Video
The Latest Advances in Machining
Get actionable insights to improve manufacturability at every stage of your product lifecycle. Simply upload your CAD files into aP Pro and our digital factories will run a detailed simulation of the manufacturing process in a fraction of the time it takes with manual calculation methods.
In this demonstration, we use aP Pro to:
1. Open a 3D CAD model
2. Enter in key details about your part to quickly build your digital factory
3. Quickly obtain a complete cost and DFM analysis for your part
4. Review the machine routing aPriori creates for your part
5. Understand how your part’s geometry contributes to cycle time
6. Review all of the machining advances in aP Pro including multi-spindle machining, our most advanced machining model
Watch this short 10-minute demonstration to get an insider-look into aP Pro’s digital factory and machining capabilities.
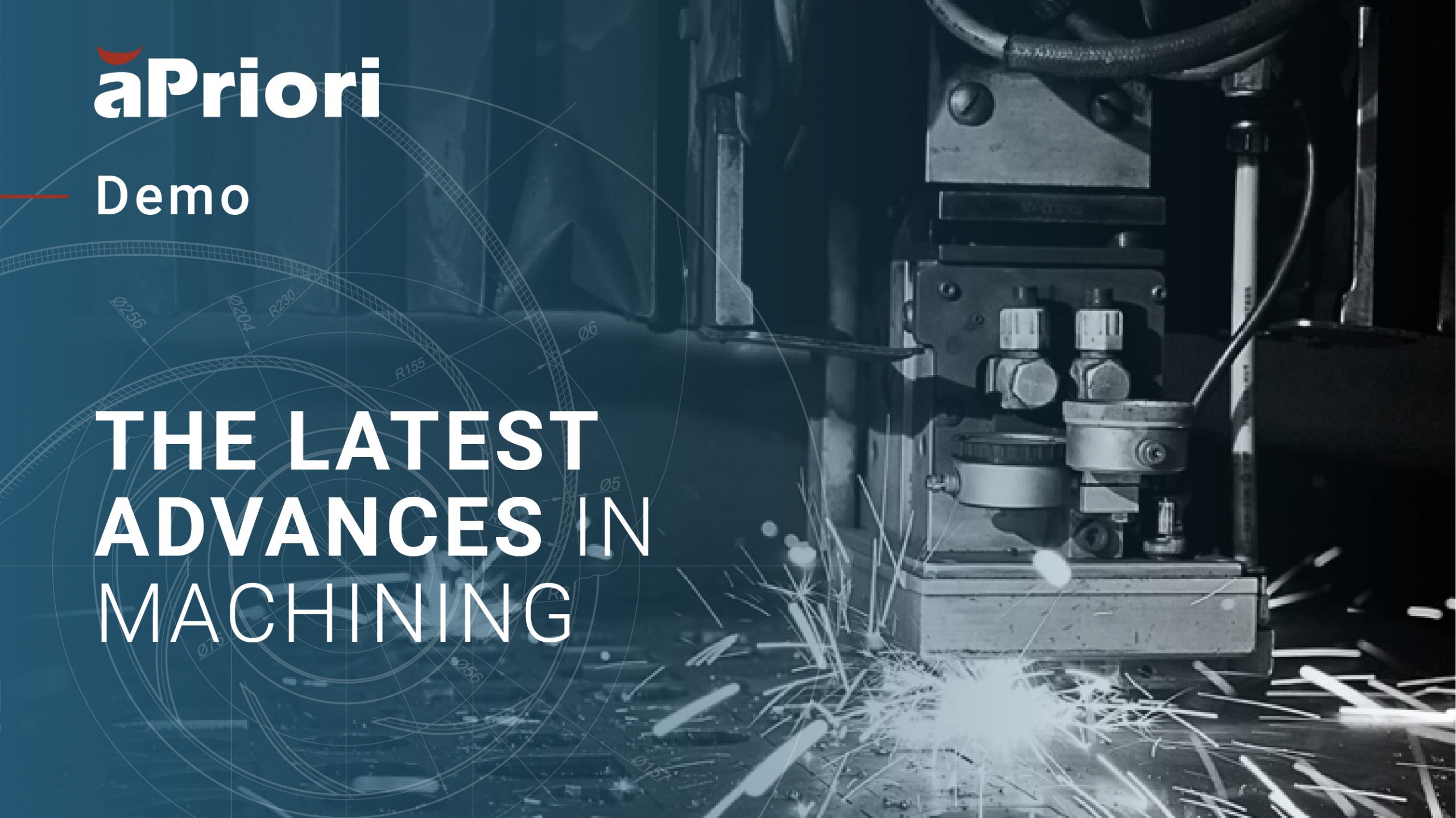
Transcript
Hello, everyone, and welcome to new updates for stock machining. My name is Frank Iacovelli and I am an application engineer at aPriori. This product demonstration will consist of a 10-minute demonstration.
Cost and DFM Analysis on Manufacturing Machining Process Models
We will begin in the aP Pro platform. I’m going to navigate to a CAD file and open it up. We can open up native CAD file formats and neutral formats, part files and assembly files. Here you can see I’ve opened a part, for us to do the analysis on the part, we need to identify the process group. In this case, it’s going to be stock machining, but we have a big list here, you can choose from.
Next, what we’ll do is choose the geographic location that we’re gonna make it. This is our digital factory, and we’re gonna choose the USA. We have 87 regions represented around the globe. These digital factories can be configured to represent your exact factory or facility. Will then go in and add a secondary process here, we can choose those from a list. We’ll choose anodizing and include that, we’ll mine the material from the CAD file and pull one from our database, set the annual volume at 250 and then kick off the part analysis. By answering those few questions, we’ll get a complete cost and DFM analysis on this part that aPriori has returned from costing.
The first thing that we’d like to do is check out the routing that aPriori has come back with. This is a look at the manufacturing process routing engine. These are the different potential ways a part can be machined, and we’ve costed it through two, a 4-axis mill and a 3-axis mill. The one that’s presented back to the user is the 3-axis mill because it’s the lowest cost. We can see a little red X by the 5-axis. A rule was broken, so it didn’t bother to cost in that. And I’ll explain that shortly.
Manufacturing Technologies: The Role that Geometry Extraction Plays in Costing a Part
Here we can see under Part summary, there’s some component information, a cost breakdown by category, the 3-axis mill and anodizing, and then you get a fully burdened cost over here. What we’re going to focus on is the geometry extraction, this is what enables us to do all this so quickly and consistently.
Each process group has its own unique set of geometry, and that’s where most of our patents lie. First off we have something called setup axes/candidates. This is how we determine how many set-ups and what routing to choose based on the potential set-up, you have on their relationship to the geometry. Here it’s chosen two setups on a 3-axis mill. These are called our hard setups.
Next what we’d like to do is understand how this geometry helps us calculate cycle time. We’ve got a 41-minute cycle time, and this is broken up into roughing, surface finishing, and holemaking. The roughing stuff primarily comes from this volumetric costing. What you have in the volumetric stuff is a stock trim. This is the excess stock around the part. We’ve recently broken that up into six different sections so each one can be addressed with different tools, maybe different machining practices, but it gives us a little bit better number on some of the roughing. Pockets are geometry that is exactly that – a pocket.
We’ve greatly expanded how much geometry these can capture. These are two new ones, relatively new ones. One is a shelf pocket with an open area on the outside and the other one is a through. Then we’ve also done a bunch of work on slots. So in the past, this would not have been captured as a slot. It says there are four of them here. We can now better address that piece of geometry. And then we’ve also done a bunch of work on o-ring grooves. Here we have straight sides, one angled side, and two angled sides. So we do a much better job of picking those up. Those tend to be very expensive, time-consuming features. Here you can see the different calculations. One is rough milling, one is slot milling, and then the ones with the sides are general slot and you can see the different times on those based on the angles.
What we’re attempting to do is capture as much of this geometry in these artifacts and begin removing stuff from bulk mill. the Bulk mill manufacturing process is a legacy process in aP Pro. It was what he used to calculate roughing, and that was everything that wasn’t either the part and was the outside of the stock. We’re now whittling away at that and capturing that stuff with these artifacts. Pretty soon we’ll see this go away and most things will be captured by pockets and slots. We’ll do a much better job of calculating roughing. Next what we have are holes and these are just that. Geometric definitions of holes and that’s where this holemaking calculation comes from. And then finally the surfaces are where most of our finishing comes from. Those are broken up into planar faces. You can see each of the faces and the time that each one took.
Automating Cycle Time Calculation and Material Waste
The longest planar face was the floor of this pocket. Then you’ve got curve walls. These are one degree of curvature. And then curve surfaces are surfaces with two degrees of curvature. Each one of these gets a tool assigned to it, a distance the tool travels, the diameter of the tool, and the rate the tool travels, that’s how we do this cycle time calculation. And then finally what we have are perimeters. We’ll dig into those. This will enable us to do nesting on this part, waterjet cut out the profile. So the next thing I’m going to do is take a look at the utilization, which is 21%. So we’re machining away most of that stock. There might be an opportunity to nest this thing. Some of the newer functionality in here is to be able to go into the process setup options and flip this over from all bulk mill, meaning all rough, the geometry, to do a plate cut with a drop off. And then we’ll go ahead and apply that and see what our results are. It’s now come back from costing and our material utilization has gone from around 20% up to 32%. So we’ve got a significant reduction in the material waste. If we come over here and look at the material nesting review, we can see that a plate was chosen and the parts were nested on the sheet.
So this is a best fit nesting. It will wiggle those in. It’s very similar to the nesting algorithms we use in sheet metal, but now you get a much better cost. And if we look at the routing, we’ve got a perimeter mill in there with a waterjet operation. So next what we’ll do is we’re going to take a look at some more advanced machining modules that we have and this is going to be something new. I’m going to bring up a mill turn part, very high volume, and we’re going to switch to a new module called multi-spindle machining. When I do that I’m going to let aPriori choose the material from the CAD file, but I’m going to do 250 or 2.5 million parts.
Analyzing The Results
And then what we’ll do is go ahead and cost this. This is going to do a geometry extraction as well, but we’re pushing it through this multi-spindle module. Within here, you have slightly different routings. You’ve got a 6 and an 8 spindle machine, and then what you’ve also got is a 2 spindle traditional multi-axis machine or a mill turn machine. aPriori has now come back from costing it says the front spindle is working on operations 1-5 and the back spindle works on 6. If we go to part summary, within here we, have simultaneous turning chosen $9 per part. We’ll go in and look at that routing routing, and what it’s telling me is it’s costed it on each of the machines. On the 6 spindle it was $1.09, on the 8 spindle it was $1.26, and then $1.13 on the dual turret machine.
What’s really nice about this is I can go in and click here, and this is going to show me exactly how each of the operations was broken up on each of the spindles and the amount of cycle time. So if I hit details, we can go in the stock feed and then take a look at the rough turning operations for the OD and then the two ODs. Each of the spindles gets assigned a geometry. These will be all operating simultaneously. Here we can see that this one was 23 seconds so you’re gonna get a part dropped off every 23 seconds and it split up each of the features. The peck drilling of that hole was the longest so there might be something we can do with that to reduce it, but this gives you very good insight into exactly what happened.
New Manufacturing Processes in aPriori
Polyturning is something else that’s new and this is polygon turning where you can go in and mill and turn the spindle at the same time. If you check that on YouTube you can see exactly what that is. There’s also rotary broaching. These polygons are also new geometric features that we’ve added. The different ones that we have are rotary broaching for the internal, polyturning for this one, and then rough milling for the outside. So we’ve done a really good job on the geometry extraction and then divided each of those features up among the spindles. And this is just an example of some of the advanced machining operations that we can do. That concludes the presentation.