returns, specifically when it comes to our factories. As I said, we’re very much committed to reducing energy in our own factories, not only here domestically in our own country, but abroad. And because of that, when we’re doing these models, it’s not so much as just looking at maybe carbon choices around material and things of that nature, it’s also looking at just taking energy out. Let’s just keep it simple. How much money do I save from not putting into the product?
And I think for something like that, our team has been chiefly responsible for being able to picture different business models and trying to come up with different revenue streams when looking at it from a carbon perspective. Because it’s not enough anymore just to say that it’s a better carbon product. It’s also you have to look at, what revenue streams, where am I actually picking up some savings by not putting the carbon into the product? As I said, operational carbon, it’s about 99% of a chiller. Embodied carbon, very little amount. But that’s not how it’s going to be forever. You put in a couple of solar cells onto a chiller, and now all of a sudden, 99% turns into net-zero real quick. So because of that, me and my team are focused on embodied carbon only. Operational carbon is something that I focus on with the business units and their leaders. We have a great leadership team in each of our business units focused on operational carbon. The vice presidents know the product roadmap going forward. And that takes a little bit of the burden off our value engineering team, because now we know more precisely what we can control.
Brian Lingaard Jensen: I would also say, for me, it’s two things. Either it’s a use case and everything we do starts with a use case. And if it’s not a use case, it’s an investment, then it’s a cost. But let’s assume it’s a use case, then you know that there is somebody who wants this. And then you dribble down in your processes. And then it’s just a matter of how, like at aPriori here, how can you help capture that you’re actually delivering that use case to the customer? But if you’re not talking about a use case, then for me, it’s just an investment that you believe that it has some cost value for potential stakeholders in the future.
But for us it’s a good use case because we know that the big cities are beginning to close down, you’re not allowed to drive, at least in Scandinavia, and I think also Berlin now, you’re not allowed to drive inside the town if you have a normal combustion engine. These things are coming. So you have strong use cases. Then of course it’s something internally in the company that one person has been measured on how much cost can he take out and all of that, but you need to work with those processes, how do you make sure that your use factors follow you through your design process? So you always can explain why did you choose what you chose. Otherwise, it’s a losing game.
Carsten Hochmuth: I have actually a follow-on question to that, a slightly related topic. In some of the early adopter conversations, I think Heliogen and Carrier have been testing out some of the sustainability software that we have at aPriori. And I think one question that’s come up a number of times in conversations is the idea of baselining. We all want to improve how much carbon is in our product, but how do we even know where to start? What is the actual current carbon in the products that we build and the products that we make? So curious, maybe, Jackson, you can share some thoughts on how you’ve looked to approach the idea of baselining, understanding current carbon in your product.
Jackson Baker: Yeah. It’s a very interesting case study for Heliogen because we’re really starting from ground zero with our product. It’s not like we have something that exists that we’re trying to calculate the carbon contained within it. So we’re able to start using aPriori from our earliest decision-making in the design process. We’re able to go by essentially our entire BOM and cost it in aPriori and get that as a baseline just to start from. And so one thing that we have been thinking about a lot, and this is both for carbon and for cost, is:what makes a good part? And while you can see that very easily iteratively, you can see “Is it better than the previous version?” It’s very difficult to see, “Is it a good part against some consistent global baseline?” And so that’s something that we’ve been looking into to figure out how to say, “Can we get a huge database of parts and look at the carbon footprint for a diecast part or something like that?” And then can we say, “On average per kilogram of diecast part, you’ve got this much CO2 aggregate across everything”?
When we design a part, we want to be 25% of that or something. We want to know that it’s a good part empirically, or not empirically, but globally, not just against the previous iteration. And because we have so much freedom in our design process right now, we can make those big trade-offs between processes, materials, and things like that. And so in terms of baseline, I think, for us, it’s more of a moving target. We’re week over week looking at our carbon and continuing to push it down, because we really, we have one really high volume product and that’s our heliostat, the thing that points to mirrors. And it’s a pretty simple BOM, it’s got maybe 100 parts and we’re trying to squeeze every last bit out of it that we can. Everything for us is about optimization. And so in terms of baseline, I wouldn’t say that we have a baseline, other than that we know exactly where we started because we use aPriori for it, and then, we’ve been week over week iterating down from there. And we want to create a way to have a more global baseline moving forward. We can only do that if we get access to a larger set of parts.
Tristan Abend: And then for Carrier, we’re a much older company certainly, and because of that, baselining products is much harder, in particular for supplier parts. When you look at some of our products, what’s involved with them from a commodity standpoint that we don’t produce, you will not find suppliers that are necessarily willing to hand on over all the information that you’re looking for. That’s more where value engineering comes in. Our team in particular is very good for baselining some of these supplier products. Because design teams very often don’t do that. Recently, I was at our mountain well site over in France, and there is probably our pioneering group when it comes to doing life cycle analysis and environmental product declarations. I was stunned at some of the material assumptions that that team was making, largely due to the fact that they are still getting into the system, they’re still understanding their own products that they create. And because of that, that’s where our team is very strategically located to be able to do baselining on supplier products.
So we will do teardowns on these things, we will weigh the parts, we will understand what the material is and then we will bring it in to aPriori to be able to make an energy model and a carbon footprint model that then can get back-fed into the LCA, and that really creates some of the most accurate LCA information that we can create and that is what we put out into the marketplace. When it comes to our own products, certainly, it relates back to something I mentioned this morning around the PLM integration, being able to show a carbon footprint for every part that we design inside our own PLM system is a game-changer for us. So then now I can see it from a cost standpoint. From a revision standpoint, each new revision, now I can see what happens to the carbon and the cost at the same time. Because of that, we’re now able to actually do baselines. Whereas right now, going forward, we haven’t had this capability before. For our supplier products though, I would say that’s where we’re seeing a lot of the returns.
Carsten Hochmuth: There’s another question from our audience.
Audience Member: You mentioned the goal of a 20% reduction in the impact of a product that’s already out in use, which I think is a great objective. But how does one go about changing a product that’s long since left your factory and is presumably out of your control?
Brian Lingaard Jensen: We are looking into the aftermarket for Vestas, what can you do more? How can you go back to what you did and try to fix it?
And here, that has been where they are taking ethanol and methanol. And you don’t have… Some of this, you don’t have to be able to run 2000 kilometers. You just need to get into the cities and back, if that’s where you start. And then you can slowly phase out the population of the cost.
Tristan Abend: Tied to that is a baseline in that particular part of that product’s life, because in any LCA you have part A, B, C and D. And really, a lot of the times when it comes to part A and B, we the manufacturers, we understand that, well, that is something that we control on any given day. Part C, which is the operation and Part D, which is the recycling and end of life, those are the parts of the process, which from a legacy manufacturer, we don’t have a lot of control over and never really had. But to answer that question, you need to know what the baseline is, that’s where we are trying to invest a lot more time into doing an LCA in getting that environmental product aspiration out the door because then that’s the baseline and now you know where you can go with things. And also working with your customers, tied to that, doing retrofitting and in our particular case, trying to upgrade to more energy-efficient systems, but doing it in a way that our service technicians, wherever they may be in the world, can actually do it out in the field because otherwise if they can’t, it’s very worthless.
Carsten Hochmuth: I’m assuming there’s also opportunities to bring the product back, like recycling and support the recycling efforts. And I think tying back to some of the data conversation earlier around things like route optimization, making sure trucks don’t drive empty, on certain return routes, things like that. The more data you have on your systems, the more, I guess, proactive you can be around optimizing its usage. More questions?
Audience Member: The one question I have is, for factories that have been around for a while, what does the investment look like? What does the actual retrofitting of a factory look like to make it auditable, to make it traceable, for these goals that you’re looking for? For some factory that might not have any traceability right now, what does that kind of ramp-up look like?
Brian Lingaard Jensen: €3 million. That’s how much a smaller turbine cost then to place it outside, and then you hook it up, then you have free power, more or less.
Audience Member: So then does the grid need to evolve around some of these factories? Is the smart devices inside tracing energy? How would you approach the question for some smaller factories that maybe you’re trying to acquire?
Brian Lingaard Jensen: Yeah. We have the same problem. The size of what we’re doing, as we have a lot of space that we need and there’s a lot of these processes that we are looking at, that is heavy industry processes. And so we are looking at, with the Industry 4.0, trying to electrify, trying to digitalize, try to get those process under control, by actually trying to put some power towards it. But we’re also trying always, when we do that, to do it sustainably. For me, sustainable business also means quality, that is to make sure that when we are setting turbines up around the world, we need to make sure that it’s top quality. The service guys that comes, it’s people we buy from outside. So how do we make sure that they have the training? How do we make sure they have the knowledge? It’s, again, applying all of these tools that we need to, in order to get that full sustainability partnership. And I think for everybody, it’s a journey.
So, how can we get our factories green, you ask again. Look at your energy consumption, where does it come from? Look at your heating, where does it come from? Stuff like this. The water, where does it come from? Do you use air condition? What can you find in other solutions?
Tristan Abend: Also, if I could tie into that too, never doubt the fact that trying to make your factory a little bit more environmentally cleaner is also good for your people. When it comes to VOCs coming off of your paints, degreasers that we use on our coil lines in various factories around the world take up huge amounts of heat and it’s not a pleasant environment to work in. And part of the innovation process has to be making your factory just that much cleaner, is also gonna make a better environment for your people to work in as well. It makes a better environment for everybody inside the factory, it makes people wanna work at your factory more. That’s another part of it that needs to be kept in sight.
Carsten Hochmuth: Related to that, I think when you talked about the data sources, Bobby, how granular does it get? Could you look at a specific factory location and say, “Okay, this is the electrical use right there, that’s the heat use right there and that’s the water use right there”?
Bobby Pinter: Yeah. We’ve certainly been trying to focus on the granularity of that. I think some of the interesting things that we’ve been working on, especially, is this idea of, how would you add a single manufacturing site or an energy-intensive facility, start to bring in that information from the utility directly? Connecting the data feed of, this is the ongoing energy usage that they’re putting out as a signal, putting that into a data platform for yourself to be able to say, “This is how we can actually line up our utilization of the facility with those other factors.” Certainly something like water or some of these bigger, more broader scale attributes wouldn’t be necessarily as closely tied, you might want to look at that as more of a watershed level as opposed to this facility specifically.
I think one of the big topics that always comes up here is certainly around IoT and some of the other use of this high data velocity applications, or how do you take as much of the sensor data you have available and bring that into a cloud-based system? So you can turn all of those into insights. I would say, Yes, very specifically on this one, energy is something that we feel pretty confident that people should be viewing that at the facility level from the “What are we bringing in? What is that grid mix? How would we want to be looking at additional renewable energy purchases of on-site solar or on-site, wind?” To go back to the comment you made earlier, that would be the kinds of outcomes that we expect people to start to make, especially when they’re thinking about this facility making creating products. The question is how do we continue on from there?
Jackson Baker: If I can add to that too. I was recently working with one of our suppliers at a sheet metal plant, and they came across some of this information as a by-product of a time study that they were doing on how much idle time there was on their machines. It ended up being something that, by increasing the efficiency of their actual manufacturing process, they were decreasing their energy usage across the board and increasing their profit margins and it all lined up very nicely. And so I think, our suppliers have been surprisingly receptive to things like, “How can we track your efficiency?”
Renewable Energy Removes Risk for Tech Startups
Audience Member: So I’ve got a question for Bobby: am I correct that Google, some of your facilities, you’re essentially off the grid, you’re generating your own electricity as opposed to it coming from power and utilities?
Bobby Pinter: That’s a bit of a rare case for us. Because we are still coming from the grid, but we are able to take advantage of different types of renewable energy purchasing through VPPAs and this other concept called T-EACs, those are the things that we look to do that allows us to effectively decouple the energy that we’re using from the grid energy or the carbon intensity of that grid. For example, if the grid by baseline is 30%, we would look to either make additional purchases or use these kind of things to reach that 100% number for ourselves. That’s the nuance. Of course, it’s easier for us if the grid is already 90%, we’re not doing as much beyond that, but the one we look at for any individual location, especially for data center, we say, “What is that grid level carbon-free energy?” And then again, we’re measuring out in the hourly perspective and they’re saying, “What would we need to do to get those kinds of incremental improvements for ourselves?”
And by the way, we’ve seen quite substantial impact from an energy hedging perspective. The more that we’re decoupled from the grid, the more that we are less subject to energy volatility. This has been something that we’ve been very carefully monitoring, especially in Europe, where we have a significant number of data centers. Because we’re realizing that all of the renewable energy purchases that we made in the name of sustainability are in fact reducing the amount of risk that we are facing at the moment. And those numbers are actually quite surprising in terms of how beneficial it has been for us to be so aggressive with our renewable energy purchasing.
Audience Member: That was my second question: if I’m a company and I can invest outside of the power and utility, if I can invest in my own off-the-grid or a micro-grid power, won’t I have an advantage because I know what my cost will be five years from now? Is that true? Would being off grid be less expensive for the startup company doing it?
Brian Lingaard Jensen: Yes. But that’s also one of the strange things. I’ll give an example. In Denmark, when it’s really blowing, you have turbines standing still and then you think “Ah, it’s because they can’t maneuver. They can’t spin around.” That’s simply not true. The reason why is because it’s generate so much power that Germany can’t take it, they cannot offset our energy, so they are paying the Danish wind turbine to actually idolize their turbines. Okay. If you think about that one, then you could say, “Yeah, we know that at least, where I come from, the wind is blowing significantly more in the evenings than it does in the daytime, strangely enough.” So, how can you then work with it? Then you can work at night, or you can work at looking at batteries. How can you store energy so you could use a bit later? And that is also some of the things that we are going into, we have batteries set up at our headquarters now. We are doing these agreements, these research projects to see how can we utilize it more. Because if you can have a battery and then you could say you could also make it to a hydrogen, whatever you do, but how do you store it? Then you can use it when you need it, and then you have a damn good business case. Then it’s good. But that’s also, if you look at the way that I see, the question also about what we can do, it’s again, it’s just like your household, again, don’t use your washing machine when it’s most expensive, use it in the night. You can adapt to that. And the storage solutions, they are rapidly increasing. That’s a lot of investments that goes there.
Jackson Baker: I’d add, one of the most viable business cases for Heliogen is, really remote mining locations that have difficulty accessing the grid. I think some of them that we’re looking at are currently trucking and diesel. And so, if they can make it an individual high capital investment now that’s going to provide power for the next 10 years, then it’s relatively easy math to do. And so that’s how we’ve been looking at cost is not just from a piece part individual cost, which is what we’ve been using aPriori for, but as a total module cost, because we’re installing a power plant. And so, the security that you get from, once we hand it over, that you are fully self-sustaining for the next 10 years or 30 or whatever it is that we insure it for. But yeah, I think that great access is something that’s sometimes taken for granted, and especially in very industrial processes like mining, sometimes the grid just isn’t accessible, period.
Carsten Hochmuth: Awesome. Thank you very much. Thanks for being here.