Video
DEMO: PCB & PCBA
The product experts at aPriori showcase the innovative PCB & PCBA commodity analysis using aPriori’s software.
Digital factories like aPriori make it easy to run cost models on your PCBs and PCBAs. aPriori’s digital factories enable you to factor in machine feasibility constraints, material feasibility rules, routing rules, chip placement rates, machine size limits, material cost rates, labor rates, and so much more.
All these inputs enable you to get a fast, easy, and highly accurate cost model for your PCBs and PCBAs. Don’t miss this complete overview of aPriori’s PCB & PCBA cost model focusing on analyzing aPriori cost estimates and tips for costing PCBAs.
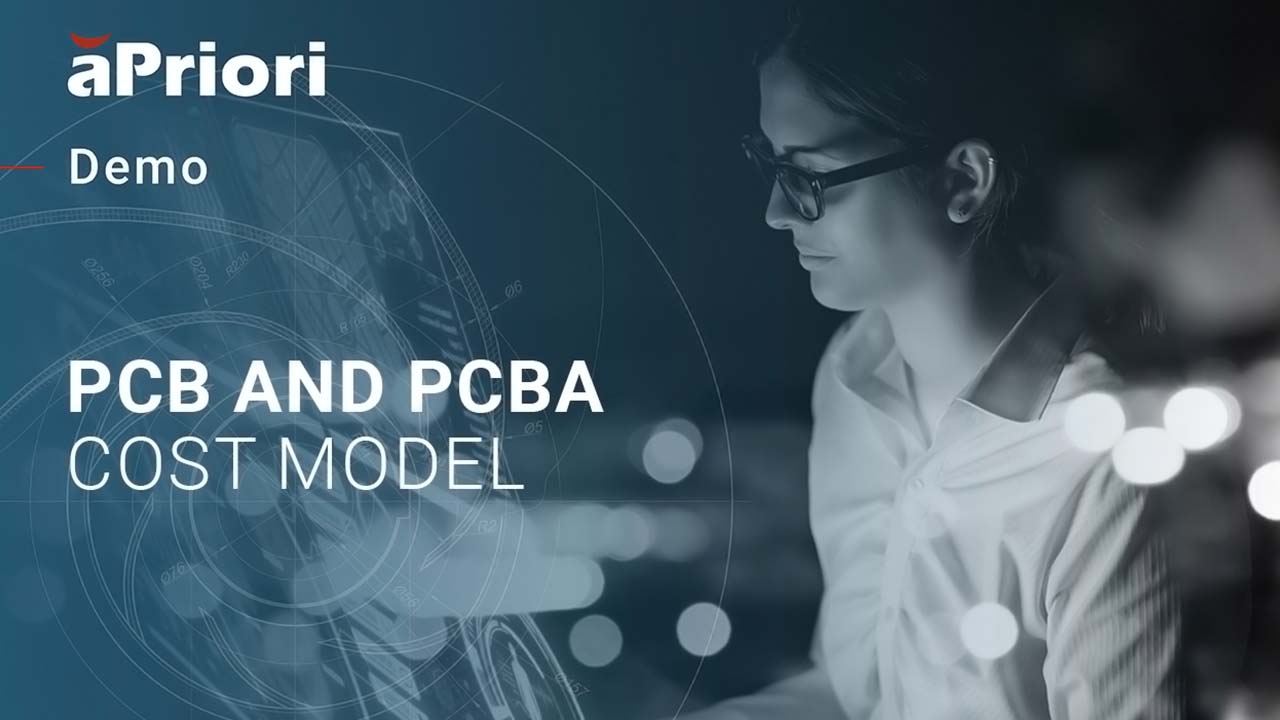
Transcript
aPriori PCB Cost Model and Commodity Analysis Demo
Lily Thomas: Hey, everyone. My name’s Lily and I’m going to be discussing tips for analyzing PCBs and PCBAs with aPriori. I’m a Senior Consultant here at aPriori, and before joining aPriori, I was a commodity manager for PCBAs. The PCBA cost model in aPriori is complex, with over 20 processes, and can be tricky to use because it requires the bill of materials, and the PCB cost model is pretty new, so I think there may be folks listening who haven’t used it before. When customers start using these cost models, they wanna understand all of the steps at aPriori models and what are the critical cost-driving processes that I need to pay attention to, and if I encounter errors, for example, if components are failing to cost, how can I fix it? So that’s a challenge when using these models, and when customers don’t understand the critical cost drivers in the model or how to fix common costing issues, it can result in your model being ineffective at helping you achieve your goals.
Today, I’m going to give a brief overview of both the PCB and the PCBA model, in case there’s anyone who hasn’t used it, and I’ll discuss a study that aPriori did on the sensitivity of the PCB model to the various inputs to determine which inputs are the most critical to cost, and I’ll talk about how the cost estimates of PCBs and PCBAs can be used to mitigate market challenges that we’re seeing today, and then finally, we’ll end with some common costing errors that I see customers have and tips on how to resolve them. During the session, I hope we’ll be inspired to tackle PCBs and PCBAs and aPriori, and after the session, you should have a good understanding of tips for analyzing PCBAs as well as how to resolve common cost errors, so your costing efficiency will be improved.
Overview of aPriori PCB and PCBA Cost Models
Let’s start with an overview. Like other aPriori process groups, we have digital factories which have the machine library with the capabilities and limits, so for example, what’s the chip placement rate, what size panel can fit on the machine, we’ve got secondary processes, inspection times, and all of the cost, account data and labor rates and overhead rates. For PCB, we extract geometric information from the Gerber file; however, for PCBA, there is no model to extract information from, and instead, we use a bill of material which provides the component prices, quantities, and types of components. So we know which assembly operations to use.
You could see a screenshot here of some of the processes that we model, but that there are so many steps that I actually couldn’t even fit them all in one screenshot. So one thing I wanna mention is aPriori does not on its own come up with a component cost estimate. You can either load your negotiated component cost into a component library within aPriori, or we can from aPriori, connect to SiliconExpert, using your SiliconExpert license and pull costs from there.
And I mentioned this because I see a lot of customers spend a lot of time trying to get component costs reflected correctly in aPriori, which is nice to have, but aPriori is not adding the most value in giving component costs. It’s adding a value in estimating the cost of assembling those components and the PCB together and estimating the testing. So in terms of investment, time investment in using the aPriori cost model, especially if you’re just starting, I would recommend focusing on getting the physical information about the components, the pin count, and the mount type, that information, aPriori needs to know what assembly operations to provide. Focus your energy, getting that information into aPriori and focus your analysis on how did aPriori estimate the assembly operations and, what are the critical cost drivers of the assembly operations, how does the assembly cost estimate in aPriori compare to my current assembly costs in reality, that will be value-add instead of spending a lot of time trying to copy your component costs from a cost of bill of materials or SiliconExpert into aPriori.
aPriori PCB Process for Manufacturing Cost Reduction
We’re going to start with the review of the PCB manufacturing process, and then we’ll go to PCBA. So we’ve got over 28 processes modeled in aPriori, only key processes are shown in this slide, and I’m not gonna read through each one because you can read it for your own. The processes in the red outline are part of the layer processing cycles and will vary depending on the board stack up in whole types. The processes in the blue dotted outline are applied to the panel once all the layers are cured. But I show this process map to give you an idea of the processes that we accounted for, but also to emphasize how many there are, and users often wanna know which steps are the most important, so if my goal is to reduce my cost, which step should I spend my time at? Or if I’m really trying to understand cost of a board, which step should I spend my time at?
aPriori did a sensitivity analysis on the PCB cost model, so first, what is sensitivity analysis? It’s a statistical methodology to check how sensitive is a model’s output to the various inputs, so we use a program to systematically adjust input variables for PCB one at a time and measure the resulting percent change on piece per cost. We’ve done this with a number of our cost models to determine what are the key variables that have the largest impact in cost, so if you’re interested in this information for another cost model, you can reach out to your customer success manager, you can reach out to me, my email will be at the end of the call, or you can reach out to aPriori support, but I wanna tell you about the results of the PCB sensitivity analysis specifically. This can help customers focus where to spend their time when investigating the cost of a part.
For PCB, we found it is most sensitive to the number of boards per panel. You’ll see that this variable number of boards per panel is used all over the PCB cost model because the more boards in a panel, the more cost of every… Most operations is spread over that panel and reduced per board. Furthermore, many machines that are involved in PCP processing can fit multiple panels, so the number of panels that can be processed in a given operation is also significant, so looking at the number of PCBS nested in a single panel, and then for each operation, how many panels can I process at a time. Those were two of the variables that the PCB costs are very sensitive to, and then the third, the third in this rank that the PCB was most sensitive to is the number of drilling heads when drilling the holes.
If you have a PCB estimate and you’re trying to understand, okay, my estimate is different from my quoted cost, or I wanna understand where a lot of the cost is coming from, these are three variables right away that you should check. So if you’re trying to investigate why is this board so expensive or why are the costs different than my expectation, check how many boards per panel we’re estimating, check how many panels per machine or per bar when plating, for example, aPriori is allowing. That’s where a lot of the cost is coming from, and one of the costing tips that I’ll cover later is how you can adjust the number of boards per panel.
aPriori PCBA Sensitivity Analysis in the Assembly Process
Okay, so moving on to PCBA again, I’ve got a high-level process map, I’m not gonna go into detail of every operation, but again, there are a lot of steps from the bill of material, aPriori will get the component pin counts and Mount types to determine which processes to apply, so is it SMT, is it played it through hole and the placement rates, if you’ve got other components that don’t have a pin count or something like a connector or a cable assembly, you will be able to specify manual assembly operations as well.
What are the processes that the PC… Or the inputs that the PCBA cost model is most sensitive to. We haven’t officially conducted a sensitivity analysis, so we haven’t done the systematic analysis like we’ve done for PCB, but I can tell you what I found based on my work with other customers and feedback that I got from other aPriori consultants on what we’ve seen by experience to be the most impactful. So one of them is the chip placement rates on the SMT machines, so make sure that the rates in aPriori are realistic for the mix of boards that you have. So if you’ve got low volume, high mix, the chip placement rates may need to be lower than what aPriori has. If you’ve got high volume, low mix, you may have higher placement rates. Oftentimes that the SMT cycle time is gonna be the gating operation, that’s gonna gate the throughput of the whole line, and so checking those rates will be critical.
Another process that is good to check is are there any manual bottleneck processes. So aPriori will identify a bottleneck process in the SMT line, and a lot of times that is driven by the placement rates in the SMT machine themselves, and it will gate other operations that it considers part of the SMT line by that throughput of the bottleneck process; however, aPriori will not pace the SMT operations based on manual operations at the end, so if you add a manual assembly operation to add a connector or to attach a cable assembly or to do some software loading or additional inspection, aPriori is not gonna gate the SMT processes based on that manual operation, but in reality, some production facilities may pace the whole line based on a manual operation, and then you would need to adjust your placement rates in the SMT machine to be gated based on the manual operation, and then finally, similar to PCB, the number of boards per panel is a critical variable for PCBA as well, so the more PCBAs you can process at one time, the lower the cost is gonna be.
The PCB cost model was released a few years ago, so it’s quite new compared to some of our other models, and some of the plans that we have on our PCB roadmap in the future are to support ODB plus plus files that’s gonna be in our ’23 release. We’ve got other projects on our road map, although I don’t have firm dates at this time, but to give you an idea of what is in our pipeline, we’re going to be updating PCB to support high-density interconnect boards. We plan to make adjustments to PCBA and PCB to represent high-volume production, the cost models right now are more representative of medium production, and therefore, the cycle times are a little slower. We’ve gotten feedback from customers who work in very high volumes, in hundreds of thousands or more, that we need to add some more to our machine library to more properly represent that type of high-volume PCBA manufacturing environment, and then finally, we have plans to change PCBA from a separate digital factory to a regular process group that’s a part of our regular digital factories, so if you’ve used… If you’ve costed PCBAs in aPriori before, you know you have to select a digital factory called aPriori PCBA USA, for example, as a separate digital factory, but we plan to combine those.
PCBA Challenges: Rising Component Expenses and Production Costs
Okay, so we’ve got done the overview, but let’s get into the good stuff. You’ve seen how aPriori creates the data, so how can you use the cost results to actually mitigate challenges in the PCBA market? Here are some of the challenges that I’ve personally faced when sourcing PCBAs, and I’ve also seen our customers dealing with. So one of them is, I’m getting price increases on all of my PCBAs across the board due to rising component increases, and so the challenge there is, I know component rates are going up, and therefore, I’m getting cost increases on all of my boards. So I feel I have no leverage to go back and negotiate because everyone knows that components have been in a really difficult supply chain situation, causing lead times to go up and prices to go up. So I’ve been in this situation, and I’ve seen customers be in a situation where it’s like, well, how can I create leverage? How can I discuss cost out when we know that so many of the costs are going up?
Another challenge is, okay, I know component prices are increasing, but I don’t know if the increase is reasonable, so how can I make sure that I’m only paying what is fair based on how the component prices are changing, and then finally, component prices are changing too fast to keep my aPriori component library updated.
I mentioned at the beginning that aPriori doesn’t generate its own estimates for components that you can load prices that you get from a cost of bill of material. Maybe you have a commodity manager at your company that negotiates component rates, you can load those directly into aPriori. So I’ve seen the market changing so fast, component rates changing all the time, that it becomes difficult to keep aPriori updated with the most recent data. So we’re gonna talk through how you can handle all of these tips, and we’re gonna start with the first one, which is all of my prices are going up due to component increases. How can I gain back some control over my costs?
Controlling PCB Assembly Costs and PCB Material Expenses With aPriori
What I’ve seen work with other customers is to focus on the cost you can control, so for the most part, you cannot control component prices. You may have a commodity manager in your organization who negotiates component rates directly with the component manufacturers, but if that’s not your role, or if you don’t have that role in your organization, then oftentimes you really can’t control the component costs, but you can control the make cost or assembly cost of the board.
While the component cost is often a large cost driver, it’s not everything. There’s still the cost to do the assembly operation, so aPriori lets you separate the component cost from the main cost. So step one to focus on cost, you can control is to isolate make cost from component costs, and aPriori does this for you. When you’re looking at an assembly, the piece part cost is aPriori’s estimate of the cost to assemble the components together, and then separately, it gives the fully burden cost of the sub-components, and that’s the component cost. So aPriori already separates this for you.
The next step is to look at the quotes that you have or the prices that you’re paying, and do the same there, isolate the quoted make cost from the component cost, so this way we can check which parts have the largest make cost spend versus largest overall spend. So boards with the largest annual spend don’t necessarily have the largest make cost spend, and this allows you to separate increases in make cost from increases in component cost, so you can see in this example here, PCB, PCBA-3, the third one in this third column has the highest annual spend, but PCBA-2 actually has the highest make cost spend, so if we take PCBA-2, we’ve got a total quoted cost of $35.12, the CBOM is $22.10, so if we subtract those, we’re left with $13.12 of make cost, and if we multiply that times our annual volume, we get an annual spend of 58,000, which is higher make annual spend than the other two boards.
This can help you understand where are my make costs the highest, and then to facilitate an outlier analysis in aPriori record that quoted make cost that you’ve calculated for these boards in the quoted total cost field in aPriori. So for PCBA-1, instead of recording $20.52 as my quoted cost, I’m gonna record $4.15 because that’s my quoted make cost. I’m gonna record that in aPriori.
One thing to note is to make sure that you’ve included the material overhead and the cost of bill of material costs, so some suppliers may include material overhead as a separate line item on their quote, so they may quote. Here’s the cost of bill of material, and here’s a total cost of the material overhead, so since material overhead is really not an assembly cost or make cost, you do wanna subtract it from the total quote when you’re estimating your quoted make cost, so just make sure that you are including the material overhead in your material costs that you’re subtracting.
Okay, so then the third step is to run an outlier analysis, so you can create… Using an ad hoc report, you can create an outlier analysis, so the scenario piece part costs in aPriori for an assembly is already just the cost of the assembly operations, and then you’ve recorded your quoted make cost in the scenario, quoted Total Cost field in aPriori. So you can create a report that’s taking the difference between the quoted total cost, and remember, you recorded that as just the make cost and then the aPriori make cost times the annual volume. So you’re getting an estimate of the… You’re getting an estimate of the annual potential savings in manufacture cost only, not components, so then you can see which boards have the largest gap and the largest annual potential savings in only manufacture cost, and this is your opportunity to go and discuss those costs and see if there’s anything that isn’t within your control to work to reduce cost regardless of the component prices, so in this example here, the aPriori estimated assembly cost for PCBA 2 is $9.11, and the quoted assembly cost is $13.12, so you’ve got annual potential savings of $20,000.
You may be thinking, Okay, but if I’m using the same component costs as the supplier, then why do I need to do this? If the aPriori component cost and the supplier quoted component costs are the same, then the difference between the aPriori fully burden cost and total supplier quote will be equal to the difference and make cost, so if you are able to have component costs in aPriori match exactly what your supplier’s quoting, then your outlier analysis will already inherently show just the difference in make cost, but that brings us to our next challenge, which is component prices are changing too fast for me to keep my aPriori component library updated. So I’ve seen customers be in situations where the component prices are changing very quickly, and that’s where it can be useful to do this isolating of component cost versus make cost, so what are some situations where the component costs could be changing? So, for example, if you’re comparing quotes from multiple suppliers and all of those suppliers have different component costs, then it can be really useful to look at, Do this isolation and say, Well, what is each supplier quoting for make cost, and how does that compare to my aPriori estimate for that region?
You may have a supplier who’s changing component costs frequently, so you might be getting multiple price updates per year, any time you go to place an order, maybe their updating pricing component costs were changing rapidly, so you may be struggling to keep up because you’re constantly getting new input from the supplier and what the new component costs are, and then it can be a task to have to go in and constantly update that information in the component library, and finally, you may have a different commodity manager in your organization, who’s responsible for negotiating costs directly with the component manufacturers, and if they’re currently in negotiations, you may not… Your component costs could be changing, or if they’ve just given you a new pricing that you’re changing, so these are some of the situations where you really could have component prices that are changing a lot, and isolating make cost from component costs can help cut through the component confusion. So the final challenge that I mentioned is, I don’t know if the component price increases are reasonable. I know component prices are going up, but I don’t wanna pay more than is fair.
If you’re using the electronic data collection tool within aPriori and you’re using that to access SiliconExpert data, you’ll see that SiliconExpert reports both an average cost and a minimum cost, and I think in my experience, a fair rule of thumb is if your supplier or a contract manufacturer is getting components directly from a component manufacturer, they’re negotiating with them directly, and the price that they pay should at least be less than the average SiliconExpert cost. From what I’ve seen, oftentimes the data in SiliconExpert is from distributors, or at least its distributor cost averaged together with the cost from the single manufacturer, and so oftentimes it’s more expensive than a large contract manufacturer who’s negotiating directly with a component manufacturer may be able to get. So I think that a good rule of thumb, a good check is that the cost that the supplier has defined directly from a manufacturer should be at least less than the average cost from SiliconExpert.
Now, it’s possible that the price has changed very rapidly, and SiliconExpert data could be stale, I believe it’s based on prices that are currently posted on SiliconExpert, but that data could come from purchases that distributors made a few months ago, but I think it’s still a pretty good rule of thumb.
And one thing that you can do is you can actually run this comparison, so take a bill of material or a couple of bill materials, see what your quoted component costs are, and see how they compare to the SiliconExpert average cost and minimum costs. And if you’re seeing that most of the components are lower than the average cost and just a few are not, then it probably is a good rule of thumb, and you can investigate why is it that there’s a few components that are higher than the average SiliconExpert cost, you may even see that your contract manufacturer is often able to get prices that are better than the SiliconExpert minimum cost, and you could use that as your benchmark for your rule of thumb.
Customer Case Study: Focus on Make-Cost With aPriori
Okay, so let’s look at a couple of examples of where focusing on make cost can yield fruitful discussions with suppliers. So in this example, the quote was provided with the cost bill of material, the labor cost, testing cost, margin, and then total cost. So the supplier had a bucket in their quote was just labor cost, they called it labor cost, but in reality, it was the total make cost of the automated operations before any manual processes or testing.
I see that a lot, depending on how organizations do their cost breakdown, they may call something labor cost, but it really may refer to the total cost of all of the automated operations. So that was the case here. So it said labor cost, but really it was the cost of all of the automated operations, and then they had a cost for the testing separately, so we compared the quoted make cost to the aPriori make cost estimate and saw a big gap. So we simply asked the supplier what is the long pole in the tent, or what is the longest operation that’s driving the labor cost. And they said, well, you’ve got conformal coating on the board, and so we have to manually mask off a lot of these components before applying the coating. And so we said, Oh, okay, but on some of our other boards, we know that you use reusable masks, which should be much more efficient, so why don’t you do that? And the supplier said, Well, yeah, but those costs money, and you haven’t given us the purchase order to go and buy these types of masks, so what we ended up doing is splitting the cost of the investment, and they were usable mask with the supplier, and then the supplier was able to truly reduce their labor cost and pass it on to the customer.
This is another example, so you can see the gap here. We had an aPriori manufacturer make cost estimate of $13, and the quoted manufacturer cost of $20, and in fact, the supplier was now re-quoting. New Year component prices had gone up, but also we saw that they were quoting a new make cost estimate of $30. So yes, component costs were going up, but we saw also for this board, the make cost quote was going up, and so that’s something that should be… We can work together with the supplier about to see if we can really do something to reduce the cost. So the customer said to the contract manufacturer, we’re trying to understand the cost of this board, and it’s higher than our expectation. Can you help us understand why? And the supplier said, Well, we’ve got scrap built into this make cost estimate, and the customer said, Okay, well, what is the scrap rate, and the scrap rate was much higher than they expected, or the yield rate was lower than the typical industry benchmark. So now the supplier and the customer were having a totally different discussion about this board, which is, How can we improve the yield? Instead of, How come the component costs are going up? And I wanna note that they focus the discussion specifically on this board because this board had a larger gap between the aPriori estimate and the aPriori estimate of make cost and the supplier quoted make cost.
There was a much larger gap between those values for this board than for other boards, so instead of trying to negotiate 5% off all of the boards that they buy or try to minimize the increase that they are getting on all of the boards that they buy due to components, they were focusing their discussion very specifically on this board because it had a large make spend, a large gap and they were able to have a discussion about manufacturability and scrap instead of component costs.
I hope that section gave you some ideas of how you can use the aPriori data in discussions, but you do need to be able to generate the data in the first place, and I know many customers will get errors when they’re costing PCBA or PCB. So I wanna go through a couple of common errors that I see, and I’ll show you how to address them, and this will increase your efficiency on generating cost estimates or PCBs and PCBAs. So this is a really common error. I’m sure folks have seen it before. You’ve loaded a bill of material, you know it had SMT components on it, and yet aPriori says, Your BOM does not include any components which require surface mount processes.
This will happen if you set this manually costed field in the bill of material to true for all of the components, so this is a really common point of confusion with customers. The purpose of this field in the bill of material, this manually costed column, is to tell aPriori if it needs to automatically assign assembly operations or not. It does not tell aPriori if it should take the component costs from the bill of material or from a component library, that’s really comes. A lot of customers will set this field to true because they say, Well, I want aPriori to take the cost estimate from this bill of material, and so I’m gonna set manually costed to true. That’s not what it’s for. Manually costed is meant to be used when you’ve got components that do not have a pin count, so aPriori cannot automatically assign operations to it.
So in this example, I’ve got… The first level is my PCBA, then my PCB, and I’ve got some resistors, capacitors, and then I’ve got a connector, so my connector doesn’t have a pin count or amount type, and so I’m going… It’s added by hand after the other PCBA processes, so I’m gonna say this set this as manually costed to true, because I’m not providing a pin count or amount type, aPriori is not gonna be able to assign an operation to it, and I’m gonna tell aPriori using my inputs that there’s a manual assembly operation, another example would be if you have ESD bags on the bill of material, and there’s not an assembly operation for those, but you need the component cost to be accounted for, that would be a manually costed as true.
Okay, so this is how that error will look in aPriori. You’ll see a big red X next to the SMT, and if you look at your messages, you’ll see that message that I showed before. So you may be thinking, well, how do I tell aPriori to take the cost of the components from the BOM? That’s what this portion of the user input box is for, so if you wanna tell aPriori, I’ve got my component costs in my bill of material. Please read them in from there, you use this component import behavior, and you tell aPriori to take cost and source information from the BOM only. So this is what tells aPriori where should I get my cost from. The manually costed field in the bill of material tells aPriori I need to automatically assign assembly operations to these, so that’s a really common point of confusion, and then finally, just a screenshot, so let’s say I had that connector that I showed before, I can add final assembly operation, and I could specify that I’ve got one manually line to component, or if I’ve got software load, I can specify that. So any operations that are applied to components that don’t have a pin count or amount type, you can usually find them here to apply them.
Okay, so another common costing error is maybe you’re bored for the most part, costed successfully, but you’ve got a component or a couple of components that failed to cost, and you’re trying to figure out why did they fail. So I actually have a video of this one. This is exactly the board that I just had taken a screenshot of on the previous slide, so you’ve got some components that costed fine and one that failed, so you can actually double click on the component that failed to cost, and it will open that scenario in aPriori, so you can see it’s a user guide component, you can see that it failed, and if you click the cost button, your aPriori will re-cost it, and you’ll see the error. Now, in this case, the error pops up right here ’cause the error was I don’t have the digital factory loaded. In some cases, you may need to consult the messages pin, and then you can see what the error is.
In this case, I didn’t have the digital factory loaded. Some other common errors are, it’s missing pin count or amount type. If you are telling aPriori to use a component library, it’s missing from the component library, it could have failed an MOQ check, and I’ll get into some of those a little bit. The other handy thing about this screen is you can change component information right here, so if the error was it’s missing a pin count, you can add pin count. Let’s say that you’ve loaded a whole bill of material, and then you realize that just this component had the wrong price. You can actually go in and change the price right from here without having to reload the whole bill of material, so that’s really handy as well if you’ve just got a couple of components that the price was wrong. So this is a handy tip that I think a lot of customers don’t know that you can make some edits to components from this screen within aPriori.
This is just a summary of what I mentioned with some of the common failure modes. So like I mentioned, it could be not having a pin count or amount type because it’s missing from the component library, or you told aPriori to get the physical information from the bill of material, but you forgot to fill it in the bill of material for this part, or it could have failed an MOQ check, and I wanna go more into that one next.
Using aPriori to Determine if Components Are Failing MOQ Checks
So if you use a component library, there is a field in there for minimum order quantity, and you can put different prices for different MOQs, and aPriori will check if the PCBA annual volume times production life is greater than this minimum order quantity, so it is gonna check it for a single PCBA, you are meeting this minimum order requirement. So let’s look at an example. So let’s say your costiveness board, you’ve got 2,000 words per year for one year, and you’ve got an MOQ of 10,000, so if you try to cost this component, 2,000 per year times one year does not exceed the MOQ of 10,000. Now, a lot of customers say, Okay, but this component is used on many different boards. It’s not only used on the single board, and therefore in total, I am meeting my MOQ. If that’s the case, then your options are, you could set the MOQ to one in the component library, you could change the production life to be longer so that it would meet the MOQ, so you could change it to 10 years, or you can also configure the cost model to remove the MOQ check. It’s something I’ve done for customers before.
So one thing to note as well is if all of the components on your board have failed the MOQ check, you might see that error that there’s no SMT components because all of the components have failed to cost. Okay, so I mentioned, I see customers spending time ensuring that their component cost in aPriori are matching exactly the component costs that maybe being quoted from the supplier. So one thing to be aware of is if you’ve added margin to your digital factory, aPriori is gonna apply that margin to the assembly operations as well as to the components. So if the component costs that you’re inputting into aPriori already have margin on them, then you’re gonna be inflating your component cost estimates, so let’s say that you get a cost, a bill of material from a supplier, they may already have added in margin to each of the component costs, so if you load those in and then aPriori is adding another 10%, you’re gonna be double-dipping on margin, and you’re gonna see that your fully burdened cost of sub-components is higher than your cost bill of material.
And so, what you could do in that case is you can remove margin from the digital factory and then just apply it only at the assembly level, or you can input the component costs without margin, knowing that aPriori gonna add it back in. So that’s something to be aware of that aPriori does add margin to components. All right, so let’s talk about a common PCB error, so I’ve had customers say, Hey, you told me that the number of boards per panel is really critical, and you can see the nesting in aPriori of how many boards it’s nesting per panel. Customers say, Okay, you told me that the number of boards per panel is really critical, but there’s no option for me to manually change the utilization in aPriori. So if you’re familiar with the sheet metal process group or even machining, you know that you can click on the material selection and override aPriori’s calculated utilization. But we don’t have that ability with PCB. What you can do is utilize process set-up options to change the spacing allowance, so let me show an example of that. I think that’s a better show with an example.
So this is a demo PCB that I costed. You can see the utilization is 39%. As you may say that’s much lower than that it should be, so you can check the material nesting and see how many boards per panel that it’s using. Now, know in aPriori, the blue outline is the panel, and the green outlines are individual arrays. So you can go to the process set-up options, and you can change… These are kind of similar to sheet metal, you can change the non-nestable trim strip width, you can change the length, the allowance for the millimeters between parts. So if I lower the non-nestable trim length, then you’ll see that now aPriori is nesting more of the boards together, and now my utilization is up to 60%. So I’ll show you one other thing that you can change in the process set-up options. You can just go in and directly change the number of boards per panel or the number of boards per array, but keep in mind that aPriori does have a maximum that it’s capable of fitting. You can also change the panel size if you’re using a larger panel size. So that’s where you would go in aPriori if you want to change the nesting to improve utilization versus being able to directly override the utilization.
Okay, and then the final error that I wanna talk through, and this one can be frustrating ’cause it seems so simple, but it does trip a lot of people up. When you’re costing PCBAs, I kind of touched on this before, you do need to make sure you’re selecting a PCBA digital factory. If you try to cost a PCBA using aPriori China, it will not work. So you have to select it on the PCBA, and I alluded earlier that on our road map, we are working to eliminate this differentiation and just have PCBA be incorporated into our regular digital factories, but for the moment, you do need to make sure you’re selecting a PCBA digital factory.
Thank you for attending this session. I hope that this prepared you to cost and analyzed PCBs and PCBAs. If you have any further questions, you can reach out to me. My email’s here. If you’re a current customer, you can also reach out to your consultant or your customer success manager. Thank you very much.