Video
DEMO: How To Get Product Costs In Bulk with aPriori
Leveraging aPriori’s bulk costing capabilities, engineering, sourcing professionals, and VA/VE teams have the ability to process tens, hundreds, or thousands of components simply by leveraging the digital twin. Gone are the days of searching through individual excel or PDF files to look at all of the data in each individual part or component.
aPriori’s bulk costing tool looks at parts from a mechanistic standpoint, understanding how and what is the optimal way to manufacture that part, and will present the user with design for manufacturability challenges or feedback as to how that component can be improved. You can then also take that result and iterate on this to understand what are alternative ways to manufacture this part or where in the world is it most ideal to source this component from. Learn how in this bulk costing demo video.
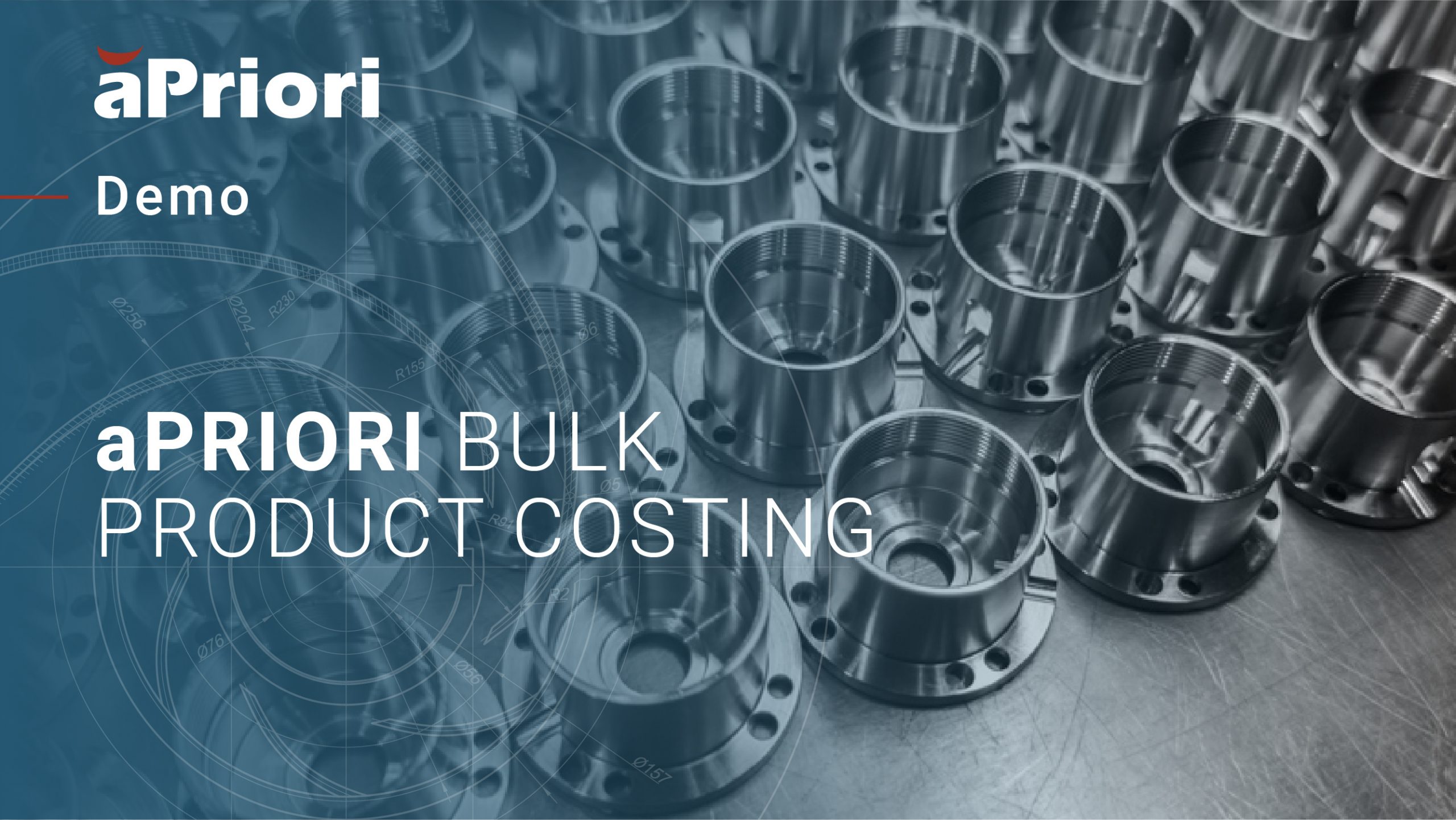
Transcript
Hello everyone, and welcome to today’s session on cost insight analysis using the bulk costing tool within aPriori. My name is Patrick O’Brien. I’m an application engineer here at aPriori. The product demonstration today is going to consist of about a 10 to 15-minute demo. I’m going to showcase a couple of different use cases as well as some functionality within the aPriori bulk costing platform.
Alright, so let’s get started. In this session’s agenda, we’ll be covering how bulk costing is done today, which tools sourcing teams use to identify where components should be sourced, or which components they’re overpaying for. From an engineering perspective, which components are challenging to manufacture or which components are going to lend themselves best for a design review, and for VA/VE teams, with the hundreds of thousands of components that could potentially exist within a business, where are the ones with the most opportunity from a product cost reduction standpoint. We’ll then take a look at how aPriori’s bulk costing tool works, and we’ll then scan through various different examples as to how we can leverage bulk costing and the reporting capabilities within aPriori to help us really make the best business decisions possible, and then we’ll wrap up with some questions.
Identifying Parts That Are Affecting Profit Margins
When a sourcing individual needs to identify a part for relocation or where are some components that we’re currently overspending or overpaying for, having large quantities of part detail may exist, but generally speaking, it’s in individual Excel or PDF formats or even hard copies. How can an individual be expected to scan through these hundreds, if not thousands of documents to help them make that decision?
From an engineering perspective, there are programs such as Stage-gate processes in place, but generally speaking, with juggling multiple projects at once, all in different phases of development, how can an engineer be expected to get the design right the first time at a lower price, every time without having a tool to aid them in manufacturability assessment or design alternative options?
And finally, VA/VE teams, leveraging tools such as costed bill of materials helps us understand where the expensive components are on a product line or an assembly, but are those truly the parts that present themselves with an opportunity for cost reduction or have they already been optimized?
A common theme associated with all of the methods prior mentioned is that engineers, sourcing professionals, and VA/VE teams simply do not have the time to look at all of the parts in the data. Leveraging aPriori’s bulk costing capabilities, your teams will now have the ability to process tens, hundreds, or thousands of components simply by leveraging the digital twin.
Bulk Costing is the Solution for Major Manufacturing Cost Reductions
aPriori’s bulk costing tool is going to look at that part from a mechanistic standpoint, it’s going to understand how and what is the optimal way to manufacture that part, it will present the user with design for manufacturability challenges or feedback as to how that component can be improved.
You can then also take that result and iterate on this to understand what are alternative ways to manufacture this part or where in the world is it most ideal to source this component from.
Here, we’ll walk through a quick sourcing example as to how bulk costing can be leveraged to really find those parts with significant savings opportunities. Now, whether these are currently manufactured products or it’s NPD projects in the pipeline that we’re interested in optimizing for cost. For example, if sourcing is trying to understand the cost of current components within an assembly, a commodity group, or maybe it’s an NPD project where quotes are starting to roll through the door, they can utilize the bulk costing tool within aPriori to simply point to a directory where the digital twin is stored of that product line or of that commodity group. By pointing to that single directory, aPriori’s bulk costing tool will locate and grab all of the digital twin files that represent that product line, commodity group, or NPD project, and with one click of the cost button, they’re able to reproduce cost estimates for all of these components found within that file. Cost estimates such as overhead costs, material costs, and labor costs, will all live within those digital twin files.
A huge benefit of leveraging this bulk costing capability within aPriori is the ability to jump right to a top-level viewpoint of the project. Whether this is looking at the commodity group in question, the assembly, or the product line costs, the user can immediately see what is it that we’re currently paying for the components today or how are those components being quoted today compared to a should cost, that mechanistic cost that aPriori has generated and then immediately seeing an annualized potential savings plot. The output from this is an indicator that these components here, we’re currently sourcing these or they’re currently quoted at a very fair price whereas we can see a couple of parts over here to the left as outliers that are sort of jumping off the page at us as having some opportunity for cost reduction. The user is able to simply click on that bubble and immediately see some part cost details relative to that component.
Shifting to a different view, the user can now see the makeup of the total cost for this component. They can look at specific information such as labor cost, the direct overhead portion, even things like SG&A associated with the cost estimate coming out of aPriori. This really allows the user to understand what is driving the total cost and arm them with the information and the data to then understand where there may be gaps from that quoted or that current cost compared to the aPriori should cost.
Matrix Costing Assemblies or Components Can Positively Affect Gross Profit
Another key component of the bulk costing tool within aPriori is the ability to matrix cost assemblies or individual components. The matrix costing tool allows users to cost one component or one product in multiple different regions. You can see here the user can point to multiple regions around the world, indicate specific manufacturing annual volumes, and then even details such as purchase quantities they’re interested in. By adding those to the list, aPriori will cost this component, this assembly, or product in hundreds or even thousands of different ways if needed, and then allow the user to mine that data. This here is one quick example of an output from a matrix costing event for an individual component.
It allows the user to see specifically within their supply chain base what makes the most sense for a sourcing location, but it also can give some insight into whether there certain areas around the world where they may want to expand their supply chain base. In this particular case, they have current factories in North America, South America, and China, but it’s an indicator that there actually may be a better price in Southeast Asia, and it could be an opportunity to expand the supply chain base elsewhere.
Bulk Costing Existing Product Lines to Get an Updated Complete Cost Price
Another fantastic use case for the aPriori bulk costing tool is to aid design engineers with design reviews. This can look at existing products that are currently being manufactured today, as well as scan entire product lines or assemblies that are in the development phase to help identify those components that need the most attention currently from a DFM standpoint, whether that’s looking at manufacturing the product in an alternative method such as die casting a currently stock machine component or just identifying components that are challenging to manufacture.
This particular report here is a design-to-cost outlier report, specifically referencing machine components within a product line. An engineer can use the bulk costing tool within aPriori to point to a directory and then scan those components for manufacturability issues. aPriori will score those components low, medium, and high, and it’ll size the bubble appropriately to the amount of annualized spend relative to that product. So effectively, with this plot, we’re looking for large purple bubbles, large bubbles indicating high spend, purple indicating challenging to manufacture. We can see that we have one clear outlier here, and by clicking on that bubble, we can jump right to a part cost report, and we can also shift gears and use the aP Design platform to dig into those details.
Using the outlier plot to identify the component, we can now load the component in aP Design and immediately start to dig through some of those challenging manufacturability issues aPriori is highlighting for us. One example here is looking at cycle time penalties. In this particular example, this face on this component is taking a much longer time to manufacture or machine than other surfaces, indicating that it’s an expensive feature. By driving cycle time, in turn, driving cost. We’re also able to dig through alternative things such as the guidance within aPriori to tell the user, “Here are some features that are either very challenging or impossible to manufacture as is, as well as features that are simply driving up total cost.”
Alright, in this particular example, we can see tolerance thresholds indicating that we have a reaming operation rather than a simple drilling operation. In this particular example, aPriori is indicating a couple of sharp corners that we’re finding in a pocket where an end mill simply cannot come in and clear out that material as drawn. We also have in-app guidance to allow the users to basically click on these bubbles and have a quick lesson or a quick coaching session as to why is it that aPriori is flagging this issue, and then how the user could then remedy the issue.
Cost of Goods Sold (COGS) is a Complicated Calculation
Throughout the few examples that we’ve covered today, we’ve looked at things such as where in the world do we want to manufacture a component, or where are we overspending on components, right through to what are the things behind the manufacturing details that are driving costs or that are challenging to manufacture. The underlying theme to all of this is we have a tremendous amount of manufacturing data as well as part cost data that we’re now able to tap into to identify cost of goods sold (cogs) and this is really how VA/VE teams can optimize or streamline their process when they’re trying to reduce cost on current products.
Bulk Costing Examples
In these two examples, a user has scanned their entire product catalog, this is across multiple groups, and multiple product families on anything that is a billet machined component, and what we’re looking at doing is identifying those components with less than a 50% material utilization factor, meaning we’re machining a tremendous amount of material away, and that’s simply lost to scrap. What this allows us to do is ask some of those what-if questions such as, “What if we looked at a post-machine die casting, maybe a post-machine forging, is there a design opportunity where we can actually break this into two components and maybe look at assembling the two together?” The example on the right, an engineer has leveraged bulk costing capabilities in a very similar fashion, where aPriori has scanned hundreds or thousands of sheet metal components within a business.
They’re trying to identify parts where the processing costs for the sheet metal components are greater than 60%. Whenever working with sheet metal components, we always want to see material as the primary cost driver, so in this case, we’re trying to flag components where that is not the case. It’s usually a quick indicator for us that there are things like tight tolerances driving machining or complex part geometry, such as forms that are requiring hard tooling. These are great opportunities for cost reductions, and leveraging bulk costing allows the user to scan those products in a mechanistic fashion and jump right to those of which that are outliers to help optimize, not only the engineers’ use of time but looking for the products that are actually going to have the most bottom-line impact from a cost-saving standpoint.